PRINT&GO is a multi-brand and multi-device software solution focused on monitoring and monitoring the 3D printing workflow. PRINT&GO unifies all the machines in a single macro dashboard and includes a series of automations never seen before in the 3D sector.
Interview with John Amin, Channel Manager of PRINT&GO.
Easy Engineering: What are the main areas of activity of the company?
John Amin: PRINT&GO focuses on the monitoring and optimization of 3D printers or 3D printer fleets to work unassisted. It is the ultimate solution to automate the management of the different stages within the 3D manufacturing process, implementing a flexible printing strategy and providing cost reduction through an optimized workflow.
With PRINT&GO you can monitor the entire workflow of your 3D printers, controlling them remotely and in real-time. It allows you to plan production by analyzing manufacturing costs and their traceability, as well as managing stock, optimizing the material consumption and production times.
It is important to note that PRINT&GO is a software solution that works with different brands of 3D printers on the market.
E.E: What’s the news about new products?
J.A: The current focus of the platform is on providing real day-to-day solutions for operators. We know that 3D printers can work 24/7, but no one can work 24/7 in front of a 3D printer. Therefore, we have developed a continuous production module, which allows your team to work uninterruptedly and without the need for operators to perform any action in person.
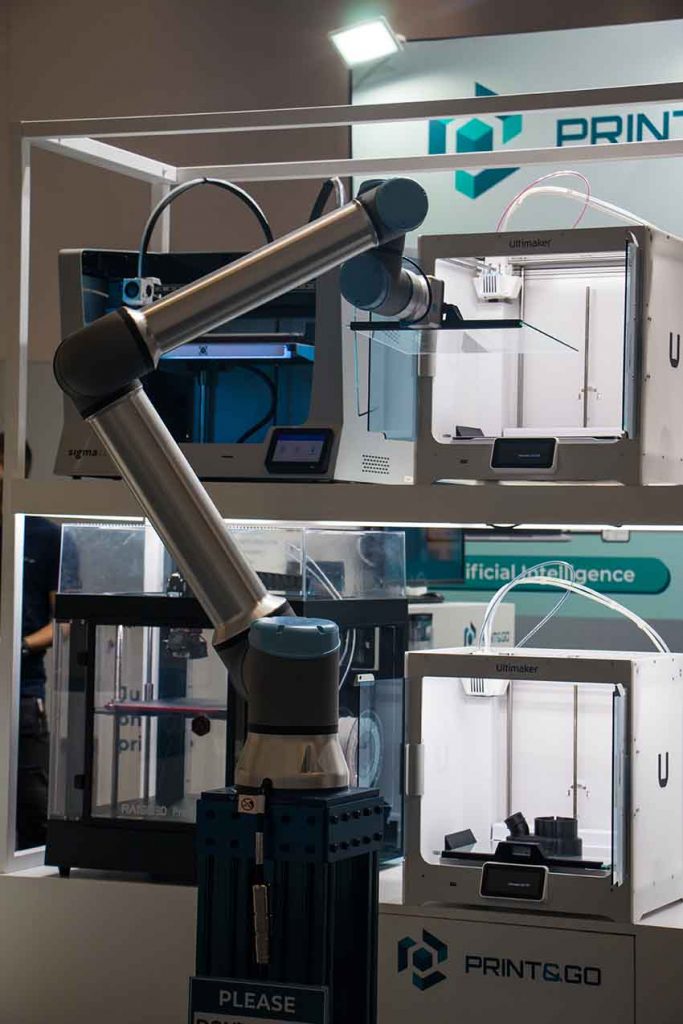
On the other hand, thanks to Artificial Intelligence, we have developed a tool that detects when spaghetti is being printed, one of the main setbacks of additive manufacturing. This new module has an efficiency of 99.6% and allows you to program the printer to stop or abort automatically. In this way, PRINT&GO acts as your 3D printing guard, so you save on costs, time and material.
It is worth noting that we have calculated that, with PRINT&GO, it is possible to quadruple the number of parts printed and reduce costs by up to 50%. At the same time, the system can learn from its actions to optimize future tasks.
E.E: What are the ranges of products?
J.A: PRINT&GO is a modular software solution. This means that we offer different modules, depending on the needs of each client. We adapt to each company to offer them the best package that provides the maximum value to their activity.
On our website you will find all the available modules and which of them we recommend, depending on the company’s activity and needs.
Everything starts with the basic pack, which includes everything you need to connect one or more printers and manage them remotely.
We also have a module more focused on projects and obtaining exhaustive control over all of them.
The Reporting pack offers a complete and detailed record and traceability of your entire workflow.
We offer a module more focused on profiles, managing permissions, hierarchies, and roles between all of them.
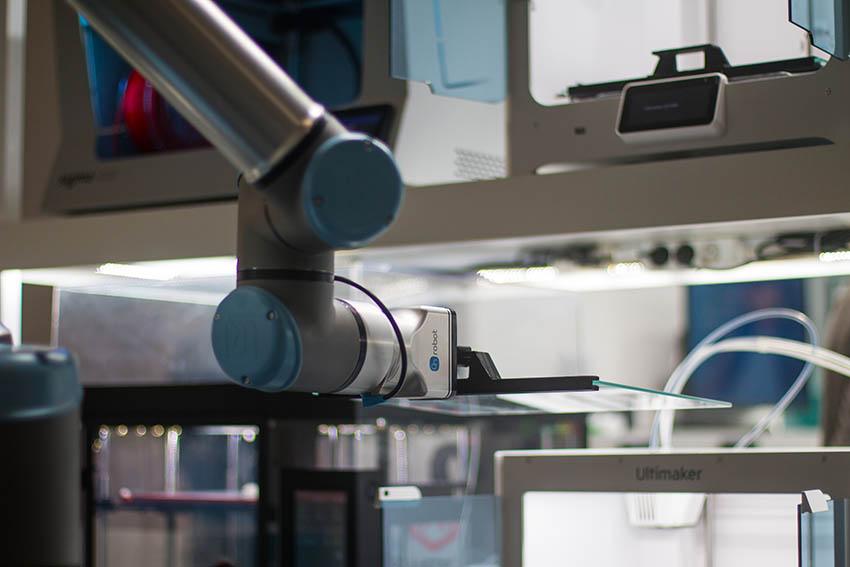
The Maintenance pack allows you to get help at all times from our specialists and other exclusive backup and solving problems services.
With the Artificial Intelligence pack, you will have at your disposal the Spaghetti Detector functionality and the automatic detection tool when a setback is occurring in your equipment.
And last, the Continuous Production pack will offer you 24/7 production, without the need to have operators supervising and managing the production all the time.
At PRINT&GO, we work with all types of companies, because the software has relevant functionalities and benefits in the value chain of multiple sectors and departments. Software is a fundamental part of the 3D printing ecosystem.
Our customer profile is very diverse, ranging from individuals or companies that have a single machine and are looking to get the most out of it, to companies that have a large fleet of 3D printers, of different brands or not, and need to monitor them remotely and on the same platform. In both cases, it is essential to have a solution that simplifies processes and covers the real needs of users and operators, such as PRINT&GO.
We have customers who have 3D printers for their internal production. Also, we work with Service Bureaus and sectors such as education or medicine. For all of them, PRINT&GO helps them to optimize production to the maximum and to obtain detailed analytics with reports and consumption graphs of the productive capacity of their equipment.
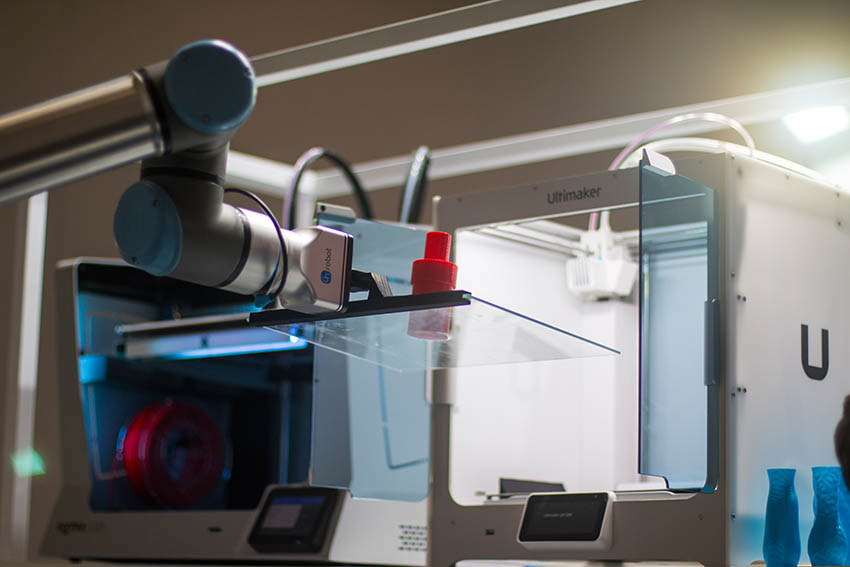
E.E: At what stage is the market where you are currently active?
J.A: In a digital age, where all 3D printing players have their cloud platforms to connect and monitor their printers, we find that a user has to connect to as many platforms as they have 3D printers. Or, even more problematic, once connected, the user has no useful or practical tools to take the worry out of making sure they get a good print. Seeing this need, in 2016, is when we decided to develop the PRINT&GO platform, a modular platform that adapts to the needs of each user.
Today, the market is more focused on Industry 4.0 and the combination of technologies to achieve the highest level of automation. In this way, thanks to PRINT&GO uninterrupted and continuous production can be achieved.
E.E: What can you tell us about market trends?
J.A: We see the future of 3D printing in Industry 4.0. Our aim is to combine 4.0 technologies in a cross-cutting manner. That is why PRINT&GO brings together different Industry 4.0 technologies in a single system.
On the one hand, we work with 3D printing, as it is obvious, together with the Internet of Things, which allows printers to be connected to computers or mobile devices via sensors. Big Data and Cloud Computing take on great relevance when it comes to processing large volumes of information and storing them securely, with the help of an encryption system.
We use Artificial Intelligence to detect and abort the printing of spaghetti during production. Also, we work with Augmented Reality to perform maintenance on the equipment, without the need for prior training. And finally, we have integrated Collaborative Robots, to have continuous production, 24/7 without the need for operators to be there all the time.
E.E: What are the most innovative products marketed?
J.A: PRINT&GO allows you to automate the production of your 3D printers with three different solutions: automatic removal systems, API integration and collaborative robots. With these packs, your 3D printers can work uninterrupted 24 hours a day.

From the collaboration between PRINT&GO and Universal Robots comes a standard and flexible solution to maximize the production of 3D printers with collaborative robots. By adding a cobotics to your production, you can run it 24 hours a day, 7 days a week, without requiring operators to continuously oversee and manage production. Do it directly on the PRINT&GO platform.
E.E: What estimations do you have for the rest of 2022?
J.A: We are focused on taking 3D printing to the next level, in terms of automation, continuous production and error detection. In addition, we are expanding our distribution channel around the world. So, we are open to new collaborations and partnerships.
To conclude, automating production is one of the most exciting frontiers of additive manufacturing. There is nothing more exciting for 3D printing than automating the entire workflow of 3D printers to achieve uninterrupted production. Continuous production is already a reality, thanks to PRINT&GO and the combination of cutting-edge and flexible 4.0 technologies.