R.A Jones is a global leader in the design and manufacturing of innovative packaging technologies and process solutions. R.A Jones’ advanced machines and high-speed equipment are state of the art and built to last – they are used by consumer packaged goods companies as well as store brands all over the world. It’s likely that many of the things you eat and drink have been packaged using their machines. The company operates three manufacturing sites on two continents – two in the U.S., Covington, Kentucky, where they’re headquartered, and Davenport, Iowa, and one in the United Kingdom in Liversedge.
With more than a century of engineering experience and superior customer service, R.A Jones is committed to partnering with customers in diverse markets to find solutions to their production line, supply chain and service challenges.
Interview with Nate Smith, Director of Engineering at R.A Jones.
Easy Engineering: What are the main areas of activity of the company?
Nate Smith: R.A Jones builds primary and secondary packaging machinery for the beverage, chemical, consumer goods, dairy, food, pharmaceutical and industrial markets. R.A Jones has an extensive portfolio of solutions for applications ranging from aerosol, cartoning, chub packaging to cup filling and sealing, multi-packing for beverages and canned foods, pouching and modified atmosphere packaging.
E.E: What’s the news about new products?
N.S: R.A Jones takes great pride in working collaboratively with brand manufacturers to find packaging solutions that will deliver on product quality, safety and convenience. This includes finding alternative packaging formats to meet brand’s sustainability goals, which are being increasingly driven by consumer, customer and retailer needs and demands. R.A Jones recently partnered with The Bumble Bee Seafood Company to develop a recycle-ready packaging solution(suggest using Bumble Bee Seafood Recycle-Ready Packaging with paper board sample image here) for their multi-pack can products. In a market-first effort to package seafood multipacks with paperboard, R.A Jones customized its multipacker machine to enable Bumble Bee to transition away from shrinkwrap and further its commitment of reducing ocean waste without sacrificing product quality.
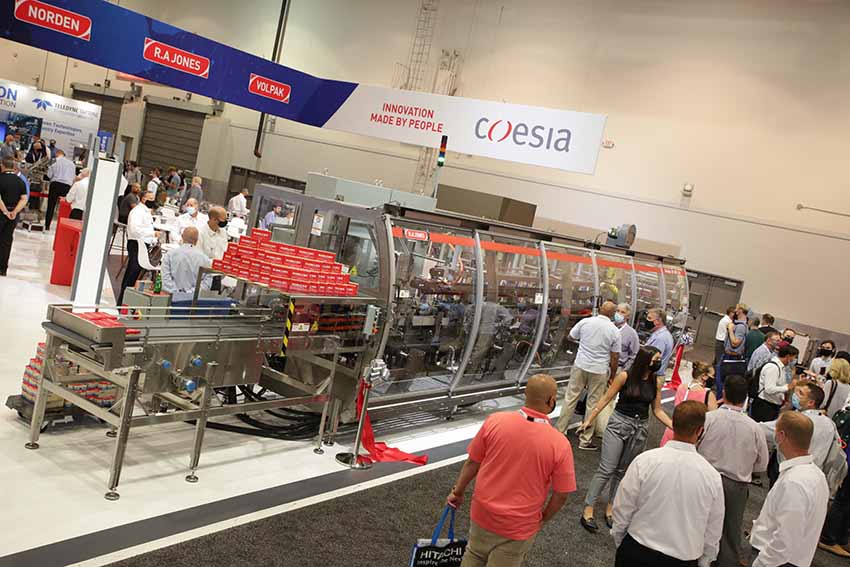
Bumble Bee’s Meridian XR MPS-300 (suggest using Meridian XR MPS-300 multipacker image) made its debut at PACK EXPO in Las Vegas in late September and is being shipped to Bumble Bee by the end of the year. The Meridian XR was able to meet Bumble Bee’s needs of enhanced operational performance, speed and reliability because of the equipment’s high adaptability. The multipacker’s unique features include a four-lane infeed for new packaging options and configurations, an air frame for reliable carton opening, integrated can count verification after loading, six- and 12-inch dual pitch transport, and more. Bumble Bee’s new recycle-ready packaging format is expected to launch in-stores in 2022.
Earlier this year, we also launched an automatic magazine loader (AML) (suggest using AML – Case Infeed Station image here) for use with our cartoning machines to help alleviate the expanding labor and demand challenges impacting CPG companies up and down the supply chain. Modular in design and easy to use, the cost-effective solution enables manufacturers to implement a labor-saving automated technology into the production line and increase output speeds within a small footprint.
The AML pulls cases off a conveyor and orients them properly for loading. It then extracts cartons from a case and loads them onto the magazine before disposing of the case. This innovation greatly reduces the number of employees required to run a line. As an added benefit, the AML eliminates the need for the human operator to pick up and rotate each individual case—a traditionally repetitive, injury prone motion.
For a plant that may run 300 cartons a minute and must function 24/7 to meet heightened demand, AML yields significant time and cost savings while helping to solve universal labor shortages and retention challenges.
R.A Jones is also offering new digital solutions developed by its parent company called Coesia Digital on its packaging machines. The suite is a full range of products designed to support a customer’s operations physically and remotely, helping them monitor machine pool in real time and prevent breakdowns and unplanned stops by exploiting data analysis and artificial intelligence (AI). The suite includes PerforMate (an integrated IoT platform for real time machine monitoring), OptiMate (a new machine interface with connectivity and smart functionalities to optimize equipment quality and performance), and UltiMate (a digital appliance for predictive analytics and AI performed at machine level).
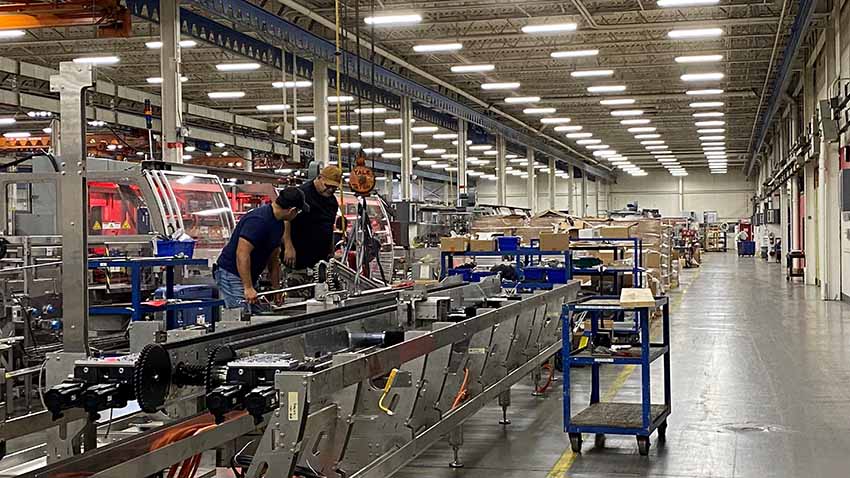
E.E: What are the ranges of products?
N.S: R.A Jones has a myriad of innovative packaging machines in its portfolio that are used for just about every major consumer product goods on the market. From our KP-Aerofill aerosol brands which are used to fill everything from food and personal care goods to automotive and chemical products to our Pouch King, a high-speed, horizontal form-fill-seal pouch-filling machine for cereals, candy and other snacks. While we’re known for creating high-quality, durable and reliable packaging technologies, R.A Jones is constantly innovating to develop smaller, faster and more flexible machines to meet customer and industry demands.
E.E: What can you tell us about market trends?
N.S: We’re seeing market trends focus around key initiatives that help companies lower their carbon footprint, address supply chain bottlenecks and increase speed to market. Brand manufacturers.
continue to search for more sustainable packaging solutions which can include reducing the amount of packaging used to protect a product, developing shelf-ready shippers, or identifying new material alternatives that eliminate plastics use in its entirely. In the pandemic era, we’ve seen buying habits change with more consumers shopping online and in greater bulk – a trend that is expected to continue for the foreseeable future. To therefore mitigate the ongoing supply chain problems and reduce the time it takes to get products on store shelves, CPGs will need to look towards digitizing their production lines, upgrade to faster and more flexible machines, and adopt labor-saving automated technologies to keep pace with consumer demand and behaviors.
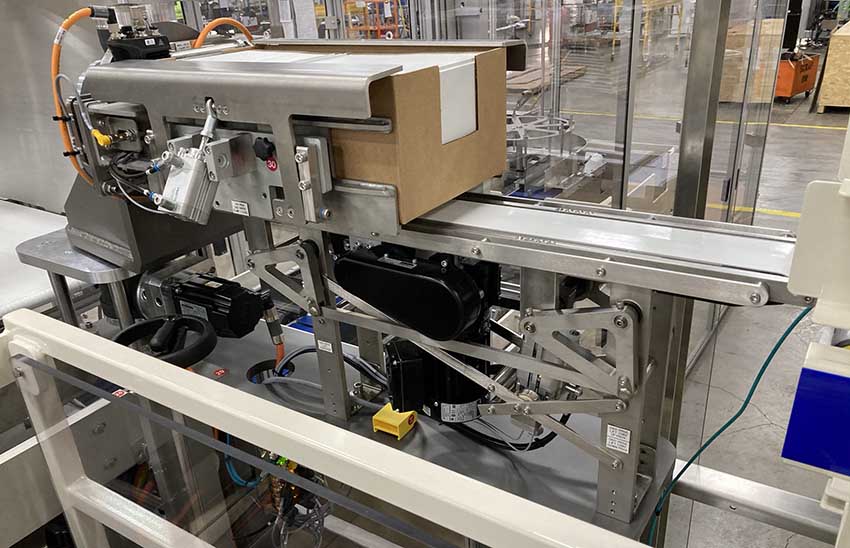
E.E: What estimations do you have for 2022?
N.S: The supply chain crisis is expected to continue to impact just about every major industry into 2022, so companies must look for new ways to address consumer demand spikes and labor challenges. While Covid-19 has accelerated the need for more connected machines and digital solutions, the ongoing supply chain delays and wide-spread shortages will push even more CPGs – who are facing a shortage of workers – to consider automating their production line to increase manufacturing output. By implementing the latest smart machine and line controls using artificial intelligence and machine learning, CPGs can achieve more efficient and reliable solutions with greater production flexibility.
As companies move towards a more robust digital integration of their manufacturing process, finding the right partner with a diverse suite of customizable cloud-based support services will be crucial. Building the capabilities that improve their overall equipment effectiveness, maintain a skilled workforce and minimize costly downtime will drive healthier, more productive operations.
R.A Jones is part of Coesia, a group of innovation-based industrial and packaging solutions companies operating globally, headquartered in Bologna, Italy. To learn more about R.A Jones’ packaging technologies and service offerings, visit www.rajones.com.