UIBS Teamwork is a team of programmers, managers and technologists who created, develop and implement POsystem – the world’s first autonomous decision-making system for production management, automating planning processes and direct resource management in production halls.
IPOsystem was developed over 12 years ago together with some production plants as a response to their main problem which was the volatility in the area of resources and production orders and where the use of a classic system based on scheduling would not work. Currently, the system operates in 60 factories, controlling the work of over 12,000 employees and generating approximately 50,000 operational decisions per day.
What is IPOsystem and what distinguishes it from other production management systems?
The most popular production management method is based on scheduling. To put it simply, production plans are created and then implemented by production supervision personnel who issue work orders to employees. In this way, production can be managed both by means of a spreadsheet in which we create a production plan, and by means of advanced APS class IT systems, the purpose of which is also to prepare a production schedule. The implementation of each such plan is possible only in one case – when in real business and production conditions all its assumptions can be met. If this is not possible, i.e. one of the assumptions of the plan has not been met, a correction should be made quickly and a new plan should be simulated. In practice, in the case of high volatility of planning parameters, planners cannot keep up with the development of new plans. In order to speed up scheduling, the creators of APS systems have developed a number of simplifications. As a result definitions of times of technological operations do not take into account differences in the actual skills of employees, production-related operations such as preparation of documentation, preparation and release of materials from the warehouse, interoperational transport, quality control activities, etc. are omitted in the scheduling process. The availability of employees is omitted when creating a plan for production centers, which causes downtimes and micro downtimes as a result of the need to “manually” manage these areas by managers. In addition, there is a tendency to “freeze the plan” for a certain period of time in order to avoid volatility related to the status of orders (new orders, changes in dates, changes in quantities), which means that companies lose flexibility, which is so important in the current economic conditions.
“Flexibility” is the key word here.
IPOsystem is one of the world’s first MOM (Manufacturing Operations Management) systems of the new generation, the operation of which is based on an autonomous decision-making system (ADS).
IPOsystem automates planning processes, direct resource management and automatic collection of precise data on the actual course of production processes.
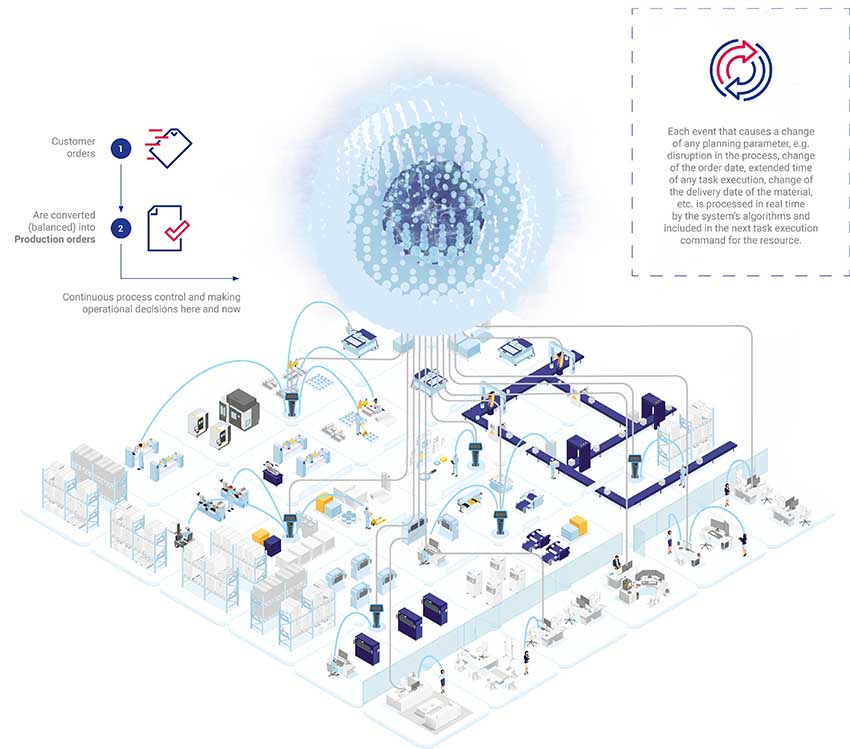
IPOsystem makes real-time decisions regarding the sequence of implementation and selection of resources for individual technological activities. Each employee/team of employees, after reporting readiness to work in the system, immediately receives an order to perform the optimal technological operation at a given moment. The system only issues works that can be carried out at a given moment, indicating precisely the number of the production order, the work post where the work should be performed, technological details of the operation and the place where the necessary materials, semi-finished products and tools are located.
Each time an employee finishes work in IPOsystem, the next system decision is calculated and a command optimized for that moment is issued. Thanks to decision-making algorithms, the entire process of calculating and issuing each job takes no longer than 5 seconds. In this way, each employee in a factory controlled by IPOsystem works in the “Work – report – work – report – …. – work – report” procedure.
IPOsystem autonomously manages all production and production-related processes (e.g. preparation and release of materials from warehouses, inter-operational transport, quality control, etc.). The main goal of the system’s decision-making algorithms is the timely execution of production orders with the maximum use of the available time of all resources.
What barriers do you see in the wider application of decision-making systems? Aren’t potential users afraid that the implementation of the IPOsystem may mean the need to make a real revolution in the plant?
Bringing innovation to market is always a challenge. During these 12 years of our activity, we have held hundreds of meetings in various production plants. In most cases, our system would certainly improve production efficiency. Paradoxically, our system does not carry out any revolution in the area of production resources. The plant operates using the same machinery and the same people. In fact, the system restores normality to the company, freeing the plant from rigid planning procedures and giving a huge development impulse. Since the essence of IPOsystem is insensitivity to changes, and more precisely, reacting to any changes in real time, any new-coming resources like employees, machines or entire production halls do not require any particular modification of the system, it is enough to enter a new resource into the system and it is immediately taken into account when calculating and issuing the next job.

In our opinion, one of the barriers is the mentality of managers who do not want to give up planning or manual production control. An important barrier is also the general underinvestment of companies in modern IT systems. Many companies must first deal with the computerization of the entire enterprise and invest, for example, in an ERP system, and only then focus on individual areas of their organization.
If we are talking about the ERP system and other systems already existing in the plants, can the IPOsystem fit in and work with the existing software?
IPOsystem integrates with any ERP system with which it exchanges a number of data. So far, comprehensive integrations with systems from SAP, Microsoft, Oracle and many others have been implemented. Integration takes place via API and allows, among other things, to fully automate the creation of warehouse documents in the ERP system, creation of production orders in IPOsystem, transfer of technology and BOMs, transfer and ongoing updating of material stocks and orders for materials. IPOsystem is a unique addition to ERP systems that provides these systems with reliable data on the actual course and use of resources during the execution of orders.
What impact does the implementation of the system have on employees and management?
When it comes to managers responsible for planning or direct supervision, their role is changing. The goal of managers at IPOsystem is not to plan and then implement the production plan, but to solve technological and efficiency problems.
An important effect of the system’s operation is a change in the behavior of employees in the production hall. They try to complete the works issued by the system as soon as possible while maintaining the quality requirements. Everyone works at their optimal pace, and the system automatically optimizes the course of production processes in subsequent decisions. Thanks to this, we obtain very precise and real data on the skills and performance of each employee, which allows us to take appropriate improvement actions in places where such actions will bring the greatest benefit.
Is there any limitation in using the system in industry? What type of plants is the IPOsystem intended for?
IPOsystem is used in production plants of various profiles and production scales, both in unit and small-lot production, as well as in large-scale production. It is especially useful in factories where a large number of various production orders are carried out simultaneously, and in nest production. The modern market often requires manufacturers to deliver tailor-made products, and placed orders are often adjusted both in terms of technology and delivery times. Combined with the typical problems of each production plant, such as sudden absence of employees, machine breakdowns, disruptions in the supply of materials or bottlenecks, we get a production process characterized by high volatility, which makes managing such a process through planning ineffective. In such cases, an autonomous decision-making system will work flawlessly.