UTILITY COMPOSITES, Inc. is the manufacturer of RAPTOR® plastic composite nails and staples, SUNDOG® UHF RFID tags, a state-of-the-art tag designed to solve problems for tracking assets with rough wood surfaces, and BLACK MAGIC® staples, completely non-metal staples used in retread tire manufacturing.
The company offers cost saving solutions with their world class products providing them to a broad spectrum of markets including timber processing (forestry), wood products manufacturing, composites manufacturing, and automotive markets.
The composite fasteners are marketed and sold worldwide implementing a dual strategy of both direct sales and industrial distributors strategically positioned around the world.
Interview with Jeff Venditte, Business Development Director at UTILITY COMPOSITES, Inc.
Easy Engineering: What are the main areas of activity of the company?
Jeff Venditte: Our company is built on developing solutions that address customer needs. We provide solutions for timber processing, woodworking (furniture, cabinetry, CNC shops, etc.), tire retreading, boat building, and wind blade manufacturing, in addition to other industries. The wide range of markets that we address is a good example of how we listen to our customer’s needs and help them be more efficient.

E.E: What’s the news about new products?
J.V: We are constantly looking at new materials to produce products requested by our customers. We recently released a line of XF finished nails and pins that work with harder woods. We are prototyping a nail for a government contractor and automotive customer that offers more flexibility for manual use. We recently introduced SUNDOG®, a state-of-the-art RFID tag for tracking rough wood assets.
E.E: What are the ranges of products?
J.V: All our products are based on our patented polymer composite technology.
RAPTOR® products range in multiple sizes that include finished nails, brads, pins, staples, spikes, clamp nails, copulas and snap studs.
SUNDOG® products are staples with embedded passive RFID microchips. We have two lines that address US standard frequencies and EU standard frequencies. These are the two standard frequency ranges used around the world.
BLACK MAGIC® products are available in multiple staple sizes.
In addition, we provide custom designed tools for each fastener type that include pneumatic nailers and staplers, compression staplers and hammer tackers.
E.E: At what stage is the market where you are currently active?
J.V: The markets for RAPTOR® and BLACK MAGIC® are mature markets that continuously reinvent themselves with new manufacturing techniques that increase production, improve distribution of product, and reduce costs. In many ways we are considered a “well-kept secret”, and when customers are first introduced to our solutions, they are quite surprised that we have been in business for over 30 years. SUNDOG® represents a new market for us in the Forestry 4.0 initiative utilizing technology to improve wood assets management.
E.E: What can you tell us about market trends?
J.V: We see our markets continue to grow year over year. There is more focus on automation and adopting new technologies like the use RFID for wood asset management. We continue to produce solutions that can evolve with the latest market demands.
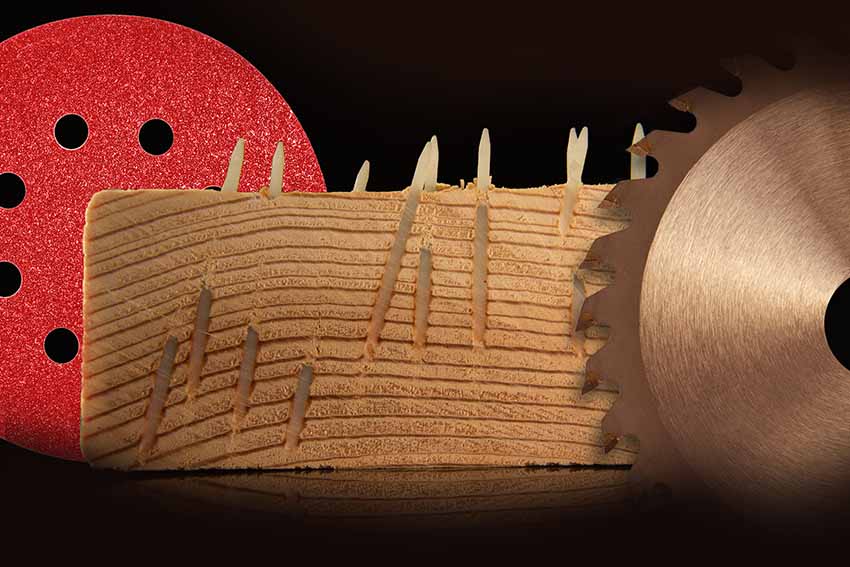
E.E: What are the most innovative products marketed?
J.V: All products are patented and provide the highest quality solutions for our customers.
RAPTOR® innovations include products are strong enough to drive through wood, yet soft enough to be sawable and sandable. They are also stainable, and they will never rust. Customers eliminate damaged blades, bits, and sanding belts caused by hitting metal fasteners. Raptor® streamlines wood processes and saves time and money.
SUNDOG® RFID tags enable long read ranges (over 11 meters), can withstand harsh environments, and provides for easy and extremely quick installation to your rough wood surface. It is one of a kind in the industry.
BLACK MAGIC® staples hold the pre-cure tread splice together and melt into the tire during the curing process, eliminating the need to remove metal staples. With Black Magic® staples there is no staple removal, staple clean up, or damaged tire envelopes.
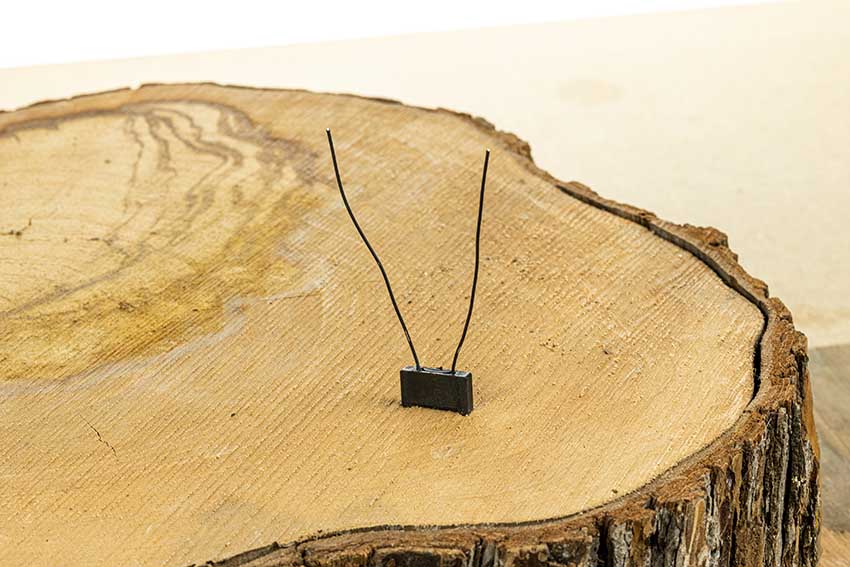
E.E: What estimations do you have for the rest of 2022?
J.V: Closing out 2022 was a great year for us. We see 2023 as another year of growth for our organization.
http://www.utilitycomposites.com