There is a significant unmet market need for nano-silicon to unleash longer-range, faster-charging electric vehicles and a cleaner energy future. The company’s mission is to become the world’s leading producer of drop-in nano-silicon anode powders for the next generation of advanced lithium-silicon batteries.
Interview with Andre Zeitoun, CEO & Founder of Ionic Mineral Technologies.
Easy Engineering: How do you see sustainability and what are your efforts in this direction?
Andre Zeitoun: Sustainability is intrinsic to Ionic MT’s mission to electrify the future and power the next generation with our silicon anode lithium-ion battery material. The company was founded to meet the much needed demand for cleaner, higher capacity battery materials and is vertically integrated through control of the largest and highest purity halloysite deposit in the world.
Our halloysite clay deposit, Halloysite Hills, is located in Utah. Our sustainable focus starts here at the source; we utilize halloysite’s natural nanotubular morphology to develop our naturally-sourced nano-silicon, Ionisil ™, at our battery materials production facility, also based in Utah.
The world must move towards a sustainable energy economy. It is known that we need to move away from fossil fuels to reach electrification, and the Inflation Reduction Act and the record carbon emissions levels shown in the International Energy Agency’s recent 2022 report echo this. However, electrification is reliant on navigating interlinked issues, such as the materials supply chain with regards to sustainability and shortages as well as an over reliance on imported minerals used in batteries, such as graphite. In 2022, China was the largest single source of foreign battery material imports and controls 85% of the global mining capacity. Ionic MT’s vertical integration within the US will remove these issues and pave the way for a more sustainable, domestic battery materials supply.

E.E: Tell us about the sustainable solutions and innovations that you offer.
A.Z: Our nano-silicon, Ionisil ™, is a drop in solution for higher capacity batteries, with one ton of nano-silicon equivalent to seven tons of graphite. We have developed the greenest, most scalable process to produce nano-silicon anode battery material on the market. This is attained through our unique feedstock and patented process. Our halloysite-derived feedstock has a naturally occurring nanotubular structure which means that it can be efficiently converted to nano-silicon and scaled up.
E.E: Tell us about sustainability in production & distribution.
A.Z: The greatest challenge of producing nano-silicon at scale is controlling its morphology during the synthesis. As our halloysite feedstock nano structure was synthesized in the ground over 35 million years ago, we can apply our top-down synthesis process requiring significantly less energy input using a continuous process. We will be continuing to scale up production at our new commercial production facility this summer.
Additionally, our nano-silicon production process creates alumina as a by-product, which is listed as a US critical mineral. For every ton of nano-silicon we produce, two tons of alumina will be produced. We will also reclaim the acid used during our manufacturing process as well as producing additional by-products from our reductants.
Based on our initial reserves, we are capable of producing over 600,000 tons of finished nano-silicon over the life of the mine, equivalent to 6 million tons of synthetic graphite based on silicon having 10x higher energy density.
Ionisil™ Gen 1 – Drop in substitution of Graphite
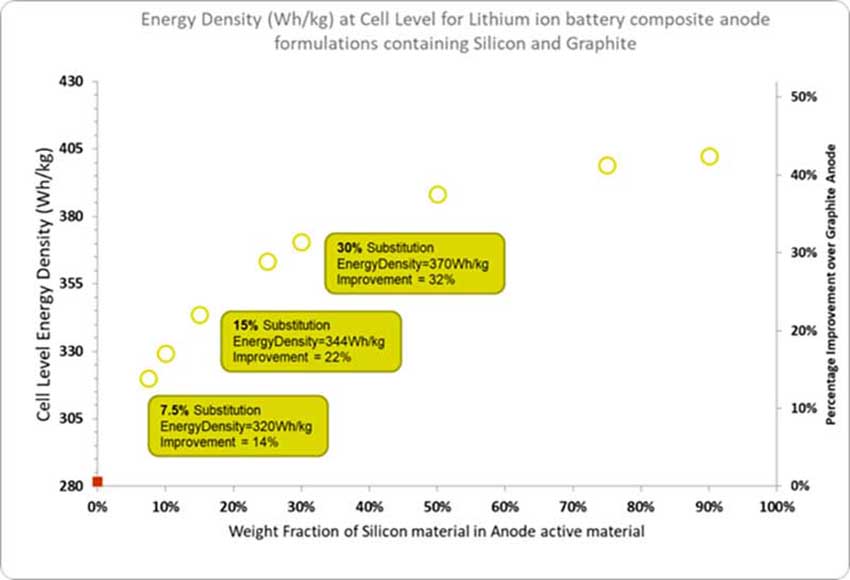
E.E: What is the company strategy to reduce environmental impact?
A.Z: Ionic MT’s strategy is to approach sustainability from the outset and this is achieved through our halloysite feedstock. We believe that while sustainability in the electrification movement is essential, it should not be difficult.
E.E: Tell us about preserving resources and driving circularity.
A.Z: Our halloysite deposit is an open pit mine and can be easily mined without using water, chemicals or explosives. Halloysite Hills was initially mined in 1952 for the production of firebrick. The operation consisted of two small open pits, though it was abandoned shortly afterwards. We then repurposed the area after discovering the vast halloysite deposits.
After an area has been mined, it is restored and revegetated with native plant life. We are also discovering significant new halloysite reserves via our extensive drilling programmes.
E.E: How do you see sustainability in the future?
A.Z: We envision the industry moving towards more sustainably sourced, domestic battery materials and adapting improved production methods to integrate sustainability throughout the process as much as possible. The electrification movement doesn’t have to heavily rely on imported minerals or compromise sustainability.