The Sempre Group was established in 2000 to help British and Irish manufacturers improve productivity, reduce human error and demonstrate compliance in quality control. Its in-house specialists work with customers to resolve the toughest of metrology challenges across all sectors and its expert service team supports customers with contract measurement, system calibration and servicing.
Easy Engineering: What are the main areas of activity of the company?
The Sempre Group: We provide everything that manufacturers need to improve quality throughout a product’s lifecycle in a variety of manufacturing industries, from medical devices to aerospace. We work with customers to uncover the problems that they face in their business and tailor a solution to meets their needs.
We offer a broad range of industrial metrology systems and hand operated metrology apparatus and can connect it with electronic quality management systems or other software tools. Alongside this, The Sempre Group offers calibration and servicing packages. We’re on hand to help install and calibrate systems to ensure all measurements are valid — we’re one of the few UK companies able to offer UKAS accredited calibration for Optical/Vision CMMs.
Companies that work on one-off projects or who cannot afford to validate parts in-house can outsource to The Sempre Group’s contract measurement service. Our expert team will establish the best measurement solution for your parts and quickly measure any quantity of components, from a simple check on a handful of parts, to full production batch sizes and everything in between.
EE: What’s the news for 2021 about new products?
The Sempre Group: We regularly introduce new and innovative metrology systems, software and automated solutions, from a range of leading global suppliers to help provide UK and Irish manufacturers find the solution to any measurement challenge.
For example, we recently partnered with coordinate measuring machine (CMM) pioneer LK Metrology. It supplies a complete range of premium bridge, gantry and horizontal arm CMMs for highly accurate and repeatable measurement. It also offers multi-sensor CMM software to help automate inspection processes, improving component quality from design to quality assurance.
This partnership means we can provide the highest level of technical support and service to help customers meet their specific business objectives, be it reducing waste, improving yield or driving productivity.
EE: What are the ranges of products?
The Sempre Group: Developing partnerships with global manufacturers allows us to provide an extensive range of metrology products and software. We stock a range of high precision measurement systems, from handheld tools to CMMs that help improve accuracy, reduce scrap and improve the traceability of quality processes. Some of our equipment includes the Jenoptik Opticline shaft measurement system, Micro-Vu optical measurement systems and Prolink plug and play SPC data collection software.
We’ll also recommend software that can enable data driven quality management and allow businesses to make more informed decisions about their quality control. Automated QMS tools, such as High QA Inspection Manager, offer manufacturers an all-in-one solution for quality management, collecting and storing data at every point, from drawing to final product. They eradicate the need for time consuming paperwork and filing, which means manufacturers can easily communicate important quality information across the supply chain and can remove the headache of compliance reporting.

Some of the interesting new technologies we have available include:
GelSight mobile handheld elastomeric imaging sensor for digitally checking scratches and defects at the point of use, used instead of making replica moulds.
Sensofar 3D optical profiler with three in one optical technology for inspecting surface profile and 3D models with applications such as bullet and cartridge surface scans
InspecVision Planar 2D scanning system that can reverse engineer parts in seconds, used widely in metal fabrication industry
RPS articulated laser and tactile measuring arms up to 7m in length with up to 7 axes, the extreme range allows full measurement in one scan for large components such as car chassis
The MicroRidge MobileCollect universal measurement gauge data transmitters that transfers data wirelessly from any gauge to any SPC software
EE: At what stage is the market where you are currently active?
The Sempre Group: Our extensive knowledge in a range of industries, including automotive, medical and energy, allows us to provide solutions to any measurement challenge. We also work with businesses of various sizes, from start-ups to global manufacturers, and will tailor the solution to the needs of the business — be it measurement, automation, compliance reporting or lean manufacturing.

EE: What can you tell us about market trends?
The Sempre Group: Manufacturers traditionally use metrology as a policing tool at the later stages of the manufacturing process, when components are taken off the production line. By this stage it can be too late to rectify any issues — time and energy has already been wasted on a product that will only be scrapped. The manufacturer has also lost the opportunity to identify the root cause of any problems.
By incorporating metrology equipment to perform continuous inspection directly on the line, manufacturers can reduce scrap rates, minimise rework and remove delays. Quality also increases as parts are inspected at multiple stages, so it is easy to identify — and rectify — issues as they occur.
EE: What are the most innovative products marketed?
The Sempre Group: As a supplier we know how important it is to collaborate with partners and provide the entire package. Our in-house team will work closely with a customer to develop a solution to their problems. We often develop bespoke systems to ensure that the solution is tailored to the meet the needs of each unique business.
For example, The Sempre Group is adding automation to its portfolio to help manufacturers adopt a fully digitised approach to quality. Using the latest in collaborative robotics, we can supply easy-to-use, flexible automation solutions to automate parts of the production line. A cobot can pick up parts from the production line and move them to measuring equipment, repeating the process 24 hours a day, seven days a week — freeing up the team member that normally carries out this process to work on another project.
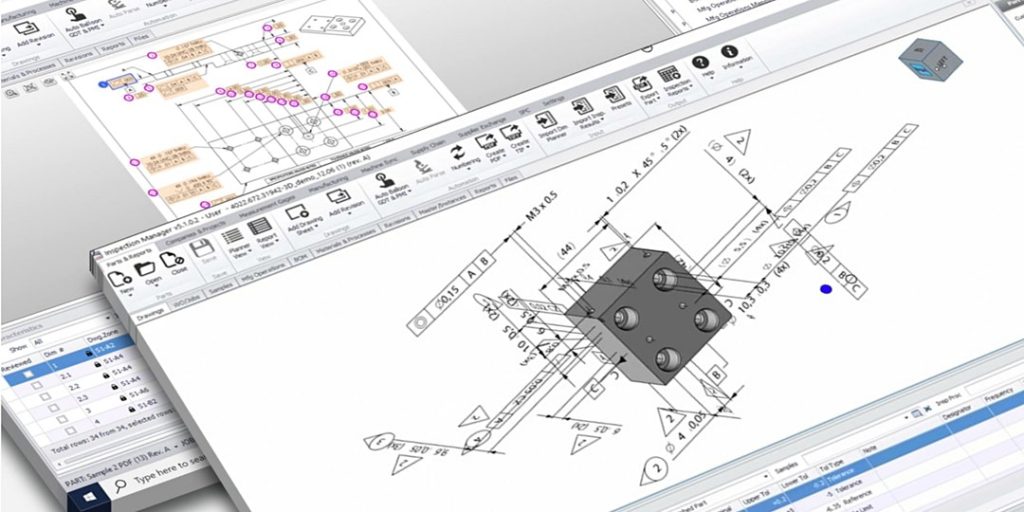
EE: What estimations do you have for 2021?
The Sempre Group: Manufacturers are thinking about how they can bounce back in the year to come. Embracing Industry 4.0 technologies is one of the ways manufacturers can drive growth, but they can also consider how they can inspire their workforce and better manage data to improve operations.
At a time when manufacturers want to cut costs, it is important to establish what outcomes they want from digitalisation before committing to an investment. By focussing on the outcome and not the equipment, manufacturers can make decisions that deliver clear return on investment.
For example, digitizing quality management is central to realizing Industry 4.0 and driving real value in the future. Investing in digital technologies can give manufacturers full control over their measurement data, so they can use it to make better decisions, improve traceability and improve productivity. A fully digitized approach to quality removes the challenge of integrating data from fragmented sources, reduces room for error and enables manufacturers to improve their productivity.