PushCorp was founded in 1993 with the primary goal of creating end effectors for robotic surface finishing processes. The company continues that mission today with their headquarters in Dallas, Texas. This is home to a state-of-the-art manufacturing facility where PushCorp designs, machines, and builds their own tooling. To support sales, they have a regional office in Wixom, Michigan and distributors strategically located all over the globe.
Today, PushCorp sells to every major manufacturing sector including automotive, aerospace, defense, energy, maritime, and the medical industry. PushCorp continues to build and develop new material removal tooling to support these industries and to help automate their processes. These include grinding, sanding, deburring, polishing, gate removal, machining, and much more.
Easy Engineering: What are the main areas of activity of the company?
PushCorp: Our first product, which was patented in 1995, was the Adjustable Force Device (AFD). This product’s function was to allow a robot to maintain a consistent yet adjustable force when in contact with a part’s surface. Previously, industrial robots simply moved from point A to point B without any regard for the amount of force being applied. PushCorp’s innovative compliance device opened the door for robotic grinding, sanding, polishing, and other surface finishing applications that require a precise force. Prior to this invention, these types of processes were considered virtually impossible to automate due to the immense programming that was required to account for inconsistencies between parts and the abrasive wear.
The innovation didn’t stop there. After selling the first AFD systems it became apparent that there was a lack of rotary spindles that could be mounted on the compliance device. In the late 90’s, most of the spindles on the market were very heavy, since they were designed for CNC’s and other fixed automation machines. On the other hand, there was a plethora of pneumatic tools; however, these were not robust enough for robotic surface finishing applications. These pneumatic tools would slow down when they came in contact with the part or when there was a drop in air pressure. Both of these factors contributed to inconsistent surface finishes. PushCorp solved the weight and consistency issues with our revolutionary servo spindle, which was released in 1997. The liquid cooled permanent magnet, servo spindle was not only lightweight, but also provided a high power-to-weight ratio and constant speed enabling consistent material removal.

E.E: What’s the news about new products?
PushCorp: The PushCorp SM1202 is our smallest high-speed servo spindle and is an ideal solution for robotic material removal applications such as: Robotic Grinding, Sanding, Polishing, Deburring, Routing, and Deflashing.
The SM1202 can be ordered in a Random Orbital Sander or ER Collet Configuration. The sander has a Random Orbital Shaft that is designed to balance a 3″, 5″, or 6″ backup pad. The sanding configuration comes standard with a dust collection shroud to extract dust from the parent material’s surface.
E.E: What are the ranges of products?
PushCorp: We have a wide range of material removal equipment that is designed for robotic applications. They include:
- Force Compliance devices
- Servo Spindles
- Belt Sanders
- Floor mounted belt sanders and finishing equipment
- Custom Tool Holders
- Cables
- Automated Paper Changers
- Weld Shaving equipment
E.E: At what stage is the market where you are currently active?
PushCorp: The market for automated material removal has grown more in the last 5 – 10 years than it has in the previous 20. This is partially due to the maturity of other application like robotic welding and robotic sealer apply, but also markets which have traditionally had a robust labor force available starting to adopt robots as well.
We are currently selling globally în North/South America, Europe, Asia, and Australia. We have multiple distributors în these continents who have a tremendous amount of experience în robotic material removal applications.
E.E: What can you tell us about market trends?
PushCorp: In the last few years we have seen a major uptick in foundry applications. These are more dangerous and labor intensive than many other material removal applications. This is due to harsh environments where they are manufactured as well as the tools needed to process the parts.
We have also seen a trend of manufactures trying to optimize their production space so they have pushed for smaller more compact automation cells. As a result, we have allocated engineering resources to develop smaller tools with very high power to weight ratios in order to complement the smaller industrial and cobot market.
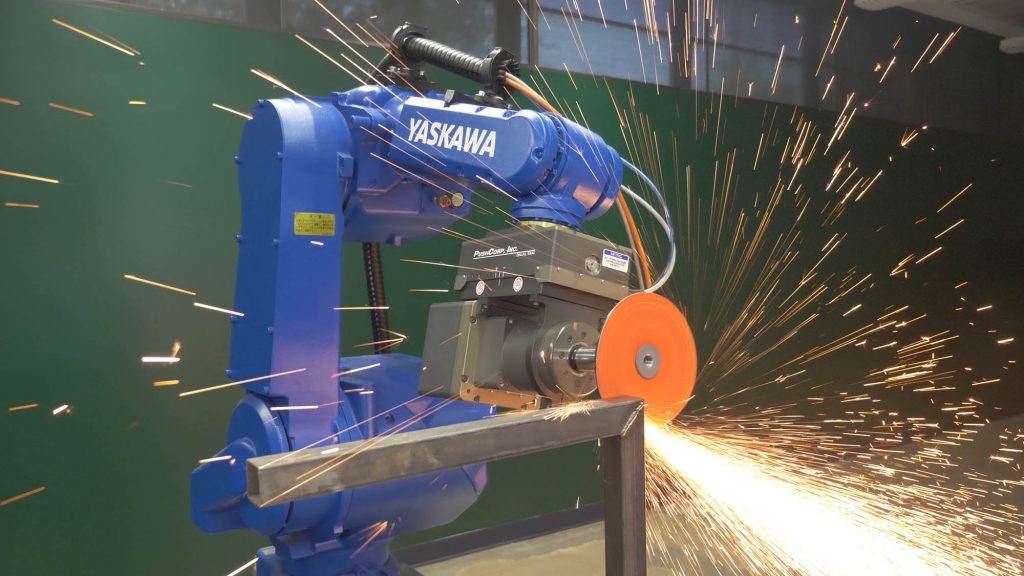
E.E: What are the most innovative products marketed?
PushCorp: Our active force control technology is what sets us apart from our competitors. PushCorp force control, also known as a force compliance device allows a robot to maintain a consistent yet adjustable force when in contact with a part’s surface. A standard industrial robot moves from point A to point B without any regard for the amount of force it is applying. When attached to robot arm, their sliding carriage allows whatever tool is attached to maintain contact with the part’s surface with a specific force. Unlike force torque sensors and through the arm compliance, our device does not have to compensate for the mass of the robot arm. This makes our equipment more accurate, precise, and easier to use than any other force compliance on the market.
Active Compliance devices apply consistent force in any orientation automatically. Just tell it what force you want and an active tool will apply it up, down, sideways or any orientation in between. This makes it a great candidate for parts with curved surfaces.
Passive devices rely on external, customer-supplied air pressure regulators to set the applied force. They work extremely well for less demanding flat or prismatic parts or more specialized processes like Weld Shaving, where high-accuracy force control is unnecessary.
E.E: What estimations do you have for 2023?
PushCorp: We expect to see the overall material removal market grow as labor shortages continue for these dull, dangerous, and dirty jobs. We feel that the many manufacturers are hungry to adapt robotic processes and that we are just seeing the tip of the automation iceberg.