The Perfect Process Company specializes in the application of Lean improvement methods to optimize processes, achieving significant business benefits through lead time reduction and right first-time delivery.
Interview with Neil Trivedi, Director of The Perfect Process Company.
Easy Engineering: Tell us about the importance of innovation in your field.
Neil Trivedi: Lean methods and techniques have now been fully accepted as standard manufacturing practice and in many organizations are quite mature. However, there is a requirement for constant training and refreshment of the skills as well adaptation to new situations and business challenges. Lean provides the basis for continuous improvement (innovation) and employee engagement. Expanding the scope of Lean to different areas of the organization outside the factory is the next logical step of progression for Lean.
E.E: Which are the most innovative products/solutions in your line-up?
N.T: From our experience the following are key innovation areas for Lean application within business organizations:
Manufacturing processes – One of the mistakes companies make when starting the Lean journey is to focus only on one or two tools and attempt to roll out that tool across the entire operation. To really drive customer value, the approach needs to consider the whole system, from order entry all the way through to delivery to the customer. This approach is called value stream improvement. It identifies what is happening in the process and detects all the wastes and issues that stop it being efficient. The final steps involve developing countermeasures and an action plan to drive customer value throughout the value stream
Business Processes: The focus for improvement in manufacturing organisations is always the factory first. However, when you consider the overall order to delivery process typically 95% of the time is taken up by activities outside manufacturing – so why improve the production line first? What about the office processes? We’ve found with many of our clients that 25-35% of business processes have never been defined, they are just a collection of activities done by a bunch of people over a period of time. In addition, we found 80% of issues are related to leadership and people behaviors rather than systems or processes. A focus on developing office processes to improve their quality and lead time will lead to benefits thought the end-to-end value stream.
The Green Factory: COP 26 highlighted the need for environmental change across all aspects of society. In manufacturing, the role of EHS manager has typically driven implementation through compliance, additionally there are new entrants to the field who lack experience in the area and revert to a directive approach to implementation rather than engagement and involvement. By using Lean as the foundation for Green deployment we’ve found that organizations can tap into the engagement and involvement systems that are part of the Lean structure to connect to the environmental conscience of staff to reduce the overall system impact to the environment.
E.E: What was the research behind the products/solutions?
N.T: I have written one book and co-authored another in these areas:
The Green Factory:
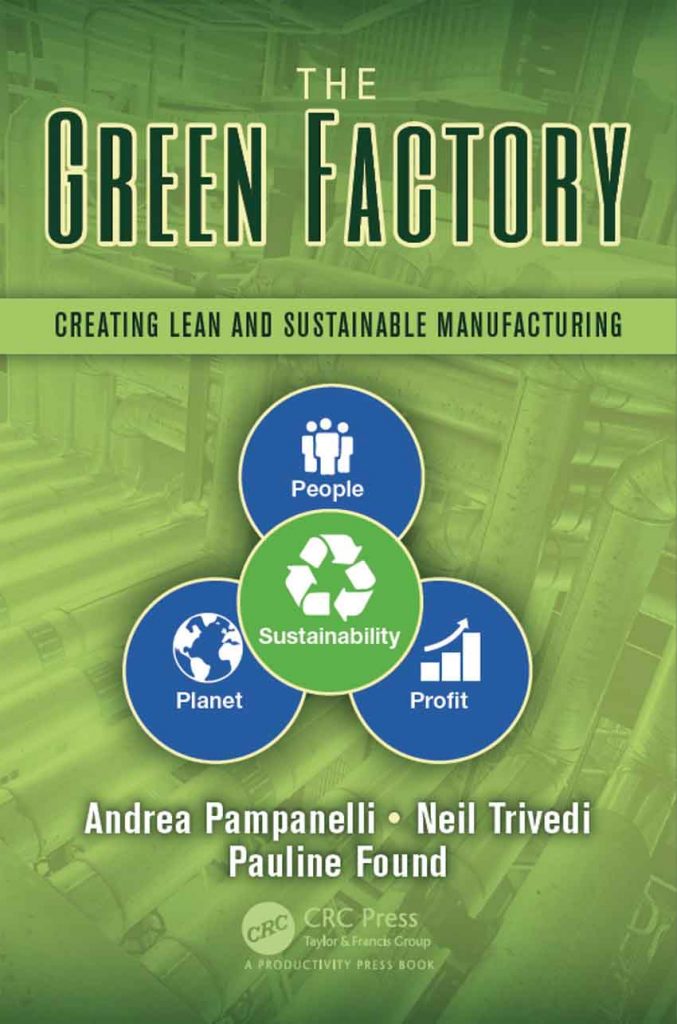
The Green Factory: Creating Lean and Sustainable Manufacturing
tells the story of how GKN, a major British multinational corporation with operations in more than 30 countries, developed and implemented a Lean and Green Business Model (L&GBM) in two of its automotive facilities in Brazil. It provides practical insight into how GKN was able to develop and deploy Lean and Green in a manner that resulted in environmental and cost benefits in the automotive facilities that operated in Brazil’s high-inflation environment.
Detailing proven concepts and sustainable models derived from the authors’ first-hand experiences, the book supplies information against the backdrop of two of GKN’s automotive manufacturing facilities. The authors take an inside-out approach, describing the real issues Environmental Health & Safety professionals face when implementing sustainable manufacturing policies. The book summarises the research of Andrea Pampanelli for her PhD – Lean and Green.
The Strategic Lean Office
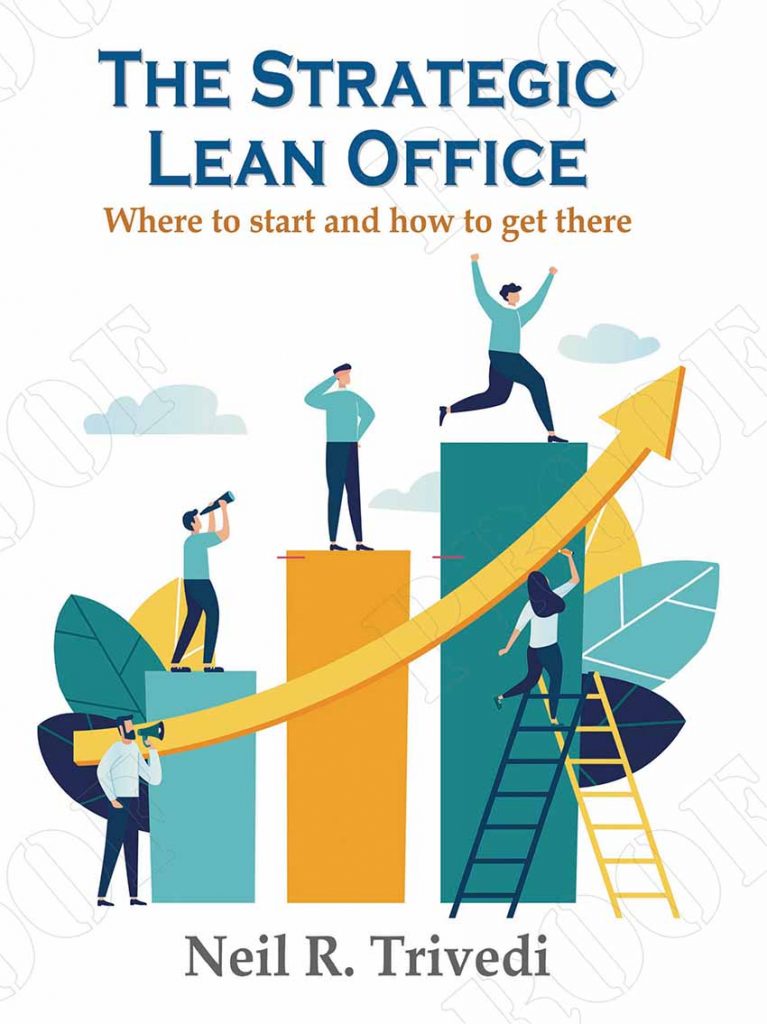
Application of Lean principles to the factory is an established improvement method. However, it is tempting to take the same approach that has been successful in the factory and apply it to the office without considering the nuances of this different setting. The book provides innovative solutions to tackle issues.
The book adapts Lean methodology into 8 steps tailored for business processes. These apply to all the classic office areas across a variety of business sectors and. The book will guide you through each step, with many practical examples and ideas for breakout sessions.
It is based on the many training events run by the author where real live business processes were reviewed and improved – over 600 in total. These improvement events helped the author develop the model and provide the experience to be able to tackle a wide range of business processes.
E.E: Tell us about their innovative features?
N.T: The book tackles head on the challenges of maintaining engagement and motivation for improvement and the lack alignment of strategy to business improvement. Its starts with asking the and defining customer value as it applies to office processes and builds by answering the WIFM question – “what’s in this for me?”. Understanding the answer to this question early on helps to recognizing personal benefit to gain engagement of staff.
As Lean has been effective in improving manufacturing operations, the natural next step is to apply the same techniques in the office that have been applied in the factory. However, understanding the differences between office and factory culture is essential to be successful. With the knowledge gained though hundreds of improvement events the book provides a realistic system to follow to get success in the office.
E.E: How important are these features for the users?
N.T: The book focuses on establishing and achieving customer value by optimizing flow and quality form office processes. This will not only impact the external customer but will help the internal process customers.
E.E: How do these features help the users?
N.T: Both the books have been developed using the experience and knowledge gained through many kaizen improvement events conducted with real-life business processes in operating environments. The practical nature of the research and experience mean that the models are immediately applicable to operating situations and not just a theoretical model.
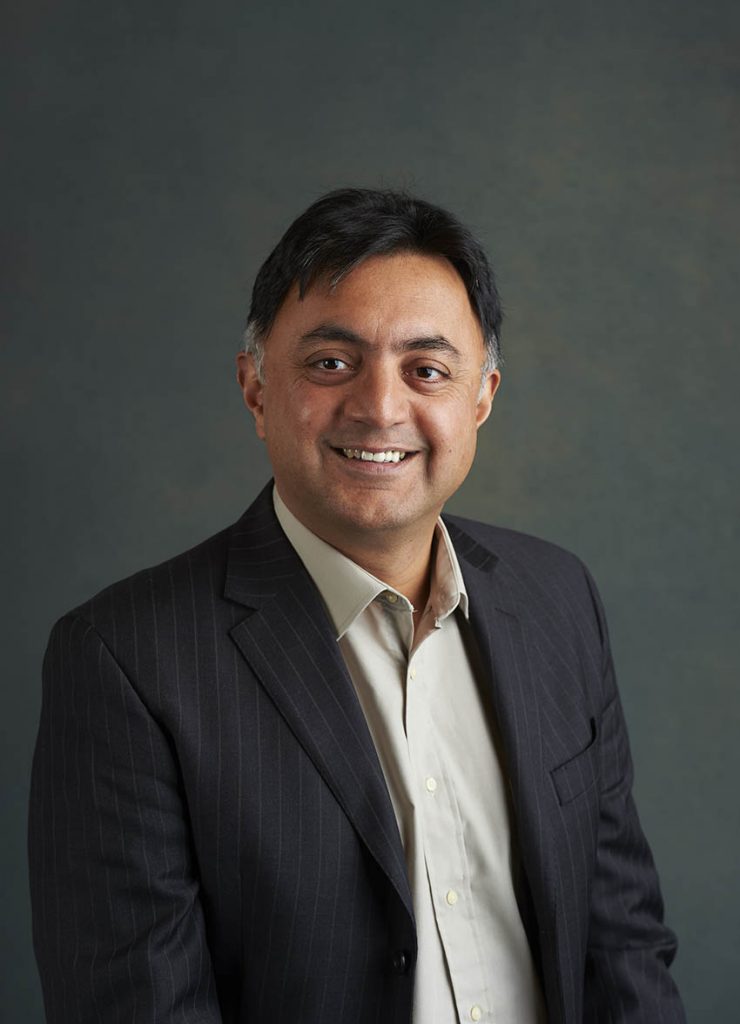
Neil Trivedi, Director of The Perfect Process Company
E.E: What industries do you think will grow in 2023?
N.T: Rather than the growth of business, the process by which is business is done will change. Remote working although previously well-established grew significantly during covid. So, making processes work virtually not only across business operations but through the homeworking environment will be the challenge for 2023.
E.E: What products/solutions do you provide for these industries?
N.T: To tackle this challenge, rather than jump to an automated workflow our approach is to review the process first busing Lean techniques to ensure that an effective efficient process is entered into any system. We have seen several clients who have copy-pasted what actually happens only to subsequently realize that they have systemized the waste and not addressed the root cause behavior issues.
E.E: How will you adapt your products/solutions for the future?
N.T: Going forward, we expect to see more interest in environmental manufacturing and in addition to providing practical “Green” methods we will be looking to expand our offering in that area.
E.E: What are your estimations for the rest of the year?
N.T: The rest of the year looks busy, with several clients looking for support with traditional Lean factory implementation and senior leadership coaching in addition to the work described on environmental manufacturing and office Lean.
E: neil.trivedi@theperfectprocess.co.uk
W: www.theperfectprocess.co.uk