Plasmac is part of both the Syncro Group and the EREMA Group of companies, Syncro manufacturers ancillary equipment for the blown and cast film extrusion industries and EREMA is the largest manufacturer of plastics recycling equipment in the world. Plasmac manufacturers equipment for the recycling of plastics waste material generated in the plastics manufacturing industry.
The company was established in 1994 and was originally based in Aylesbury, in the UK, in 2017 Syncro took full ownership of the business and the company relocated to the heart of the “Plastics Extrusion Capital of Italy” in Busto Arsizio, near Milan.
Plasmac Srl was established in 2019 and this is when the EREMA Group took a 60% share of the business.
Easy Engineering: What are the main areas of activity of the company?
PLASMAC: Plasmac designs, manufactures and assembles a range of machines, all machines are designed to the latest standards using SolidWorks 3D design and modelling software plus fluid dynamics software to model the flow of polymer through our extruders. Due to the location of the business, there are a multitude of suppliers for all components of Plasmac’s equipment, plus industry standard suppliers of such things as gearboxes and motors are used in our machines.
E.E: What’s the news for 2021 about new products?
PLASMAC: This year we launched our latest machine offering, the Epsilon which is an inline shredder extruder repalletizing machine designed to recycle inline trims, start-up scrap, non-woven’s, apron cut-outs and masks among other things. It uses an innovative extruder screw design and feeding entry and needs less than 0.2kW/Kg of energy to recycle the scrap material, plus it ensures there is the absolute minimum of material degradation and heat history put back into the material. The integrated shredder sits above the feed entry of the screw and size reduces the material entering the extruder before plastification, this means it can recycle high speed trims, thicker films, injection moulded parts and small pieces of start-up lump scrap. The slow rotating shredder requires no water cooling, adding to the efficiency of the machine and due to the short screw technology, the machine has a very compact size.
The machine is also designed with flexibility in mind, it can be equipped with either an air or water pelletising system, with a vacuum degassing system to allow it to handle printed materials or materials that are hydroscopic and require venting such as biodegradable materials and can also be supplied with a variety of feeding systems such as trim baskets for inline trims, a roll feeder for scrap or start-up reels and an elevator with metal detector for lumps, pieces, slabbed or loose materials. Due to the unique screw design, very little heat is needed to melt the material, typically the extruder will run at processing temperatures of 40 to 50o lower than an extrusion line, this ensures the pellets produced have the highest quality and can be used directly back into the extrusion process, even up to 100%. The key objectives of this development were to design a recycling machine that can repelletise all forms or extrusion scrap that today’s extrusion factories produce. We also wanted to produce a machine that could handle the scrap material from the sudden explosion in PPE products such as masks and aprons, so the machine also needed to be able to handle non-woven’s and fabrics.

E.E: What are the ranges of products?
PLASMAC: Plasmac offers three types of machine, the Alpha direct extrusion system, the Omega Shredder extruder line and now the Epsilon. The first Alpha was sold in 1994 and the first Omega in 2004. Since then, Alpha and Omega’s have been installed on pretty much every continent on the planet.
The Alpha direct extrusion design means the waste material such as inline trims, reels, injection moulding parts or other thin parts are fed directly onto the screw, with no prior size reduction required. The Alpha’s are based around our dual diameter, short screw technology, they have an 8:1 L:D ratio screw, which is approximately half the size of our competition meaning we use less energy to melt the polymer and we put less heat into the material to pelletise it. Less heat leads to less degradation of the material and less shear in the material, also as the material is fed directly onto the screw, this ensures less dust is generated, which means less gel formation in the pellets. We supply quite a few inline Alpha extruders for edge trim recycling, the trims are taken from the lines and fed directly back into the process. Off-spec reels, start-up reels or damaged reels can be recycled the same and because like for like materials are being put back into the process therefore there’s no contamination of the materials.
The second type of machine is the Omega, this is an extruder with an integrated shredder, the Omega can recycle nearly anything, start-up material, big lumps, bales, raffia bags and bulk bags, or any other kind of larger sized scrap. The Omega uses the same screw technology as the Alpha and Epsilon machines, but the screw length is 14:1 for non-vented and 26:1 for vented machines. It uses an integrated slow rotating shredder with a unique screen design that size reduces the material that is then auger feed directly in to the extruder screw.
The quality of the repelletised material from all of our machines is very similar to virgin pellets, Plasmac runs trials for customers repelletising their own material which clients then take back for testing at their own facilities. They test the MFI, the gel inclusions, the properties of the materials and in the majority of cases they confirm that the quality of the pellets is very similar to their virgin material.
E.E: At what stage is the market where you are currently active?
PLASMAC: The plastics recycling market is a well established market serviced by some well established machinery suppliers. However, with the challenges put forwards by the European Union on Circular Economy and new legislation such as the EU’s waste framework directive, the packaging waste directive and the regulations on landfilling mean the market is being forced to change. Many of our customers have zero pellets to the environment policies in place now and a lot of them are required through their brand owner customers – to include a significantly larger amount of recycled content into their products.
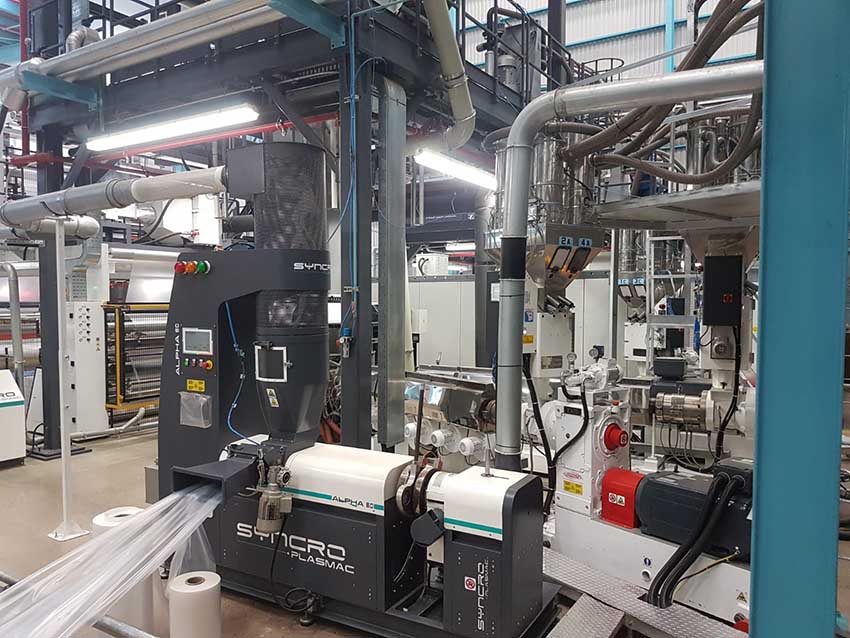
E.E: What can you tell us about market trends?
PLASMAC: We’ve seen many requests for trials where customers take the recycled material back from us and trial it in a few products. They present these to their end customer and basically have their end customer approve the use of the recycled content. As a company, we have traditionally supplied products mainly to blown film producers but we are now increasingly expanding into other areas as well with customers in pipe manufacturing industry, sheet extrusion companies and injection moulders also looking to recycle their scrap material.
E.E: What estimations do you have for 2021?
PLASMAC: 2019 and 2020 saw us grow at a phenomenal rate and this year we have set ourselves another aggressive target to continue this growth. Now that we are part of the EREMA Group our brand is also growing rapidly. To help us manage this we will move in to a new factory with double the assembly space we have now. Our existing factory will become the home for a new technical centre which will also incorporate a material testing lab and a small scale extrusion production line to test the recycled materials on. Syncro itself will move into a new production facility in June which incorporates the latest in automated material stock handling and the same state of the art systems will be installed in the new Plasmac building before the end of this year.
2022 is the date for the next K-Show, the industry’s leading exhibition and Plasmac intends to use 2021 to prepare itself for another bumper show in 2022.