Pollen AM is a ten-year-old French company, that designs and develops additive manufacturing solutions. Offering manufacturers, design offices, laboratories and various industries open 3D printers, both in terms of materials and machine parameters. pam 3D printers allow their users to benefit from a production tool adaptable to the needs of projects and materials.
Interview with Didier Fonta, General Manager of Pollen AM.
Easy Engineering: What are the main areas of activity of the company?
Didier Fonta: Pollen AM printers are primarily used to enhance R&D potential, also to produce prototypes, pre-series, and increasingly cost-effective small series. Our technologies can, as well, be useful to reduce the spare-parts warehousing and production relaunching.
Our targets are various, and we are not limited to specific sectors. We aim to help every industrial sector: automotive, healthcare, dental and medical devices, retail, cosmetic, packaging, metal industry, electronics…
E.E: What’s the news about new products?
D.F: The last innovation released was the system pam o2, the new generation of 3D printers. The pam o2 range allows to directly transform standard injection materials, in order to benefit from the same properties. It addresses industries, design offices, laboratories, research centers and academia.
The robust mechanical architecture and the temperature resistance of this new solution open the possibilities to answer many challenges. Made and assembled in France, this open and automated system integrated reliable electronics to improve component durability and efficiency. It is the best compromise between compacity, speed and accuracy.
Moreover, pam o2 systems can be equipped with new range of extruders to cover the whole family of thermoplastics, plus ceramic and metal applications.
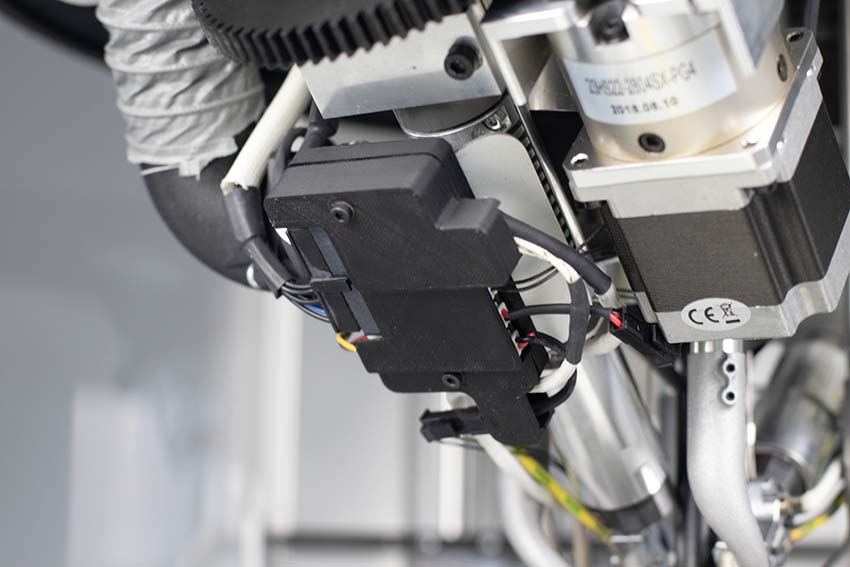
E.E: What are the ranges of products?
D.F: Pollen AM is a 3D printer manufacturer, our range includes three pam o2 printers: pam o2 MC (metal & ceramic), pam o2 HT (for performance materials) and the standard pam o2 (for thermoplastics and elastomers).
But Pollen AM is going beyond, our expertise is also taking place in material choices. The pellet market is wide, and it is somehow hard to choose the good material for the specific applications. We have partnerships with pellets sellers to advise our customers and we are proud to support them in their projects, from the printers to the materials.
E.E: At what stage is the market where you are currently active?
D.F: We have been a pure player in granular additive manufacturing for 10 years and have seen this market grow. When we started out, there was very little competition and granular solutions were not very popular with the market, which preferred closed, off-the-shelf solutions. Since then, additive manufacturing has become much more widely available, which has led to the emergence of new needs for manufacturers, particularly in terms of printable materials. The current challenge is to demonstrate the relevance of additive manufacturing in production contexts, in favor to the open system. Our approach is consistent with market needs thanks to an exhaustive catalogue of materials, the most economical format on the market materials. We are entering a very dynamic phase and are proud to be able to promote on our 10 years of experience to offer our customers reliable expertise.
E.E: What can you tell us about market trends?
D.F: The market is more mature than ever. Companies do not ask anymore what 3D printing is, they want to know the prices, the ROI, and the technical possibilities. The democratization work is done, after long years of explanation. Some activities are more mature than others, but globally, everyone understands the advantages of 3D printing.
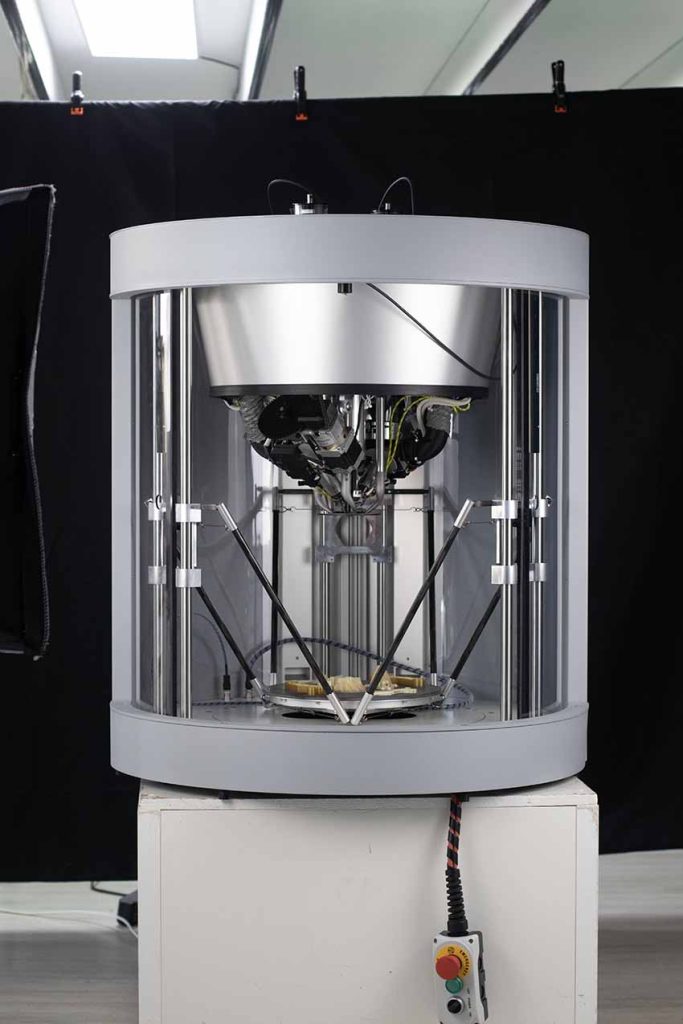
Concerning our pellet additive manufacturing technologies, it is a bit different because we have a disruptive innovation, in an innovative process. So, we still must explain the advantages of our technologies compared to standard 3D printing. In fact, it is an easy explanation, we took the best of injection molding (materials availability, technical characteristics, wide range of pellets) and the best of 3D printing (compacity, flexibility and speed), to launch pam o2. According to these elements, we think our pellet additive manufacturing is a market trend.
This trend is strengthened with the inflation on proprietary materials, and broadly the constant prices fluctuations. This is a major preoccupation for the industrials, driving to uncertainties and lack of visibility.
Another tendency is the advent of open systems, bound with the previous ones. The opening of additive manufacturing systems allows companies to have several options, not to be wedged with one supplier and not to suffer prices changes, materials dependance… That is the path Pollen AM chose, to have by design an open printer, to unleash industrial productivity and innovations.
E.E: What are the most innovative products marketed?
D.F: Our last 3D printer pam o2 is a major innovation for the sector. With our application-specific extruders, we pushed back the limits of flexibility, productivity, security, and environmental responsibility.

Using pam o2 means to produce is 5 to 10 times cheaper than the 3D printing market average. The ROI is way more interesting, including the cost of the HSE aspects thanks to the absence of additional expenses (PPE, specific room, ventilation system, etc.).
This new generation of 3D printers is twice as fast as the previous generation and machine set-up times are 7 times faster. The customers have a lot of benefits from open programming and enhanced mechanical architecture, with the ability to automate user-defined tasks, a lighter structure and redesigned motion transmission. This simplicity is paired with a unique user comfort. The silent system, the easy maintenance, the simplified system diagnostics and a 10% reduction in electricity consumption are important arguments for the companies and notably for the technician’s teams working on our machines.
E.E: What estimations do you have for the rest of 2023?
D.F: We expect sales to increase by 10-15%. We see particular appeal for our most flexible configuration, which can offer thermoplastic, metal and ceramic applications.