MELD Manufacturing is a woman-owned company based in Christiansburg, Virginia that was started in 2018 after more than ten years of research. MELD manufactures machines used in Additive Manufacturing (AM) – also known as 3D printing.
MELD is an additive manufacturing process for metal. It is a solid-state process, meaning the material does not melt during the process. Metal bar feed stock is inserted into a MELD machine and then – through rotation and pressure – it plastically deforms onto the build surface.
MELD can be used in additive manufacturing, coating applications, component repair, metal joining, and custom metal alloy and metal matrix composite billet and part fabrication. And MELD deposits material at least 10 x faster than fusion-based metal additive processes.
Since MELD is a solid-state process, it yields isotropic, fully dense parts with low residual stress using significantly less energy than conventional fusion-based processes. MELD deposited parts are not susceptible to porosity, hot-cracking, or other problems common to other technologies. MELD is a single-step process – no follow-on processes such as hot isostatic pressing or sintering are required.
The MELD process is capable of printing large metal parts at a scale not yet seen in the metal additive market because MELD is not restricted to small powder beds or costly vacuum systems. MELD’s open-atmosphere process makes it an ideal candidate for real-world manufacturing.
MELD prints metal faster, larger, and at higher quality than any additive manufacturing process.
Interview with Beth Wyatt, Director of Marketing at MELD Manufacturing.

Easy Engineering: What are the main areas of activity of the company?
Beth Wyatt: The combination of material freedom and scalability make MELD a revolution for a wide range of industries including aerospace, defense, turbomachinery, shipbuilding, and more. These industries look to MELD to provide an alternative solution to their manufacturing pain points that they experience with long lead time parts through traditional manufacturing methods.
E.E: What’s the news about new products?
B.W: MELD’s newest 3D metal printer combines additive and subtractive technology into one hybrid machine. 3PO, named after Star Wars droids like other MELD printers, was recently unveiled during Formnext in Frankfurt am Main, Germany. It features a 3-axis additive head with a standard 3-axis subtractive head. It has an immense cubic build space while eliminating the need for a separate subtractive machine.
MELD’s technology was selected by the US Army for their Jointless Hull Program to build the World’s Largest Metal Printer. It will have an unheard-of print capability of 20” x 30’ x 12’ (6.1m x 9.1m x 3.7m). The printer will be installed at Rock Island Arsenal in Illinois.
E.E: What are the ranges of products?
B.W: In addition to machines in standard sizes with cubic build spaces from 14.2ft3 (0.4m3) to 380ft3 (10.8m3), MELD also offers custom built machines. MELD also offers services to qualify material and parts along with contract manufacturing services.
E.E: At what stage is the market where you are currently active?
B.W: The market of industries interested in the MELD technology sees MELD as a potential game changer for the way they manufacture their parts today.
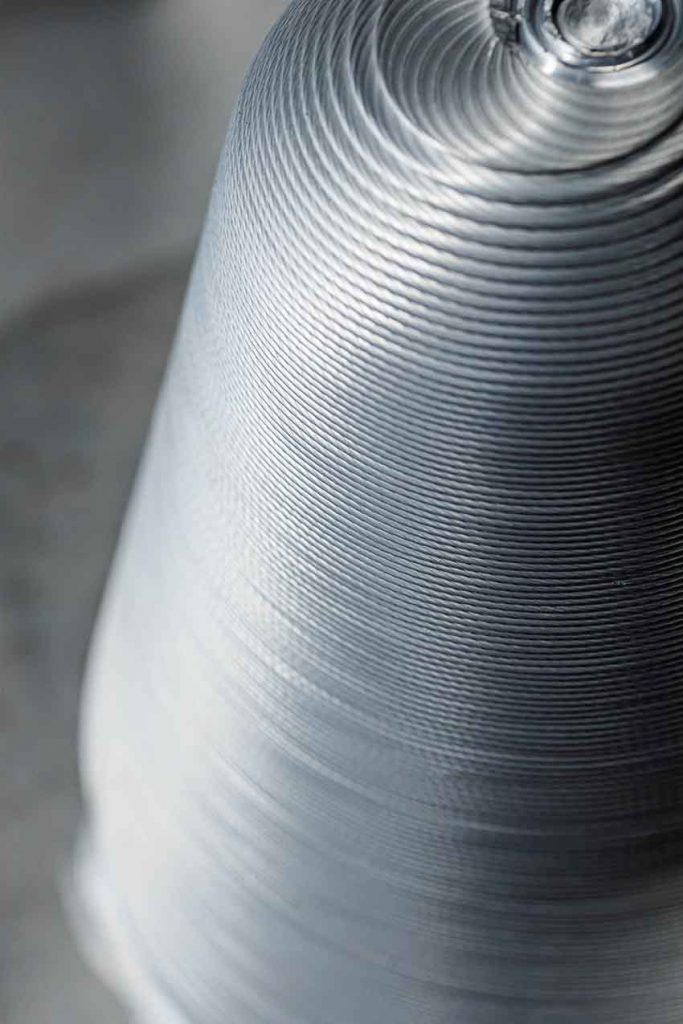
E.E: What can you tell us about market trends?
B.W: According to a report published by Data Bridge Market Research, The AM industry is set to have significant growth from 2023 to 2030. A major factor is the increased demand for lightweight components in the automotive and aerospace industries.
MELD has positioned itself to integrate within those industries due to our ability to produce parts using materials such as Ti6-4 and aluminum alloys. These are sought after alloys because of their high strength to weight ratio. An Army program recently confirmed that MELD’s as-printed Ti6-4 material exceeded the minimum requirements for forgings.
E.E: What are the most innovative products marketed?
B.W: Our K2 machine with a continuous feed system is most desirable across industries for substituting the manufacturing of large forged parts. This product allows customers to avoid long lead times and supply chain issues.