This article addresses the impact of brake emissions on urban particulate matter and air pollution. It examines the European Commission’s Euro VII standards, which regulate these emissions, explores concerns over non-exhaust sources such as brakes, and introduces initial technological solutions for mitigation. This sets the groundwork for further detailed exploration in a subsequent article.
Brake wear particle emissions and their environmental impact
Brake emissions are a substantial source of particles in urban areas, increasing the total number of particles in the air and contributing to PM 2.5 pollution. As engine particulate emissions have been decreasing over the last decades, the major source for particulate matter (PM) and particulate number (PN) are now tires and braking systems.
Taking a closer look on the impact of particulate emissions on health conditions reveals that this is not only a matter of mass (debris) but also size and chemical composition. While mass is mainly affecting the lifetime of the brake friction partners (pads and rotor), particulate size is responsible for picking up particles in the lung. Brake emissions should obviously not contain any toxic materials or heavy metals. Consequently, new braking systems will have to address all of them.
The influencing parameters for brake emissions are numerous and include rotor and pad material, hardness, roughness, friction, resistivity to temperature increase when applying brake pressure, thermal conductivity and heat capacity, chemical reactions between rotor and pad material at elevated temperatures creating toxic specimens, chemical reactions between rotor and pad material in wet conditions, roughness or porosity acting as a reservoir for particles while braking.
All of this requires extensive research in the context of new technologies such as electrical drive trains, electro-mechanical brake systems and autonomous driving.
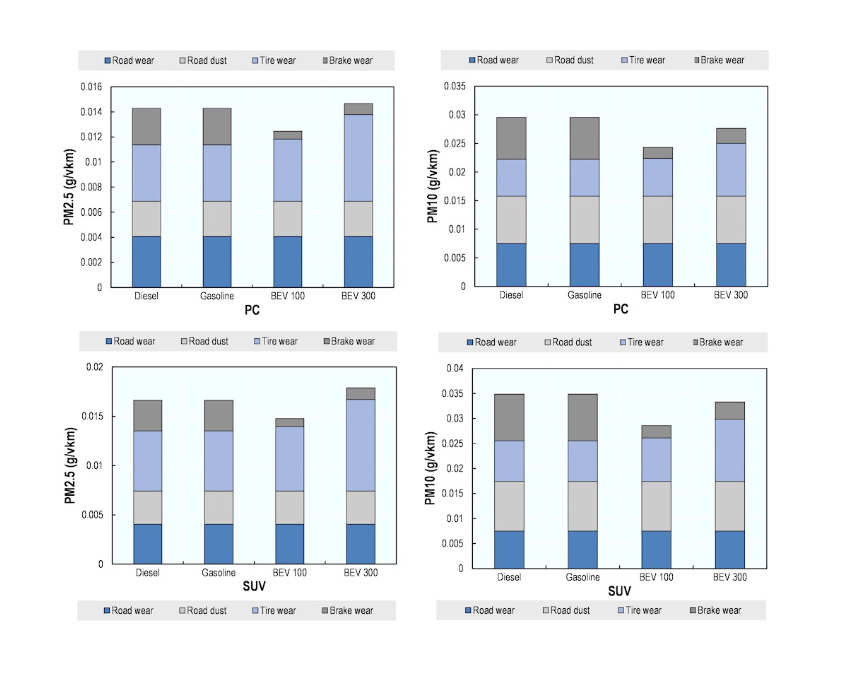
Overview of Euro VII standards and their implications for vehicle manufacturers
What Euro 7 emission standards from the European Commission are expected to income into force in 2025 for passenger cars and commercial vehicles?
The new regulations will force vehicle manufacturers to further reduce particulate emissions from cars, among other things. As powertrains have become cleaner and particulate matter from combustion has decreased over the last decades, the share of non-exhaust particulate emissions is getting into focus as their numbers are increasing in relative terms but also in absolute terms with the growing demand for transportation. Non-exhaust particulate emissions are mainly caused by abrasion from tires and brakes which applies as well to other transportation systems like rail and aviation.
As part of the Green Deal [1], the EU is now extending the fight against particulate matter to tires and brakes. Specifically for the latter, some solutions have already been developed to production maturity. However, they will only become more widespread when the EU’s binding regulations require their use.
According to Market Research Future (MRFR), a global market research company, the automotive disc brake market is projected to reach around USD 18 billion by 2025 [2].
TRW Aftermarket, a member of ZF Group, the world’s leading supplier of safety-related vehicle parts and comprehensive service, states that it produces more than 12 million brake discs per year for vehicle manufacturers and the independent aftermarket around the world [3].
Brake system design and function
According to Friction Brakes—About Tribology [4] taken from tribonet.org and published on May 10, 2021, the primary purpose of a brake system is to slow down an object in motion and/or bring it to a standstill, using mainly so-called friction brakes. This system fulfills its function by pressing a brake lining (pads) against the moving part (rotor). This creates a frictional force that is opposite to the direction of the moving part. The kinetic energy of the moving object is thereby converted into heat.
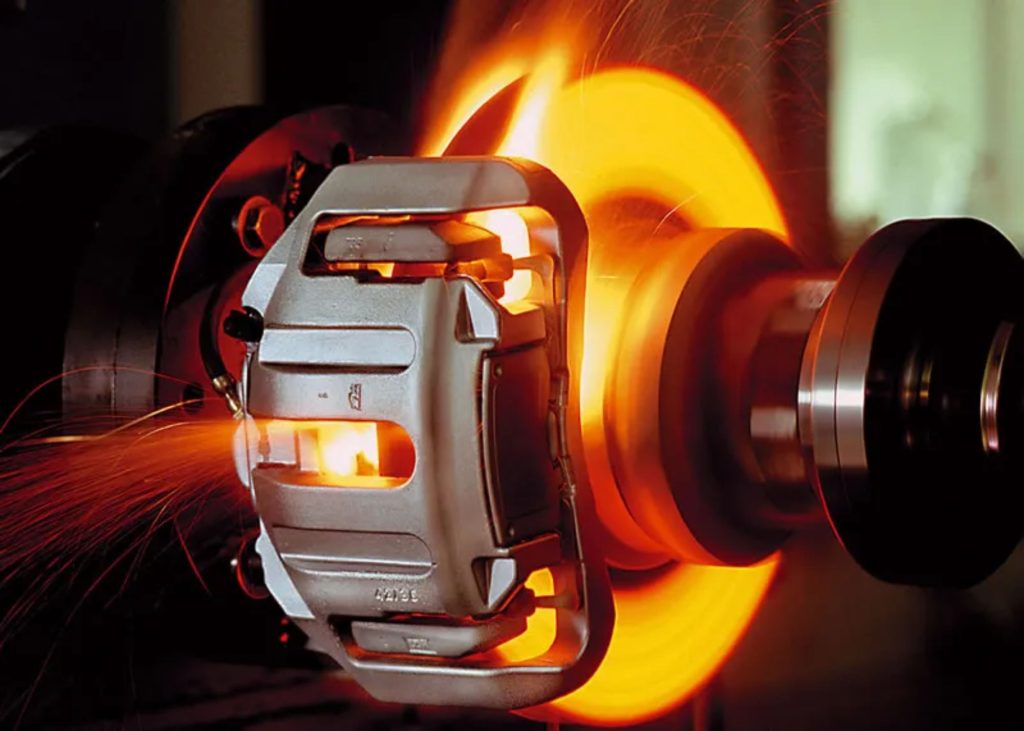
Therefore, it is essential for the friction force to remain high and stable during the entire braking action, which applies to any condition involving a wide range of contact temperatures, contact pressures and relative velocities between the static and moving parts of the brake, including any environmental changes.
The braking action leads to wear and induces vibration that also contributes to noise. Consequently, the lifespan of a braking system is mainly determined by the wear of brake components, making the topic relevant from an environmental perception, especially as the worn particles released can negatively affect living organisms.
The design of brakes is determined by the physical properties of the components as they are responsible for the friction generation, the heat dissipation, and ultimately an effective stop due to friction; their wear resistance determines the lifespan of the brakes. In short, brakes should show optimum behavior in the aspects of efficiency, durability, space for installation, and cost.
Up to now, the primary target focused on minimizing friction-induced vibrations and associated noise and considerable enhancement has been achieved by modifying the contact surface’s roughness and chemistry. With the new regulation, other parameters need to be considered: environmental friendliness paired with high stability and minimal need for maintenance.
Early research and developments: Technological solutions explored to reduce emissions
“In September 2015 the LOWBRASYS research project co-financed by the European Horizon 2020 program and coordinated by Brembo was started setting the overall goal to reduce brake wear emissions by 50%.
‘’LOWBRASYS investigated into a variety of possible solutions, among them ceramic coating for the surface of brake discs and pads, bearing the capability to reduce the number of particles emitted by about 60-90% depending on the selected layouts, also limiting the total mass of emitted particulate by between 10-30%. Applying this technology to series production on the other hand will require further development steps, as the project’s goals were of pre-competitive technical research.
‘’Changing the braking strategy by software on board a vehicle will allow for a 40% reduction in the number of emitted particles and a 20% reduction in the overall particulate mass.
“Adding a capture system to the brakes can reduce the number of emitted particles in a range between 15 -50% and reduce the emissions’ mass by 10–30%. This system will be fitted near the caliper and directs the flow of particles towards a filtering point. Initial results of the capture device look promising and development for robust operation are still carried out.’’ [sic] [5]
The findings suggest that besides other measures like recuperation in EVs, specific software additions and cleaning/filter systems, reducing brake wear particle formation addresses replacement or modification of the brake system, consisting of multicomponent composite pads bound in a polymer matrix, and cast iron or steel rotors.
One very expensive solution would be using carbon-ceramics, typically found in high-end luxury and sports cars, and simply avoiding today’s standard cast iron or steel discs. The production process requires pressing green bodies, converting them into ceramic components by carbonizing at 900°C (1,652°F), followed by siliconizing at 1,700°C (3,092°F). As such parts have very high hardness, final machining requires the use of diamond tools.
A more moderate modification would be applying a still very costly coating process to standard brake discs aiming for higher thermal conductivity to avoid high disc temperatures and therefore reducing wear and particle formation that increases proportionally at temperatures above 170°C (338°F). This coating technology would also harden the surface of the brake disc, further reducing wear and particle formation.
The most cost-effective alternative addressing mass production has been identified by applying the ferritic nitrocarburizing process (FNC) to finished standard cast iron brake rotors. Applying FNC on standard cast brake rotors is known to provide a technically and economically suitable solution when paired with a stress relieve (SR) process prior to final machining, considering the projected worldwide automotive disc brake market volume of USD 18 billion by 2025.
“Ferritic nitrocarburizing (FNC) is a thermochemical case-hardening processes whereby nitrogen and carbon are introduced into the surface of a solid ferrous alloy, in the ferritic state of the material. The nitrided layer created during treatment typically consists of a surface layer of iron nitrides and iron carbonitrides—referred to as a compound layer (also known as a white layer, due to its appearance in an etched micrograph). Underneath the white layer is a diffusion zone, which also contains carbonitrides of alloying elements.
“The principal reasons for nitriding and nitrocarburizing are:
- To improve wear resistance by providing
- High hardness (compound layer, diffusion zone)
- Improved pitting resistance (diffusion zone)
- Chemical resistivity (compound layer)
- Low coefficient of friction (compound layer)
- To improve strength behavior by providing
- Improved fatigue life (diffusion zone,expanded austenite)
- To improve resistivity against the following forms of corrosion:
- Neutral salt solutions (compound layer)
- Atmospheric corrosion (compound layer)
- Chloride ions—pitting (compound layer)
- Liquid metal (compound layer)
- Pitting (crevice) corrosion (expanded austenite)
- To improve heat resistivity up to nitriding/ nitrocarburizing temperature (diffusion zone).” [sic] [6]
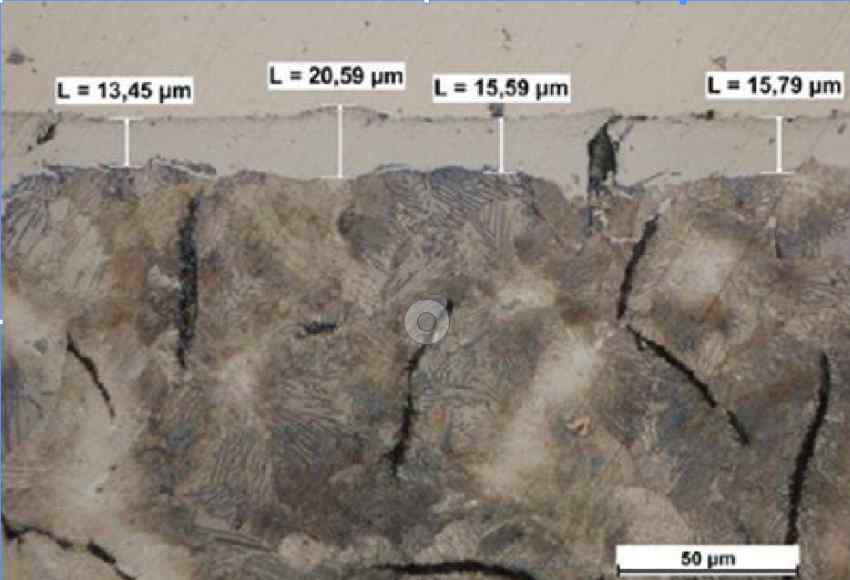
A General Motors Case Study: Applying FNC technology for mass production of brake rotors
General Motors (GM) began investigating solutions for brake-rotor corrosion and extended service life already in 2006, starting with salt bath nitriding, then implementing an environmentally friendly gaseous nitrocarburizing process [7]. By applying FNC, GM was able to reduce brake-related warranty claims by over 70% [8].
In 2011, GM brake engineer and materials expert Jim Webster presented the advantages of FNC brake rotors at the SAE World Congress & Exhibition [9].
“Ferritic nitrocarburized (FNC) cast iron brake rotors are proposed as a means to improve corrosion resistance, improve brake lining wear, as well as reduce corrosion-induced pulsation of automotive brake rotors. FNC processing of finish machined brake rotors presents challenges with controlling distortion, i.e., lateral run-out (LRO). Prior investigations of FNC brake rotors suggested grinding the rotors to correct distortion. Post-grinding the FNC-processed rotors may reduce the FNC layer with an accompanying reduction in performance. Stress relieving (SR) the casting prior to FNC was found beneficial in providing a dimensionally acceptable rotor.”
General Motors has been applying this technology to minimize corrosion from its brake rotors, while at the same time doubling rotor service life. By 2016, the automaker was already using corrosion-resistant FNC rotors on 80% of its U.S. market vehicles.
GM’s proposal addressing corrosion exposes rotors to a temperature of 560°C (1,040°F) for up to 24 hours within a nitrogen and carbon bearing atmosphere aiming for a 10-μm-thick compound layer across the entire rotor surface [7].
The resulting friction surface is significantly more durable than that of a rotor without
the FNC treatment, while remaining virtually impervious to corrosion and rust, which doubles the rotor life. Other benefits include reduced brake dust accumulation on the road wheels and smoother brake-pedal feel over time.
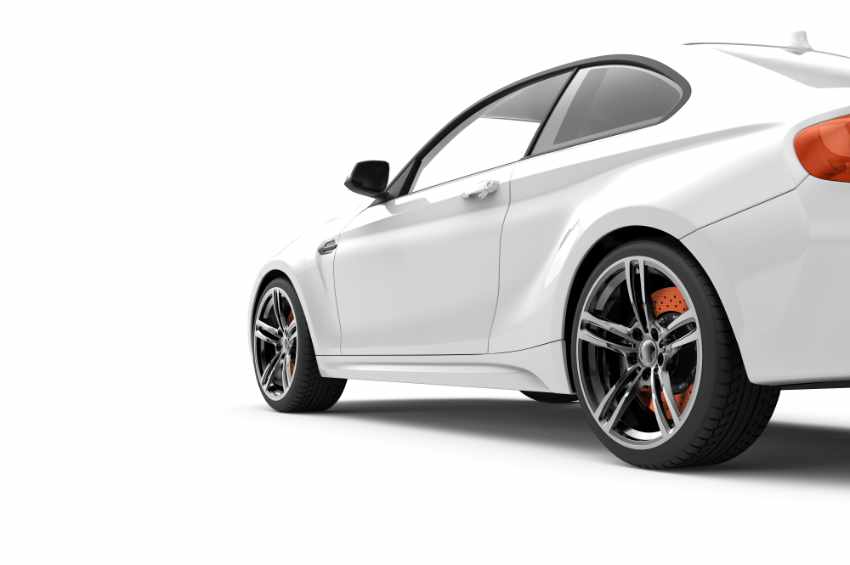
In the Next Installment
The follow-up to this article ‘LATEST TECHNOLOGICAL SOLUTIONS FOR REDUCING BRAKE WEAR EMISSIONS’ focuses on the further development of ferritic nitrocarburizing processes and their effectiveness in reducing brake wear particle emissions. The discussion extends to the integration challenges of new technologies in mass production, the potential for automation, and the future direction to mitigate brake wear particle emissions.
REFERENCES
- https://en.wikipedia.org/wiki/European_Green_Deal
- https://www.marketresearchfuture.com/press-release/automotive-disc-brake-market?msclkid=5d17a057cf8211ecab68712caf420214
- https://www.trwaftermarket.com/us/import-program-pc/disc-brake-systems/brake-rotors/
- https://www.tribonet.org/wiki/friction-brakes-aircraft-automotive/#:~:text=A%20friction%20brake%20performs%20its,energy%20of%20the%20moving%20object.
- https://www.bmb-consult.com/en/presscentre/2019/lowbrasys-the-clean-technology?msclkid=f911e8a3cf5f11ec9f608d6c4491e598
- K. M. Winter, J. Kalucki, “Gas Nitriding and Gas Nitrocarburizing of Steel”, 2013, ASM Handbook, Volume 4A, Steel Heat Treating Fundamentals and Processes, Ed. Dossett and G.E. Totten, editors.
- https://www.crossdrilledrotors.ca/blog/gm-aims-to-double-brake-rotor-service-life-with-new-fnc-treatment
- http://www.safebraking.com/brake-tech-gm-fnc-rotors-the-cure-for-lot-rot-and-more/#:~:text=Since%20its%20introduction%20on%20brake%20rotors%20in%202008%2C,the%20top%20three%20bothersome%20things%20about%20their%20cars.?msclkid=28330725cf6411ec8cd692229e66ab15
- Holly, Michael L., DeVoe, Lisa, Webster, James; SAE Technical Paper Series [SAE International SAE 2011 World Congress & Exhibition – (APR. 12, 2011)] SAE Technical Paper Series – Ferritic Nitrocarburized Brake Rotors.