Interview with Christian Kübler, Product manager Vario-X & Drives at Murrelektronik.
Decentralization of electrical installations is a big topic at the moment. What actually led to the fact that most systems were historically handled centrally?
Christian Kübler: The fact that machines have been equipped with centralized drive technology in the past has mainly to do with the fact that the hardware was previously subject to too great losses to pack it into a decentralized housing without external cooling. In addition, historically grown machine structures existed that have not yet been replaced. In addition, machine and plant construction has developed towards modular structures, so that individual machine functions can be added or omitted depending on requirements. Decentralization is particularly useful here, so that a new, expensive control cabinet does not have to be added to every machine module. All in all there is a new thinking in the manufacturing areas together with new technical possibilities this leads to the decentralized automation.
And what technical advances now make decentralized control possible? Why wasn’t it possible before?
C.K: On the technical side, new, loss-reduced components such as silicon carbide or gallium nitride semiconductors are particularly worth mentioning. These raise the efficiency to a completely new level and thus make the use of decentralized automation technology possible to the extent known today. In addition, machine manufacturers have started to rethink installation technology, which strengthens decentralized automation.
In the past, control cabinets were needed because it was not possible to install the necessary peripherals in a convection-cooled enclosure with usable derating. Today, new possibilities are available due to the significantly increased efficiencies.
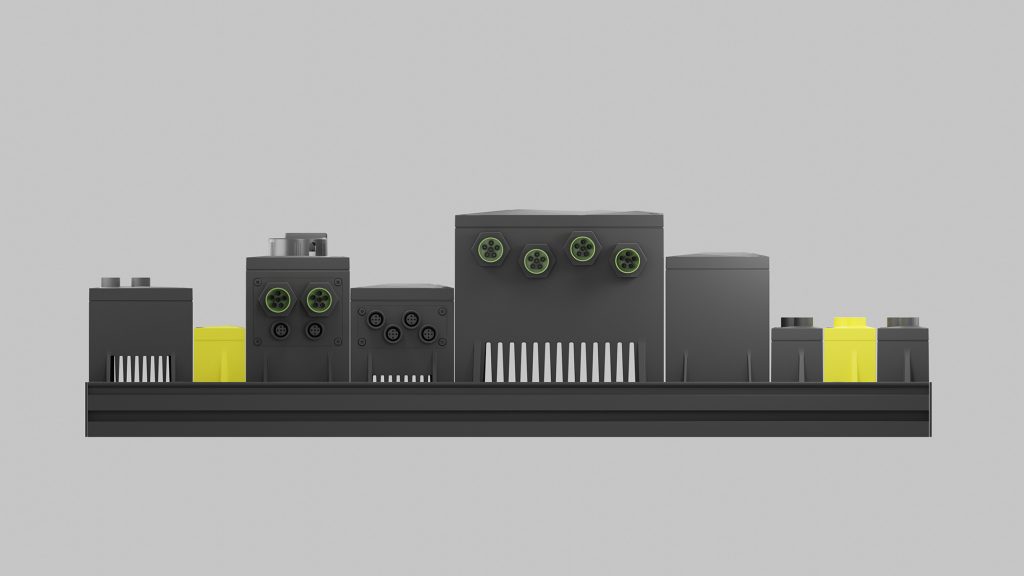
What are the main advantages of decentralization? Ideally, using the example of a production facility with several machine tools.
C.K: Decentralization opens up new possibilities for the machine builder and enormously reduces the planning and wiring effort as well as the susceptibility to errors. This means that, for example, the wiring of a system with approx. 8 axes, which used to take approx. 2 working days for the wiring, can now be done in a few hours.
The new Vario-X even makes it possible to operate machines completely without a control cabinet. What modules does Vario-X contain?
C.K: VARIO-X contains in the first release package the following modules:
- VARIO-Backplane: Backplane for mounting the modules
- VARIO-CTRL 1.000: High performant industrial PC for controlling different fieldbus participants (e.g. Impact IO-modules, drives, etc.)
- VARIO-Power In: Infeed for 3 x 400VAC + STO-Signal (Safe torque off for the decentralized motors)
- VARIO-Powersupply 24VDC: 24VDC Powersupply with integrated EtherCAT 3-Port Branch
- VARIO-Powersupply 48VDC: 48VDC Powersupply
More modules will follow after the market start. VARIO-X will grow step by step and constantly adapt to the market.
Isn’t the Vario-X more expensive in each machine compared to one central control cabinet?
C.K: In direct comparison with control cabinet components, VARIO-X could appear more expensive, but it must be noted that VARIO-X pays for itself in the total cost of ownership. Due to the significantly lower wiring costs, the reduced susceptibility to faults during commissioning and the reduced costs because of less effort at the device exchange in the event of a defect, VARIO-X is more cost-efficient.
You mentioned speed of installation among the advantages of decentralization, do you have any idea how much time is saved by using Vario-X?
C.K: We assume that time savings of up to 80% are possible.
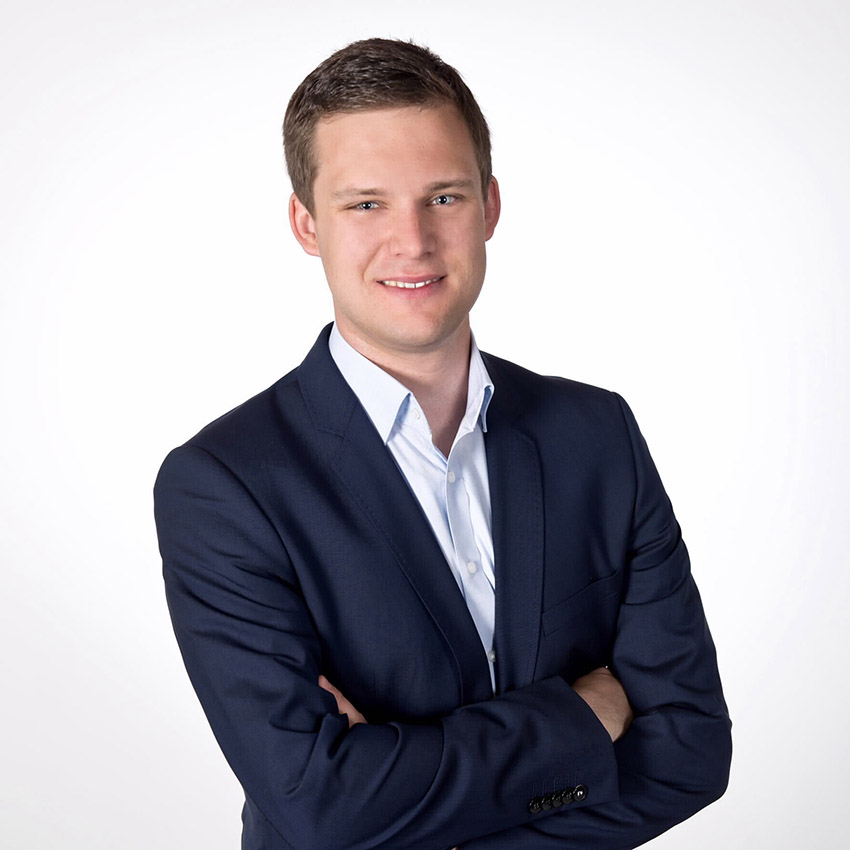
Christian Kübler, Product manager Vario-X & Drives at Murrelektronik.
I was intrigued by the possibility of using a digital twin of the Vario-X, I assume it has the most benefit when combined with a digital twin of the machine. Is there any concrete cooperation with machine manufacturers running now? Can you give an example?
C.K: The digital twin is currently being tested on our own sample machines, which we build for trade fairs and internal purposes. We are working together with a partner on the development of the digital twin. The aim is to provide our customers with the interfaces of VARIO-X suitable for their own digital twin. Later, we also want to implement functions such as automatic cable length calculation, which will make our customers’ daily work easier.
For illustrative purposes we have so far focused our gaze mainly on machine tools, but the use of Vario-X is certainly much broader. Please introduce the range of equipment where Vario-X is beneficial.
C.K: Basically, we see the use of VARIO-X in a variety of applications with a maximum power per drive axis of up to 1kW. There is great potential in replacing pneumatic actuators with servo-electric drives in the field of factory automation. However, general mechanical engineering or intralogistics also represent an increasingly important sector in which we see VARIO-X, in the context of automation without control cabinets, as an important factor for the economic and ecologically sustainable realization of new systems. Everything is conceivable, from servo-electrically operated power clamps in automobile production to a delta robot application in the pick-and-place area.
Murrelektronik GmbH