Predisys is a global technology company, providing licensed software for use by manufacturers. The software platform provides enterprise-grade Statistical Process Control (SPC) and real-time quality analytics, to help customers better build quality into their manufacturing process, and achieve Quality Beyond Conformity™. Predisys’ flagship product, the Predisys Analytical Suite™ was designed for discrete manufacturers that leverage a variety of manufacturing processes.
The combination of SPC and quality data analytics allow manufacturers to connect process inputs to quality outcomes in real-time. Unlike other applications in this space, Predisys does not sell a one-size fits all solution, but rather configures the application specific to a manufacturing process such as plastic injection molding, extrusion, medical device manufacture, or electronics assembly and test. This allows for more impactful insights to the end customer, and the derivation of increased cost savings and benefits.
In this sense the product remains the same, the range of the product is its capacity to be adapted to various manufacturing processes, and its ability to connect to and collect data from an extremely wide range of test instrumentation and quality systems.
Interview with Robert Fink, Executive Vice President at Predisys Inc.
Easy Engineering: Which are the most innovative products / solutions and what special features do they have?
Robert Fink: Our flagship product is also our most innovative, and this was intentional. In order to be able to provide dramatic benefit to our customers we recognized that we needed to deploy “whole products”, specific to unique processes across discrete manufacturing. Manufacturing is not the same across the discrete manufacturing space, and therefore to truly be impactful the application must be able to be configured to account for these differences, and provide actionable insights to our customers. We deploy whole products specific to all types of manufacturing processes, with all the features and functionality necessary to produce rapid ROI, and help our customers achieve Quality Beyond Conformity™.
Furthermore, the Predisys Analytical Suite֭™ is a managed application that is deployed in the customers Azure tenant. This deployment methodology allows for unequivocal data ownership by the client, world class data security, and enables the application to be rapidly scalable across the entire supply chain footprint of our customers. Additionally, the managed application approach reduces the internal IT burden for the end customer, as this is all managed by the Predisys team.
Lastly, the application is unique in the sense that users are able to connect process input data to product outcome data. This allows for a complete three-hundred-and-sixty-degree view of all aspects of quality, and for customers to be able to be able to transform the way quality is built into the production process.
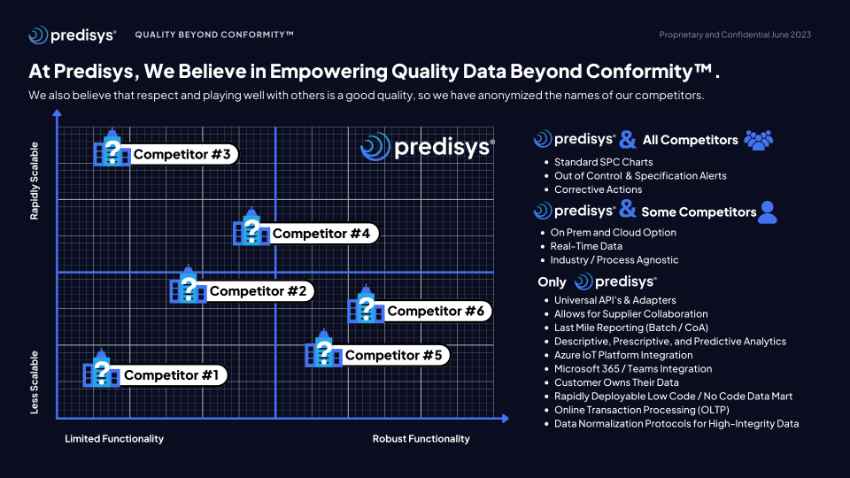
E.E: How do your best products / solutions work?
R.F: As our application is in the quality manufacturing space and leverages analytics to help our customers improve the consistency of quality in manufacturing, we recognized that we would need to allow for the collection and aggregation of data from a variety of sources. Quality or product test data can be captured via automated test machines, coordinate measuring machines, manually, and can be commonly found in MES and ERP systems. To account for this, we built a series of proprietary drivers to be able to collect the data in real-time.
Once collected, the Predisys Analytical Suite™ features a data normalization engine that converts all inbound data to a common Predisys data structure. This commonization process allows for data with varying taxonomy or structure to be analyzed in real-time. This eliminates the need for customers to perform this data aggregation and cleansing on their own, which can be an extremely lengthy process. In fact, it is common for many organizations to spend 90% of their time performing tasks to “make data ready” for analysis, leaving only 10% of time for qualified resources to analyze the data.
The role of our application is to make it easy for or customers to understand the existence and the degree of variation that exists in their processes, as well as how best to reduce variation to the greatest extent possible, while concurrently increasing product consistency from a quality perspective.
E.E: In what types of projects do clients use your products / solutions?
R.F: Our application, the Predisys Analytical Suite™ is not used on a project basis, but rather becomes part of the manufacturing process in perpetuity. We find that once deployed this application becomes a mission critical aspect of the manufacturing process and our customers rely on this data to ensure the highest degree of quality consistency.
From automated inspection reports, Certificate of Analysis, and batch reporting that can often be required by customers, to real-time SPC charts and analytics the features in the Predisys Analytical Suite™ become a mission critical element for quality execution.
Our mission statement of enabling manufacturers to achieve Quality Beyond Conformity™ was born out of feedback we received from our customers. While all quality products conform to specifications, not all conforming products are of quality. We believe that quality is the quickest path to ensure brand loyalty, increase market share, and drive profitability.
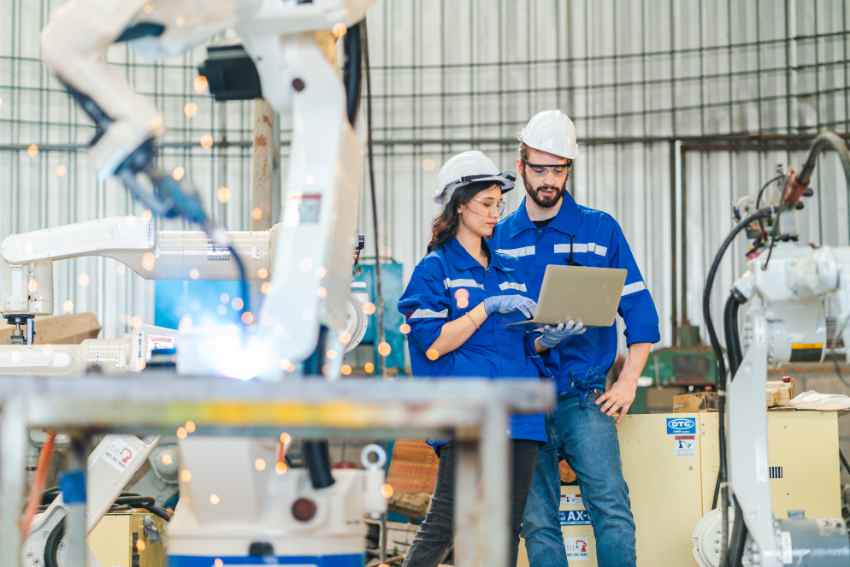
E.E: How important is innovation / R&D in your field?
R.F: R&D and innovation are tremendously important in our field. Our ambition is to revolutionize and modernize how quality is managed in manufacturing. In order to do this, we must be innovative and constantly seek to push the boundaries of the status quo.
Our R&D team is dedicated to this pursuit, and has enabled breakthroughs in our space such as leveraging the Azure platform to deploy a managed application, integration with the Microsoft Teams platform that allows for quality data to be democratized and socialized quickly throughout an organization, and our ability to aggregate and communize vast volumes of quality and test data and provide analysis in real-time.
We believe the role and need for R&D is perpetual and we are always working on making the application as cutting edge as possible.
E.E: How do your products /solutions increase profitability for users?
R.F: There are two answers or elements to this question. The first way that profitability can increase the use of the Predisys Analytical Suite™ is through the reduction of certain cost elements, and therefore a subsequent increase in profitability.
The primary way that this can occur is through the reduction of scrap and rework in the manufacturing process, while increasing throughput. This saves on both material and labor costs.
Since we deploy a managed application, internal IT costs are reduced dramatically and resources can be allocated elsewhere.
The use of the Predisys Analytical Suite™ removes the need for any data aggregation or cleansing for the end customer. This saves on labor, and allows for the time to be spent on the value-added activity of data analysis, and action on the data insights to drive quality.
The second way that the Predisys Analytical Suite™ for manufacturing increases profitability is by maintaining or increasing the end consumer perception and experience of quality. Quality is directly linked to brand loyalty, market share and profitability. We help our customer maximize their brand value through quality and therefore increase profit.
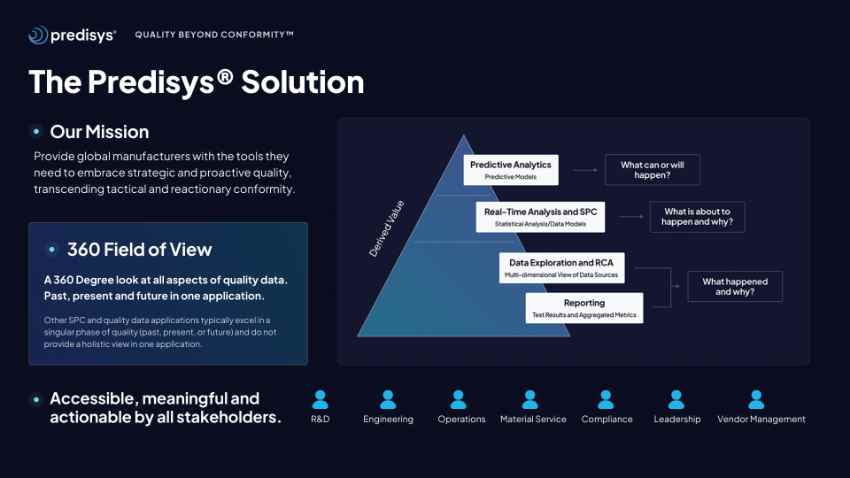
E.E: How can clients sustainably use your products / solutions?
R.F: This is an interesting question and one that is not commonly asked about most SPC and quality applications, but should be.
An interesting fact about product development is that 80% of the lifetime emissions associated with the manufacture and distribution of the product are determined in the product design phase. By allowing for access and socialization of quality data throughout the supply chain, OEMs and their manufacturers can collaborate and align on best practices for the design for manufacturability. This process allows for a product to be designed in the most efficient and economical fashion possible, while at the same time ensuring quality to the highest degree possible.
The Predisys Analytical Suite™ also allows for digitized inspection and batch reports that can reduce or eliminate the use of paper for these reports. This adds to the analytical quotient of the application, while also eliminating paper from the process. The volume of paper that is reduced from the process is extensive and provides a quantifiable sustainability benefit.
E.E: How is AI affecting your field of activity?
R.F: AI is an in-focus topic in the manufacturing space. Manufacturers are eager to understand how AI can help increase the existing benefits of our application.
In order to best answer the question, it is important to first explain that we see a distinct difference between Artificial Intelligence and Augmented Intelligence, and also there is a role for both forms of AI.
Augmented Intelligence is a form of technology that contextualizes information in order to make it easier for humans to make informed decisions. This involves the analyzation of large data sets, and presenting a condensed analysis of the data to a human for their input or decision. In Artificial Intelligence the machine or software is typically making decisions autonomously, or takes a more active role in this process.
The use of artificial intelligence can be useful in manufacturing on several fronts:
Predictive analytics – it can be just as important for our customers to understand what may happen as what did happen. Modeling that allows for simulations to better understand predicted defect rates, based on process changes allows for manufacturers to be able dramatically reduce variation associated with new product launch for example.
Interface / Query – AI can be a very useful tool on the shop floor to allow for users to interrogate an application for data through voice as opposed to a typical manual data query.
Design of Experiment – AI can help manufacturers run simulations in a digital twin environment as opposed to production, which can produce the same results without the cost of running production runs to validate outputs.
We believe in a balance of augmented and artificial intelligence, as each has applicability in certain aspects of computing. We seek to deploy a software platform that leverages both to make the end user experience as rich as possible.
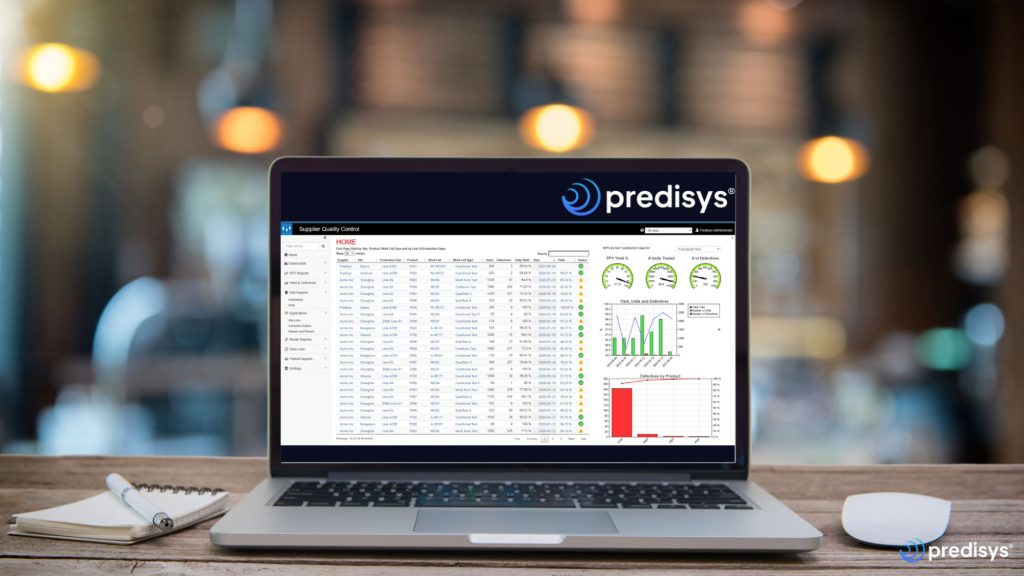
E.E: How do you see the future in your field?
R.F: Quality has become a mainstay in the news cycle, and the regulations that exist for manufacturers to help ensure the delivery of quality products to the market grow weekly. That said, I believe the focus on applications that can quantify, measure, and aid in the improvement of quality products will gain even more visibility and focus in the market.
Additionally, there is a move away from internally developed and managed applications, at least to a degree. Most large manufacturers will continue to leverage some home-grown platforms, but seek to diversify from a complete technology stack perspective. The composable enterprise model that takes advantage of publicly available SaaS and PaaS platforms for specific needs in on the rise, as organizations have seen the benefit from a cost and feature viewpoint.
E.E: What are the business plans for 2024?
R.F: The organization is focused on the continued completion of the whole product across even more manufacturing processes in the discrete manufacturing space. The aim is to make these applications as feature rich as possible while simultaneously available in the Microsoft Azure Marketplace for quick transactability and the ability to be rapidly scaled.
To date, we have completed this process for plastics processing, electronics assembly and test, medical device manufacturing, and general SPC. Deployments to date that served other manufacturing processes have involved customization and project work to support.
While we aim to deploy whole products for our customers, our development roadmap from a sequence of importance perspective is influenced by customer demand and market growth.
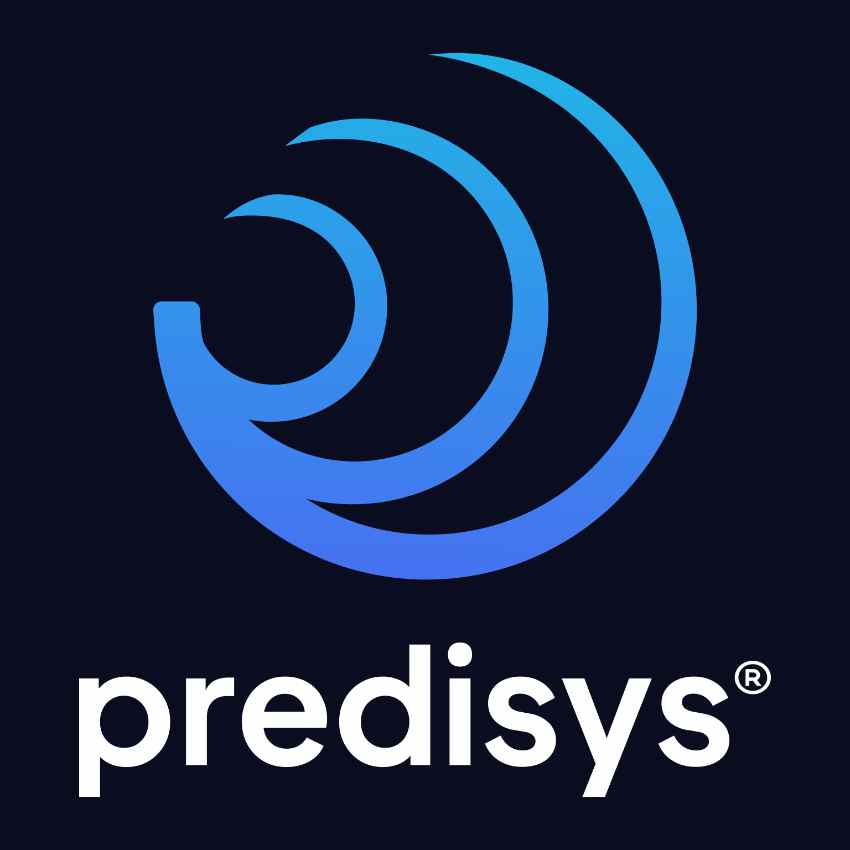
330-418-7954