Warner Electric is the largest manufacturer of electromagnetic brakes and clutches in the world. The company is present on every major continent, operating multiple manufacturing facilities in Europe, the U.S.A and China. Founded in 1927 by inventor Arthur Warner on the strength of a pioneering electrical brake design, Warner Electric is now a leading brand of Altra Industrial Motion Corp. The business provides power transmission solutions globally for multiple sectors, supporting applications as varied as off-highway vehicles to robots.
Interview with Mathieu Ruault, VP of Sales and Marketing for the Warner Electric division of Altra Industrial Motion.
Easy Engineering: What are the main areas of activity of the company?
Mathieu Ruault: Our key markets and applications include turf & garden, forklifts, agricultural, material handling, off-highway and construction vehicles, autonomous guided vehicles (AGV), elevators, cranes, robotics and servo motors.
For any rotary machine movement, clutches are often needed when the application requires engaging and disengaging of the drive. Additionally, certain applications may require a brake when the drive needs to be stopped and held into position. Our extensive global experience, combined with leading engineering and manufacturing operations, differentiates us from the competition when providing electromagnetic brake and clutch solutions for a wide variety of modern power transmission requirements.
Naturally, electrification is top-of-mind for our business. Following the market trend towards electric or hybrid powertrains is one of our key areas of focus. As original equipment manufacturers (OEMs) move away from traditional combustion powertrains, hydraulics and pneumatics, we can offer a ready-made range of proven electrically powered products that can meet a wide range of application requirements.
These applications can include braking systems for electric motors, as well as clutches for hybrid vehicles where engagement and disengagement between electric and combustion powertrains is required. Ultimately, we provide solutions designed to keep pace with modern powertrain technology.

E.E: What’s the news for 2021 about new products?
M.R: In order to meet the ever-changing requirements of our OEM customers, we are continually innovating and expanding our range of solutions.
As a result of two years of development, we have recently launched our spring-applied electrically released ERX Series brakes. A pre-assembled electromagnetic brake suitable for parking and stopping applications, the ERX combines a compact size with a torque range from 5 to 400 Nm. Designed to meet the needs of varied industrial applications, the ERX can be specified as a single or double brake, as well as in standard, high-torque or high-speed configurations. With a choice of three friction materials, the ERX Series combines performance with versatility.
Our range of electrically operated bell housing clutches are another new introduction. These clutches operate without hydraulics or pneumatics, requiring only two wires. This improves packaging while simplifying installation and retrofitting. Available as a standalone unit or a complete assembly, our ability to customise these clutches ensures OEMs can upgrade power take-off (PTO) drive assemblies in a very straightforward manner, thanks to features such as modified hubs and varied sizes. As a result, bell housing clutches are ideal for marine, agriculture, construction, mining, rail as well as oil and gas applications. This solution enables OEMs to move away from traditional mechanical PTO clutches, modernising the powertrain.
Our Warner Electric Sensor (WES) was developed to combat the reduced accuracy of mechanical and proximity microswitches used in brake wear monitoring. In precision applications, mechanical microswitches suffer from contact pollution issues, while proximity microswitches are affected by temperature variations, which increase hysteresis. Both limitations compromise accuracy of brake wear monitoring. Specifically designed for electromagnetic brakes, the WES has no mechanical contact to ensure accuracy, while it reduces hysteresis to 0.05 mm between operating temperatures of -40°C to 105°C. This means highly accurate performance throughout its service life across a wide range of environmental conditions, ensuring superior brake wear monitoring.
E.E: What are the ranges of products?
M.R: We offer electromagnetic brakes and clutches for both precision and heavy-duty applications. For example, we have developed brakes that are 10 mm in diameter and clutches that have a torque rating of 10,000 nm or more. Our engineering capabilities and technical expertise mean we can offer a comprehensive range. Working with a multitude of OEMs across many major markets ensures we have the experience to provide tailor-made solutions to meet the needs of almost any application.
As a business, we are always looking to add smart features into our products. This means that we can support technically demanding applications by embedding electronics into our brake and clutch solutions. Additionally, this ensures a level of futureproofing for developments such as the Industrial Internet of Things (IIoT).
E.E: At what stage is the market where you are currently active?
M.R: We operate in a multitude of markets globally, but we have seen some common trends this year. Markets such as turf & garden, robotics, servo motors and agriculture are rebounding from last year with strong growth. In some cases, we are even seeing an increase in activity compared to 2019.
E.E: What can you tell us about market trends?
M.R: For Warner Electric, the key market trend is electrification. OEMs are moving away from traditional combustion powertrains to full electric or hybrid designs. Therefore, we are developing our product ranges to meet these requirements. Our bell housing clutches are a good example of this – a modern and efficient solution that can be easily integrated within existing applications.
In the turf & garden market, we are seeing equipment such as lawnmowers become increasingly electrified. For forklifts, even larger designs are now moving to electric powertrains. Smaller moving construction equipment such as excavators, loaders and shovels are going electric. In agriculture, larger equipment is undergoing a move to hybridization in new designs. Increasingly, driverless tractors and robots are taking a more involved role in farming. Usage of AGVs is growing in general, with most relying on electric powertrains.
We have a wide range of products designed for electrified and automated vehicles, with IP67 ingress protection variants available to ensure maximum reliability and service life in demanding agricultural and construction applications.
E.E: What are the most innovative products marketed?
M.R: Our SSPB pulse brake is a particularly innovative addition to our range. Its design offers greatly reduced power usage compared to traditional electromagnetic brakes. Typically, constant current is required to keep these brakes open, which increases power consumption. However, the SSPB utilizes pulses of current to open and close. This minimizes power demand when the brake is released, ideal for electrified vehicles where conserving battery life is all important.
Another innovation is our W134 brake friction material. For brake manufacturers, it can be difficult to source a friction material that provides consistent performance across a range of duty requirements. Typically, friction materials are specialised for specific applications, environments and temperatures. This means it’s difficult to specify a material that can deliver consistent static and dynamic braking across all conditions. To overcome this, we developed W134 in-house over five years to deliver a friction material that provides reliable braking performance regardless of temperature or humidity. High torque stability across a wide range of rotation speeds is an innate characteristic of the material. With minimal wear, W134 delivers consistent braking performance and a long service life in heavy-duty braking applications.
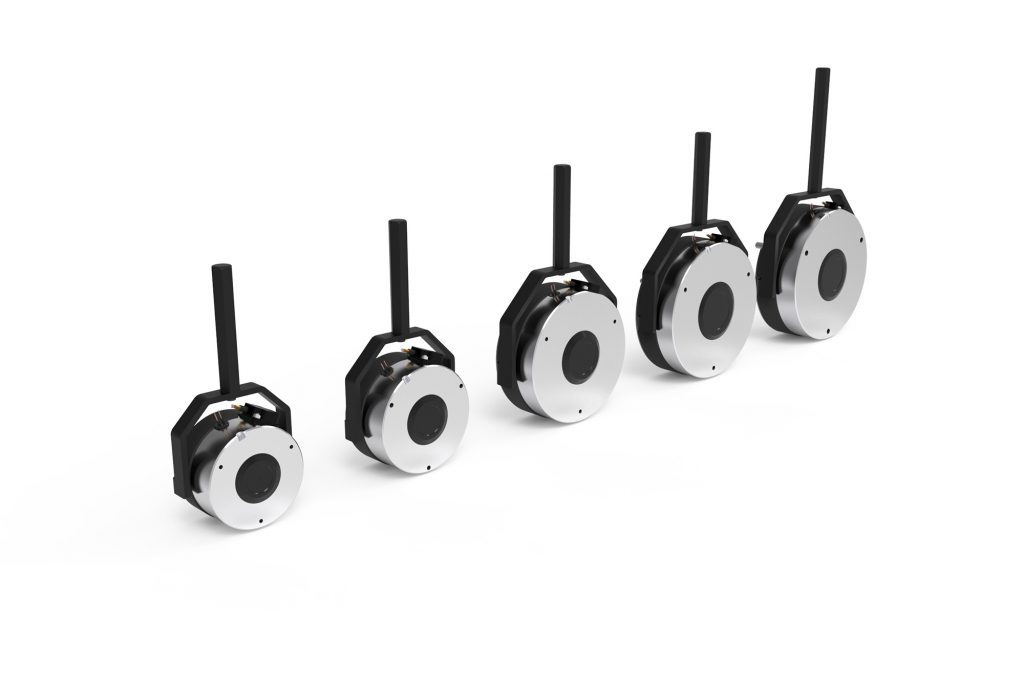
Furthermore, the WES overcomes the accuracy limitations of mechanical and proximity microswitches used in brake monitoring. By eradicating the contact pollution and greatly reducing the hysteresis issues inherent to these designs respectively – the WES offers improved brake monitoring accuracy.
Each of these three innovations were developed in response to technological challenges we faced as a business. However, with our engineering capability and experience, we were able to deliver advanced solutions with in-built performance advantages.
E.E: What estimations do you have for 2021?
M.R: We are encouraged with the economic recovery that began earlier this year. We will continue to innovate, focus on penetrating our core markets, serving our customers and creating value for all of our stakeholders.