Bunting is one of the world’s leading designers and manufacturers of magnetic separators, eddy current separators, metal detectors and electrostatic separators for the recycling, mining, mineral, plastics, quarry and processing industries. The European manufacturing facilities of the global Bunting Group are in Redditch, just outside Birmingham, and Berkhamsted, both in the United Kingdom.
Easy Engineering: What are the main areas of activity of the company?
Bunting: Bunting specialises in designing and manufacturing technical equipment to separate, identify and recover metal and magnetically-susceptible minerals and materials. This includes an extensive portfolio of magnetic separators to separate ferrous metals, eddy current separators to recover non-ferrous metals, metal detectors to identify problematic metal contamination, and electrostatic separators.
The range of separation and detection equipment is widely used in the processing and bulk handling industry including recycling, mining, mineral processing, ceramics, plastics, and food.
E.E: What’s the news for 2020 about new products?
Bunting: The 2020 launch of the new Bunting ElectroStatic Separator is in response to enhanced material separation requirements in the recycling, plastics and minerals industries. The ElectroStatic Separator uses tungsten electrode wire to generate electrostatic charges to separate dry liberated particles. The new technology significantly broadens separation capabilities, opening up new opportunities for recovering materials from waste and optimising mineral reserves. Advanced ElectroStatic Separation technology is only available from a limited number of global companies. Customers are invited to undertake controlled tests on a laboratory-scale ElectroStatic Separator at Bunting’s Europe Customer Experience Centre in Redditch, UK.
Additional information – https://www.mastermagnets.com/new-electrostatic-separator/
2020 also marks a major expansion of the Bunting manufacturing and office facilities at their plant in Redditch, UK. The extension will increase both production and office space by 50% and follows a sustained period of sales growth. The work is scheduled for completion in October 2020.
Additional information – https://www.mastermagnets.com/bunting-redditch-site-expansion/
E.E: What are the ranges of traded products?
Bunting: Bunting specialises in designing and manufacturing a wide range of separation equipment including Magnetic Separators, Eddy Current Separators, Metal Detectors and ElectroStatic Separators.
The most commonly used magnetic separators include Overband Magnets (using both permanent and electromagnetic designs). Overband Magnets automatically remove tramp ferrous metal from conveyed products such as aggregates and recycled materials. The full range of magnetic separators is one of the most extensive in the world and includes widely-used small Tube and Grid Magnets and complex high-intensity Rare Earth Roll Magnetic Separators.
Bunting’s range of Eddy Current Separators includes both eccentric and concentric magnetic rotor designs. Different magnetic rotor configurations enable the efficient separation of both large and small non-ferrous metals.
The Bunting range of Metal Detectors extends from industrial designs for quarries and mines to high-sensitivity models for the food processing industry. Robust and heavy-duty Metal Detectors for conveyors handling bulk materials identify and reject tramp metal that damages processing plant such as screens, crushers and conveyors. Free-fall Metal Detectors, such as the quickTRON, locate and separate small metal fragments found in materials such as granulated plastic.
The Customer Experience Centre at Bunting’s Redditch facility in the UK features more high-intensity magnetic separation technology than any other laboratory in the world. Companies send samples for testing to prove the separation capability and efficiency.
E.E: At what stage is the market where you are currently active?
Bunting: Each market has varying degrees of both maturity and evolution. The mining, mineral processing, plastics and recycling sectors are adapting to rapidly changing legislative requirements. Due to restricted reserves, mineral and mining companies are processing more complex deposits, often requiring enhanced beneficiation including adopting high-intensity magnetic separation and electrostatic technology. Additionally, mineral waste is being remined and processed to recover valuable minerals previously considered waste.
The recycling sector continues to evolve and adapt to the ever-increasing demands to recover, reuse and recycle waste materials. Pressure from politicians and environmentalists is driving investment, with separation technology being a key part of the recycling process, especially as the value of the recovered metal is vital to the economic viability of recycling. The continued global backlash against plastic waste is driving plastic manufacturing companies to adopt new designs and processes. Stricter regulations on plastic waste drive the industry towards enhanced reuse of secondary plastics or organic plastics.
E.E: What are the most innovative products marketed?
Bunting: The three most innovative products are:
ElectroStatic Separator – The ElectroStatic Separator, launched in 2020, enables material separation that were previously difficult or posed environmental problems. The technology is designed specifically for use in the mineral processing and recycling sectors.
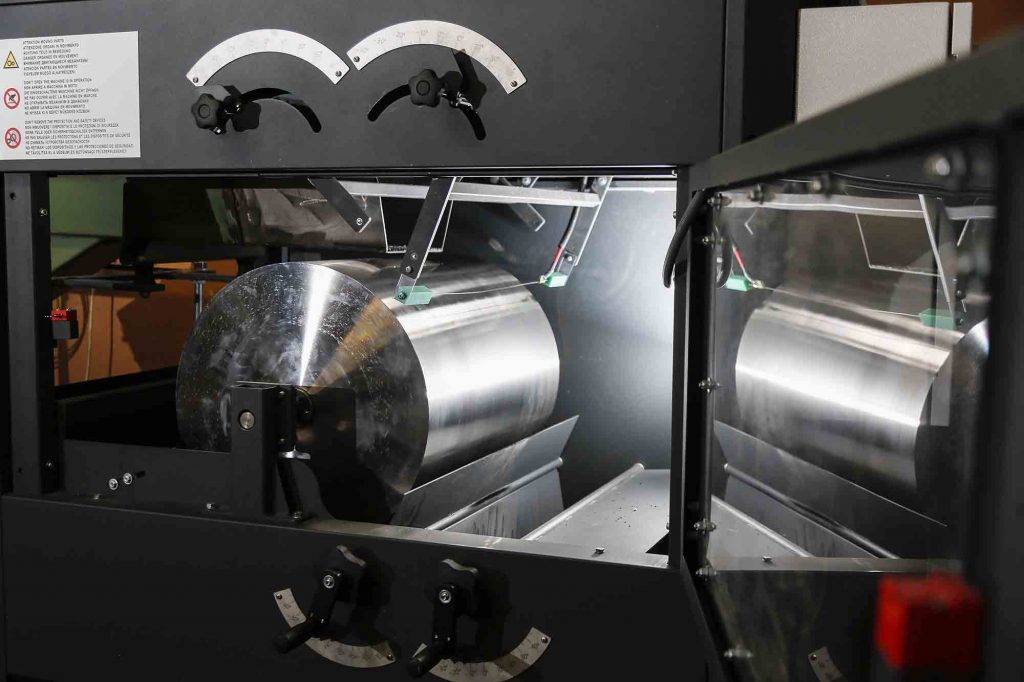
More information – https://www.mastermagnets.com/product/electrostatic-separator/
Stainless Steel Magnetic Separator – The patented HISC and SSSC magnetic separators enable the recovery of work-hardened stainless steel from secondary materials in the recycling process. This either produces a valuable recovered metal fraction or cleanses the waste material (i.e. plastic) of problematic stainless steel. The design of the high-intensity magnetic head pulley is unique, producing intense attraction of weakly magnetic materials.
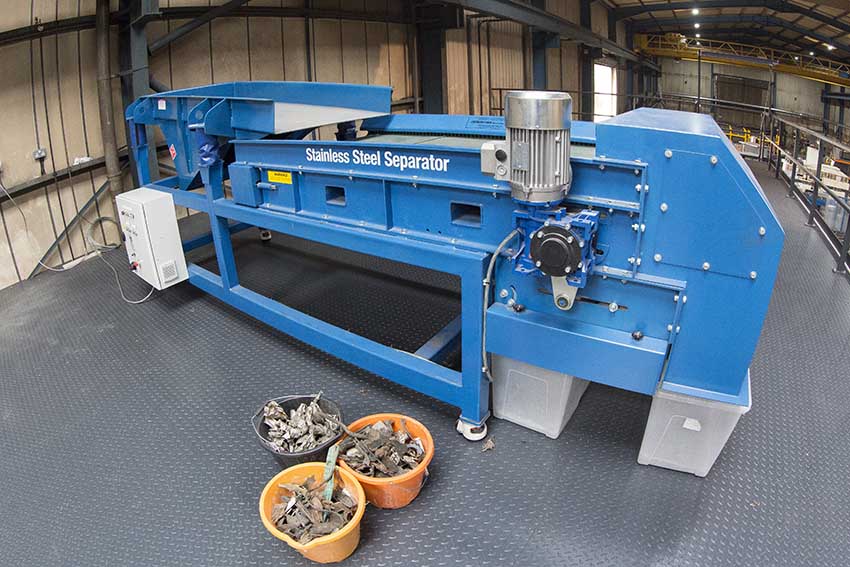
More information – https://www.mastermagnets.com/product/stainless-steel-separators/
Magnetic Disc Separator – The Magnetic Disc Separator preferentially separates minerals in accordance to their magnetic susceptibility. Installation experience has led to redesigns to enhance the separation performance. Presently, Bunting is one of a select number of companies manufacturing the technology and the latest design enables enhanced mineral separation and recovery. One of the most common applications for the Magnetic Disc Separator is for processing beach sands and coltan (a combination of columbite and tantalum).
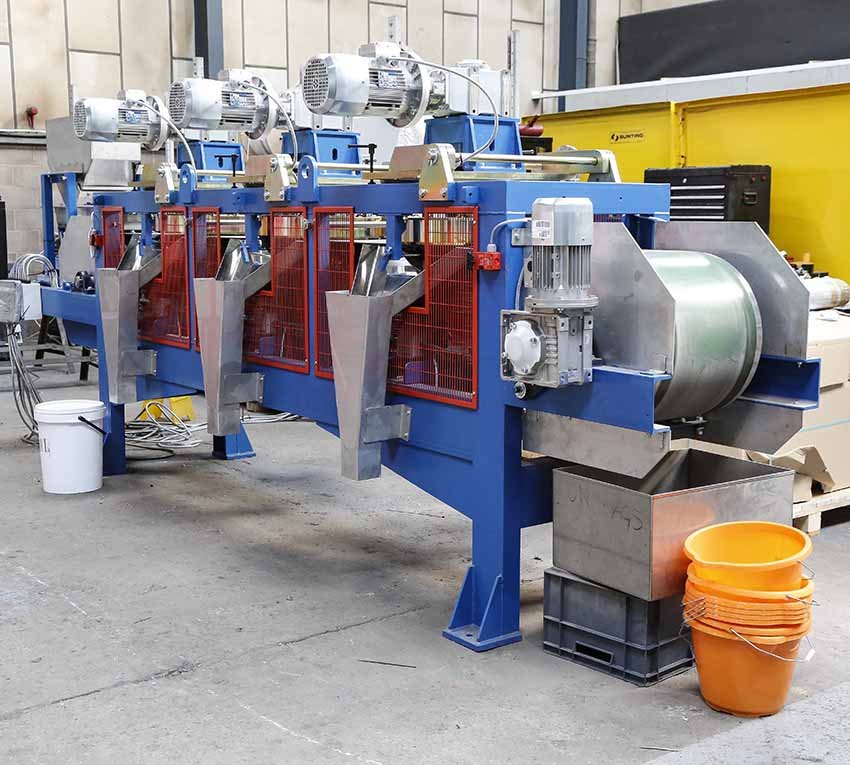
More information – https://www.mastermagnets.com/product/disc-separators/
E.E: What estimations do you have for 2020?
Bunting: At the beginning of 2020, nobody could have predicted the chaos and uncertainty created by the Covid-19 virus. The outlook continues to appear uncertain, with a second surge in cases across Europe. Throughout the crisis, Bunting has continued to manufacture and operate, supporting customers around the world. With the growing demand for high-purity raw and recycled materials, separation equipment is playing an increasingly important role. Bunting’s investment in expanding their manufacturing facility is in preparation for the anticipated growth in demand towards the end of 2020 and moving into 2021.