UBQ is a scientific breakthrough that converts unsorted household waste, including all organics (food residues, dirty cardboard, and paper) together with mixed plastics, into a patented, climate positive material. UBQ™ substitutes conventional plastics in production of everyday items across many different industries – from logistics, furniture, and retail to automotive and even construction.
Not dependent on oil or other fossil fuels for feedstock, UBQ™ is able to offer a competitive and uniquely stable price point that is unaffected by market volatility. Not only is the material independent of oil, its feedstock is derived of 100% landfill-destined waste leading to a negative cost of raw material to manufacture UBQ™.
UBQ™ is a novel thermoplastic material that compounds with most polymers, and seamlessly drops-in to today’s standard manufacturing processes. At a competitive material cost and no additional adaptation fees, UBQ™ enables manufacturers to divert waste and offset their carbon footprint without compromising profitability. To date, UBQ™ is compatible to injection molding, compression molding, extrusion and 3D printing.
UBQ has positioned itself as the new standard in eco-conscious manufacturing; one that goes beyond climate neutral goals and strives for climate positivity. Their impact on the earth as individuals, as manufacturers and as an industry should be to leave it better than we received it.
Interview with Liat Arad, VP of Marketing at UBQ Materials.
Easy Engineering: What are the main areas of activity of the company?
Liat Arad: UBQ offers the industry a new sustainable raw material available in powder, tablet and custom masterbatch compounds. Deemed the most climate positive thermoplastic on the market by Quantis, leading LCA auditors, substituting even small quantities of conventional plastics with UBQ™ is often able to offset or even reverse the carbon footprint of final products.
Since 2019, UBQ’s partnerships have included production of recycling bins for Central Virginia – an almost-poetic demonstration of circularity, where recycling bins are themselves made of trash; Development of premium auto parts with Motherson and Mercedes Benz, introducing UBQ™ material into the highly-regulated automotive industry and winning the ATZ MTZ Sustainability Award in Automotive 2021; Launching serving trays with McDonald’s across Latin America, leveraging UBQ’s near-food contact certification; partnering with Mainetti, the retail solution distributor in the world to develop a climate-forward garment hanger; and most recently we’ve announced a partnership with Keter, the largest resin-based consumer goods manufacturer in the world (they make and distribute outdoor furniture, garden products and sheds).

E.E: What’s the news for 2021 about new products?
L.A: The R&D department is always working to strengthen and expand the UBQTM material. With several new patents in progress, we anticipate the imminent launch of the next generation of the UBQTM material that would open access to new applications, greater variety of polymer compounds, and compatibility with niche production processes. In parallel, UBQ is exploring different waste streams and compositions that don’t currently have sustainable end of life solutions.
E.E: What are the ranges of products?
L.A: UBQ(tm) is a homogenous and consistent material offered in pellets, powder, and masterbatch compounds that are customized for the client’s needs. This singular material can substitute plastics, woods and minerals across industries and product applications. After years of rigorous testing, UBQ™ has been proven fit for use in the production of durable plastic products, spanning everything from shopping carts, shipping pallets, hangers, automotive parts, furniture and even bricks.
From injection to compression molding through to extrusion, the UBQ™ material has been tested and proven to be compatible with PP, PE, PLA, and PVC. Like with any other polymer, virgin or recycled, UBQ™ can be compounded with additives commonly used in the industry to address product specifications such as coloration, impact strength or UV resistance.
E.E: At what stage is the market where you are currently active?
L.A: UBQ™ is already being implemented in the production of a range of interior and exterior automobile parts. Following many trials and examinations, UBQ and its partners in the automotive industry have every intention to implement this in serial production currently in final stages of regulatory approval. Products like clothing hangers (in collaboration with Mainetti) and food trays (in collaboration with Arcos Dorados) are already in commercial use. The hangers will be distributed across major retail stores in 2022 and the trays are being used in more than 30 McDonald’s restaurants across Brazil.
To meet growing demand, UBQ is embarking on a fast scaled global expansion, with the first industrial facility set to begin operations in the Netherlands in 2022.
E.E: What can you tell us about market trends?
L.A: Multi-layered Environmental Propositions
The future of the plastics industry like that of every industry is characterized by a responsibility to our future generations, upholding ourselves to standards that respect the finite nature of our natural resources. Industry leaders are driving bold sustainability goals – net zero emissions, zero waste, circularity – and are looking for technologies, systems and advanced materials that are able to efficiently support these goals.
Waste Diversion
Every ton of UBQ™ is made from 1.4 tons of 100% unsorted municipal solid waste that would have otherwise been buried in landfills. By giving new life to this waste, UBQ is able to empty landfills while conserving finite natural resources (oil, wood, concrete, minerals) for future generations, promoting the transition into a truly circular economy.
Emissions
By diverting landfill-destined waste, UBQ™ prevents the emission of methane, groundwater leakage and other environmental harms. Every ton of UBQ™ prevents 11.7 tons of CO2eq from polluting the environment (GWP20); Life Cycle Assessment auditors Quantis have designated UBQ™ as “The Most Climate Positive Thermoplastic Material on the Market”.
Protecting Natural Resources
By diverting waste from landfills and converting it into UBQ, we are saving precious natural resources, landfill methane emission and replacing oil-based plastics. Emptying landfills, one product at a time.
Large Scale ESG Investment
A trend currently in place, anticipated to only grow further is the widespread interest in ESG investments from financial institutions, venture capital and enterprises. All eyes are on ESG matters; public perception, government taxes and incentives, industry regulations. All driving further interest in fast adoption and implementation of disruptive sustainable technologies and materials.
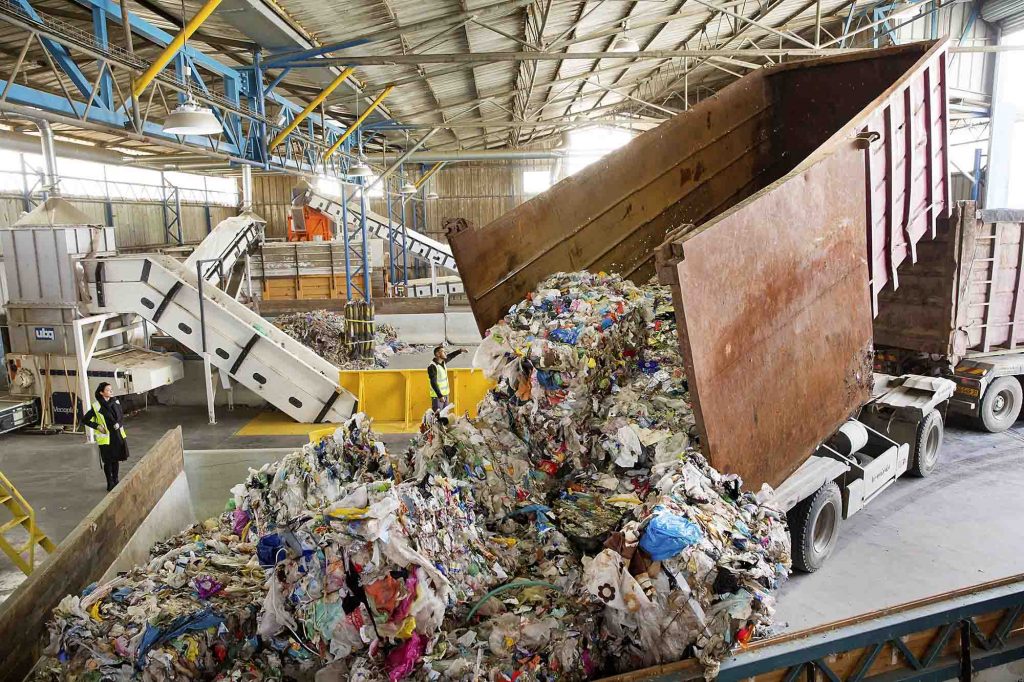
E.E: What are the most innovative products marketed?
L.A: Together with Plastics App, we recently launched a line of novel 3D printing filament that are both functional and carry significantly reduced carbon footprints.
Widely recognized as environmentally responsible, 3D printing is a versatile manufacturing technique that enables less energy and raw material usage than traditional production methods. Significant R&D has been invested across the industry with the aim of reducing the carbon footprint of the materials used in 3D printing. To date, the most sustainable 3D filaments have been largely based on a Glycol-modified version of Polyethylene Terephathalate (PETG), which has limited properties and has confined use cases to dimensional models and dummies.
UBQ Materials converts unsorted landfill-destined waste into a sustainable, climate-positive and cost-competitive thermoplastic (UBQ™) that substitutes oil-based resins for manufacturing. Plastics App has developed UBQ™ inside filaments, which, when applied to 3D printing, expand sustainable application to functional uses such as jigs, fixtures and spare parts. UBQ™ will be incorporated into four types of carbon reduced sustainable filaments. Perform Q is a high-performance, UBQ / Polypropylene filament suitable for standard applications; Perform QCF, which has Carbon Fibers, is a reinforced UBQ / Polypropylene-based filament suitable for demanding applications. Both grades are available either on virgin PP or PCR PP carriers.
E.E: What estimations do you have for 2021?
L.A: Due to increased demand and the desire to further localize the waste to production cycle, we are quickly scaling up with global expansion. Today we focus our efforts in expanding our company in Europe, currently building the first industrial scale UBQ plant in the Netherlands with an annual capacity of 73,000 tons. The rapid global expansion plans hope to have UBQ technology and plants located throughout Europe, United States, Canada, Australia, Japan, among others in the next 10 years. The greater the industry’s demand for UBQ, the faster we are able to power UBQ facilities around the world, lowering the carbon footprint of transportation and diverting more local landfill waste into UBQ™ for local manufacturing. The objective is to use local waste to supply local markets. The greater the demand for sustainable materials, the faster we scale up and operate additional UBQ facilities, the more landfills we can empty and the more oil-based plastic we can replace around the world.
UBQ MATERIALS