VBN Components is a Swedish materials development company, 3D printing extremely wear-and heat-resistant metal components and tools for industrial usage. The products are made according to customer drawings and are produced through a patented 3D printing process (the finished alloys are also patented). The material used for printing is metal powder produced through large-scale gas-atomisation. The concept is that VBN’s patented metals are used to improve customer applications through better properties and, in some cases, new geometry. Customers can benefit from material savings to up to 87% in certain applications, as well as improved features like integrated cooling channels, increased lifetime and reduced weight. The finished metal alloys, branded Vibenite®, have exceptional wear and heat resistance.
Today’s portfolio includes five steels and one cemented carbide (including a steel that will be released in the summer of 2020). They are the most wear resistant alloys on the market, 3D printed or not, with a hardness between 48-72 HRC, and an unexpected toughness due to very small, well-dispersed carbides. With Vibenite® new frames for performance of metal alloys have been created. Through the years it has been proved that components made with Vibenite® have considerably longer lifetime than those manufactured with traditional metals. VBN is the only company offering 3D printed steel with high carbide content, and it also 3D prints industrial components in cemented carbide, which is unique worldwide. On top of it all, environmental impact of the production process is reduced with around 90%, compared to traditional component manufacturing methods.
Easy Engineering: What are the main areas of activity of the company?
VBN: VBN Components 3D prints industrial tools and components in patented Vibenite® steel and cemented carbide, according to customer drawings. These tools and components get extreme wear- and heat-resistance and a hardness that reaches up to 72 HRC, and they can also be improved design-wise, thanks to 3D printing, with for instance new functions and less weight. VBN is also constantly conducting research to develop new materials and printing methods.
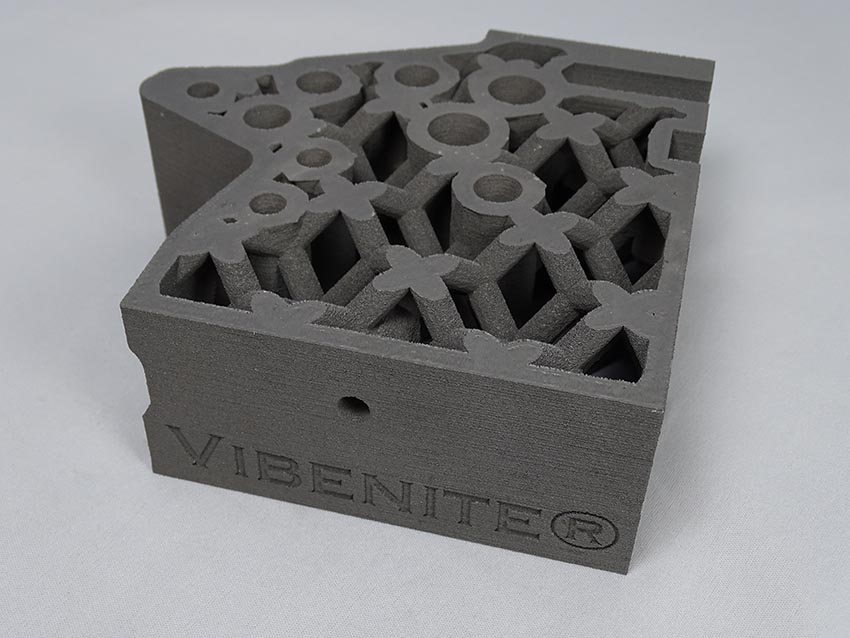
E.E: What’s the news for 2020 about new products?
VBN: In the summer of 2020 a new, extremely tough steel, Vibenite® 130, will be released.
E.E: What are the ranges of traded products?
VBN: Today’s portfolio includes five steels and one cemented carbide, all developed and patented by VBN Components. These alloys are 3D printed according to customer drawings, so the customer chooses the alloy most suitable for a certain application and gets a 3D printed component made with this alloy. The range of possible industrial tools and components is very vast and adaptable to what the customer needs. Applications that require extreme wear- and heat resistance are particularly beneficial. It is also possible for a customer to purchase a license solution, in the case where it is interesting to produce large volumes in-house.
E.E: At what stage is the market where you are currently active?
VBN: It is an evolving market with a relatively new technology. Even though the performance of VBN’s materials has been proved in several applications, customers are still testing new applications and learning about the benefits.
E.E: What can you tell us about market trends?
VBN: Metal additive manufacturing is a strongly growing market. Industrial companies are discovering the benefits you get from creating new functions through changed geometries, and how you can reduce the time for product development from months or years to weeks when you 3D print instead of using traditional techniques.
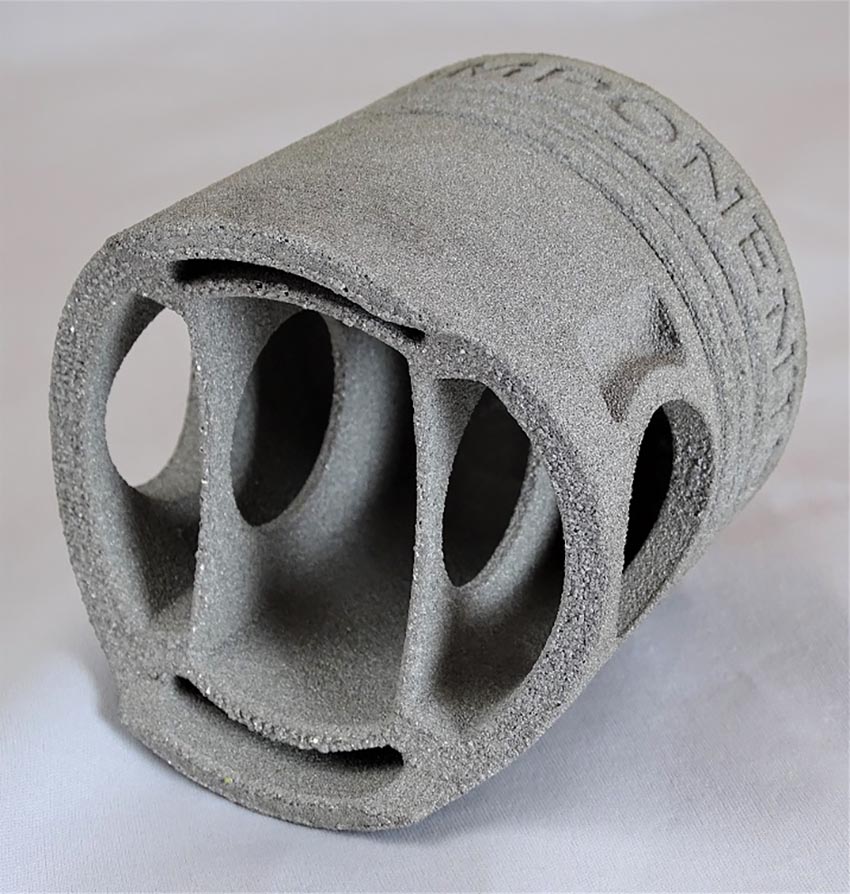
E.E: What are the most innovative products marketed?
VBN: All of VBN Components’ materials and production processes are patented, so they represent a high degree of innovation. VBN Components has made it its niche to 3D print with high carbide content, which has long been considered “impossible” by most people. VBN is one of very few companies that does not try to copy existing, traditional metals, but that actually develops new and better ones. However, two materials stand out a bit more than the rest:
In November 2017 “The world’s hardest steel”, Vibenite 290, was launched. It reached global awareness with its unique properties. It contains 25% of carbides and comes in the hardness range of 68-72 HRC, which means it could never be processed traditionally. 3D-printing is a necessity to shape components of this unbeaten steel hardness. New levels of materials performance are reached, and previously “impossible” components are shaped. Naturally, it is perfect for cutting in other metals and for usage in other high wear applications.
In December of 2018, VBN Components announced that it had developed the capability to 3D print cemented carbide. This type of material has previously been considered “impossible” to print, due to high carbide content. VBN had already proven that high carbide content is possible with Vibenite 290, but the cemented carbide Vibenite 480 really beats all the odds, since it contains ~65 vol% of carbides. There is no mixing, drying, pressing or sintering needed, as in the traditional cemented carbide process. This new type of cemented carbide has a long-term heat resistance of 750°C, a hardness of ~66 HRC, is corrosion resistant and magnetic. Vibenite 480 is niched both towards applications where steel is normally used, but where replacing it with cemented carbide would increase production efficiency, and also towards cemented carbide applications with complex geometry. Since it combines the best of two material worlds – PM-HSS and cemented carbide, it is referred to as “hybrid carbide”.
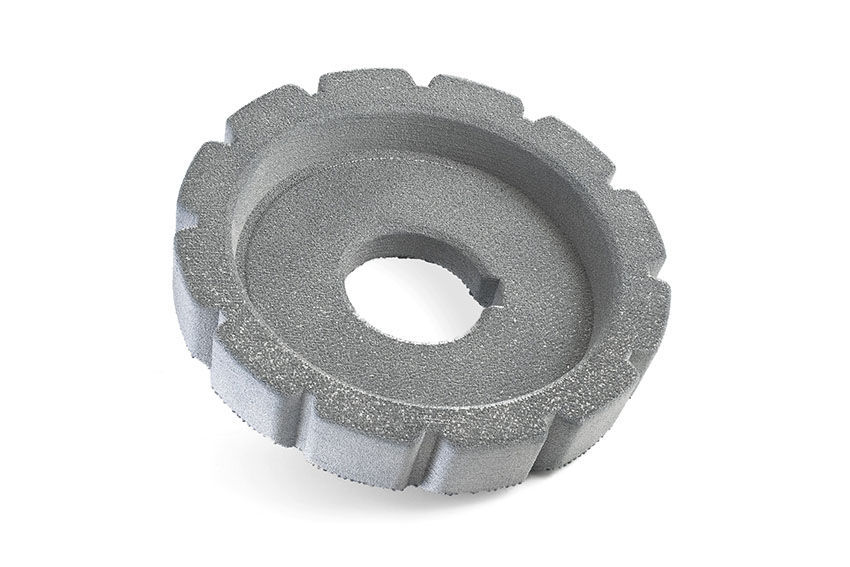
In some applications, customers are looking for different properties in the same component. After several requests to print one material on top of another, VBN Components has developed the production method Vibenite Combo. As the name indicates, the method combines different materials in the same component. In this way different levels of hardness and toughness can be chosen within the Vibenite portfolio, in the same application. What is more, it is also possible to print Vibenite on top of a conventional, non-3D printed component. This is beneficial in the case where you only need Vibenite properties in a certain part. To illustrate an example, VBN Components has printed a drill bit combining its toughest material, Vibenite 150, with its hardest, Vibenite 290, the world’s hardest steel. Vibenite 290 has been used for the cutting part of the tool, printed upon a cylinder of Vibenite 150, which constitutes the lower part of the drill bit.
E.E: What estimations do you have for 2020?
VBN: Fortunately, the corona crisis has not hit us very hard. We have research projects with industrial partners that are still running, and sales are going well. We believe 2020 will be a good year for us.