Since the company’s introduction in the 1920s, pneumatic actuators are still used in more than 340,000 Europe manufacturing facilities today and are responsible for over €4 billion per year in annual energy consumption and more than 50 tons of CO2 emissions in Europe – the equivalent of all passenger car emissions in Switzerland.
Founded in Switzerland by aeronautical engineers Salvatore De Benedictis and Ross Fleming, as well as former Vice President of the Swiss Federal Institute of Technology, Marcel Jufer, KOMP-ACT designs and manufactures innovative electric motion devices such as actuators and grippers destined for the automation machinery market. KOMP-ACT solutions can be retrofitted onto existing machinery for increased energy and maintenance cost efficiency or built-into new machinery for increased output and customization.
Through its technology, which is 10 times more efficient than existing pneumatics, the company’s vision is to help various manufacturers, from food packaging to aircraft, transition towards cleaner, more efficient actuators.
Further to the replacement of standard pneumatic actuators, they also see an important opportunity in line with industry 4.0 trends: the possibility to collect and monitor various data points such as machine performance, identify production line bottlenecks as well as enable predictive – instead of reactive – actuator maintenance.
Long term, the goal is to work with machine suppliers and end users on new concepts for flexible and fully programmable machines thus allowing live customization of mass produced items (product type and/or product size – an unique concept in the packaging machinery industry.
Easy Engineering: What are the main areas of activity of the company?
KOMP-ACT: The company is strongly investing in researching innovative design technologies using novel materials and manufacturing techniques to reduce manufacturing costs while increasing density force, which means making product smaller but keeping the available power constant. To do so, KOMP-ACT collaborates with the Polytechnic of Lausanne, local and international small, specialized firms.
Of course, the KOMP-ACT is also dedicating its efforts towards commercialization activities, for now mostly in European countries where there is a dense population of machine builders.
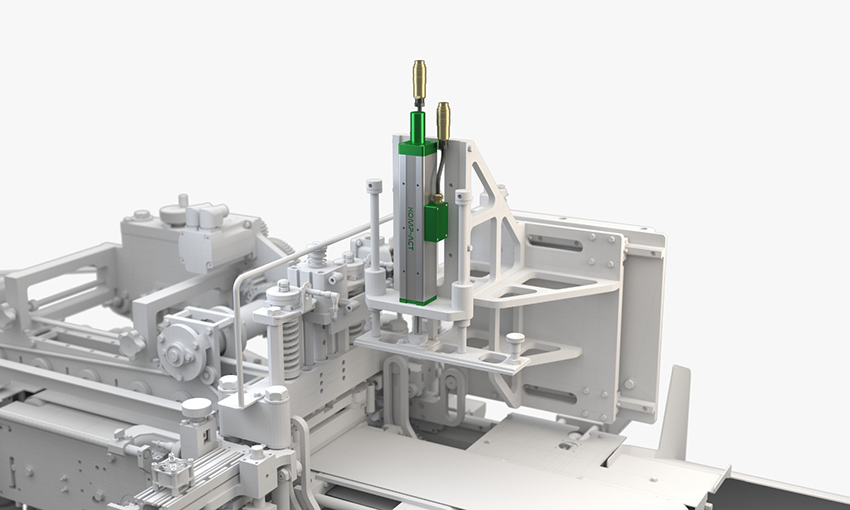
E.E: What’s the news for 2021 about new products?
KOMP-ACT: Thanks to the extensive client onboarding efforts in 2020, we will see the first KOMP-ACT-equipped hybrid and full electric machines hit the market in 2021.
E.E: What are the ranges of products?
KOMP-ACT: While our KOMP-ACT KLA actuators were officially scheduled to launch at Interpak 2020 back in May 2020, the event was pushed to 2023 due to the pandemic. That said, we forged ahead and will soon be launching a new series of electric actuators available in 4 models offering up to twice the power of our baseline products, different power and axial length as well as stroke length up to 240 mm.
In Q3 2021, we will also be launching our first electronic controller master module supporting EtherCat and Profinet fieldbus protocols allowing us to address customers who need to integrate multiple actuators through centralized programming systems.
E.E: At what stage is the market where you are currently active?
KOMP-ACT: While the machinery industry is a very large and fragmented, we noted that many clients in different segments have expressed a common need to “rethink” pneumatic machines but no solution was readily available to be integrated on their machines in an easy and cost-effective way.
Today, KOMP-ACT is the first and only solution of its kind which can replace traditional actuators in virtually any application – without redesigning any machinery.

E.E: What can you tell us about market trends?
KOMP-ACT: Main market trends observed are the following:
China’s ever-growing presence in the European and US markets is pushing western companies to be more competitive in their respective industries, thus driving the need for greater manufacturing efficiency, flexibility and customization.
Climate change awareness on a global stage, together with the increased end user awareness of increased energy and maintenance costs related to pneumatics are driving the need for the electrification of automated manufacturing machines.
Biodegradable materials – which are typically more fragile to handle – are becoming more present in the packaging industry which will drive the need for more sophisticated motion control solutions.
Several SMEs and start-ups are launching new products requiring more flexible processing and packaging solutions to grow with their evolving needs. Unlike compressed air infrastructure in their factories which take up larger footprints, an electric “plug & play” machine would allow for increased layout flexibility.
E.E: What are the most innovative products marketed?
KOMP-ACT: In response to overwhelming customer demand for a gripper solution that, along with our actuators, would effectively replace all pneumatics from “pick-and-place” machine applications, we will be launching an innovative gripper featuring our internationally patented linear motion technology in 2021 – a first in the industrial automation market.
Unlike most electromechanical grippers currently available on the market, the absence of a mechanical transmission on our solution allows for a significant reduction in size and weight, which, in turn, allows offer gripping times of up to 10 milliseconds and cycling rates of up to 600 cycles per minute – all of which are quite impressive given that robot arms typically cycle 60 to 80 products per minute on average.
Future versions of the grippers with different stroke and shape factors using linear motion technologies are currently under development.

E.E: What estimations do you have for 2021?
KOMP-ACT: The pandemic has particularly impacted the market in Q1 of and part of Q2 of 2020 as end user companies and machine suppliers remained in wait-and-see mode.
Ensuing Q2 of 2021 during which machine suppliers and end user companies were still in pandemic-induced “wait-and-see” mode, we have since seen a notable demand for non-food machinery such as mask-making, wet wipes, packaging of vaccines, etc.
Thanks to this new demand coupled with the order backlog stemming from Q1 and Q2 2020, we estimate that 2021 will be busy year ahead for the machinery industry. Manufacturing efficiency will be a key factor in fulfilling end user demand which puts KOMP-ACT in a privileged position.