Xtrutech specialize in the design of Twin Screw Extruders for Powder Coating producers across the globe. The company manufactures cooling systems, feeders, and ancillary equipment to create a complete production or laboratory line. Xtrutech also supplies spare parts such as screw elements, shafts, and barrels to further support customers.
Interview with Ryan Moore, Managing Director at Xtrutech.
Easy Engineering: What are the main areas of activity of the company?
Ryan Moore: Xtrutech manufactures Twin Screw Extruders and ancillary equipment. We supply a range of production equipment to our primary market in Powder Coatings.
We have a separate range of laboratory extruders and equipment for Thermoplastics, Biopolymers, Medical Plastics, Chemicals, Food and Pharmaceuticals.
Alongside our machine sales, Xtrutech is a leading independent supplier of OEM spare parts.
E.E: What’s the news about new products?
R.M: Our latest product release is the XTS Compactor, a Fines Recycling System for the Powder Coatings Industry. Xtrutech’s machine has been designed to effectively reduce waste, by compacting fines and reintroducing them to the mill as chips.
The XTS Compactor provides a discreet and effective solution to fines waste. Offering measurable cost savings, increased efficiency, and improved sustainability.

E.E: What are the ranges of products?
R.M: XTS or Xtrutech Twin Screw is our signature range for Twin Screw Extrusion. Each machine is designed and manufactured by Xtrutech in our UK Headquarters.
The XTS range features production extruders, exclusively created for powder coatings. This includes the XTS35, XTS44, XTS56 and XTS65 Twin Screw Extruders. To create a complete extruder line we manufacture drum coolers, cooling conveyors and feeders.
Our laboratory range of extruders includes the XTS11, XTS19, XTS24 and XTS35 Twin Screw Extruders. This range is suitable for a variety of industries and focuses on R&D and sampling applications. To accompany our laboratory extruders, we have a selection of bespoke ancillary equipment that includes High Speed Mixers, Water-Baths, Pelletizers and more…
To provide comprehensive support for our customers, we supply spare parts such as screw elements, barrels, and shafts. Xtrutech supply quality OEM spares for a range of Extruder manufacturers.

E.E: At what stage is the market where you are currently active?
R.M: In recent years it has become clear that our customers are more aware of environmental issues. As a result, they are actively seeking responsible choices amongst their supply chain.
Xtrutech are pleased to offer a selection of innovative solutions for our customers. This includes Bio-Polymer Extrusion Lines and Fines Recycling Systems. Our designs focus on energy efficiency, decreased maintenance times and the reduction of waste. This means we can offer our customers reduced energy charges, production downtime, transport times, and landfill costs.
E.E: What can you tell us about market trends?
R.M: The pandemic led to a reduction in air travel across the globe, which had a direct impact on the availability of service support. It became evident that our customers required a robust, high-quality, Extruder Line that prioritized reliability.
Xtrutech have invested in creating extrusion equipment with longer production lives and consistent high outputs. We utilize only the very best materials and parts during manufacture. As a result, Xtrutech have successfully reduced downtime for our customers, as they require fewer spare parts during maintenance shutdowns.
Xtrutech follows the quality product market model. So that our customers can enjoy high outputs and production, without feeling the effect of the current global shortage of materials and parts.
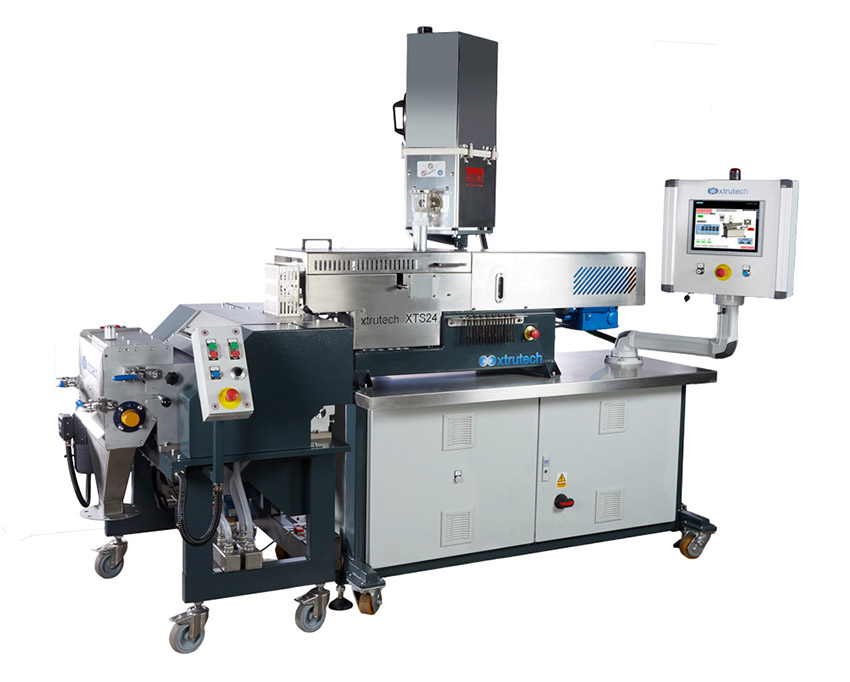
E.E:What are the most innovative products marketed?
R.M: Xtrutech focuses on providing sustainable solutions for our customers. For example, the XTS Compactor is a Recycling System that addresses fines waste during production.
Fines are small particles of powder coating paint that are wasted due to their size and density. Typically, a powder coating plant produces between 2% and 10% of fines during the milling process.
The XTS Compactor receives these fines via the diverter valve, which is then fed through to the compacting rolls, reaching the kibbler to be cut into chips. The compacted chips are then reintroduced to the mill. Using this method, we can successfully improve raw material & environmental efficiency for our customers.
E.E: What estimations do you have for 2022?
R.M: Currently we are seeing a tentative marketplace due to various external factors. Covid related issues, especially within Asia. Also, the consequence of an ongoing war in Europe.
However, we expect to see a continued growth due to our expansion into Asia and North America. Through innovative ideas and developments Xtrutech remains ahead of the competition, within the bio polymer and powder coating extrusion markets.