Maestri designs and manufactures custom industrial furnaces and machinery complete with automation.
Interview with Andrea Maestri, Sales Engineer & Board of Directors’ member at Maestri Srl.
Easy Engineering: A brief description of the company and its activities.
Andrea Maestri: The history of our family company is rooted in ancient metalworking, which led our ancestors from forging weapons for the Duchy of Milan and the Serenissima Republic of Venice to the management of the water-powered hammer in Calcinato (Brescia) in the mid-eighteenth century. Since that our headquarter has never changed its original location, and in 1953 Mr. Pierino Maestri started a completely new business about maintenance and construction of industrial furnaces and ovens, the production plant grew visibly following the necessities of the new production. in 70 years of ovens many things have changed, but not the production process, which has always been carried out 100% within our company in all its phases. We have the means of production necessary to build everything we offer on the market. we offer solutions for gas or electric heating of materials. We specialize in heating brass, aluminum, and steel, offering specific machines for sectors where automated production is required. We collaborate with the main Italian and European press manufacturers to provide customers with perfectly integrated automatic lines.
E.E: What are the main areas of activity of the company?
A.M: We specialize in the construction of automatic furnaces for heating metals, we started 70 years ago with brass and its supply chain, which has always characterized the province of Brescia, and over the years we have expanded towards steel for the agricultural sector and aluminum, above all for the automotive sector. We have developed various skills in the application sectors of our machines, as we are convinced that it is essential to make our customers’ needs our own, to offer the most specific and effective solutions possible. Over the years we have designed and built many solutions for the most diverse fields, today we are specializing among other things in the treatment of rubber and techno polymers, thanks to the collaboration with some companies in the sector, leaders in their field Developing laboratory test machines with them or process machines for their end customers.

E.E: What’s the news about new products?
A.M: To be honest, each machine itself is new compared to the previous one. By internal policy, we do not produce in stock, but only on order to provide the customer only and exclusively with what is needed for its production. Often adapting what exists can be limiting and represent a limit for our customers over the years. This allows us to develop for each order the technologies necessary for the full fulfillment of the tasks required for each project. In more general terms, in the last 5 years we have concentrated on reducing and optimizing the energy consumption of our machines, applying inverters where partialisation of the electric power was required and on making the heating part more efficient and improving, in order to reduce the on-heating costs. To do this we have developed several new burners and chambers that differ in design and materials, developed and tested with our technology partners. All this combined with an intelligent management of the exhausts from the kilns, which are always equipped with thermal energy recovery. For example, these efforts have led to a 15% reduction in the consumption of our TGV brass series, which may not seem like much, but just consider that we are talking about the type of furnace with the lowest gas consumption per kg of brass produced on the market already before the improvements, which places us in an advantageous position compared to our competitors.
E.E: What are the ranges of products?
A.M: Our current production includes:
- Furnaces for hot forging of metal alloys (brass, aluminum, copper, steel, titanium)
- Furnaces for the thermoforming of plastics, rubbers, and techno polymers
We produce specific ovens for the fashion sector, designed and built to meet the specific needs of an ever-growing sector in search of perfection.
- Controlled cooling tunnels and chambers for the various materials
- Furnaces and systems for heat treatments of various kinds from 60°C to 1400°C, for metals, polymers, rubbers and various materials.
We can then create systems dedicated to the customer’s needs, of which there is no predefined series, but a tailor-made solution is studied to meet the requests of the same.
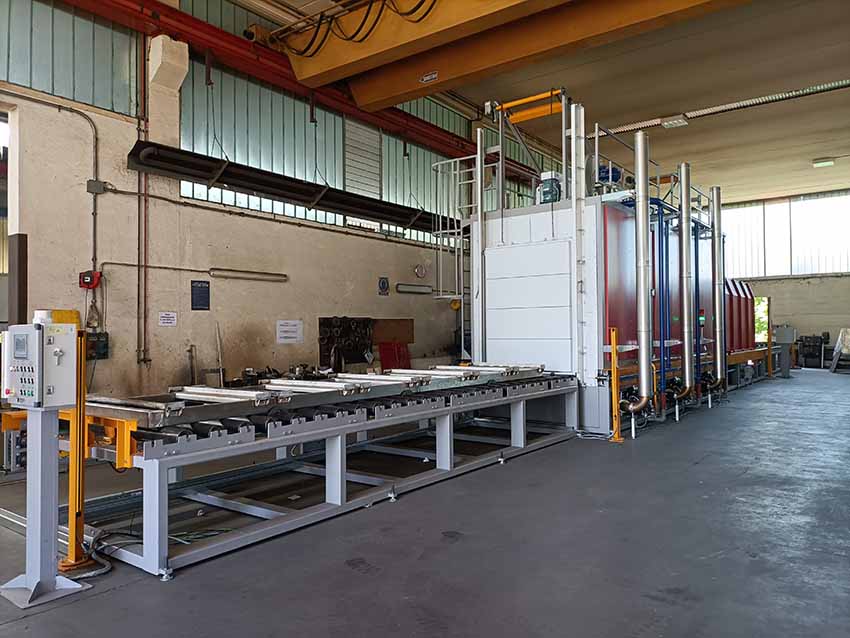
E.E: At what stage is the market where you are currently active?
A.M: The fields of application of our products are varied and the reference markets well differentiated. Each sector has moments of growth and stagnation, in recent years we have noticed generalized and continuous growth, especially in Italy. Some European technological sectors are in a phase of restructuring and reorganization, we therefore deem it physiological to reduce activities in these sectors, to give producers time to read the new market demands and set up the production lines in the appropriate way. As regards the historical sectors of application of our products, such as the thermo-sanitary sector rather than the water and gas valves and more generally the brass forging, the market has evolved in terms of quality and process efficiency, which has required important investments by our customers in new machines, capable of operating efficiently and keeping track of production, to give total and continuous control of the finished product.
E.E: What can you tell us about market trends?
A.M: As humanity we are experiencing a profound reform of our lifestyles, we have realized that recycling is essential and that materials that until recently seemed harmless are turning out to be poison for us and those who will come after. The market is reacting to this trend by seeking sustainable solutions to increasingly complex problems, materials have changed and continue to change. We have noticed a consistent growth in forged aluminum, as it represents a valid and, in some cases, superior alternative to steel, giving superior performance with much lower masses. Furthermore, having a density 2.5 times lower than steel and 3 times less than brass, in many cases it can represent an effective defense against speculation on the prices of raw materials.
We have found important investments in the agricultural sector, where our customers, manufacturers of tools and equipment for working the land, have developed new and more performing lines to meet the ever-growing market demand, also improving the quality of the finished products.

E.E: What are the most innovative products marketed?
A.M: The most innovative product we can offer today is certainly part of our family of aluminum furnaces. these are ovens built in modules with a chamber developed in the form of a cartridge.
The indirect heating technique (hot air) is optimal for aluminum: through this system the piece is heated gradually and uniformly in all its sections (even preformed pieces or multiple molding phases), and the final temperature of the component is the same as the air in the chamber where the piece is located. We therefore gain two significant advantages, a precise and homogeneous heating, together with a surface that is not oxidized at all and free from defects due to exposure to more aggressive types of heating. Heating indirectly with air allows you to stop your production (failure on the press, mold adjustment, etc.) and keep the material at temperature without the risk of dripping.
These features make the machine able to produce without any safety concern, even in delicate alloys (series 2000, series 7000), where the precision of the forging temperature is very binding to guarantee the proper mechanical properties to the molded part. In fact, process technologists strongly recommend the use of this type of heating specifically on parts for the automotive, aerospace, defense and in general where a high technological content is required. To meet the ever-increasing demands of our customers’ quality productions, we have developed a new chamber design, which combined with a new type of suction turbines guarantees an innovative, more efficient, and consistent air circulation. To achieve this, the heating process has been divided into phases, pursued individually in chamber modules (cartridges), giving us the possibility to apply the same concepts on machines of different sizes, being able to scale up the modules to obtain the same result on large and small machines. The machine is equipped with a management and monitoring software of the working parameters, which through a wide and intuitive HMI interface allows, through numerous and exhaustive illustrations, to have under control the working cycle immediately and to modify it according to the production needs. It also has an integrated library of parameters and working conditions, which is compared with the active program and generates feedback in real time that suggests to the operator whether the choices made are precautionary or jeopardize the final quality of the forged product.
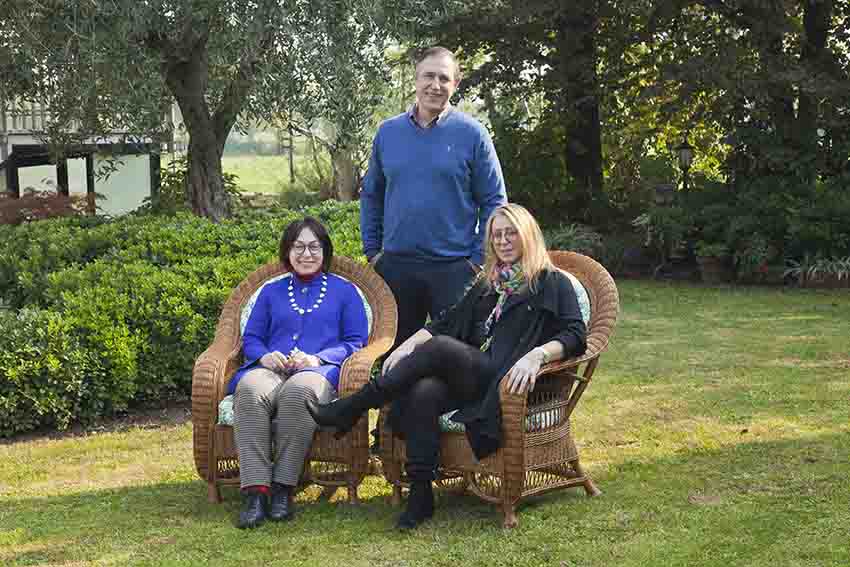
Maestri Family directors
E.E: What estimations do you have for 2023?
A.M: In our opinion, 2023 will probably be like 2022, with perhaps worse working conditions given inflation and the persistent difficulties in finding materials, especially electronic ones. But after all it seems that Europe and even Italy against the estimates are demonstrating a perhaps unexpected resilience and tenacity for such old ladies. We are optimistic and do not fear a slowdown in the market, which may not be so negative considering the rhythms and working conditions that are certainly not optimal, and which do not allow for more resources to be concentrated in research and development. A more streamlined order book and flexibility in the roadmap would certainly be less attractive from an economic point of view but would represent an important oxygenation for the technical department which could flourish even more.
We don’t have market strategies, and we don’t set ourselves turnover targets, we work every day to solve the problems that are posed to us by offering the best solutions available and doing our utmost to satisfy the customer. Economic results are the physiological recognition of technical efforts and do not always go hand in hand. improving as a lifestyle is our motto, and what we believe in, day after day always a little ahead.