Magnetic Analysis Corp. (MAC) is a company established over 90 years ago providing non-destructive testing (NDT) equipment for the metals industry, primarily producers of tube, pipe, bar, wire, and parts. The company’s focus is in-line automated testing systems ensuring the identification of defects that would impair the functionality of the product.
Interview with Michael Moist, Vice President – Sales at Magnetic Analysis Corp.
Easy Engineering: What are the main areas of activity of the company?
Michael Moist: We operate globally and specialize in the manufacture, sale and lease of high-speed testing systems using ultrasonic and electromagnetic technology. These systems identify and locate defects in the surface and body of metallic materials. Our solutions are found in high-speed manufacturing environments that produce welded and seamless tubular goods as well as solid bars and billets used in the oil and gas, power generation, automotive and aerospace industry, and small diameter tube and wire used in the medical industry. The users of our products specialize in selling in critical applications where a material failure can have catastrophic consequences. As an example – the testing of pipes used in off-shore deep sea drilling, the rotating components of an aircraft, or a stent for medical applications.
E.E: What’s the news about new products?
M.M: Our customers have a constant requirement for new testing capabilities that push the use of the newest technologies. The use of phased array is an example of technology that offers an increased capability of ultrasonic testing. Computer and software technology provide the customer with easy to interpret images of the material being tested highlighting the location, size, and orientation of the defects. Advanced algorithms can be used to process NDT data allowing the customer to determine material strength and integrity.
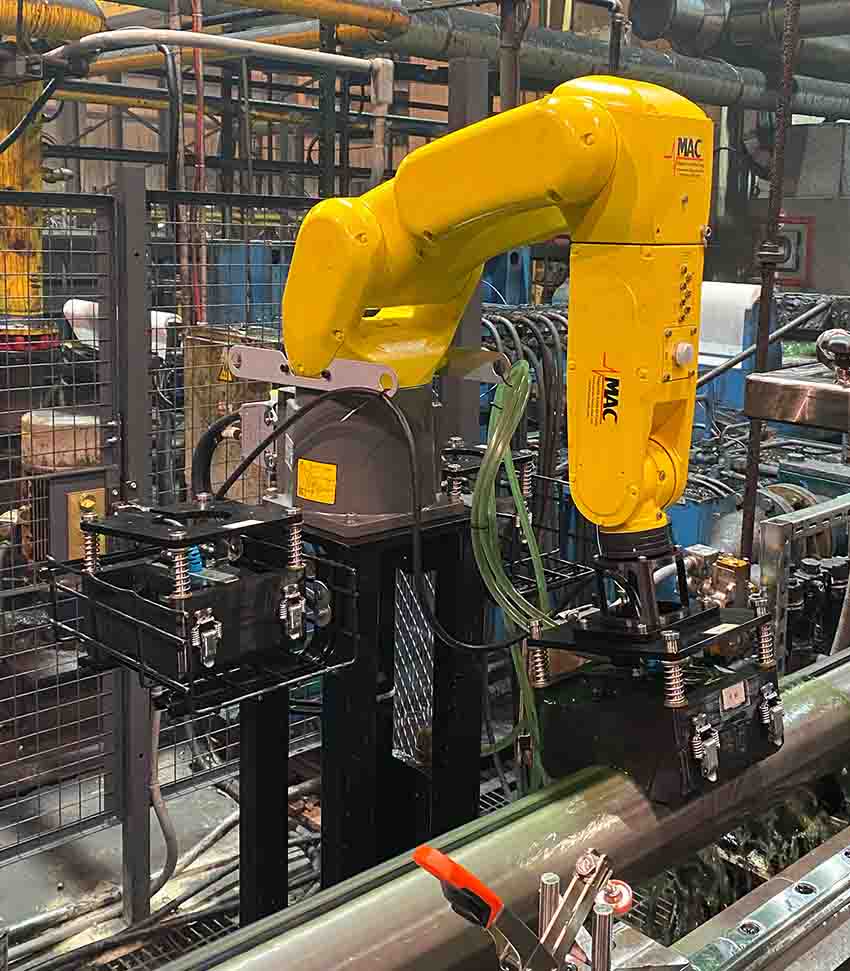
E.E: What are the ranges of products?
M.M: The range of our products starts with small magnetism detectors and compact instruments that detect surface, subsurface defects, hardness, and other conditions, and extends all the way up to very advanced, high-speed systems to test the surface and core of in-process materials in the manufacturing process. These sophisticated systems can use one or more test technologies to optimize the test results providing the user with the most accurate analysis of the product structure and fitness for use. MAC also provides comprehensive mechanical systems to convey and position the product through the test.
E.E: At what stage is the market where you are currently active?
M.M: The NDT market is well established and has been used for many decades as an acknowledged method for material evaluation. The market has advanced based on the ability of the computer/semiconductor industry to provide better technology in the design of the equipment. Size/form factor, post processing, data evaluation, archiving and user experience constantly are shaping the products in NDT.
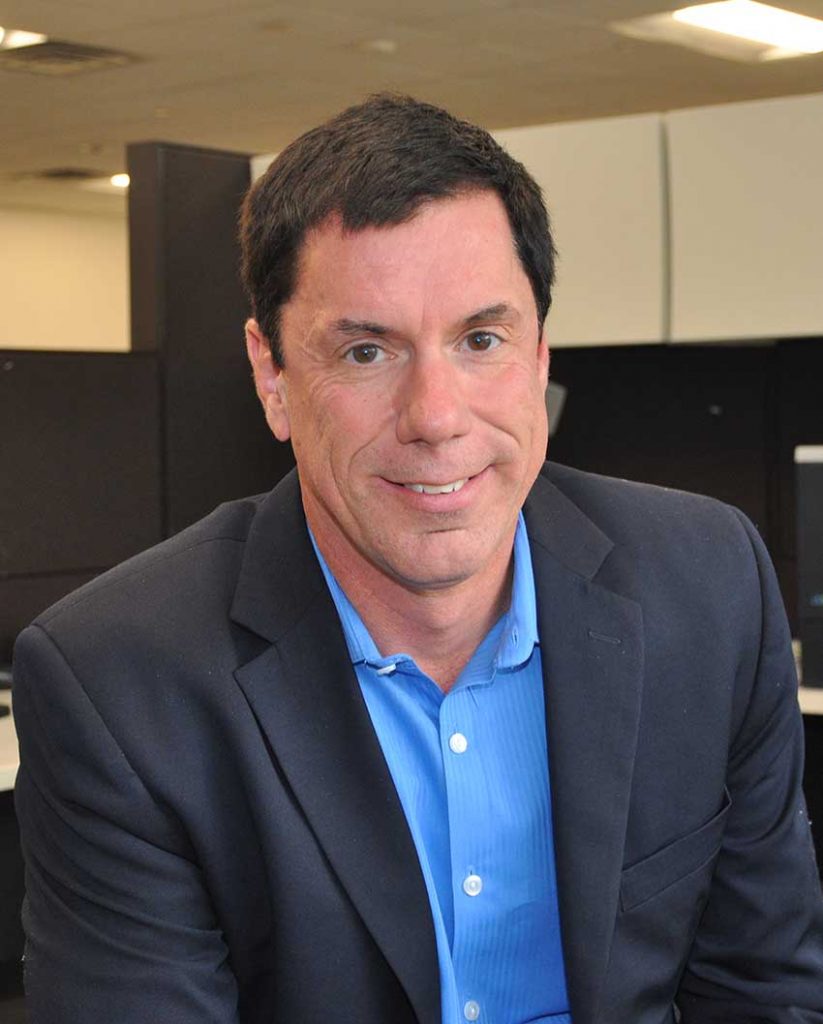
Michael Moist, Vice President – Sales at Magnetic Analysis Corp.
E.E: What can you tell us about market trends?
M.M: The need for processing more data that can easily be interpreted allowing for quick evaluation of the product is essential. This is especially true where obtaining experienced operators has become more and more difficult. Highly engineered mechanical systems are being replaced by off-the-shelf robotic solutions. Advanced testing techniques like phased array eliminated the need for highly complex mechanical systems and as phased array continues to advance, more complex processing allows for an easier user experience and more thorough testing techniques.
E.E: What are the most innovative products marketed?
M.M: Our most recent product that is very innovative from a user perspective is the robotic Echomac® UT- TW phased array ultrasonic system for evaluating ERW welds. It is innovative in that it provides a very cost-effective solution for the real-world issues of welded tube evaluation. The system allows for testing both the scarf removal tool and the weld for defects. This flexibility combined with an operator interface that is very easy to set up and evaluate data creates a complete solution for the market.

E.E: What estimations do you have for the rest of 2022?
M.M: The market for NDT post-Covid has been very strong. This is a natural reaction anytime the economy has had a prolonged down-turn. As companies came back on-line with existing production lines that have become older and obsolete, they want to optimize their ability to supply products. Supply chain issues allowed companies to maximize profits by producing when their competitors were unable to do so. Companies were pushing very hard to gain additional capacity and NDT is an important part of the process of fulfilling the end user’s requirements.