Seiki Corporation is the largest Japanese manufacturer of Hotrunner Systems for plastics and LSR (Rubber) injection moulding. Seiki’s headquarters are located in Yonezawa (Japan) approx. 2h by high speed train from Tokyo. The company has factories in Yonezawa (Japan) and Shenzhen (China), subsidiaries in China (Shenzhen), Germany (Dieburg), USA (Chicago), Hongkong, Philippines (San Rafael) and sales offices in Shanghai (China), Bangkok (Thailand), Jakarta (Indonesia), Silao (Mexico), Suwon (Korea), Taipei (Taiwan), Essex (England).
Seiki Corporation has around 200 employees worldwide.

Easy Engineering: What are the main areas of activity of the company?
Seiki Corporation: Development and production of hot runner systems for plastics and LSR runner-less injection moulding and development of controllers for the automation of hot runner systems.
E.E: What’s the news about new products?
Seiki Corporation: Seiki’s systems with separate heating of the nozzle tips for high precision runner-less injection moulding are still outstanding in the market for hot runner technology.
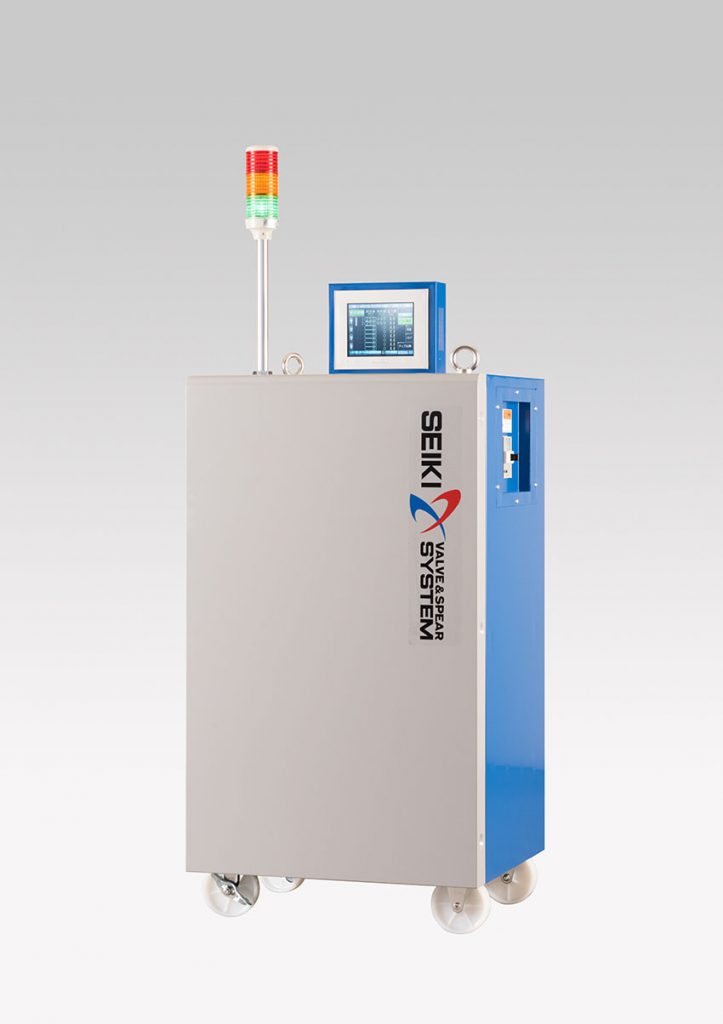
In the last years we introduced the:
- WMC hot runner controller for full automation with included leakage prevention system and full HR surveillance
- the SMV Valve Gate System for tools with limited height (120mm) and small pitches as small as 29mm including our tip-heater technology enabling the use of super engineering plastics reinforced with glass- or carbon-fibers
- the SPT Spear System (miniaturized open-type nozzle with thermal close-off due to our tip-heater system) for pitches of 9mm and the use of reinforces resins
- the TS Valve System for “Sandwich” moulding (moulding of multiple layers of plastics in one shot, e.g. for the embedding of barrier layers)

E.E: What are the ranges of products?
Seiki Corporation:
- Hot runners for the usage of all kind of plastics and LSR / Rubber in injection moulding: valve gate nozzles with hydraulic, pneumatic, electric actuation, open-type nozzles, Seiki Spear System with thermal closure of the nozzle tips for shorter cycle times and the usage of highly reinforced resins (e.g. glass fiber), hot-halves, pre-wired hot runners, single nozzles, manifolds in all sizes and shapes; heaters for hot runners.
- Controller Technology for Hot runner Systems
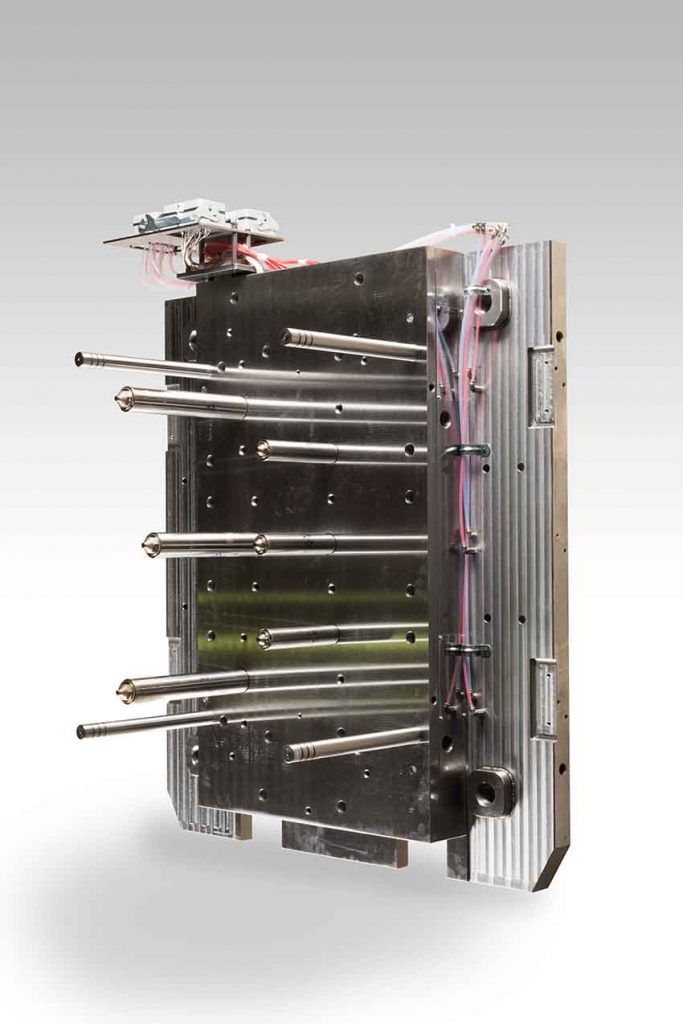
E.E: At what stage is the market where you are currently active?
Seiki Corporation: Our hot runner technology profits from the stricter regulations concerning the use of plastics in many countries, as injection moulding needs to be more efficient as waste, for example stemming from the use of could-runners or sub runners, needs to be reduced.
Resin costs are rising which is also leading costumers to invest into runner-less – hot runner technology.
Automatization is progressing in every market, our systems with separate heating of the nozzle tips enables customers to shorten cycle times and increase production output of their injection moulding machines.
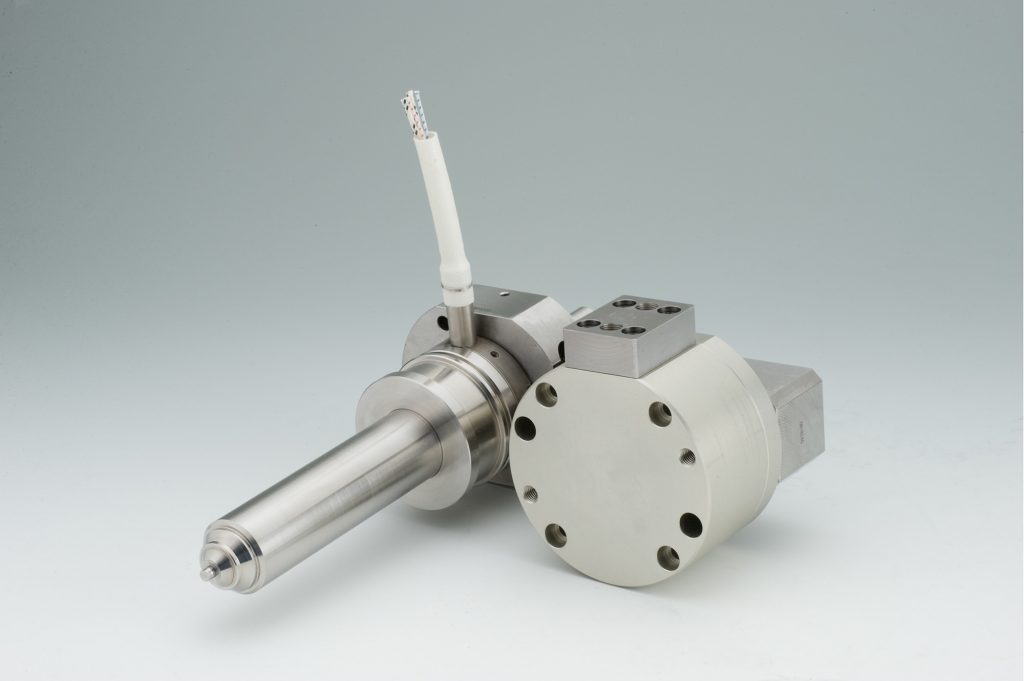
E.E: What can you tell us about market trends?
Seiki Corporation: Market faces some difficulties due to the corona pandemic as many customers face procurement issues (e.g. semi-conductors, resin) and related cost issues.
Nevertheless, hot runner makers invest in digitalization (Industry 4.0 approach, AI in hot runner controllers, sensor systems for real-time tracking of moulding parameters, pre-emptive production quality control, etc.).
E.E: What are the most innovative products marketed?
Seiki Corporation: The 3D printing of metals enters the market, based on this technology mould makers are able to realize new pitches and mould designs, e.g. the 3D printing of cooling bushes enables us to provide new solutions to our customers enabling even shorter cycle times by employing our tip-heating (thermal closure nozzles) technology.
3D printing also plays in terms of the manufacturing of nozzles – reducing the mass (nozzle) that needs to be heated saves energy costs in terms of heating and cooling.
Sandwich moulding (covering recycled materials with layers of new resin) for the use of recycled plastics in packaging for food and beverages could be a game changer concerning the move towards circular economy.
The use of biopolymers and bio-degradable plastics increases (due to the high oil prices, these types of resins from biomass become competitive).

E.E: What estimations do you have for 2022?
Seiki Corporation: We think that the negative effects of the Corona pandemic are mitigated in from the second half of 2022.
Continuation of the boom in the market for connectors and battery related plastic parts due to the shift towards electro mobility.
Increase in the use of bioplastics