Today, 70% of the 2bio tons per year waste produced by humanity is still landfilled. Landfilling has often dramatic consequences on our environment like water pollution, soil contamination, plastic dissemination, air pollution and climate change.
Since more than 45 years, Keppel Seghers is offering world class ‘Waste-to-Energy’ technology to divert waste from landfills and produce renewable, local and clean energy plus recyclable materials from the residues of the waste to energy process.
With more than 100 waste to energy plants in Europe, UK, Middle East, China, India, Singapore and Australia, Keppel Seghers is one of the major global players in the field of waste to energy.
Interview with Benoit Englebert, Sales and Business Development Manager at Keppel Seghers Belgium NV.
Easy Engineering: What are the main areas of activity of the company?
Benoit Englebert: Our role in the inception of such ‘Waste-to-Energy’ plants is to develop and finance the projects, to design the Waste-to-Energy process, to supply core technology and associated performance guarantees, and to operate and maintain the plant during its lifetime.
E.E: What’s the news about new products?
B.E: We are continuously improving our core technologies to stay at the top.
In the meantime, we are developing new technologies addressing the new challenges of our society. Currently, the focus is on decarbonization and circular economy.
The last 5 years, we are doing pioneering work on the integration of carbon capture and utilization/storage in Waste-to-Energy plants.
We are also looking at the further improvement of recycling from the residues, to further increasing circularity of the waste to energy process.
E.E: What are the ranges of products?
B.E: Our core technology is the combustion grate SIGMATRIXTM. This is the very core of the waste to energy process: it is where waste is effectively converted into energy. It is the distillate of 45 years of return on experience with waste from different parts of the world like Europe, Qatar, China or Singapore.
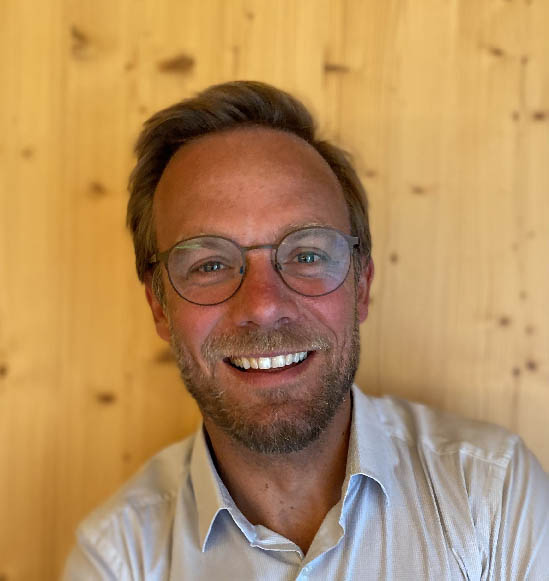
Benoit Englebert, Sales and Business Development Manager at Keppel Seghers Belgium NV.
We have different variations of the combustion grate: air cooled and water cooled in function of the waste quality. Indeed, waste in Qatar is different than waste in UK or Australia.
We also have an extensive and world class experience in every kind of steam boiler design and in flue gas treatment, which are the 2 steps downstream from the combustion grate in the waste to energy process.
E.E: At what stage is the market where you are currently active?
B.E: We are a global company. Depending on the geography, the Waste-to Energy market is at a different stage of maturity.
Northern and Western Europe, UK, South Korea, Japan, Singapore and North America are mature markets: retrofit is the main driver for new projects.
Southern-/Eastern Europe, China, South-East Asia, India, Africa, Central- and South America, Australia, New Zealand, the old Soviet bloc, Middle East are new markets: new Waste-to-Energy plants still need to be built. At Keppel Seghers, we are looking at markets and projects where we can add value and deploy our unique expertise in a repetitive way and sustained in the long term.
E.E: What can you tell us about market trends?
B.E: Waste-to-energy is a proven solution for the 70% waste which is still landfilled globally. So, there is a need sustained by this global issue, at different speed in function of the geographies.
Australia for example is quite actively developing new projects, like Middle East. However, in Russia, Africa and South America the development of waste to energy projects is still challenging.
Further, the actual energy crisis adds two new drivers for developing waste to energy projects: to generate affordable renewable energy, and to move away from fossil fuels.
Waste-to-Energy can help address those two challenges: it recognized to be a local, sustainable, partially decarbonized and renewable source of energy. We see lots of projects developing where waste is seen as an alternative to coal to produce industrial steam. Or projects where waste is used to divert from coal or natural gas for combined heat and power plants for electricity production and district heating production.
E.E: What are the most innovative products marketed?
B.E: In markets where Waste-to-Energy is new, our waste combustion technology is still seen as an innovative product.
In more mature markets, the most innovative topic is carbon capture. The potential of Waste-to-Energy to produce negative CO2 emissions, when combined with carbon capture starts to be understood, as it provides a way to accelerate decarbonization of our society.
The art there is in the smart integration of those two complex technologies, with a minimum impact on the CAPEX and OPEX and a maximum delivery of negative carbon emissions with a possibility to recycle carbon back to society.
E.E: What estimations do you have for 2023?
B.E: 2023 will still be a challenging year with high energy prices, disturbance of global supply chain, increasing interest rates yet a slower inflation.
However, those first two challenges will continue to accelerate two trends that the world needs: energy transition to a cheaper, decarbonized, renewable form and circular economy where we try to recycle more and use fewer virgin materials.
Those two trends will continue to develop and accelerate their deployment at different speeds globally.
Waste to energy is ideally placed as it offers a local, partially decarbonized energy.
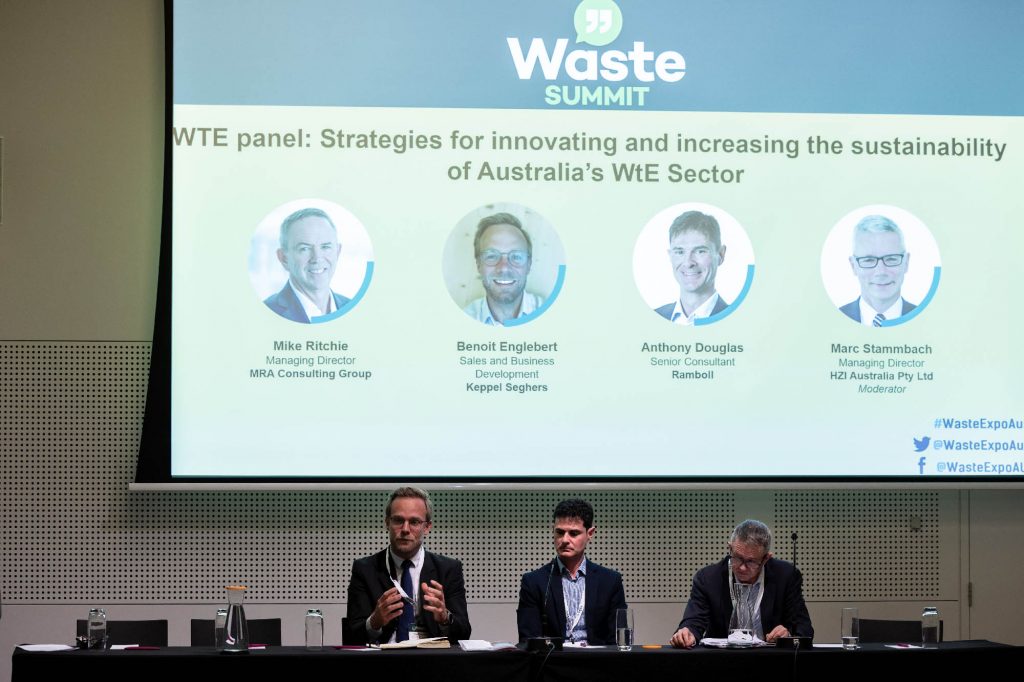
Waste-to-Energy contributes also to the circular economy by:
- Providing a hygienic service to the community by treating non-recyclable combustible waste and pollutants, which would otherwise end up in landfills.
- Providing secondary raw materials from incineration residues, a process known as material recovery and including aggregates, minerals, ferrous (steel and iron) and non-ferrous metals (copper, aluminium, zinc) and even precious metals, such as silver and gold.
- For instance, if we consider all the Waste-to-Energy plants in Europe, it should be possible to recover almost 1.2 million tonnes of iron equivalent to building 164 Eiffel towers, and about 250.000 tonnes of aluminium per year, i.e. the amount contained by roughly 8 billion smartphones.
- Recovering the emitted carbon from its processes through carbon capture technologies and producing further products and fuels from the captured carbon.