InfraCore® Company is an engineering office specialized in designing, simulating, prototyping heavy load bearing structures made with composite materials, also called fiber reinforced polymers.
Specifically, the structures the company designs are based on the InfraCore® technology, a patented way of building a sandwich-like panel that makes use of the so-called Z-layers. The essence of InfraCore® is that continuous fiber layers start in the top skin, continue through the core and end in the bottom skin, thereby creating an oblique layered structure (i.e. each individual layer makes a slight angle with the horizontal plane as a result of the stacking).
InfraCore Company has two main focuses: Firstly, they work based on a licensing model, whereby InfraCore offers interested parties the possibility to either just sell, or design, manufacture and sell products that contain the InfraCore® technology. The partner companies can either be an agent, whose sole responsibility is to handle marketing and sales operations, or a full licensee who can handle a portion of / the complete manufacturing process. Today their InfraCore® technology is licensed in USA, Canada, Australia and Europe.
Secondly, InfraCore Company aims to find new product-market combinations where the InfraCore® technology provides clear, distinct benefits, such as, among others, increased robustness and damage tolerance, resistance to environmental factors, light weight, quick installation times and low hinderance.
Interview with Teodor Gheorghe, Senior Engineer at InfraCore Company.
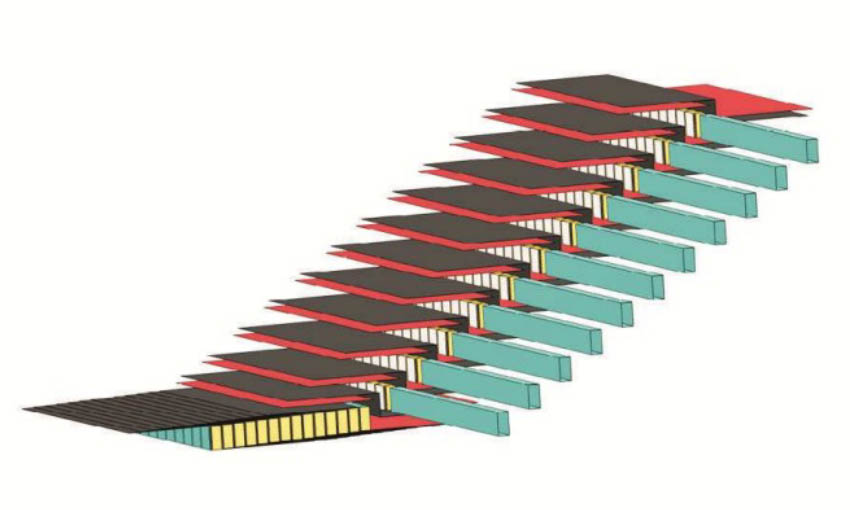
Easy Engineering: What are the main areas of activity of the company?
Teodor Gheorghe: The company focused on the infrastructure sector for several years, however, that is now taken over by most of the licensees who mainly supply InfraCore® Inside pedestrian and traffic bridges as well as lock gates in many countries.
The current focus of InfraCore Company is spread between the maritime, energy and the building sector with several specific applications currently under investigation.
E.E: What’s the news about new products?
T.G: We are currently focusing on InfraCore® balconies for residential apartment buildings, primary structural elements of bulk carriers, and railway bridges.
As a sidetrack, we are currently investigating ways to recycle FRP products at the end of their lifespans. The current state of the art involves some form of mechanical processing (i.e. shredding) followed by a continuous chemical process (such as pyrolysis). We are pursuing the pyrolysis option, but are interested in assessing the viability of a batchwise process in which a full product is introduced at the start of the process, with no preliminary mechanical processing up front. We believe it is important to consider what happens to a product throughout its lifetime and to have relevant solutions.
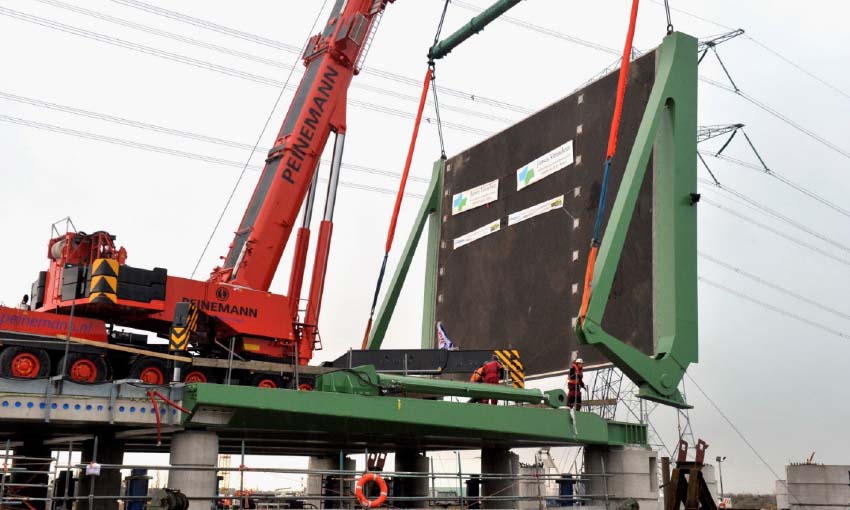
E.E: What are the ranges of products?
T.G: In general, we are willing to collaborate with new or existing partners for the design of any product as long as the benefits of using InfraCore® are clear and give an advantage compared to the current solution, either by expanding the market with a higher load bearing capacity product or opening up a new market segment.
Specific products include, but are not limited to pedestrian and traffic bridges, lock gates, helicopter decks and road mats, all containing InfraCore® Inside.
E.E: At what stage is the market where you are currently active?
T.G: We pioneered the application of load bearing FRP structures in civil engineering, building our first FRP bridge in 1996. But the infrastructure market has slowed down in recent years, not aided by all the supply chain issues that arose from the Covid-19 pandemic. However, it has stabilized recently, and extensive growth is expected for the next years in NL. InfraCore® even improved its position in market.
As for the maritime sector, there has been a clear decline in funding available for R&D within many major companies and thus, although there is a clear interest and enthusiasm in getting composite parts on board ships, the funding definitely is slowing down the process.
For the building industry, we see an increase in interest in the use of load bearing FRP structures, particularly due to logistical advantages related to transportation and installation at a particular stage.
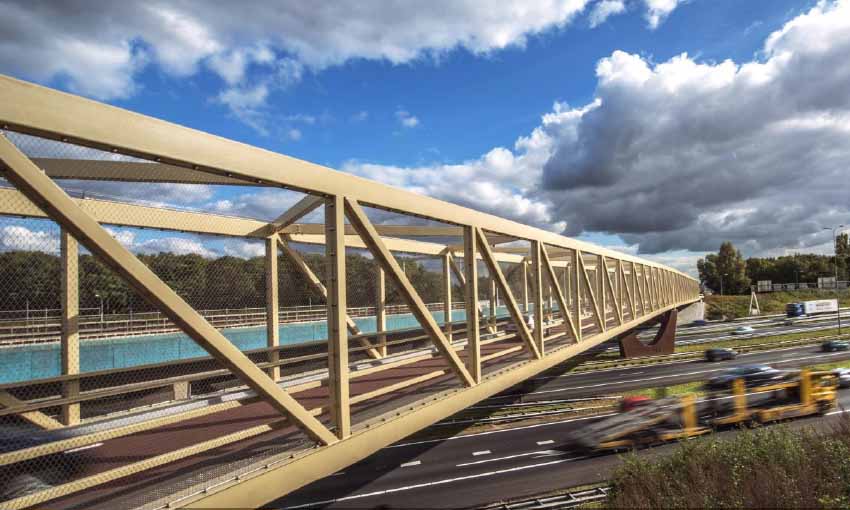
E.E: What can you tell us about market trends?
T.G: FRP will be the third construction material, next to steel and concrete for heavy duty structures. And that will happen much faster than expected. Our licensees already realized over 1700 structures, such as lock gates, heavy traffic bridges in several countries all over the world.
The application of InfraCore® in maritime and building applications is expected to grow rapidly once the first steps are taken and large companies with a significant impact on the market are willing to follow along through the development and approval process.
E.E: What are the most innovative products marketed?
T.G: The fact that FRP is being used as load bearing material in bridges and lock gates was pioneered and developed by our company. The way we see it, the InfraCore® technology in and of itself is an innovative principle compared to traditional sandwich panels and therefore, any product built this way can be considered innovative.
As mentioned above, the primary focus of our licensees is bridges. A few examples of the most innovative ones are given below.
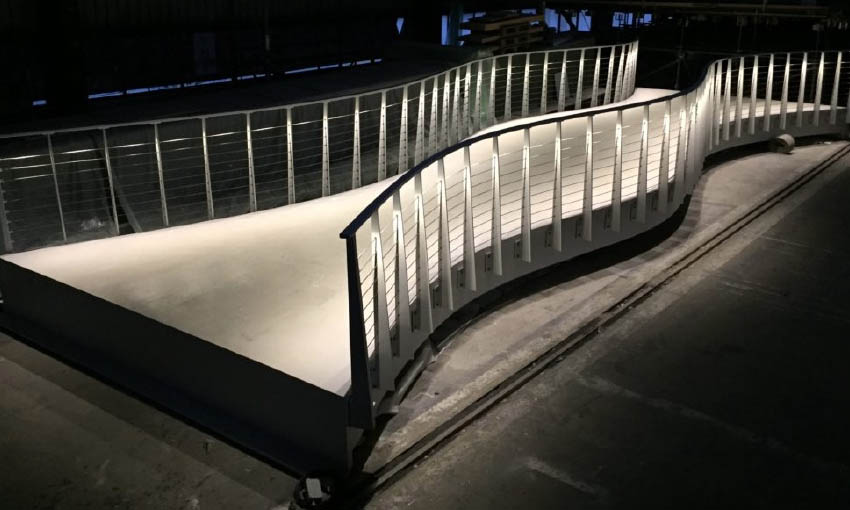
Another eloquent example is the primary structural elements of a SOLAS, 85m offshore patrol vessel that were designed and built fully with composite materials and are based on the InfraCore® technology. All load bearing elements (i.e. helideck, tween deck, hull, and the connections between them were engineered, built and tested according to class requirements.
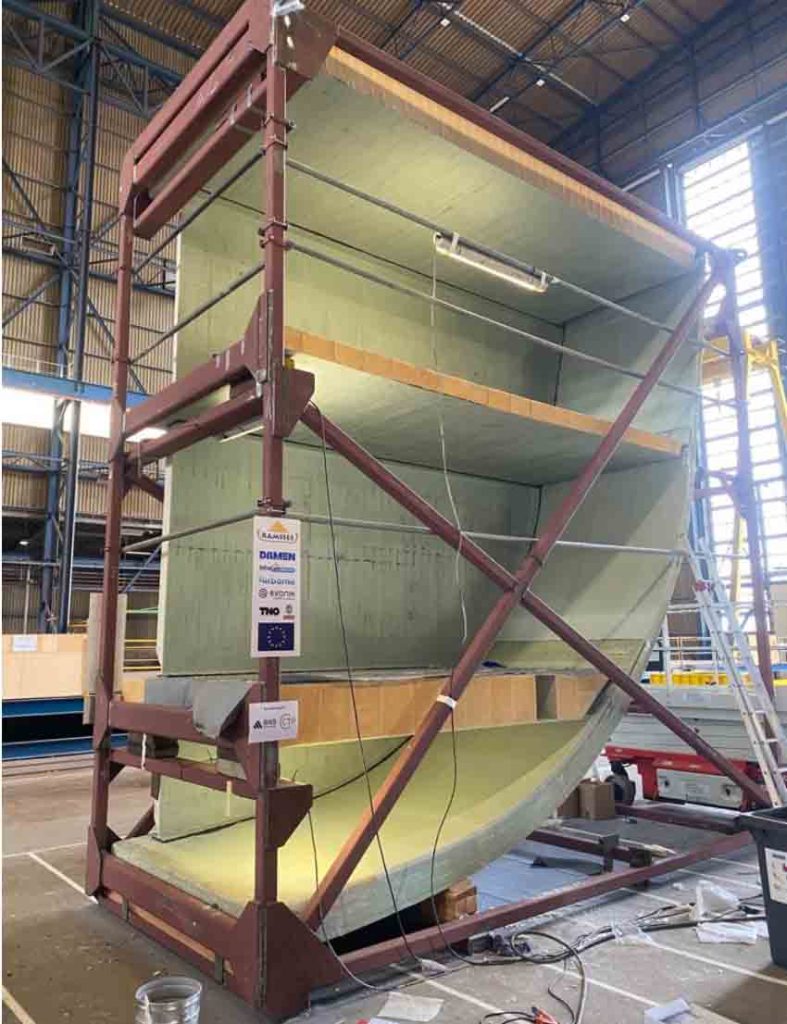
Other, older, but extremely relevant structures are the largest lock gates in the world (13×6 m each, holding back up to 8 m of water), currently in use in the Netherlands upstream from Rotterdam. There is a high risk associated with the failure of these gates and yet the authority realized the benefits of an InfraCore® structure and approved its use in this project.
Finally, there are many existing bridges in need of refurbishment and or upgrading. For this reason, we have also developed a process through which an existing, either concrete or steel bridge can be improved, its lifespan can be extended, it can be widened or any number of other changes through the use of an InfraCore® deck on top and carbon fiber strips along the bottom.
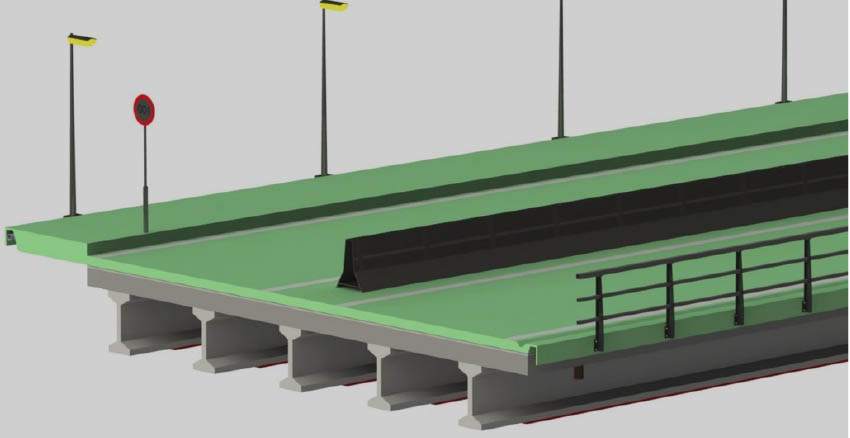
E.E: What estimations do you have for the rest of 2023?
T.G: InfraCore® technology will gain a foothold in the maritime sector with load bearing elements, as the groundwork has already been completed through a few European projects.
It is important to understand the snowball effect of such technologies, once the first product is accepted, the floodgates will open. We saw this with infrastructure, we are sure we will see this with ship building. We are keen to see where these developments will lead InfraCore Company.