MOTEON offers a holistic approach to optimize mechatronic drive systems in terms of their energy and material efficiency as well as costs in development, production and application. The company provides customers the technical support for MCTRL software and mechatronic system conception and realization.
Interview with Dr. Veit Zöppig, Chief Technology Officer & Marius Klausnitzer, Senior Engineer Mechatronics at MOTEON.
Easy Engineering: A brief description of the company and its activities.
Marius Klausnitzer: MOTEON was founded in September 2020 as a spin-off from Infineon. We are a “Preferred Design House”, i.e. a partner of Infineon and its customers. Our main field of activity is system integration and motor control software in the automotive sector, for example for auxiliary units such as fans, pumps, innovative 48V systems or even smart home applications.
We want to offer turnkey solutions in the area of motor control, so that the time to market for the product can be significantly reduced for our customers, as well as the effort they have to put into their projects.
E.E: What are the main areas of activity of the company?
M.K: There are different ways in which we work with our customers. Some come to us because they want to use Infineon products and need support. Others take advantage of the opportunity to license the embedded software we developed and use it in their systems. Thus, we accelerate the development timeline of our clients.
In our premium services the customer receives application specific concepts and engineering services from us. We provide an end-to-end service offering reaching from mechatronic system concept, electromagnetic design of the motor, mechanical design, electronic design to embedded software.
We want to accelerate the development cycle of our client, by supporting during the concept and development phase. For the industrialization, we help our clients to hand over their project and our concepts to the technology providers and manufacturers with whom we are connected.
E.E: What’s the news about new products?
M.K: To accelerate our development cycle, we need comprehensive data acquisition and test tools. These devices replacing the manual test of the embedded software and system and reduce test time by 80%.
Reproducible automated testing will ensure a rapid detection of bugs and allows us to fix them immediately. If a client is not able to detect and fix a software bug in time, the costs for bug-fixing double with each revision. In addition, in classical projects the majority of bugs are found towards the end of the development. This puts a huge risk on the timeline.
To avoid these, we have developed three hardware system: a motor test bench, a more compact version for the individual developer and a data tracing tool called TraceBox.
Test bench technology – (mobile)Motor Test Bench
With our products (mobile Motor Test Bench and Motor Test Bench) it is possible to perform fully automated tests on complete mechatronic systems and also to test various environmental influences (e.g. fluctuations in the supply voltage or simulated communication errors). This allows a software test against the requirements of the individual application of our own software and our clients software.
These two motor test bench types, a mobile version and the main one are used for verification in our development, but can also been sold to our clients to allow them to benefits from these advantages.
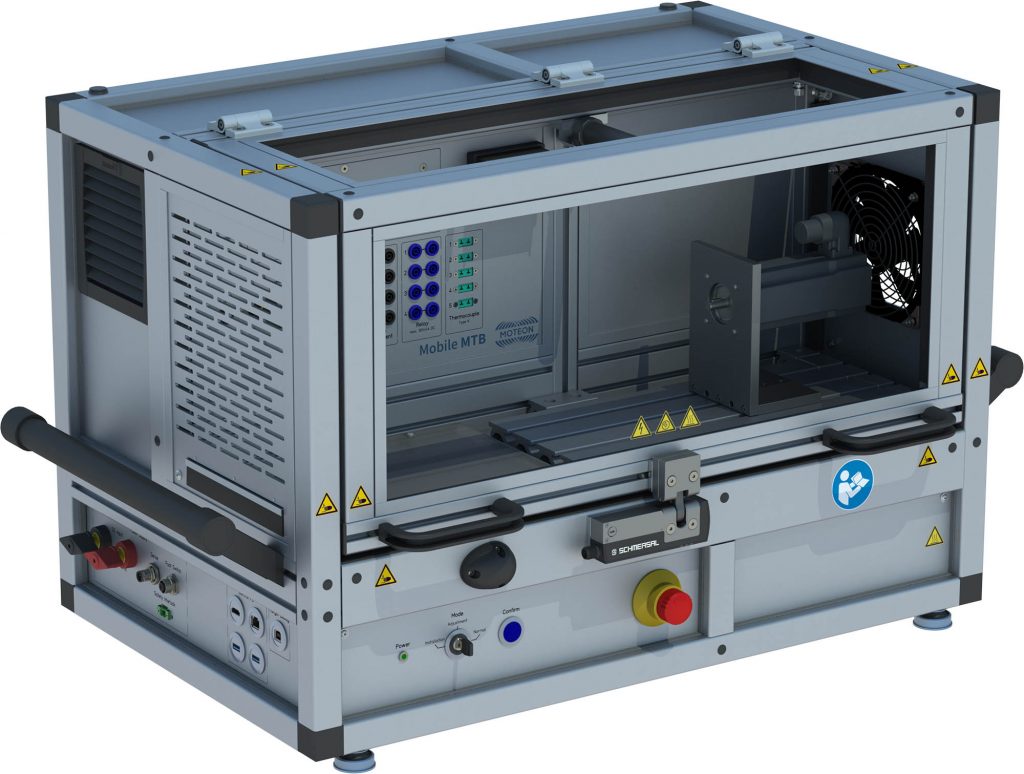
Our product TraceBox is a versatile data acquisition and communication tool for the development and validation of motor control software that can be used in conjunction with real target hardware. It can handle the communication between PC and target through a variety of protocols: SPI/UART, LIN, CAN, EtherCAT, RS232 and USB. Flashing and debugging of the motor control software can also be handled. It was originally created for our own motor control developers, but has reached a value and maturity that we want to offer it to our customers as well.

Together with our partner Infineon we develop a software kit, tailor-made for their microcontrollers (e.g. MOTIX™, XMC™). With the components contained in it, customers can bring motor control into their product more quickly after acquiring the licenses; when implementing, we can also offer support.
E.E: What are the ranges of products?
M.K: We are an end-to-end engineering service provider for motor control applications from software, engineering to testing and tools.
Customer can assemble their individual solution with software libraries from us, use the tools for developing and testing, up to full customer-specific solutions, i.e. software implementation or entire mechatronic system development.

E.E: At what stage is the market where you are currently active?
Veit Zöppig: The main field of activities are automotive on-demand controlled low-voltage auxiliary units with electric motor drive. The automotive industry is in a global transformation state. In the next five years we expect more changes than in the last 50 years. This includes the propulsion technology moving from combustion engines to different configurations of alternative drives, the board-net voltages and technologies and the changes in the electrical supply and information exchange architecture (E/E-architecture) and the increasing autonomy.
Beside these technological changes, also the customer expectations on a car, the business models and the supply chain structuring are changing dramatically. This creates a high level of uncertainty in the market. But independently on the final development direction, the needs of electric motor control solutions increase.
E.E: What can you tell us about market trends?
V.Z: Let us focus on one major trend, the change in the E/E-architecture. Over decades, for each new function a dedicated box was developed. This one function/one box approach has reached its end: the complexity of the wiring harness, the material cost and the resulting mass leads to a change. In a first step, a function or domain centered concentration of control units occurs, referenced as domain architecture. The most promising architecture is a so-called zonal architecture. A central car computer is connected to the outside world and to a low (2-4) number of zone controllers. These zone controllers manage the electric supply flow as well as the information flow with high-speed busses and a service-oriented software architecture. To integrate the peripheral mechatronic auxiliaries in such an architecture, the zone controllers must run an AUTOSAR driver to translate the service requests to a signal-based legacy bus communication as LIN. This is just one example that shows, that software becomes more and more decisive.
E.E: What are the most innovative products marketed?
V.Z: We materialize our motor control system know-how in MATLAB/Simulink model libraries. With this internal base, we are able to generate the control and signal processing code for the motor control on different controller platforms. We combine this generated code with a hand-coded base framework for the best usage of the peripheral hardware. We named our approach “Hybrid Programming”.
To allow for a simulation-based control optimization, the identification of the parameters of the controlled motors is key. Here, we provide identification measurement services to measure the machine parameters. For the following testing, we also provide safe motor test systems with dynamic load emulations. Thus, the control optimization can start before the actual load system (e.g. a fan or a pump connected to a complex hydraulic circuit) exists. The integrated measurement systems allow us to acquire and visualize real-world sensor signals time-synchronized to controller internal signals.
E.E: What estimations do you have for 2023?
V.Z: First of all, we hope for an end of the war in Ukraine. We are optimistic to start more and more customer projects after the establishment of our company. We also want to concentrate our innovation and research activities more on energy saving and decarbonization. Among other things, we want to enable the fuel cell technology for trucks and passenger cars with fitting auxiliaries (pumps, compressors).