Volframi makes nanotechnology utilization possible in traditional industries. The company develops a method and tools usable in the coating processes of surfaces. With their tool, you can make targeted coatings on a surface of any size without coating the entire surface.
Interview with Jukka Vuoristo, Chief Technology Officer, Inventor of patented Partial Sputtering method at Volframi Oy.
Easy Engineering: How was 2022 for your business, a short summary?
Jukka Vuoristo: The year 2022 was very busy for Volframi. We launched several product development projects to create completely new coating methods for our customers. All the methods were entirely different from the methods customers used before. We made a lot of new contacts, particularly at trade fairs, which had not been organized for several years. Long delivery times for components caused challenges, including a cancellation of one project.
E.E: What products did you launch this year?
J.V: We developed new methods for coating conductive electrodes, for example. They are significantly faster than the current method. At the fair, we presented our first end-product Intelligent Glass Control (IGS). IGC is a method for glass processors where the control surface can be made directly on the glass surface. The product is manufactured using the “rethought process ” glass coating method we have developed.
E.E: How did the market change, compared to previous years?
J.V: At trade fairs and events, you could see how much people and businesses had missed these encounters. It was really nice to meet people face to face, after several years.
The market is already showing clear signs of what the EU’s new climate targets will require from companies. The old ways of doing things are no longer enough and companies need to develop their operations in a more responsible direction, even though this may involve major production challenges. This is a good opportunity to consider whether the current, familiar way of doing things is the best way. We can learn from others and gain a competitive advantage over the old way of doing business.
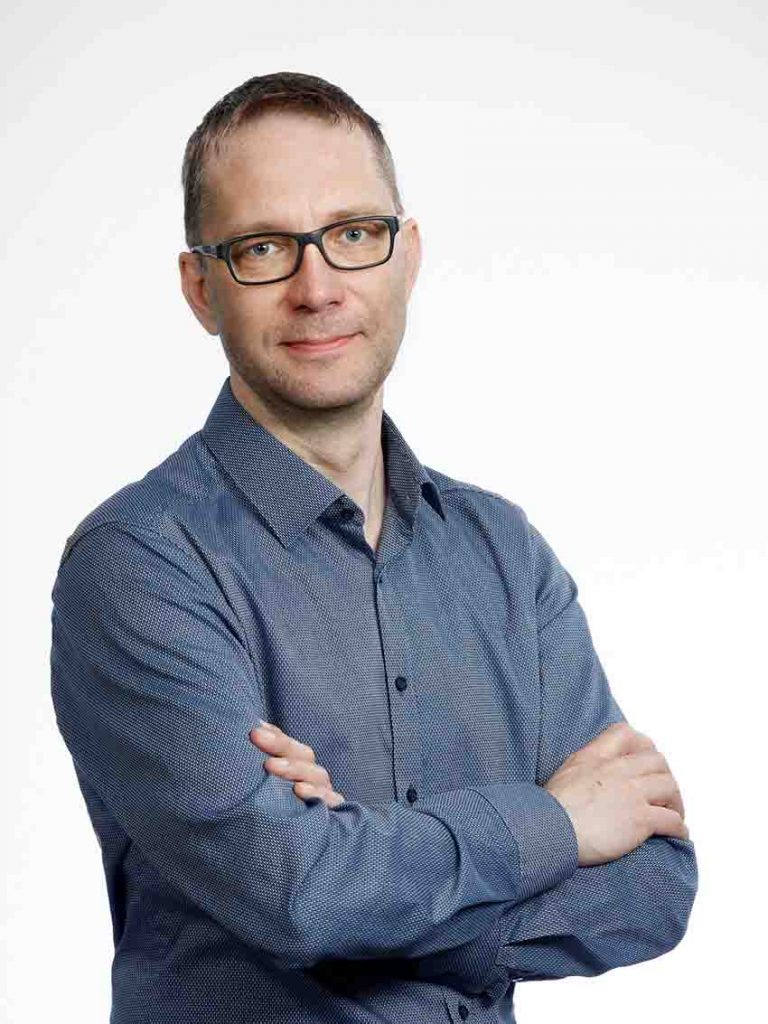
Jukka Vuoristo, Chief Technology Officer, Inventor of patented Partial Sputtering method at Volframi Oy.
E.E: What are the new challenges in your field of activity?
J.V: Pandemic and especially the war in Ukraine have brought unprecedented problems in production and supply chains. The availability of components was already severely reduced by the impact of the pandemic, but the situation became even worse after the war started in Ukraine. Now, when starting new projects, it is almost impossible to say what the actual delivery time will be. This affects both larger and smaller operators. Smaller players have the advantage of more flexible working methods and the ability to react faster.
E.E: How did you overcome these challenges in this more competitive environment?
J.V: Contrary to our previous plan, we have started to produce the basic components ourselves, while retaining the possibility to use ready-made units when they are more readily available again. We have also explored the use of refurbished products and the recyclability of components as part of our production.
E.E: Tell us about product innovation and how will it impact the future?
J.V: The partial processing we have developed allows the manufacture of completely new types of products. It provides glass processors with new production methods that enable both environmentally friendly and cost-saving activities. This also gives them the opportunity to deliver new added value and profitability to their customers.
Volframi Oy Ltd Targeted Glass Coating Method
E.E: How will product innovation help the customers?
J.V: The previous method required the use of large and expensive machines to produce the coatings, or the use of very valuable fully coated glass. Now, even the more valuable coatings can be made using our method on only the necessary part of the glass. This minimizes the waste of source materials and reduces the environmental impact. It is worth noting that some of the coated glasses cannot be recycled or it is much more difficult and expensive to recycle than uncoated float glass. The smaller size of the equipment is also reflected in the cost of purchase, operation and maintenance.
E.E: What are the industry trends in the markets you are currently active?
J.V: Sustainability and new products are the cornerstones of our equipment development. As a newcomer, we have to stay at the forefront of development and offer completely new solutions that give our customers new ways to boost their production in a constantly changing and highly competitive market.
E.E: What do you think the trends will be next year?
J.V: Growing product demand in the automotive and construction sectors, rapid industrialization and urbanization and, increasing technological advancements are expected to boost market growth. In Europe, the climate-neutral EU objectives by 2050 are requiring increasing attention; demand is driving the production of highly energy-efficient windows, for example. Given the long timescale for sustainable development, we all still have a lot of work to do. I also believe that the glass sector must increasingly change its attitude and approach and accept future changes. I hope that the global situation will ease and normalize.
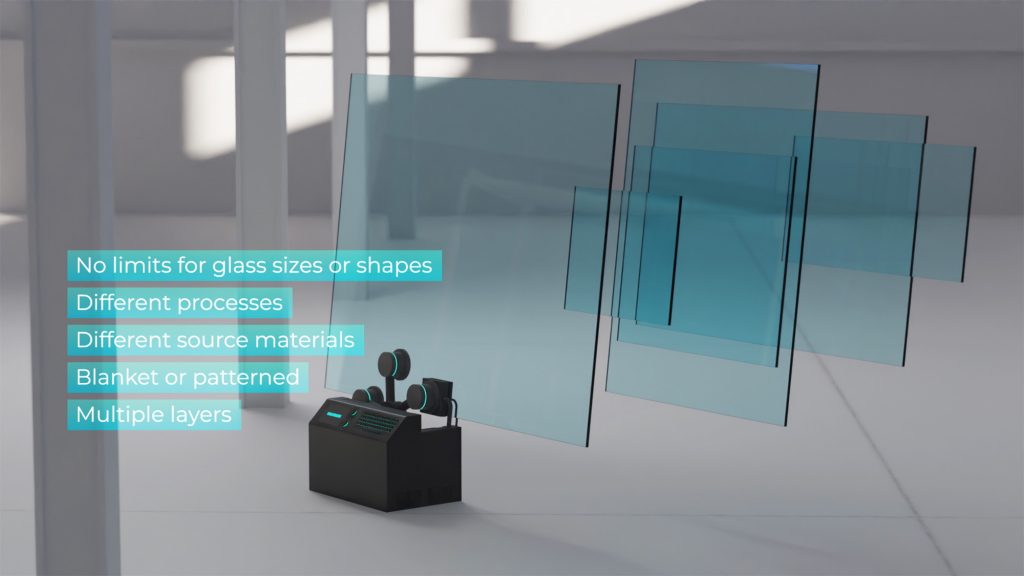
E.E: What is the outlook for 2023?
J.V: In 2023, we look forward to successful projects with our existing customers, good partnerships with new customers and more challenging development projects. The growing focus on the aesthetic and functional features of glass, the increasing demand for value-added products such as automotive glazing and new innovations in architecture, and the expanding solar energy market offer us new growth opportunities. We also hope to meet our partners, old and new, more face-to-face because interaction is after all the most effective way of driving development forward.