Roboze designs and manufactures the world’s most accurate 3D printers for producing parts with super polymers and composite materials to replace metals in industries with extreme working conditions.
The main goal is to shape a new paradigm in digital manufacturing: Roboze Distributed Manufacturing that connects demand with supply, creating a distributed production model, which allows to produce avoiding waste, reducing shipments and CO2 emissions, bringing production back to the point of use.
Consistent with their goal of expanding the adoption of 3D printing with innovative materials to accelerate the digital and sustainable transformation of companies, the company has decided to gather their experience and put it at the service of those companies that want to explore the advantages and trends of the market in which they operate.
Interview with Fabrizio Brandi, Marketing Director at Roboze.
Easy Engineering: What are the main areas of activity of the company?
Fabrizio Brandi: We provide advanced 3D printers for high temperature and high strength super plastics, also offers the chance to produce custom finished parts On Demand and Just-in-Time through its manufacturing as a service global network. We are replacing metals parts, helping our customers in cutting costs and time up to 80%, producing end-use parts in super polymers and composites through our patented 3D printing technology, made accessible thanks to customers-centric business models like subscription and on demand marketplace.
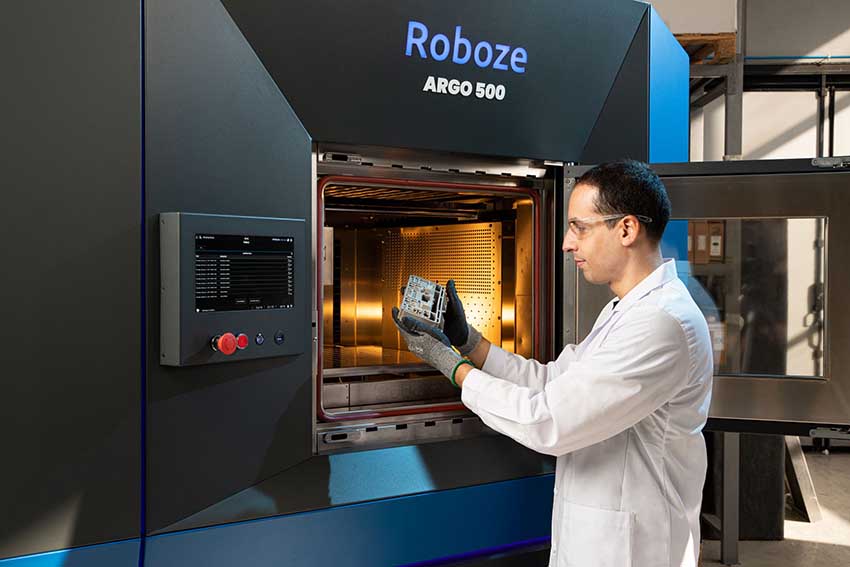
E.E: What’s the news about new products?
F.B:We launch 3D printers PRO Series, which has been designed to enable functional prototyping and additive manufacturing with super polymers and composites. The One PRO and Plus PRO machines are the latest Roboze product offerings to facilitate the replacement of metals in the product development cycle. Both of Roboze’s PRO Series machines are equipped with a 300 x 250 x 200 mm build plate, which can reach temperatures of 100°C, and can print at a precision of 15 microns. They can process composite materials like: Carbon PA, PEEK, Carbon PEEK, PEKK.
During the last Formnext we presented a new bio-based polyamide. The new material originates from renewable sources and is the first result of our intense research for the development of super materials of the future. The new techno-polymer was produced with a bio-based matrix reinforced with natural fibers.
We believe that sustainability is the “necessary prerequisite” for lasting progress for people and the planet. We invest in research and development of diversified solutions to satisfy the various stages of development and production of goods, which it says is a strategic choice for obtaining answers and proposing corrective actions to current business methods and models.
E.E: What can you tell us about market trends?
F.B: 3D printing is a growing manufacturing technology that offers unparalleled design freedom and possibilities. Since it can simplify or eliminate manufacturing constraints such as the production of moulds, AM (Additive Manufacturing) is fast, agile, and innovative and will keep growing in the future.
3D printing offers a plethora of options in the production, design, and performance of novel parts and materials. It is more agile, faster, and innovative compared to more traditional manufacturing techniques, and this is reflected in the fact that the CAGR of the 3D printing sector is expected to be 24.3% by 2027.
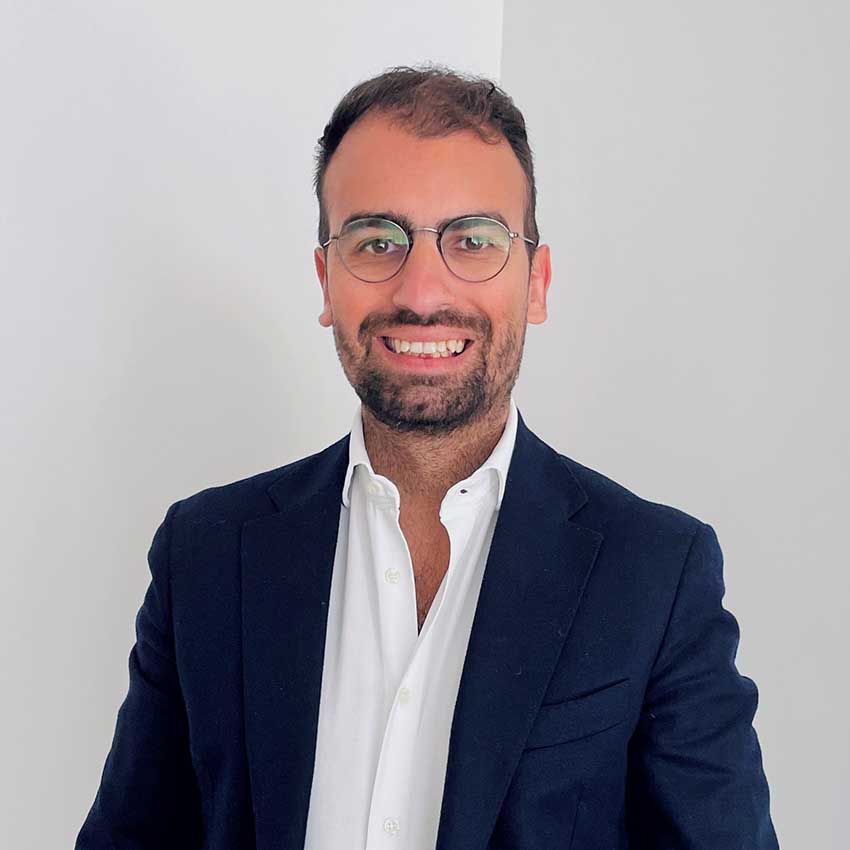
Fabrizio Brandi, Marketing Director at Roboze.
The use of Roboze additive manufacturing solutions has spread to many sectors: Manufacturing, Energy, Mobility, Aerospace, Education, and Medical.
The greatest user of Roboze technology is the Manufacturing sector with 26% of the applications, where fast and cheap production of tooling and manufacturing of spares are the main drivers.
This is followed by the Energy and Mobility sectors with a fifth of applications each. In these sectors, the focus is the same: optimization of parts and reduced weight, as well as spare parts and tooling.
E.E: What are the most innovative products marketed?
F.B: The most innovative product marketed is our industrial 3D Printers ARGO500, The ARGO 500 platform allows the replacement of metals in numerous applications with enormous advantages in terms of lightness, mechanical strength, workability, and chemical resistance.
It provides repeatable, controlled, and traceable systems that allow customized production for each individual customer in every part of the world. Everything is designed to bring 3D printing into the new era of industrial production of customized medium batches, reducing time and costs for manufacturing companies.
This technological evolution allows the real application of the Manufacturing as a Service model, where additive manufacturing centres for goods close to the point of use, known as Roboze 3DParts certified manufacturing partners, significantly affect the production and procurement costs of a company. Since the goods are produced locally, savings on logistics costs are immediate, thanks to the greater involvement of the end customer making it possible to reduce inventory costs.

E.E: What estimations do you have for 2023?
F.B: The next 10 years will be key in increasing end-user awareness of the benefits of industrial additive manufacturing. This will lead to new challenges that we think will be played out on two distinct levels: sustainability and the integration of technology into all stages of production. Roboze is already working on both fronts, proposing not only innovative technologies and materials, favoured by our strong nature in the research and development of completely new and competitive ecosystems, but also more sustainable business and financial models.