infeo was founded 2010 emerging from a university research project on waste logistics optimization in Austria. Since then, the company has developed a comprehensive all-in-one hard- and software solution for digitalization, automation, and optimization of processes in logistics, planning and workflow through the branch of waste economics.
Infeo’s solution provides tools to capture data from moving and stationary assets such as garbage trucks or intelligent bins, transforming them into data models which can be analyzed and optimized. Their customers are municipalities, associations and waste collection companies in all german-speaking countries.
Interview with Florian Reischer, CEO of infeo.
Easy Engineering: What are the main areas of activity of the company?
Florian Reischer: We solely operate in environmental services, which makes us both focused and expertised in that area. Aside from waste logistics we also provide a telematic and tour planning solution for winter services which is usually related in the same department of municipalities. In both branches we provide full scaled hardware and software solutions for fleet monitoring, analysis, planning, route optimization and navigation.
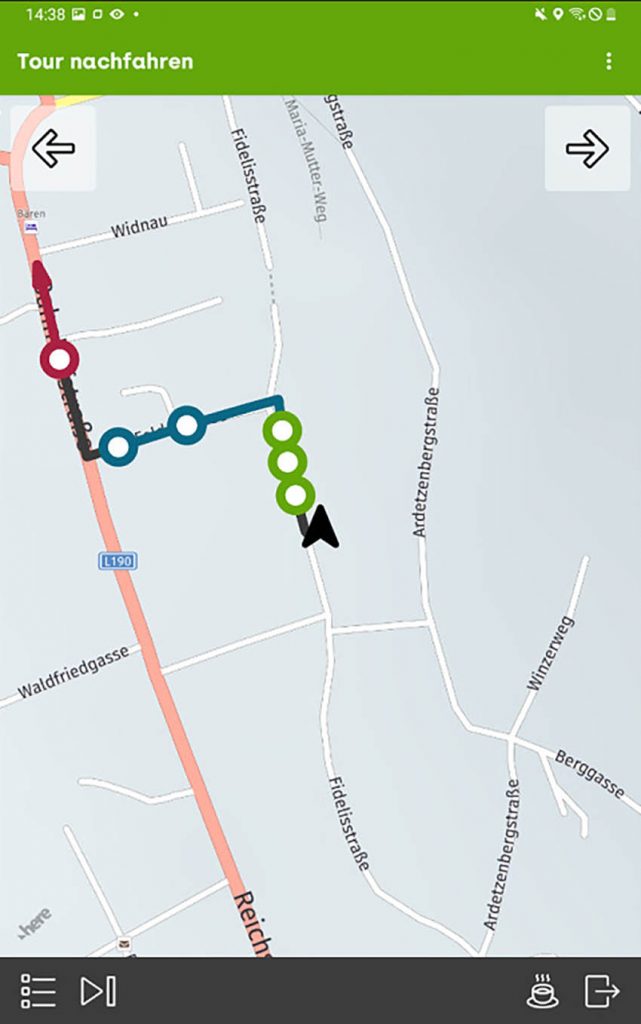
E.E: What’s the news about new products?
F.R: Our newest product is our android app, which can gather information from municipal tours including data from truck-mounted sensors such as scales, RFID-systems and lifter units on the truck’s body. The app captures all data and sends it to our web platform where it can be analyzed and processed in various manners. The GPS-tracking can then also be used to provide guidance routes for navigation, so that new drivers can follow a predefined collection tour and not miss any bins to be collected. The app is in use by approximately 200 vehicles around german speaking countries, and since Android allows us to implement multilanguage environments, we are on the edge of stepping into emerging markets such as Eastern Europe.
E.E: What are the ranges of products?
F.R: We provide solutions for waste logistics and winter services only. Within those branches, we provide a full range product and consulting service, from vehicle procurement to software and application design, as well as accompaniment of tenders for municipalities.
E.E: At what stage is the market where you are currently active?
F.R: In german speaking countries, the digitalization boom has kicked in for about 5 years already. The transition from analogue business processes to paperless offices and logistics is part of our consulting routines. The ones which have already achieved a digital business are on the verge to “intelligent autonomous” systems, meaning they are equipping assets with technologies such as fill-level-measurement to make decisions not by people, but by self-learning machines, to improve the on-time-on-demand decision making in logistics.
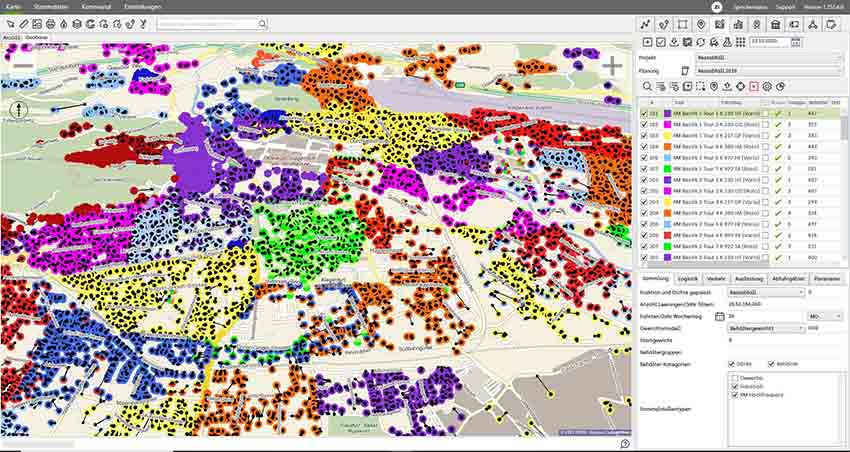
E.E: What can you tell us about market trends?
F.R: We see a significant motivation in terms of digital service confirmation and documentation. In Austria for example we provide a documentation and analysis toolkit for “ARA” (Austrian Recycling Agency) which captures all collection tours concerning package-material (plastic, paper, metal) and is capable of generating reports on distances, durations and performance parameters for each tour, without any user-interaction. Another trend is about transparency in polluter fair billing, which means to measure the amount of waste collected on a specific customer site and only taking the actual amount into the receipt. This has massive influence on the waste separation morale of customers and improve the overall quality and pureness of the collected material.
E.E: What are the most innovative products marketed?
F.R: The biggest innovation of this year is our brand new optimization toolkit that allows us to optimize a set of versatile mathematical problems in waste logistics such as classic residual collection tours, pick-up-and-delivery routes (e.g. slip-containers) also bulky waste tours and vehicle routing problems with time windows and other restrictions. The toolkit was developed by one of our employees during his master thesis in Computer Science. It will be integrated into our standard software by the end of this year and provide a new range of optimization capabilities.

E.E: What estimations do you have for 2022?
F.R: In 2022 we will reach a fleet size of 400 vehicles equipped with our wide range of hard- and software. Also, we will finalize the transition from pre-existing desktop-applications to full-range functionality in our web platforms for both winter services and waste logistics.