watttron GmbH is a spin-off of the Institute for Natural Materials Technology of the University of Dresden and the Fraunhofer Institute for processing machines and packaging technology (IVV) Dresden. The company was started by Marcus Stein (current CEO at watttron), Ronald Claus von Nordheim (CPO) and Dr. Sascha Bach (CTO), supported by Michaela Wachtel (COO) in February 2016 in Freital, near Dresden. Meanwhile the company employs approximately 50 people at the corporate office in Saxony and two offices in the USA.
The company develops and produces innovative heating systems, which are used in industrial processes where temperatures with pinpoint accuracy are needed. This patented heating technology enables, amongst others the optimization of material- and energy consumption of packaging formats. The digital sealing systems allow for very precise temperature control, also with larger sealing surfaces, which makes it easier to work with recyclable, biobased or recycled materials.
Interview with Kathrin Eckhardt, Marketing Manager at watttron GmbH.
Easy Engineering: What are the main areas of activity of the company?
Kathrin Eckhardt: At the moment the international packaging industry is the main target industry branch of watttron. Watttron has customers worldwide. Sustainability is one of the biggest drivers for innovation in the packaging industry right now. Different materials and material structures will need to be adopted and along with them new packaging technologies. Using mono-materials is the obvious solution for recycling. Such materials have a very small processing window. That means that the sealing temperature window must be between 2 and 5 Kelvins. Existing heating systems have temperature deviations around 5 to 10 K and cannot guarantee an accurate temperature control and therefore the hermetic food safe closure is not guaranteed. This is particularly true in critical sealing areas such as zipper location, double fold areas of a pouch or the critical sealing areas near spouts.
These deficiencies of the current heating systems can be solved with the help of the patented new category of heating systems, introduced by watttron, and called cera2seal. Watttron develops and provides digital heating systems that can generate heat directly at the film surface contact point. Instead of one heating element as in conventional systems, watttron‘s cera2sealÒ system provides multiple independently controlled heat circuits (heat pixels, size 5x5mm) with integrated temperature sensors which are placed close to the sealing surface to achieve very short closed control loop. This is done by the ceramic thick film technology, commonly used to produce circuit boards, for high temperature applications. In the case of bag sealing or cup membrane sealing the printed resistive circuits provide individually controllable heat applications to specific areas. This allows individual heating in small zones and at specific temperatures as each has a specific heat supply. The integrated control electronics additionally provide a very fast temperature control up to several hundred times a second. This leads to a very precise temperature control and process stability for sealing applications. Due to the low mass of the heating systems provided by watttron and the thermal insulation, the heaters can be heated up within several seconds and thus immediately reach steady heating status without temperature overshooting. Additionally, the low thermal mass enables the reduction of the energy consumption by more than 30%. This is a major contribution to achieve the zero emission goals for the packaging industry.
With watttron’s cera2sealÒ system an inline process control during the sealing process is possible. We offer a data driven solution which enables this inline process control.
https://watttron.de/heating-solutions/sealing/?lang=en
Another advantage of watttrons system is that due to the construction of our production they can be easily adapted to various seal profiles. We can deliver heating systems as a component for a new machine or as a retrofit module to update an existing machine in a factory. We deliver complete heating systems including heating elements, electronics and software.
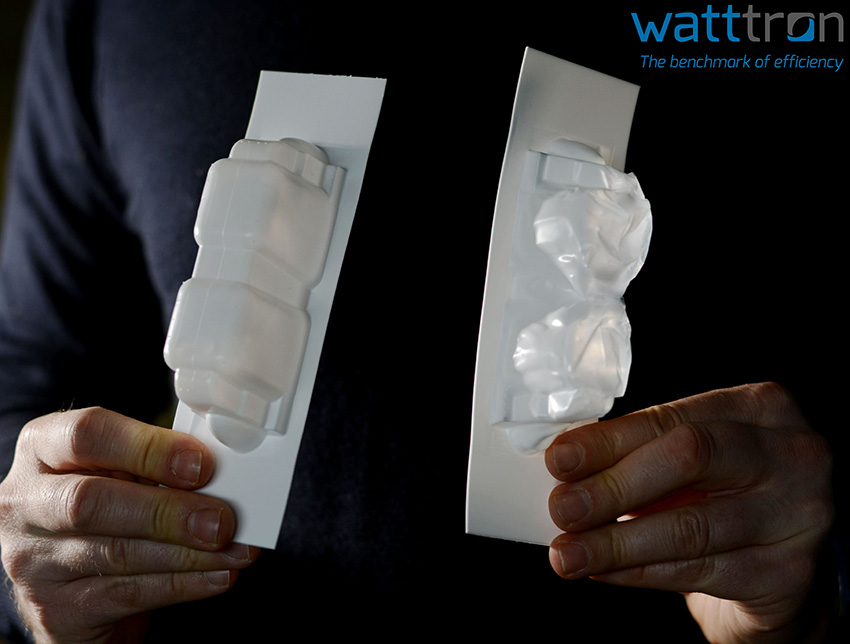
E.E: What’s the news for 2021 about new products?
K.E: Our focus is on spoutsealing tools for all kind of spouted pouches. We also complete our portfolio in the area of our cera2seal matrix sealing bars to adapt on various applications such as HFFS as well as VFFS applications. A completed new product line, the watttrix system, reaches the pilot status. With this software tool we are able to offer our customers a 100% inline quality and process control.
E.E: What are the ranges of products?
K.E: At the moment we offer the following digital heating tools. On the one side we have the patented cera2heat-system which is used for thermoforming processes. On the other side we can offer the patented cera2seal-system with different tools especially for all kind of cups and capsule sealing for the food industry. In our cera2seal – product family we also have different sealing bars in various length – which are normally used for bags and pouches. And last but not least we produce tailormade sealing bars for spouts for all kind of spouted pouches „Quetchies”, in Germany.
E.E: At what stage is the market where you are currently active?
K.E: We are in an extremely changing market at the moment. As mentioned earlier Sustainability is one of the biggest drivers for innovation in the entire packaging industry. In line with the sustainable development goals of the united nations (number 12), many brand owners have announced ambitious sustainability goals to come to 100% recyclable or reusable packages by 2025. These objectives have led to a rethinking of current packaging solutions. Different materials and material structures will need to be adopted and along with them, new packaging technologies implemented.
E.E: What can you tell us about market trends?
K.E: Simple as that! Mono materials allow easier recycling, which is inline with the ambitious sustainability goals, globally embraced by the leading brand owners. The consumers are becoming much more eco-conscious and will increase the pressure on the market. The great thing about our technology is that it not only allows for mono materials to be used, but it also reduces the energy consumption in the production process. As mentioned before, our systems can be retrofitted on existing machinery.
Flexible packaging and transformation from rigid to sustainable flexible solutions is still a major trend in the packaging industry. The use of sustainable recyclable or recycled mono-material films is the main driver in the packaging industry these days. Watttrons technology is part of the solution for reliable processing of this kind of materials.

E.E: What are the most innovative products marketed?
K.E: Basically, all of our products are revolutionary for this kind of applications, some of them are even often mentioned by customers to be game changer. Our new spout sealing tools are definitively one of those game changers and very unique and innovative – in many cases they are the enabler for the use of mono-material solutions.
The whole digital heating technology itself is one of the most revolutionary innovations in the packaging industry since many years. Not only does it allow for a much more accurate production process (with better materials), it also reduces complexity in the production process and uses a lot less energy.
E.E: What estimations do you have for 2021?
K.E: We expect a significant growth, especially now that the sustainability topic will start having an enormous effect on the market after the pandemic.
Current customers are brand owners like Procter & Gamble or Reckitt Benckiser, co-packers, machine suppliers and material suppliers. In 2021 we already retrofitted several existing machines to make them ready for the future. That’s why 2021 seems to be a very important year for us and the whole packaging industry in terms of transformation to sustainable mono-material solution. Watttron is aiming to stand out as THE solution provider in packaging sealing applications. We are upscaling our production and production capabilities to be able to provide our solutions in every application.
Video animation of one cera2seal tool
Video animation of spoutsealing tool
watttron meets Schubert – using the digital sealing technology for flowpacker machines
Video animation of our sealing bar
Phone: +49 (0) 351 271 808 09
Email: kathrin.eckhardt@watttron.com
Web: www.watttron.com