DMG Digital Enterprises SE (DDE), which owns the MOIIN brand, is itself still a young player, although it forms part of Mühlbauer Technology. The family-run Group based in Hamburg employs around 500 people who have been involved in the research, development and production of innovative materials for the dental industry for 60 years. These material solutions are trusted by dentists and dental technicians in more than 80 countries around the world. DDE was founded in 2020 and consolidates the Group’s digital business with a focus on 3D printing. It currently employs about 40 people.
Interview with Anna Babel-Drusenthal, Corporate Development Manager / Head of MOIIN.
Easy Engineering: What are the company’s main areas of activity?
Anna Babel-Drusenthal: The material specialists at MOIIN have been bringing high-quality resins for 3D printing to the market for several years now. Deviating from the Group’s core dental activities, the areas of application for MOIIN’s high-performance plastics range from jewellery design to industrial manufacturing and medical technology.
Moreover, at MOIIN we also work in close cooperation with research institutes and universities.
At this point I would very much like to mention the project concluded last year with the DESY Research Centre. Deutsches Elektronen-Synchrotron DESY is one of the world’s leading research centres for accelerator, particle and Astro particle physics as well as for research into photon science.
The tests conducted by DESY using existing MOIIN products showed that these materials can indeed be used for printing miniature accelerators in 3D. Very promising results were achieved in the precise printing of miniature capillaries (inner diameter of ~1 mm with walls as thin as 100-200 µm). The project was presented to Senators Katharina Fegebank (Second Mayor and President of the Ministry of Science, Research and Equality in Hamburg) and Michael Westhagemann (Senator for Economics and Innovation in Hamburg) as part of an Innovation Tour 2021 to showcase a local project between DESY and a medium-sized company in Hamburg.
E.E: Can you tell us about any new products?
A.B.D: Two new products were presented at the MOIIN booth at the most recent Formnext trade fair:
MOIIN Tough Clear
The application opportunities for 3D-printed objects using MOIIN Tough Clear are wide-ranging. By varying the structure and thickness of the material, it is possible to print more flexible or firmer parts to suit your needs. Through a mixture of ductility and flexibility, the objects remain dimensionally stable even when subjected to extreme stresses, e.g. those caused by dropping or impact, and are malleable without being brittle.
MOIIN Flex Clear
The also newly developed MOIIN Flex Clear is extremely elastic, offers an elongation at break of 123% as well as exceptionally good strain recovery. This makes the 3D printing resin perfect for seals and shock absorbers, and for a wide range of applications where traditional elastic materials such as rubber or silicone are usually used. The high UV resistance and low water absorption of the material also make it particularly resistant to weathering. MOIIN Flex Clear is therefore also suited for a wide range of outdoor applications and process engineering systems.
Both materials have been very well received and we already have our first orders and a number of enquiries from various industrial sectors. Therefore, you never get bored working at MOIIN because we are constantly exploring new horizons. This is precisely what we love in our cross-disciplinary MOIIN team – and the 3D possibilities seem limitless to us!

E.E: What are the product ranges?
A.B.D: We serve very heterogeneous markets with MOIIN products. We provide material solutions with specific material characteristics for various industrial sectors where quality, process reliability and precision are crucial factors. Biocompatible solutions are also not a problem. After all, our roots lie in medical technology.
Apart from the existing MOIIN brand materials, we also offer material developments or customisation according to the individual wishes of our customers.
MOIIN resins are mainly designed for open systems. Supported printer technologies include DLP, SLA and LCDs with 385 or 405 nm wavelength output. However, we recommend our customers to use one of our carefully selected printer partners, depending on their printing requirements, because they have profiled or validated our materials for the respective systems. So far, we have been working very successfully with ASIGA, MiiCraft, GENERA and Rapidshape. We are currently also in negotiation with further printer partners.
E.E: At what stage is the market where you are currently active? What can you tell us about market trends?
A.B.D: The market is changing to our advantage. Not long ago, it was common to first learn how Additive Manufacturing works using the cheapest possible printers and materials. However, the trend today is towards more sophisticated systems. In this respect, we are of course in line with the trend.
E.E: What are the most innovative products available?
A.B.D: There is innovation in virtually all MOIIN materials: our CDB technology offers exceptionally precise printing.
Using previous technological capabilities meant that smaller or larger deviations always had to be expected in the print result – especially when creating highly precise internal structures and cavities. A major step towards precision and safety can now be achieved with the new CDB technology, which was developed by MOIIN researchers, is present in all MOIIN resins and has already been registered as a trademark.
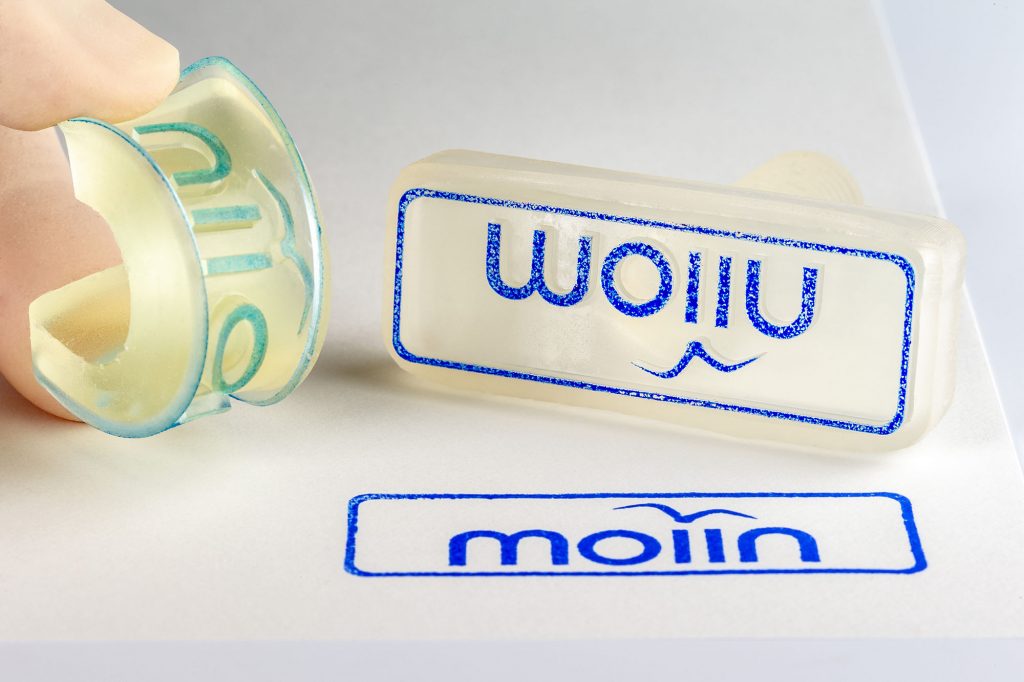
CDB stands for Cure Depth Barrier. It describes the minimised overcuring of the 3D printing resins in the Z direction – resulting in a previously unattained precision in all dimensions of the printed objects.
The technical background:
In SLA and DLP 3D printing processes, the objects are built up layer by layer using a liquid printing resin. The liquid material is cured layer by layer by exposure to light, i.e. UV radiation. In order for the layers to adhere to each other, the light must pass through the layer being cured and into the layers that have already solidified. This phenomenon is known as overcuring.
Overcuring is therefore necessary and cannot be completely prevented. However, there may be a problem with overcuring if the 3D object has a hole or cavity in the Z direction, i.e. its vertical direction. At the moment, when this cavity is closed, there is no previous layer to which the current curing layer can adhere. Instead, the light radiates into the liquid resin in the area of the 3D model where there should be a cavity. The liquid resin is cured by the light and forms an unwanted structure in the area of the cavity. At worst, small holes or channels are completely blocked.
The CDB technology reduces the required overcuring to an absolute minimum. This leads to reliable maximum precision, even in terms of inner structures and cavities, without any loss of printing speed.
E.E: What are your predictions for the rest of 2022?
A.B.D: Well, 2022 will soon be coming to an end. We are currently working on some of the requests we received at the Formnext trade fair. A plant-based resin and an “ABS-like” resin are also in progress. We look forward to 2023 and, as always, expect many exciting new challenges – to which we at MOIIN are certain to find a solution.