As a global industry expert, NETZSCH has been active in plastic material science and sensor technology for over 50 years. Over the last two years, sensXPERT® adopted and rethought the technologies they have in place as a group to help plastics processors and ecosystem stakeholders to achieve unseen holistic process stability, thus allowing dynamic manufacturing.
sensXPERT realizes the full potential of smart manufacturing through the vertical integration of unique state-of-the-art, AI-powered, cloud-based process control tools in combination with NETZSCH Group’s renowned material measurement instruments.
The plastics manufacturing solution is data-driven and enhances productivity in real-time. Sensors measure and stream machine data that allows an AI-based answer to characterize materials dynamically and control all necessary influencing factors to optimize the molding process.
Dielectric sensors are the heart of the system, favorably positioned at or close to the main gate, while the second one sits best at the end of the flow—regardless of part size. Data collected by the sensors are transferred to the sensXPERT edge device, which is placed machine nearby. The edge device acts as an industrial PC with the main task of evaluating and communicating the data received to the Cloud via secured servers maintained by Amazon Web Services.
Besides the immense measurement hardware know-how incorporated in their sensors and the edge device, the sensXPERT technology excels in its mathematical and physical/chemical models of material behavior and machine learning algorithms that constantly scan incoming data for patterns and deviations in the background. The algorithms translate the raw sensor data into predictive quality criteria, feeding them back to technicians, monitoring a given machine and process via a web app.
An additional layer of machine learning algorithms supports the system parsing the process parameters and sensor data flowing in from customer molds in manufacturing facilities worldwide, displaying the process outputs and operating conditions using data science. Over time, the amount of data created enables predictive analytics to kick in, thus promising unseen process stability. In more depth, algorithms note data set deviations; correspondence starts with the local edge device, which alerts the workers that monitor the process. The machine learning models running in the background experience consistent retraining when patterns change, ensuring the process’s performance.
Interview with Cornelia Beyer, Managing Director at sensXPERT.

Easy Engineering: What are the main areas of activity of the company?
Cornelia Beyer: Once started with the intention to optimize plastics manufacturing processes, it turned out to be heavily impacting and contributing towards sustainable production, achieving to decrease of up to 50% of existing scrap, 23% in energy savings, 30% cycle time reduction, and 15 days p.a. in downtime and installation reduction. sensXPERT is committed to providing the change for sustainable plastics production that is so desperately needed. The integrated product solution addresses plastics processing companies and their diverse stakeholders worldwide. sensXPERT supports several manufacturing processes like (Reaction) injection molding, resin transfer molding, compression molding, vacuum infusion, and others. Various studies and reports show that injection molding is the most dominating plastic part production market and is also currently the strongest for sensXPERT.
E.E: At what stage is the market where you are currently active? / What can you tell us about market trends?
C.B: The industry needs to see a step change caused by cost pressure, supply chain challenges, and legislative and public pressure regarding sustainable goals, such as material recycling, reduction of energy, scrap, and optimization of production processes, are steadily increasing.
Customers seek end-to-end, integrated, and tailored solutions to tackle their challenges around consistent process stability while ensuring cost efficiency.
Unfortunately, many topics and aspects get mixed up when discussing sustainability and ecologically friendly measures. The industry needs to look at fast and efficient actions, differentiating between long-lasting and disposable products, especially emphasizing avoiding single-use plastic packaging.
Another significant issue is recycling and the clean separation of the materials. The challenge of the plastics industry is dealing with the enormous number of plastics in the market – around 500 different plastic materials – that cannot be shredded together and recycled easily. On the other hand: Nothing works without plastics in lightweight production.
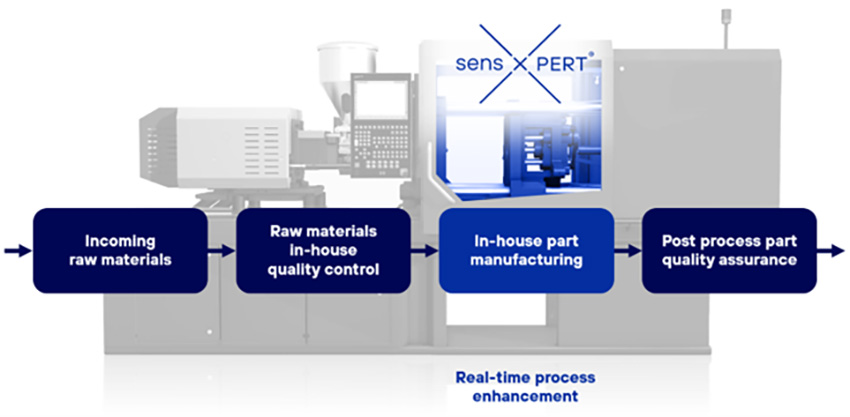
E.E: What are the most innovative products marketed? / What is the innovation sensXPERT stands for?
C.B: At sensXPERT®, we turn data into product quality.
From a technological perspective, we offer a solution combining material science and an in-mold material evaluation system that provides real-time answers. The know-how and complex and sophisticated sensor technology come with broad domain knowledge and leaves the market looking for its equal. In addition to creating complete transparency in the manufacturing process of plastic parts, sensXPERT openly welcomes ecosystem partners who understand that stand-alone solutions will not be sufficient to meet tomorrow’s customer needs in increasing production challenges.
We consider ourselves thought leaders and collaborators, true to the motto: Better together!
In the long run, we all benefit from a more profound understanding between machine, process, and inline material behavior, which becomes more measurable through collaborations.
In a nutshell, sensXPERT stands for
- Dynamic cycle times – up to 30% cycle time reduction
- In-mold quality control on each part produced
- Tackling raw material deviations in real-time
- Turning machine, mold, and material data into quantitive numbers
- Sustainability in focus – up to 50 % scrap reduction & 23 % energy cost savings
The solution enables customers to break predetermined processes and verifies that shorter production cycles do not impact the final component’s high material quality. Further, we prove to our customers from varying industries, such as Automotive, Aviation, and Electronic Applications, that certain process amendments make sense to enhance materials for better results. An intelligent monitoring and evaluation solution is beneficial, particularly in the shortage of skilled workers.

E.E: What estimations do you have for the rest of 2022? / What is sensXPERT’s market strategy for the next year?
C.B: Europe is sensXPERT’s entree region with a strong focus on the DACH market. However, being in the public eye creates awareness. We happily onboarded customers from Mexico and Australia and plan to expand officially to North America and Latin America next year. We serve clients from diverse industries, including automotive, aerospace, building & construction, renewable energy, electrical application, military defense, consumer goods, and electronic encapsulation. As we stated before, sensXPERT sees itself as a thought leader, keeping in mind that customer centricity is key. Therefore, a strong commitment goes toward the establishment of a robust ecosystem. We aim to build stakeholder collaborations to exchange know-how, create additional benefits, and leverage synergy effects.