With many years of experience in research and innovation for the lightweight design of the future, LKR Leichtmetallkompetenzzentrum Ranshofen of AIT Austrian Institute of Technology is a leader in the development of high-quality light metal alloys, their sustainable processing through to the development of functionally integrated lightweight components and their recycling.
Thanks to this holistic research approach, which is supported by simulation methods, new technologies such as wire-based additive manufacturing of aluminum and magnesium as well as innovative casting and forming processes are emerging. Based on these new methods and know-how in the entire processing chain, the lightweight components developed by the LKR are widely used in the automotive and aviation and aerospace sectors.
The LKR Leichtmetallkompetenzzentrum Ranshofen is characterized by an excellent team of scientists, the highest level of methodological expertise, and many years of experience in managing international research projects.
Interview with Christian Chimani, Managing Director at LKR.
Easy Engineering: What are the main areas of activity of the company?
Christian Chimani: LKR Leichtmetallkompetenzzentrum Ranshofen (Competence Unit for Light Metal Technologies Ranshofen) specialises in the development and processing of high-performance light metals. The focus is on the design and sustainable, efficient production of vehicles and components. Lightweight vehicles consume less energy, produce fewer emissions and increase range. In order to achieve this aim, LKR researchers investigate novel light metal materials (e.g. aluminium, magnesium and titanium alloys) and associated forming technologies complemented by highly specialised material characterization and simulation methods. One particular field of research focuses on wire-based additive manufacturing, one of the most promising methods for 3D light metal printing.
The distinctiveness of this Competence Unit is that its expertise covers the entire light metal process chain, from alloying to casting and forming as well as process and lightweight design, including the simulation tools required for all these processes. This allows materials to be tailored exactly to customer requirements, while also ensuring sustainable and energy efficient processing – with the ultimate aim of creating new light metal materials with advanced characteristics for future applications.

E.E: What’s the news about new products? | What are the ranges of products?
C.C: Materials Development
LKR researchers have long-standing experience in the design and processing of light metal alloys which meet the increasing demands on materials. Of special importance are material properties such as strength, corrosion and fire resistance, joinability, crash behavior and processability. Our services include adapting and developing alloys to meet customer requirements, the thermodynamic and thermokinetic simulation of alloy systems, casting, homogenisation, extrusion, the forging and deep-drawing of test alloys, development of customised heat treatments for increased strength and finally, microstructural and mechanical characterisation.
Casting Technology
We explore different casting technologies for innovative light metal alloys so as to develop cost and energy efficient solutions which meet the high quality demands required by our customers, while keeping the carbon footprint as small as possible. LKR has facilities for horizontal and vertical continuous casting, mould casting and low-pressure die casting on a semi-industrial scale and also operates an industrial-scale high pressure die casting plant. Our services include simulation-based component and process development, tool development, prototype, pilot and small-batch production, and the provision of plant capacity. This allows us to offer holistic solutions – from the idea through to the final component for series production.
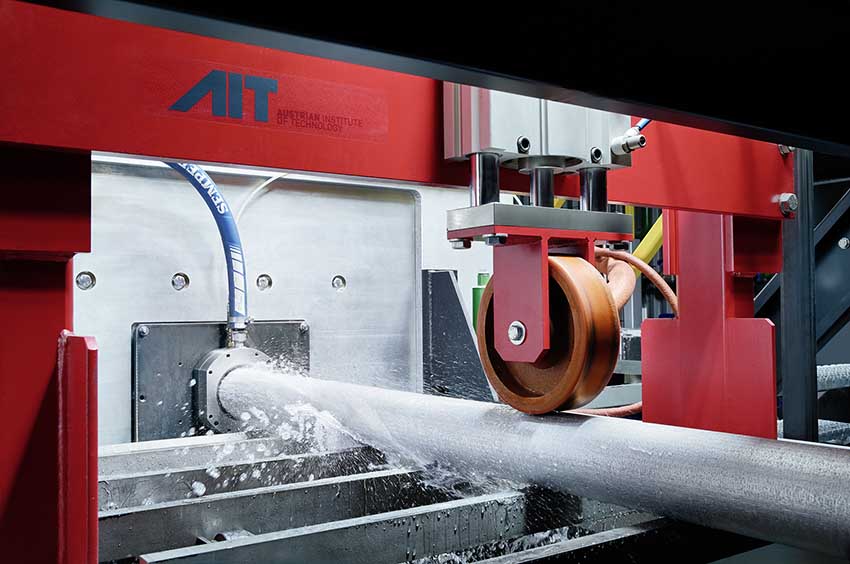
Forming Technology
Our research leads to more efficient, stable, productive and cost-effective forming processes for novel light metals and the optimal use of modern materials. Our services include the development of new forming processes on a laboratory and semi-industrial scale, optimisation of process chains in sheet and bulk metal forming and finally, extrusion, forging and rolling at semi-industrial facilities. LKR experts are also working on the optimisation of essential associated heat treatment processes, the digitalisation of the individual process steps, and data evaluation.
Wire-based Additive Manufacturing
We explore new methods of wire-based additive manufacturing, a seminal method for the 3D printing of large light metal components. The manufacturing process is controlled by computer, without the need for forming tools. Our services include the development of special light metal wires, concept development and the production of demonstrator parts and prototypes. The LKR team has expertise in optimising hardware and processes so that components can be manufactured through direct metal deposition at comparatively high deposition rates and with theoretically unlimited component size. We also conduct research into combined process and material optimisation and analysis using numerical methods.
Numerical Simulation
Simulations can help to predict, optimise and better understand material properties, processes and component behaviour in practice. This numerical approach partly or completely eliminates the need for expensive, energy-intensive trials and machine resources in the development phase. Our expertise in the field of numerical simulation ranges from new theoretical concepts such as model order reduction through to application-oriented simulation – always taking into account the end users’ processes and components. Our services cover the complete chain from atomistic alloy simulation to material modelling, simulation of casting and forming processes and component simulation. There is a key focus on linking the individual simulation steps in a through-process modelling approach in order to understand and predict the effects of individual process steps on subsequent processes and on the final material quality.
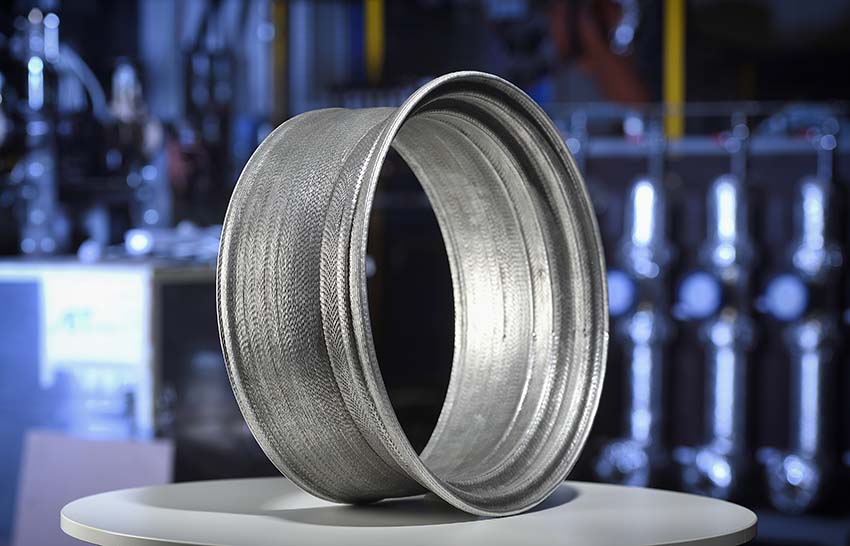
Material Testing and Characterisation
LKR offers a wide range of methods for microstructure, material and process characterisation using cutting edge methods. We provide material, process and product analysis and damage evaluation, which helps us verify and validate our research while also offering our clients a broad testing and characterisation portfolio. We can draw on a range of state-of-the art methods including spectrometry, dilatometry, notched impact testing, deformation analysis, mechanical material testing, fatigue testing, metallography, differential thermal analysis and electron microscopy using electron backscatter diffraction (EBSD) and energy dispersive X-ray spectroscopy (EDX).