Impact Innovations was founded 2010 and is since that time rapidly growing. The founders have more than 20 years of experience in the cold spray technology and are one of the pioneers of this technology. Nowadays Impact Innovations is the global technology leader in High Pressure Cold Spray equipment for industrial applications. Impact is located in southern Germany and operates its own cold spray in-house R&D center. Impact consists of a dynamic team for flexible industry-specific solutions. The company considers themselves as an industry partner for metal coatings and additive manufacturing. With German advanced engineering Impact stands for highest quality and efficiency.
Easy Engineering: What are the main areas of activity of the company?
Impact Innovations: The cold spray technology is a thermal spray process for metal material using powder as a feed stock material. But in contrast to all other thermal spray processes, cold spraying doesn’t melt any metals, but uses high kinetic energy to apply very dense and homogeneous metal built-up and coatings with superior bonding strength. By accelerating metal powder to about triple supersonic speed it operates at low temperatures and there is almost no thermal stress in the coating. This way we achieve material properties that are similar to bulk material. The high process (deposition) efficiency and deposition rate lead to low coating costs in serial manufacturing. These advantages make the cold spray technology attractive to several industries.
We can apply metal coatings starting from below 50 μm and can go up to several centimeters. This means we can also do additive manufacturing with almost all metals and their alloys, but at about 50-100 times higher speed than typical 3D printers. With other words the output capacity per minute of a cold spray plant is higher than the capacity of a 3D printer per hour.
This way we serve all different kind of industries. But there is especially higher demand coming from those industries:
- Electrical & cookware industry: with no oxides in the coatings cold spraying achieve best thermal and electrical conductivities
- Aerospace as well as Power & Energy market: demand for superior material properties
- Automotive industry: low process costs for high volume due to highest deposition efficiency and minimum pre- and post-processing costs
- Other industries: wear resistance and corrosion protection for different applications as well as repair work for valuable parts

E.E: What’s the news for 2021 about new products?
Impact Innovations: Just beginning of 2021 we released a new product generation the Impact cold spray system EvoCSII. All past developments and experiences were used as the basis to design a perfectly coordinated plug and play solution. Impact Innovations achieved to offer customers consistently high quality for single part and series production based on a durable, but also maintenance-friendly system architecture through intelligent process control.
Due to the parallel operation of up to four Impact Powder Feeders, the new Impact Cold Spray System EvoCSII is great for serial production. It is also possible to operate two Impact Spray Guns in parallel for double-sided coating or simply higher capacity. Thanks to a higher number of sensors, data recording and an integration in higher-level control, the process reliability increased significantly. It was a major step to successfully prepare the Impact cold spray system for industry 4.0 requirements. In addition, the EvoCSII system has a 100% modular system architecture, so that all modifications and upgrades can be done at a later point in time as required.
E.E: What are the ranges of products?
Impact Innovations: Impact Innovations is the specialist for high pressure cold spray equipment. Due to the manifold advantages of the cold spray technology over other thermal spray processes Impact Innovations focuses 100% on the cold spray technology. We offer a smaller spray gun called EvoCSII 5/8, which is mainly suitable for spraying low melting materials as pure copper, zinc, aluminum, nickel and their alloys. The larger version the Impact Cold Spray Gun EvoCSII 6/11 can also spray all other less ductile metals as stainless steel, magnesium, Inconel, titanium and carbide-based mixtures etc.
Next to regular spray guns Impact Innovations developed and manufactures several other components for cold spray systems such as:
- Rotating spray guns and adapters for coating inner diameters
- Powder feeders for constant smooth powder supply
- Application specific injectors and nozzles for highest efficiencies and avoidance of nozzle clogging
- Water cooling unit for constant temperature and reduced nozzle wear
- Several other components that simplify operations and improve coating results
Supplementary Impact Innovations provides industry specific turnkey solutions that are highly automated and always adapted to the specific customer requirements.
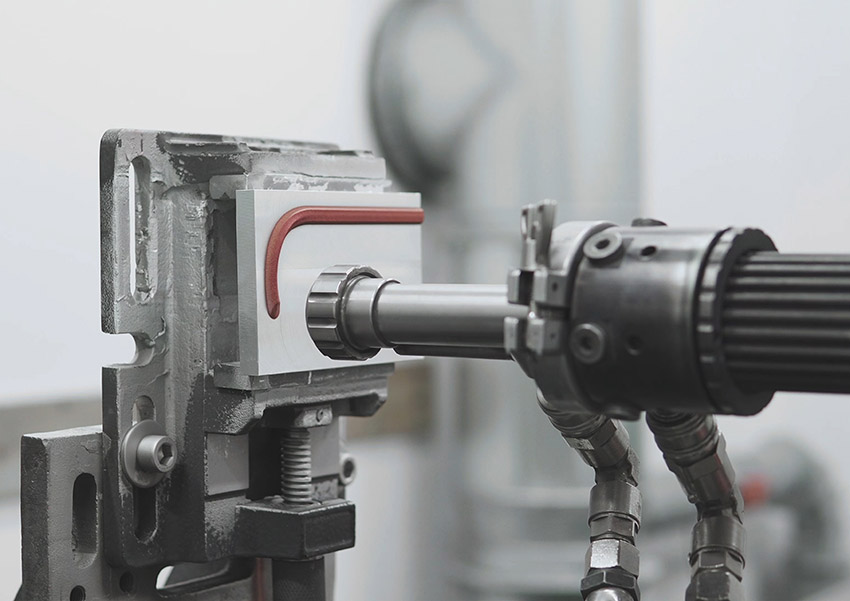
E.E: At what stage is the market where you are currently active?
Impact Innovations: As mentioned in the beginning we serve a huge variety of markets. Most of them already use mainly other thermal spray or additive manufacturing technologies. But our customers are fascinated from the superior advantages of cold spraying and its capabilities. Sometimes existing technologies already reached their limits and with cold spraying we can surpass them or lift their processes to the next level regarding quality, material properties, efficiencies or simply production costs. In other industries new or changed requirements lead to a change of mind and initiate a search for new technologies. Therefore, we start projects in many cases with R&D departments from our customers to explore the opportunities. Supplementary we see an increasing demand from different industries for the past 3-5 years, because cold spraying left the R&D stage and enters serial manufacturing in more and more industries. Therefore, we triple our manufacturing and office capacity at the moment and we look forward to moving into the new buildings in the upcoming weeks.
E.E: What can you tell us about market trends?
Impact Innovations: We can see an increasing electrification not only in the automotive industry. The unique and outstanding coating properties of copper, silver, aluminum, nickel etc. without any process-related oxides provide best thermal and electrical conductivity. Next to that there is an increasing demand for wear resistant and corrosion protective coatings as new and lighter materials are used in many products, which require coatings with that characteristics or reinforcement. The possibility of spraying bi-metallic products offers many new opportunities as well like for the aerospace business, where many new companies have been founded to start space travel or launch small satellites.
E.E: What are the most innovative products marketed?
Impact Innovations: The launch of our new product generation Impact Cold Spray System EvoCSII was a major milestone. This system offers many advantages for industrial manufacturing regarding process automation, process safety and flexibility. It is suitable for 24/7 operations with permanent documentation of all process related data and for an integration of a higher-level control system. The full modular system architecture provides all flexibility for customer specific requirements and later modifications. Next to that there are continuous developments in applying new materials and increasing coating properties and process efficiencies. Of special importance have been our developments on tungsten-carbide-based coatings for wear resistance and the spraying of aluminum without any nozzle clogging.
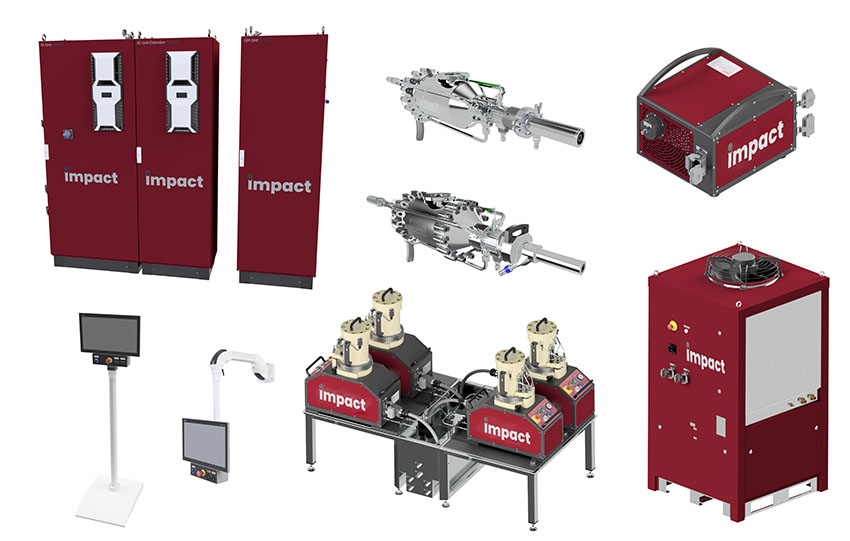
With our Impact EvoCSII system we are able not only to increase the line capacity, but also to coat with 2 guns e. g. discs on both sides in parallel with one spray system. By adding more powder feeders to the system, you can reduce changeover time even when you operate 2 powder feeders in parallel with a mixture of metals. Last but not least we expanded our capabilities for coating inner diameters by launching a rotating ID coating device. This means that the gun is rotating and can coat inner diameters of fixed pipes or cylinders above diameters of 70 mm.
E.E: What estimations do you have for 2021?
Impact Innovations: For 2021 we expect the best sales year in the history of Impact Innovations. The increasing demand for cold spray systems is continuously growing. Adopting to that market need, we expanded our staff and already started harvesting the fruits of our increased project activities. With the strengthened manpower, our enlarged capacities and our latest developments Impact Innovations is facing a bright future as the global technology leader for industrial cold spray. We are sure that our existing markets continue growing and that we further develop new markets with high potential for metal additive coatings.
IMPACT INNOVATIONS GMBH
Tel.: +49 8636 695190-0
Fax: +49 8636 695190-10
Email: info@impact-innovations.com
Web: www.impact-innovations.com