The fish industry is booming now but rising energy prices are forcing companies to look for ways to increase their production efficiency, for example, by upgrading their equipment or robotising their processes. Lavango Engineering, a Lithuanian company manufacturing equipment for international markets in this sector together with its partners, uses green energy itself. That is why this engineering and production company with 15 years of subcontracting experience is today an especially attractive production partner even for those food industry equipment companies that did not even consider subcontracting before.
The CEO of Lavango Engineering notes that it is companies manufacturing food industry equipment for the fishery sector from whom his company receives the most subcontracting requests in the last few months.
The contribution of the aquaculture and fisheries sector to the world’s gross domestic product (GDP) ranges from 1% to 10% in recent years. This is because of the growing demand for seafood and the so-called superfood as well as the price of the products. The growing popularity of healthy lifestyles and healthy diets also contributes to this.
The fish industry can no longer ignore the issue of efficiency
According to the interviewee, this sector of the food industry is unfortunately one of the most sensitive to fluctuations in energy costs: energy is needed for fish farming (electricity), fishing (marine fuel), processing of raw materials, supply of ice, refrigeration, drying, smoking and other processes. In addition, rising prices of raw materials also encourage food industry companies to look for solutions to optimise production. The purchase of fish and raw material is the dominant cost item for the sector, accounting for more than 70% of the total production costs, increasing over time.

Rising operating costs are another reason for the need to improve the efficiency of operations. Over the past two years, the index of global fuel energy prices has grown sixfold due to persistent energy supply shortages. It was further aggravated by the war between Russia and Ukraine. These are the most pressing issues, but one should not forget about rising wages, the legal obligations on industrial companies to invest in sustainability, and other external factors. All of them are drastically putting food industry companies in a trap, i.e. a situation where they can no longer afford to ignore the need to solve this problem. There are already cases when entire factories stop their operations due to a sudden increase in costs.
Synergy of two engineering companies produces the best results
In order to get out of the difficult situation, food industry companies are looking for solutions. One of them is to invest in new equipment that increases efficiency. Although some companies expect payback within just 2.5 years, in this sector, according to Srėbalius, a payback period of 5 years is usually estimated. “However, there are also extremely successful examples where the impact of the installed equipment on operational efficiency becomes apparent as soon as within the first year, and companies succeed in making several hundred thousand euros. Such results inspire confidence in both us, as subcontractors, and our partners.
Equipment manufacturers engage subcontractors in management of development
Srėbalius notes that not only lower production costs or the pursuit of synergy in looking for the best solution determines the need to search for subcontractors.

“Such a partnership can be beneficial for a number of reasons. One of them is that an engineering company with excellent sales skills gains flexibility in managing the scale of its operations and can maintain the relationship with the customer at the peak of its activities and meet customer needs without compromising on production deadlines. Another is the possibility of avoiding additional costs, especially if the project is not typical for them or requires certain competencies or production capacities that are not available to the company at the time. In this case, extra costs of hiring employees and, sometimes, investments in production equipment and machine tools, about the future load of which the company is not sure, are avoided. In principle, it can be summarised that both cases are related to the development of companies, when subcontracting partners become a strategic tool for the optimal management of the company’s development costs,” says the company CEO.
The analysis ensures that the investment is not fruitless
An efficient production process can also be hindered by so-called production peaks, which are determined during the analysis. The example presented by Srėbalius can show this best of all. “Let’s imagine that a bakery has an automated bread packaging line that allows packing 11 to 12 pieces of bread products or even more per minute but later they have to be placed into boxes by a person who is able to put only 9 pieces within a minute. Let’s not forget that in such a continuous production process, the packaging film may run out, so a human resource will be needed to replenish it. During this operation, bread products will not be packed, which means that a production peak will be recorded. Such production peaks are usually the biggest enemies of efficient production. It is the identification of these peaks and the analysis of their causes what is the most important analytical work that we perform when looking for ways to make production more efficient,” says the expert.
The specialist responsible for the analysis performs it in three stages: first, the analysis and evaluation of the maximum productivity of individual devices is performed, followed by that of the maximum possible productivity of the entire production line, and finally a mathematical simulation of beats per minute is performed.
Investing in new devices or upgrading the existing equipment?
In order to keep up with the technologically sky-rocketing field, food industry companies more often choose to upgrade the equipment they purchased at the beginning of their operations rather than to purchase a completely new unit. The latter is chosen much less often. Most companies start the first stage of upgrading their production equipment around the 4th year of activities. The turn of the second stage of production efficiency and productivity increase comes in the 7-10th year of operation. Then the “bottlenecks” of the entire production process are looked for and thought is given to how to solve them. According to the expert, the biggest breakthrough usually happens in the 15th year. Then the entire production process is reviewed in essence and the volumes and the efficiency of the entire production cycle are significantly increased.
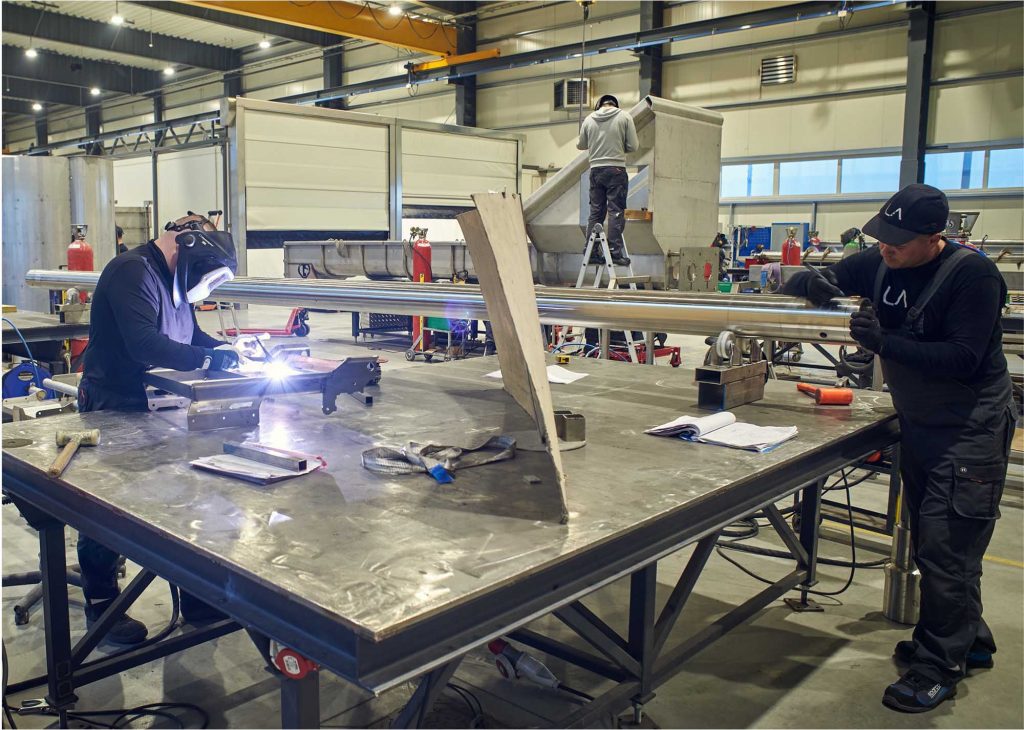
The pursuit of the communion of technology and human is not only about sustainability
Srėbalius emphasises that when planning the upgrading of a production line or individual units in order to increase their production efficiency, food industry companies should try to see the whole picture. Today, human is still there. According to the expert, production processes are rarely fully automated in companies, although technology often allows having this done. This means that when solving the problem of production efficiency, they must not only align with the highest parameters, but also adapt the rhythm of the equipment to that of the work of a human being and his or her changing productivity during the day. “In order to optimise a sustainable production process, it is important to try to achieve synergy between the technology and human”, Srėbalius shares his insights.