norelem is a world-leading manufacturer and supplier of flexible standard parts and components for mechanical engineering. The company supplies over 70,000 standard products relating to standard machinery and operating elements, as well as automation components. Ninety-eight per cent of these parts are available from stock, and the business delivers on-site technical support for products. This high level of inventory enables norelem to provide fast and reliable delivery times.
Interview with Marcus Schneck, CEO of norelem.
Easy Engineering: Can you give us a brief introduction to norelem and your company’s main activities?
Marcus Schneck: norelem is a world-leading manufacturer and supplier of flexible standard parts and components for mechanical engineering. We supply over 70,000 standard products in the standard machinery and operating elements industry, as well as automation components. Ninety-eight per cent of these parts are available from stock, and the business delivers on-site technical support for products too.
E.E: What are norelem’s main goals?
M.S: At norelem, our strapline is ‘Green Means Go.’ So, our main goals revolve around increasing the speed at which engineers and designers can get their hands on the components that they need.
For example, standard parts do not require drawings, drawings can be downloaded as finished 3D models cost free, which means that these corresponding parts are physically available as standardized products from stock.
Therefore, the product can simply be ordered and doesn’t need to be elaborately manufactured, which immediately gives the designer the advantage of plannable availability. There is no drawing, no configuration, just finding and downloading. By using standard components engineers simply define the product they need, download the drawing, place the order via our online shop, and receive their component the very next day.
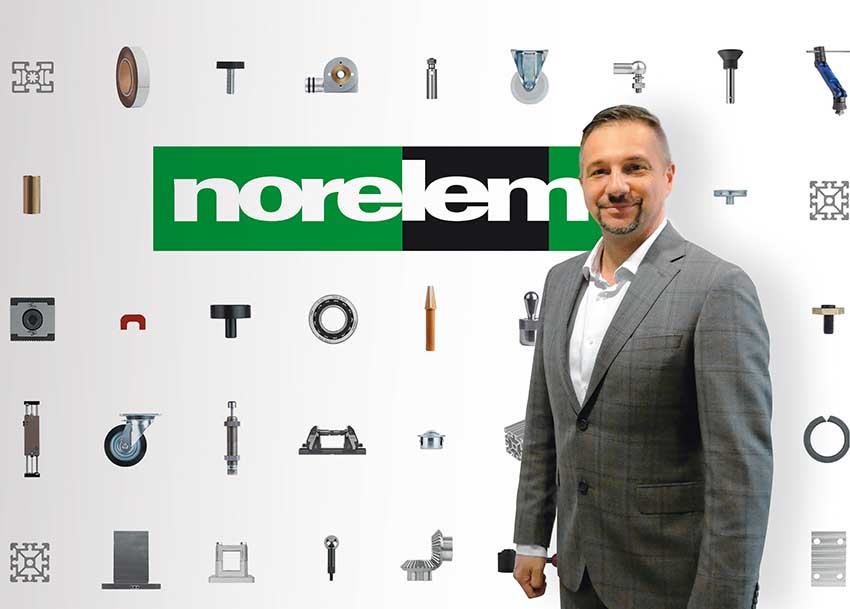
Even for spare parts, the required goods do not need to be engineered or produced again, instead they can simply be reordered. In total, by using standard components, you save time and cost, which leads directly to a higher planning reliability and increased efficiency. And the more standardized items are in use, the higher is the positive impact on the whole project.
In a nutshell, we want to help our customers and design engineers implement their ideas by providing all the parts they need from one single source.
E.E: What range of products does norelem offer?
M.S: norelem offers a complete range of standard components. Everything from systems and components for power transmission in machine and plant construction to wheels castors and ball transfer units. Our two-volume catalogue, THE BIG GREEN BOOK lists more than 70,000 standard components to help engineers find what they need at one glance.
As we strive to maintain our position as a European market leader in standard components, we are always engineering and designing new components to match the speed with which the industry changes and innovates

E.E: What can you tell us about norelem’s new products?
M.S: Across the industry, many machines currently work digitally, however, in the future, more and more machines will be working ‘smart’. At norelem we are finalizing the launch of our new SMART products, which will continue to drive forward the evolution to smarter, more efficient manufacturing. With the new SMART products, norelem is developing intelligent components and solutions that help to control machining or manufacturing processes in a more stable, precise, and reliable way. We have one simple goal: error-free machining.
E.E: What estimations do you have for 2022?
M.S: The biggest challenges the manufacturing industry is facing at the moment, are the raw materials situation, supply chain issues in general, and the huge resulting cost and price increases.
At norelem, we put all our efforts in serving our customers quickly and in time, as most of our products are available from stock. This also means constant optimization of our global logistics centers and logistics flow. We are aiming to minimize dependency, by increasing in-house production at our production sites both in Germany and in France. And for parts that are not manufactured in-house, we aim for independency by thinking long-term and by taking preventive action. This means tightening our strong relationships with existing suppliers, while at the same time forging trusting bonds with new suppliers and alternative sources.