SIKO is a German manufacturer of sensors and positioning systems. Beside two factories in Germany, they have subsidiaries in Switzerland, Italy, Singapore, China and USA. Today SIKO sums up five decades of experience in length, angle and speed measurement technology. Building upon this core competence, SIKO develops and manufactures products for automation and drive engineering.
Interview with Christian Fischer, SIKO Head-of-Marketing.
Easy Engineering: What are the main areas of activity of the company?
Christian Fischer: SIKO focuses on the development and manufacture of sensors and positioning systems for customers in industrial and mechanical engineering sectors. As a solution provider for demanding measuring tasks and automation processes, we supply our products to all conceivable sectors of industry. SIKO sensors are used in computer tomographs, operating tables, packaging or woodworking machines, elevators or in industrial 4.0 manufacturing, e.g. for the production of smartphones.
E.E: What’s the news for 2020 about new products?
C.F: We are currently expanding our product portfolio in the areas of sensors for mobile machines, production automation and drive technology as well as positioning systems for mechanical engineering. An example is our new magnetic encoder MSA213C is developed for handling and assembly automation, machining systems, pick-and-place applications or PCB processing. The encoder impresses with its small design and its high absolute resolution of 1 μm, ensuring precise position detection at all times. Absolute measurement is essential, especially in safety-relevant applications when a change in position has to be reliably detected, even if power is off. The repeat accuracy achieved of ± 1 μm enables reliable use in multi-axis applications or positioning systems where exact control and position recognition is required. It achieves this performance level over a length of up to 16 meters.
The MSA213C is available with many different absolute interfaces so that it can easily be integrated into the application by the customer. Even in the basic versions with SSI, RS485 and BiSS-C, the sensor is also available with IO-Link and supports protocols from various control unit manufacturers. In addition, an incremental interface is available in parallel as a digital line driver or analog 1 Vss signal output.
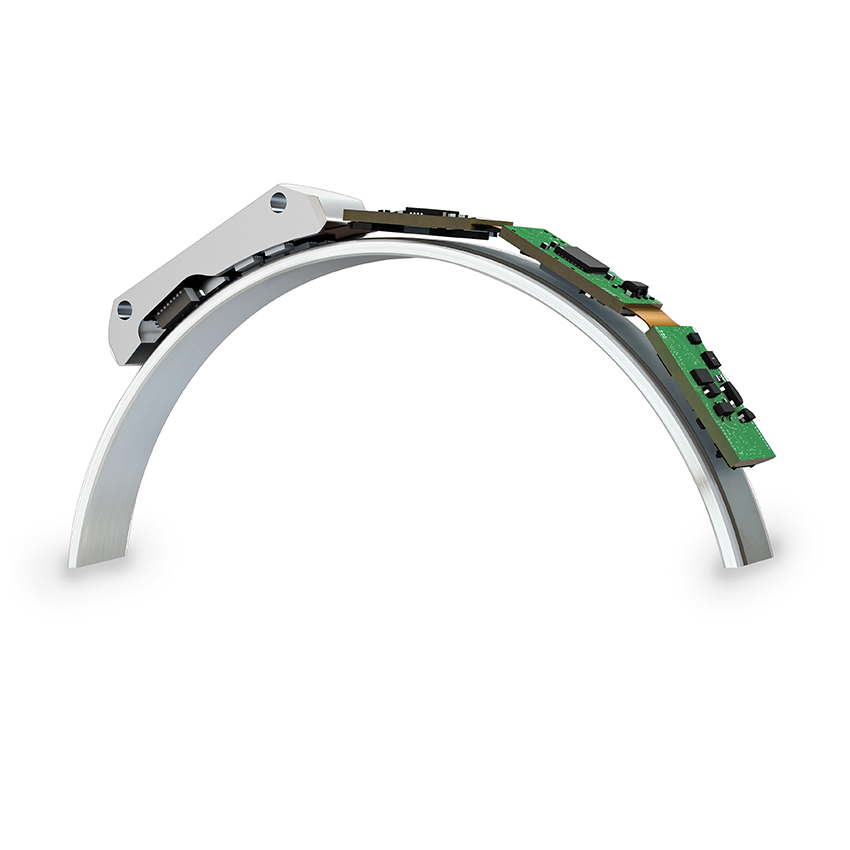
E.E: What are the ranges of traded products?
C.F: SIKO is known for having a wide range of products in every category on offer. Strictly speaking, we are a manufacturer of variants, offering products that are manufactured for our customers in over 1000 variants, for example. This fact shows that SIKO always puts the customer’s wishes first. This means that every customer receives exactly the product that is not only good but also perfectly tailored to his needs. We are constantly working to develop customer-specific solutions with or for our customers, for example, if new applications that place special demands on sensor technology are required. Therefore, we see ourselves as a partner for our customers and as a solution provider who listens and understands exactly what our customers need.
E.E: At what stage is the market where you are currently active and what can you tell us about market trends?
C.F: The market is very dynamic in every sector where we offer our products. Recently, and also in the future, certain communication protocols, such as IO-Link, are becoming increasingly important. Our products must speak the language of the customer’s machine so that they can be easily integrated. This means that we have to recognize constantly coming trends and adapt our own products to them. In addition, more and more legal requirements and regulations play a role, so our sensors have to meet legal standards all around the world in order to be accepted by the market. Also, requirements such as predictive maintenance are increasingly important to monitor machines and detect failures or maintenance needs in advance. Data migrates via the cloud to the smartphone and the machine operator recognizes, for example, that stiff mechanical components on his production machine need to be lubricated. This prevents a machine from failing at some point, resulting in a loss of production and sales.
E.E: What are the most innovative products marketed?
C.F: This question is not so easy to answer. Sometimes a new mechanical realisation of a product that you have been manufacturing for many decades, which actually seems quite simple, is very innovative and causes you to suddenly open up completely new fields of application. For example, we have rethought our draw-wire encoders, which are used to measure linear adjustments via the draw wire, and have invented a draw-wire encoder that can be integrated into hydraulic cylinders as a position measuring system. This was and is very innovative. But also innovative are our electronically complex and intelligent position sensors, which have to be very small and flexible, for example to adapt to various diameters and minimum installation spaces. An example for this is our new encoder MSAC200 with flexCoder technology. The MSAC200 can be flexibly adapted to the customer’s design and provides precise absolute values with high installation tolerances at the same time. It is basically possible to adapt the encoder and the magnetic ring for precise fitting, for example in motors. An additional feature is the high reading distance ≤0.6 mm and axial tolerance of ±0.2 mm to facilitate the design of the overall system and enable use in dynamic applications.
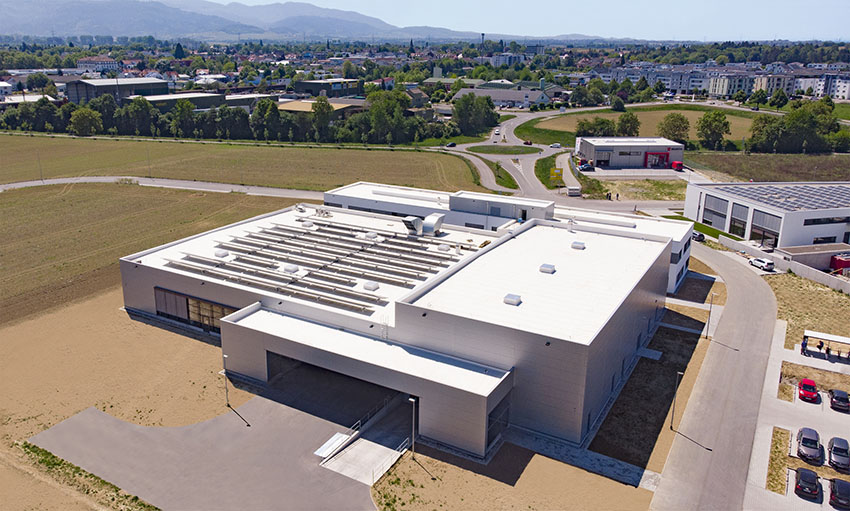
The flexibility of adaptation of flexCoder technology allows it to be built exactly into the customer’s design. The key factor is that both the sensor and the scale can be adapted. For example, this makes it possible to use the compact sensor mount, and modification is required only to the attachment of the scale on the customer’s shaft. With other applications, a standard SIKO magnet ring is used and the mounting of the flexible sensor array and the evaluation and interface electronics are adapted to the customer’s specific fixing options in the housing. Since the electronics can be both bent and stacked, integration can be very compact. Thanks to these adaptations to the encoder and rule with regard to the shaft diameter and the fixing options available, the application can be designed more compactly and more uncompromisingly.
E.E: What estimates do you have for 2020?
C.F: The year 2020 is very challenging due to global lock-downs in the Covid-19 situation, for all of us. SIKO had learned from previous crises and has a large stock of components. We were not affected by the partial collapse of the supply chain due to missing electronic parts from China, we were always able to deliver. But we also had to adapt quickly to a new digital working world with home office, remote meetings etc. within the framework of the circumstances. We still hope that restrictions in the world will soon be lifted and that physical meetings and events will be possible again. The hope is for spring 2021. With our new and modern factory in Bad-Krozingen, based in the south-west of Germany, we are prepared for the future.