STADLER is a global leader in the design, manufacturing, and assembly of automated sorting systems and machines for the recycling industry. The origins of today’s STADLER Anlagenbau GmbH date back to 1791, and the business has been family-run for seven generations.
Easy Engineering: What are the main areas of activity of the company?
STADLER: STADLER is a globally active business which to date has installed more than 400 complete turn-key systems and sold more than 1.000 ballistic separators worldwide. STADLER’s headquarters are located in Altshausen in southern Germany. One of the company’s two production facilities is also located in Altshausen, the other in Slovenia. Both manufacturing plants have a technical centre where customers can test their materials on STADLER machines.
STADLER also has sales offices in several European countries, in South America, and North America, as well as partner companies in a number of nations around the world including Australia, Mexico and Japan.
E.E: What’s the news for 2020 about new products?
STADLER: New this year is STADLER’s close cooperation with Krones, a specialist in beverage filling lines and technology leader in plastics recycling lines. STADLER and Krones now jointly offer high-quality turn-key solutions, from sorting out a plastic bottle from a mixture of recyclable materials all the way through to producing the new, recycled plastic bottle.
Also, in 2020, STADLER acquired a stake in weeeSwiss, a specialist in electronic scrap recycling plants. STADLER anticipates strong annual growth in waste volumes in this sector, and for environmental reasons it is essential to offer suitable solutions for modern recycling.
Another exciting development in 2020 is in Scandinavia, where STADLER has built the first automated textile sorting plant. More automated sorting of textiles can be expected in the future.
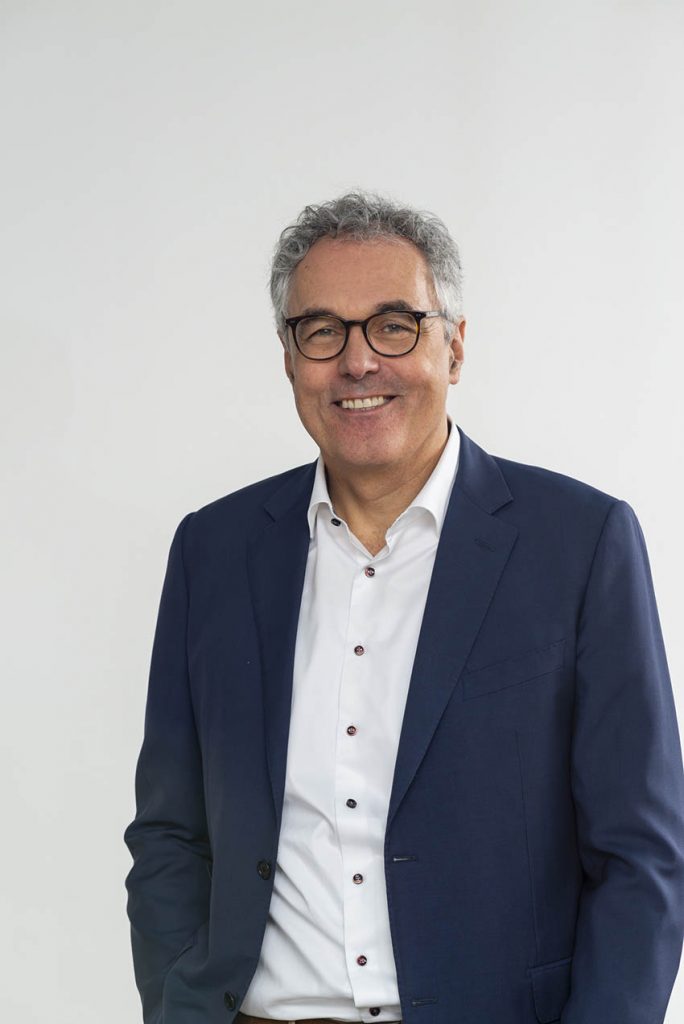
E.E: What are the ranges of traded products?
STADLER: STADLER produces turn-key waste sorting plants and individual sorting machines.
STADLER’s sorting plants handle a wide range of materials: municipal solid waste (MSW), dry mixed recyclables, paper and cardboard, plastic bottles, light packaging, film, industrial waste, construction and demolition waste, electronic waste, and wood, as well as producing refuse-derived fuel.
Some of STADLER’s sorting plants are small and some large. In fact, STADLER recently built the largest household waste sorting plant in the world. Located in Galicia, Spain, this has a capacity of one million tons per year. STADLER has also built the first fully automated MSW sorting plant in the world. This plant, located in Oslo, Norway, has won numerous innovation awards.
STADLER also designs and manufactures light- and heavy-duty conveyor technology, screening drums, ballistic separators, and label removers.
STADLER’s Label Remover can remove a large part of the labels from plastic bottles. This means that subsequent sorting, using near-infrared technology, is simplified and improved and the labels do not appear in the washing process. The Label Remover is designed in such a way that even large impurities in the mass flow, such as metals or inert material, do not damage the machine, guaranteeing high levels of machine uptime.
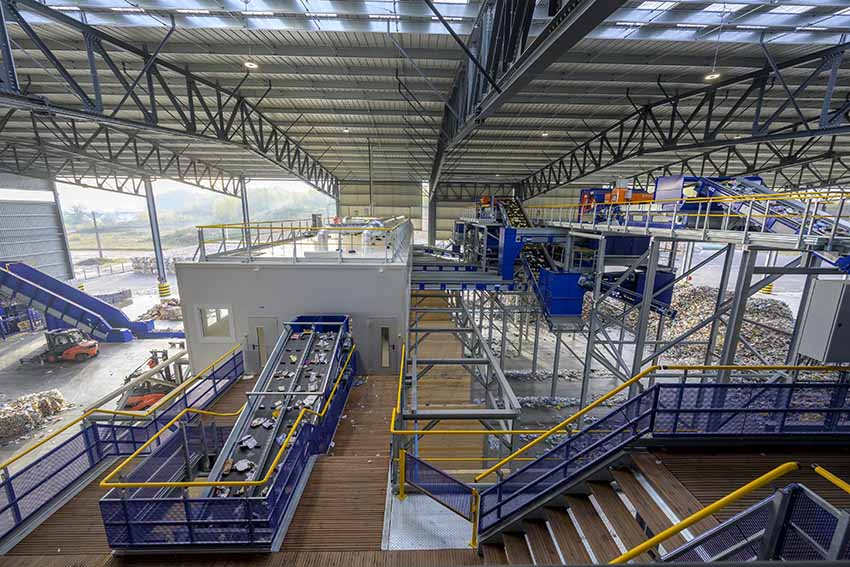
E.E: At what stage is the market where you are currently active?
STADLER: The sorting and recycling of valuable materials is still in its early stages in many countries worldwide. Even in Europe, a large proportion of waste, and the valuable materials contained within it, is incinerated or landfilled without first recovering materials for recycling. This of course has negative consequences for the environment. Therefore, there is still great potential for wider adoption of STADLER’s technologies.
E.E: What can you tell us about market trends?
STADLER: Recycling is constantly becoming more important because of climate change and the need for sustainability. There is an increasingly urgent need to reduce greenhouse gas emissions and to reduce the consumption of primary raw materials. STADLER’s technologies help address these important issues.
E.E: What are the most innovative products marketed?
STADLER: STADLER’s latest ballistic separator, the STT6000, is so robust that it can sort materials even if they are very heavy or unshredded. In an EU-funded project, NEW-MINE, several universities have cooperated to explore the potential of enhanced landfill mining for resource recovery from waste. This project and the STT6000 ballistic separator are a good example of the interaction between innovation, sustainability, resource conservation, and climate protection.
In another highly innovative project, STADLER has built one of the first sorting plants in the world specializing in film. The Integra Plastics plant in Sofia, Bulgaria, sorts the fractions into high-densitry polyethyelne (HDPE), polypropylene (PP), and low-density polyethylene (LDPE), and by colour (transparent, blue and green).
Also innovative is STADLER’s Service Data Cloud, a small internal start-up business activity involving young engineers and IT specialists. This collects varied data from STADLER’s plants in order to increase plant uptime and optimise the output and purity of the sorted products. This data is also very useful for preventive maintenance.
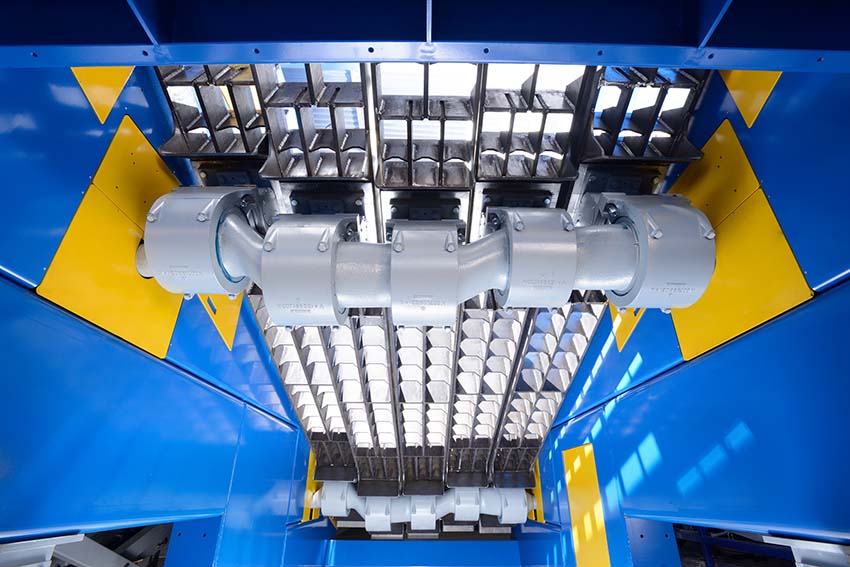
E.E: What estimations do you have for 2020?
STADLER: Due to the Coronavirus crisis, there have been severe restrictions in 2020, especially in the assembly area (though restrictions have varied according to country or continent). Another handicap is that all important environmental trade fairs have been cancelled. However, the demand for sorting and recycling technology remains very high. This means that, even if business activity is somewhat subdued in 2020, strong demand can be expected in the years to come.