Laserax provides turnkey laser solutions for industrial applications that include automation, vision, class-1 laser safety, fume management, laser process optimization, and so on. The lasers used in the turnkey solutions are designed at the HQ, so integrators and machine builders can use them in their custom solutions as well.
Laserax is based in Quebec, Canada and serves manufacturers from all around the world, including some of the largest automotive OEMs and foundries. The company has partners and subsidiaries all around the globe working with them to ensure smooth integration and quick customer support.
Interview with Pierre-Luc Marchand, Content Marketing at Laserax.
Easy Engineering: What are the main areas of activity of the company?
Pierre-Luc Marchand: Our areas of activity have widened over time as we slowly moved up the automotive supply chain. We first developed inline laser marking solutions for major smelting plants, then used our reputation in this industry to approach casting plants and automotive parts suppliers, where we began offering laser marking, laser cleaning, laser texturing, and laser welding.
Batteries, powertrain and drivetrain systems, foundries and casting plants, seating and stamping lines. Although we are serving other manufacturers, these are our bread and butter.
E.E: What’s the news about new products?
P.L.M: One of our fastest developing markets is the battery industry, so our recent products are for this industry.
For example, our new busbar laser welding machine is operated by robots and can replace dozens of ultrasonic bonding machines. This product is massive for battery manufacturers to allow them to enter a new era in terms of production speed and floor space usage.

Our R&D team has also developed an ultra-precise vision algorithm to clean EV battery cells. Battery modules have hundreds of cells that must be cleaned before welding. Laser cleaning is a great solution for this, but integration requires an unprecedented level of precision. Temperature variations, cell positioning variations, and other imprecisions need to be accounted for, and that’s exactly what we’ve achieved by working hand in hand with clients to develop the solution.
We also have a new ultra-high-power laser—a multimode pulsed fiber laser of 3kW that can clean large surfaces at unmatched speeds.
E.E: What are the ranges of products?
P.L.M: Laserax offers turnkey laser solutions for marking, cleaning, texturing, and welding. Our solutions are for industrial applications: workstations are operated manually, some automated machines are integrated directly on conveyor lines, and several are meant to be operated by robot arms.
Many of our manual workstations and automated machines use what we call a dual-position rotary table. They are used to process parts in hidden time while other parts are loaded, whether it’s by a robot arm or an operator.

E.E: What can you tell us about market trends?
P.L.M: Automotive OEMs and suppliers know that the times are changing. Governments all around the world are pushing for the electrification of the industry, and fossil-fuel vehicles are slowly phasing out with bans announced as soon as 2025.
We should see major changes before 2035. At that time, there will be bans on gas-powered vehicles in an important part of the world: the USA, Canada, China, the UK, Italy, Japan, South Korea, Singapore, and Thailand are just a few examples.
It’s no surprise then that automotive OEMs are massively investing in the development of electric vehicles and scaling up their production for this market. They don’t want to miss the boat and become irrelevant. At the same time, other areas are seeing less investments.
For example, we’ve seen a huge increase in the sales of our cleaning, texturing and welding solutions, as they’re used to develop new production lines. However, we’ve also seen a significant drop in marking for traceability, which doesn’t seem to be a priority for automotive manufacturers right now.
Hydrogen fuel cells could represent an important share of commercial electric vehicles. As of right now, the charging time for lithium-ion batteries is too slow to make them realistic for large vehicles like buses, trucks, ships, trains, and airplanes. Fuel cells are not as energy efficient as li-ion batteries, but they provide much faster charging times. As a result, there’s a lot going on with fuel cells right now: Airbus is developing airplanes powered by fuel cells; Germany has trains powered by Cummins fuel cells; Dana, Bosch, ZF, and many other automotive manufacturers have fuel cell programs.
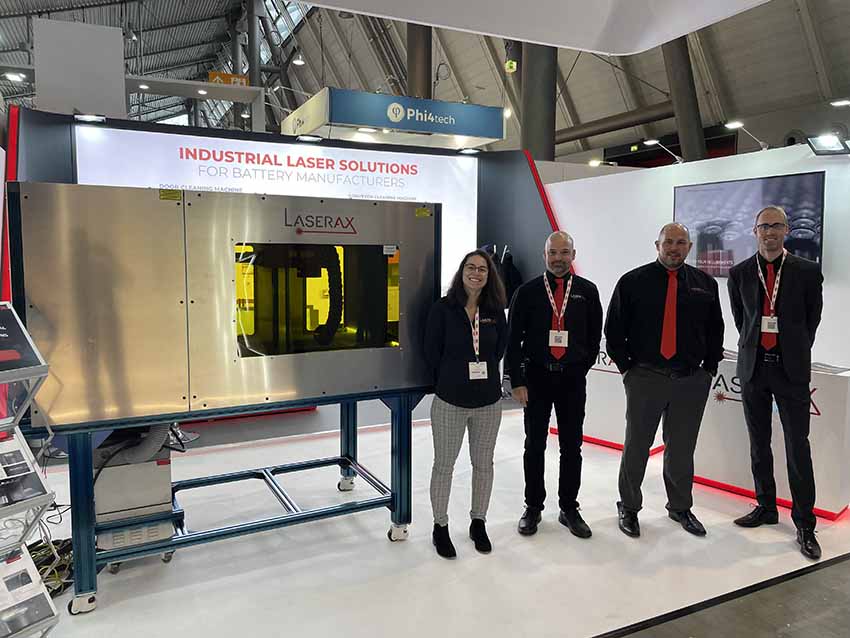
As for the automotive supply chain, we’ve all seen how it was disrupted in the last few years and how production was hindered. There were various causes: the microchip shortage, labor shortages, port disruptions, problems in inventory management caused by the global pandemic, and the list goes on.
As a result, many automotive OEMs no longer want to depend on their suppliers or on scarce resources. They are undergoing vertical integration of their supply chain to become self-reliant and produce everything they need. Consequently, many smaller automotive part suppliers are bound to disappear or get acquired by larger companies.
Conflicts between governments are also affecting supply chains. Relations are especially tense between the United States and China, where both nations are competing for economic, military, and supply chain domination. The recent Taiwanese conflict in is just one example of how the two countries are at odds. Nancy Pelosi’s visit to Taiwan was important to the US to protect its access to semiconductors, as Taiwan produces 92% of the world’s most advanced chips. Similarly, China has been securing cobalt supplies in Congo, where 70% of the world’s reserves are. Both materials are important to the automotive industry.
For companies like us operating globally, conflicts like these are creating major headaches. As opposing governments set up supply chain regulations, companies might need to set up different supply chains if they want to operate in different areas of the world. For example, companies wanting to serve Chinese customers may need to manufacture in China. Similarly, companies wanting to serve American customers may need to manufacture outside of China. For most companies, this probably means operating in one market or another—not both.

E.E: What are the most innovative products marketed?
P.L.M: That’s a good question for us! Innovation is what’s allowed us to build a great reputation and get referrals throughout the automotive supply chain.
Laserax got a reputation for designing sturdy laser marking machines that can operate with minimal maintenance in harsh environments like casting, extrusion, and smelting plants. Previously, lasers could not operate in those conditions.
We also developed an engraving process to create 2D codes that withstand shotblasting. This has allowed many parts manufacturers to implement complete traceability before shotblasting. In fact, we offer a full range of laser processes for complete traceability.
One of the most exciting innovations at Laserax is our new robot-assisted busbar laser welding machine. It uses several robot arms that simultaneously move and apply pressure on the areas to be welded while the laser head performs the welding from a distance. This patent-pending method overcomes mechanical movements that typically cause bottlenecks during welding.
E.E: What estimations do you have for the rest of 2022?
P.L.M: All over the world, governments want to attract battery factories. Programs will be announced by the end of 2022 for the upcoming year. These will include tax breaks and subsidies for investments in batteries and in the electrification of the automotive industry. Businesses will plan their budgets accordingly to spend the money in 2023.
Many manufacturers will jump at the chance to invest in batteries. Automotive OEMs have already started the transition. Ford recently laid off 3,000 workers in just one week to cut costs for its transition to electric vehicles.
For Laserax, it’s an opportunity to be part of these programs, not only through our laser technology, but also by working with battery and automotive manufacturers to develop solutions to technical challenges no one’s ever faced before.