The company is based in Monza (ITALY) since the very beginning back in 1967. A family-based business, started from the strong will of Nava brothers to deeply innovate hydraulic presses for metal-forming.
Back in those pioneering years, the goal was to create a brand-new generation of presses both capable of performing at higher level and, anticipating the spirit of later years, assuring a high level of safety for people involved in production.
The new presses brought to the market distinguished themselves for a very high-quality level, both in design and product as well as service for customers, delivering high overall availability of our solutions for customers.
Interview with Andrea Nava, Co-Owner of F.lli NAVA srl.
Easy Engineering: A brief description of the company and its activities.
Andrea Nava: Many of our customers – beginning their operations as a “startup” said in the language of nowadays – have built the success and so far the growth of their companies relying on the continuity and quality of production of the Nava hydraulic presses.
This spirit of innovating the product and often anticipating the safety requirements laid down by technical regulations, first in the Italian and later in European market, has been continuing through the years.
Nowadays the new requirements of the market and the most demanding customers are about green design (optimization of energy consumption mostly) and full lifecycle support of the press / forming application, preserving value of investment both of new press through maintenance and after several years of deep exploitation in production with retrofitting of machines to bring them to top performance.
The care of the customers extends also in supporting them with mould issues / applications as well as supporting them in order to solve inconveniences with presses of other manufacturers.
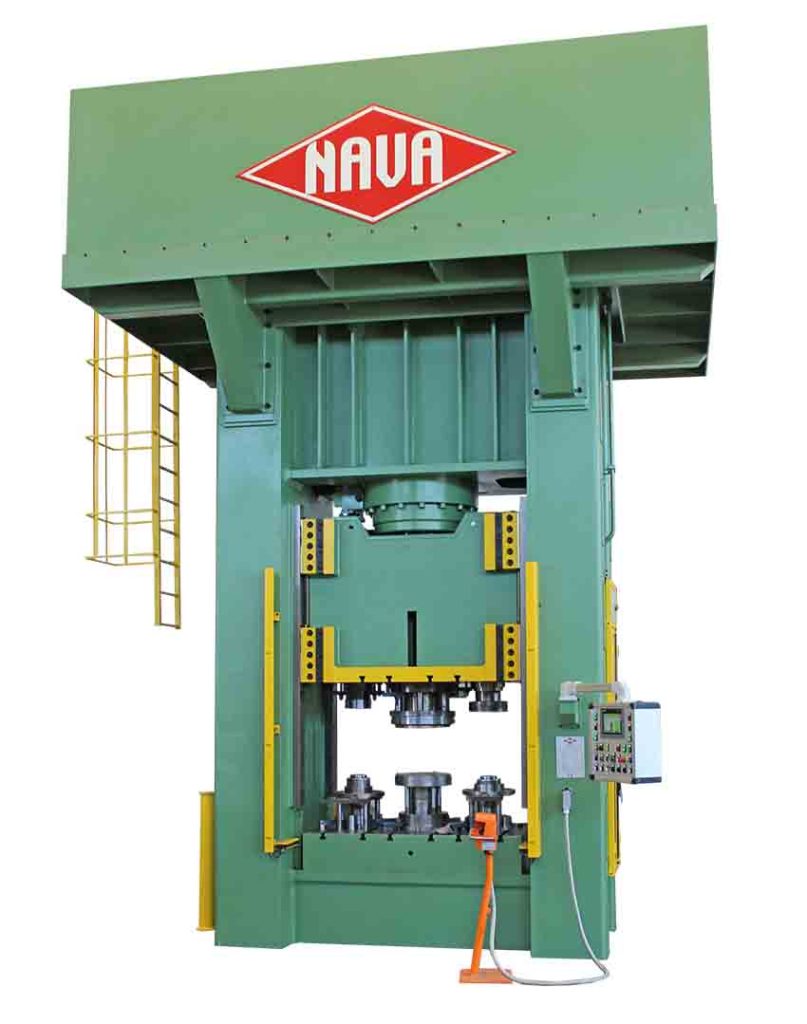
E.E: What are the main areas of activity of the company?
A.N: The company is involved in design and manufacturing of hydraulic presses, mostly aimed for metal forming. This ranges through deep and very deep drawing of sheet metal parts, both of mild steel and stainless-steel parts, as well as aerospace meant materials. A role is played also by special forming technologies, normally devoted to metal forming: rubber-forming (Guerin method) and hydroforming (both tube and sheet metal applications for pieces with undercut).
E.E: What’s the news about new products?
A.N: Our products are always on the run for improvement through the cooperation with end-users.
Assisting them for special / new needs, is the key to innovate our solutions continuously, helping customers to cope with their special or day-to-day needs. The developments flow into design of the next wave of our hydraulic presses.
A very high level in mechanical structures and hydraulic cylinders is for us the basis on which we start the foundation of our presses, with fundamentals fit to reach the highest levels of performance and continuity over time.
The design of hydraulics to drive the press is another key factor of competitiveness for us: we are one of the not so many manufacturers actually owning the technology and the design capability to manage hydraulics.
By means of this, we can avoid just to stick in the press “foreign” solutions from outsourcing partners, not understanding really what they are about.
Same issue about electrical and software design: we own the technology in the sense that the design phase happens all inside our project office.
Owning the keys of design of our presses makes always a great difference in our favor, towards other manufacturers just assembling parts gathered on the market from different players with a weak coordination among the parts of the whole press.
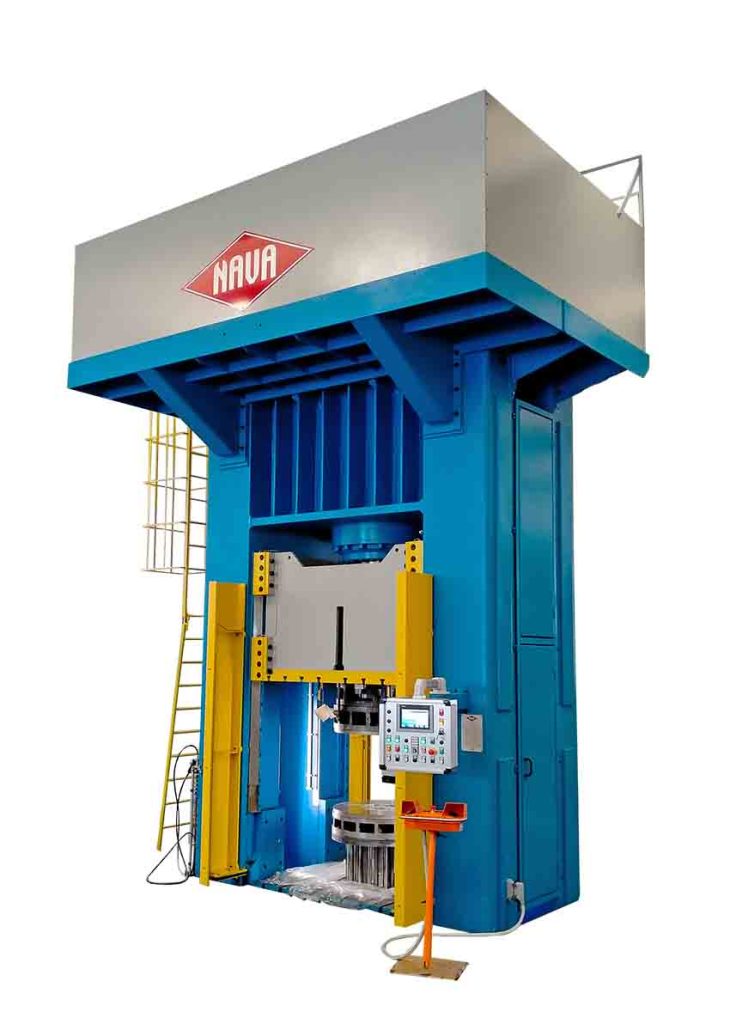
E.E: What are the ranges of products?
A.N: The product range is mostly between 100 ton up to 2000 tons for deep drawing machines.
As well, we have supplied also hydraulic presses with higher pressing force for some special applications.
E.E: At what stage is the market where you are currently active?
A.N: Our products are targeted for quality conscious markets, where the customer is looking for high quality both in design and manufacture of the press, as well as in the customer support to cope with the whole press life cycle.
Key is normally the well-known level of competence and effectiveness of our service, sometimes also providing help on presses of other manufactures, gaining so far the reputation to become the next supplier for further investments about presses.
E.E: What can you tell us about market trends?
A.N: Efficiency and flexibility as a response to current challenges
The challenges that press users have to face – and especially the hydraulic ones, which represent the core business of our company production – are connected to the need for flexibility and efficiency. When we visit our customers, whether they are new or consolidated, these are the main issues that emerge, since we are facing with a final market that asks for ever smaller lots and ever shorter order fulfillment times.
Optimization of training tools and proactive maintenance
Downstream we therefore observe attempts to respond to these inputs which consist not only in optimizing the tools that constitute the heart of the forming, e.g. the press-mould pair, but also in increasingly advanced maintenance of this whole. And this in order to guarantee continuity of use of the press, above all, but also of the mould, by means of a more proactive approach to maintenance, not aimed merely at solving emergencies, or any remote breakdowns.
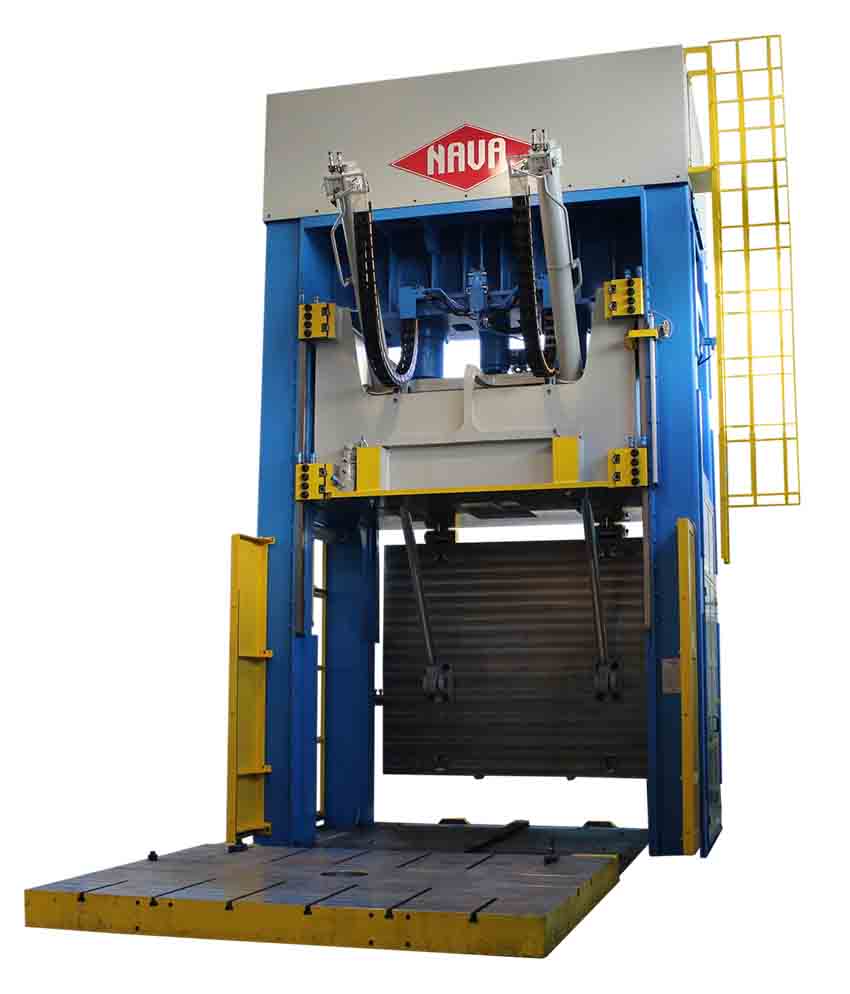
E.E: What are the most innovative products marketed?
A.N: Integration of mould and press technologies
To respond to the needs we observe in the field, the technological solutions we propose mainly focus on the integration of press and mould forming technology, which concretely translates into the same mould designed, where possible, new, to integrate several phases of processing. From this point of view, the press and the mould act not as two separate worlds, but as two correlated tools, with on the one hand the press which follows the moulds which have certain more performing improving characteristics, and on the other the moulds designed to exploit specularly machines that are more equipped, more flexible. The positioning of the mould, the way in which it is linked to the planes of the machine, is also a parameter to be controlled, since it can make tooling faster, and the entire process safer and more monitored.
We are going to propose – where requested, because some customers are already equipped and autonomous – moulds developed to be able to manage multiple versions of certain families of pieces, either by extracting different combinations from a basic figure, thanks to a mechanical update of the mould, or, in the most advanced cases, by exploiting the functions of a die itself, automated, therefore electrically piloted by the CNC of the press, which allows to pass from one combination to another with great speed.
Production data management and customized solutions
Another important dimension to consider is the integration with the management of production data, in line with a culture that has been gaining ground for some years, and which in our case was already present well before people started talking about industry 4.0.
This integration takes place above all by trying to make the customer more sensitive to this process, accompanying him in this growth, proposing more or less integrated and evolved systems, according to his needs, and therefore offering him customized solutions.
In fact, the collection of large amounts of data allows not only greater evidence about factors such as production times, the quantity of pieces produced and so forth, but also to have detailed technical and technological data available, to be exploited to carry out analyzes looking out for trends.
For example, it is possible to know how a single mould is working overtime, to understand if the performance remains constant, and therefore to improve the maintenance of the machine, also improving its energy efficiency.
The data-driven approach is much more concrete, it really reflects the reality of the field.
Data makes it possible to offer solutions based on numbers, to identify the points where real potential for improvement lurks and therefore to propose suitable solutions.
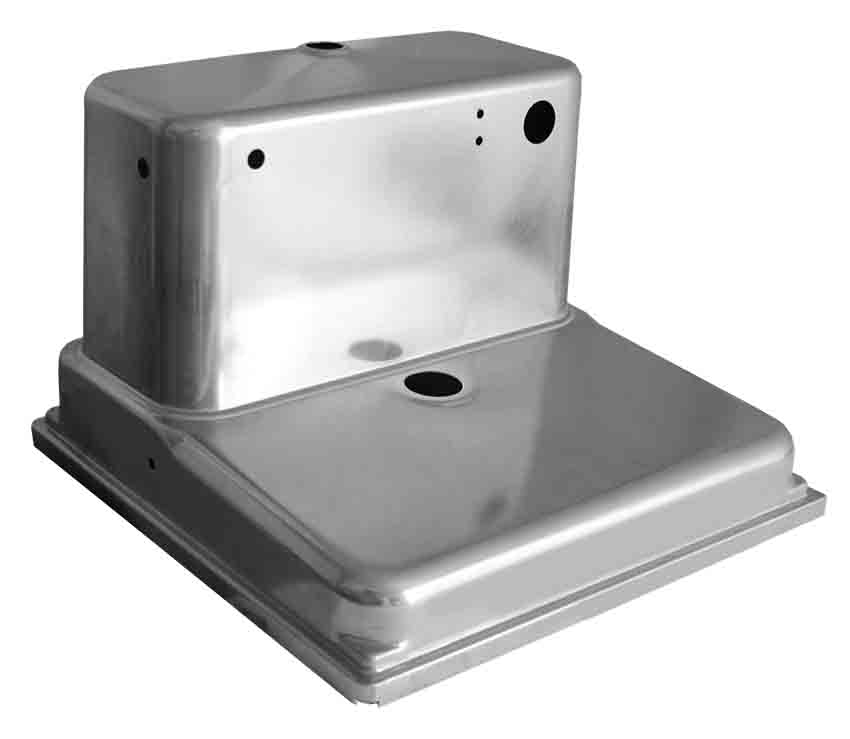
E.E: What estimations do you have for 2023?
A.N: Managing amidst the great turbulences created by political and supplier market instability, we strive to remain always positive, founding our action in the motto bringing a constant flow of quality both in presses and in services to all of our customers, firmly convinced that one of the most important assets of ours is the competence and commitment of people active in our company.
NAVA can support your company in metal forming in many ways as illustrated above, please do not hesitate to contact us at info@navapresse.it or by means of our website under www.navapresse.com.
F.lli NAVA srl
+39 (0)39 83 11 91