Interview with Dr. Moritz Maier, CEO and Co-Founder ELISE GmbH, Bremen, Germany.
Why did you develop a new platform for engineers? What is the advantage on current software solutions?
Moritz Maier: With our open Generative Engineering platform engineers can model algorithmic workflows without coding in our visual DNA editor, get real-time CAD feedback and reduce product development time and cost while simply exploring and evaluating several design variants.
We are convinced that only open systems offer adequate capabilities to create outstanding products. For this reason, ELISE consistently offers the possibility of integrating existing, state-of-the-art software tools and controlling them via our uniform user interface.
How does ELISE change the development process for engineers?
Moritz Maier: With ELISE, the term “computer aided design” finally gains its true meaning: the user defines the boundary conditions and objectives of the design, and the computer works out the details. In this way, the designer is relieved of routine work such as the exact geometric design and concentrates – again – on his creative tasks. What we call Technical DNA is created by the logical connection of components to form algorithms. ELISE therefore requires no knowledge of programming or scripting, but still allows engineers to build algorithms from the simple to the awe-inspiring. ELISE also enables the seamless integration of logics and data coming from spreadsheets like Excel or other data sources.
Our geometric modeling capabilities enable importing and exporting of major CAD files, creation and editing utilities such as boolean modeling operators, feature modeling support, advanced surfacing, thickening and hollowing, blending and filleting and sheet modeling. We include tools for subdivision modelling, algorithm-based model editing, including tapering, offsetting, geometry replacement and removal of feature details with automated regeneration of surrounding data.
Our meshing capabilities enable highest quality 2D and 3D meshes as well as print-resolution voxel meshing. ELISE controls existing FEA software like e.g. Altair Hypermesh® to build comprehensive FE models. The integration of 3rd party FE solvers like e.g. OptiStruct® enable the physical simulation of complex models at industry standard quality as well as topology optimization.
The idea of algorithmic modeling is not new; it is used, for example, in architecture to develop recurring geometries that can be described mathematically. Instead of describing the geometry directly, this philosophy uses function blocks, called components, with input and output interfaces. Input and output flow in and out of these blocks from other blocks. In ELISE, these blocks are represented visually and the user connects inputs and outputs of different components with “cables” that transport the values and data.
Why is the developing of technical parts so much easier with ELISE?
Moritz Maier: Since the selection of components in ELISE goes far beyond pure geometry, all requirements for a component can be defined in the software – this is the technical DNA mentioned above. The network of components and inputs describes all requirements for the component and also the interdependencies of all values. A FEM solver returns result values, for example, a strength, which itself can be used as an input variable for the geometry. Likewise, instead of fixed input variables, value ranges can also be specified to allow optimization. Thus, the original goal of an evolutionary optimization can be achieved.
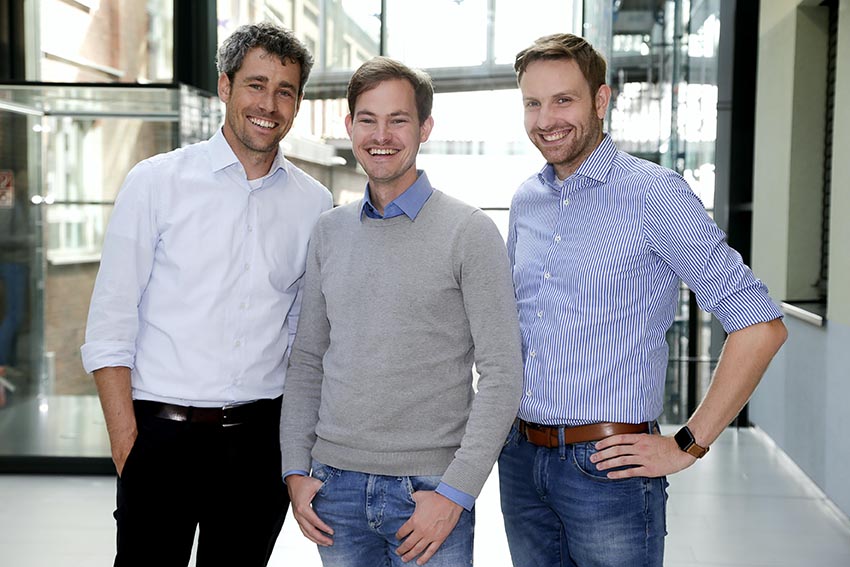
ELISE is constantly expanding its range of components and cooperates with partners in this area. These include software providers whose solutions can be “remotely controlled” via ELISE on the one hand, and research and development partners who contribute algorithms that are integrated into ELISE components on the other. And last but not least, many ELISE users and third-party providers develop their own components, which they make available to other users.
The software already offers components that calculate the cost of a part, so that, for example, the cheapest solution can be calculated with maximum strength. The company is currently working on components that calculate the sustainability of a component. In this way, the ecological footprint of a component can be included in the optimization.
Why can ELISE save time for my next engineering process?
Moritz Maier: Once such a workflow has been created, it can be fed with new values or modified in a few areas to create a successor component or variant. For example, once the requirements for the A-pillar of a car have been defined, this definition can be reused in ELISE for the successor model by adjusting the modified values. Or a component is exchanged, for example to create a round beam instead of a rectangular one. The system then calculates a new optimum and the matching geometry based on these values.
Compared to conventional optimization systems, ELISE goes one step further, because the computational model directly controls the solver, builds the geometry itself and can thus act much more flexibly. Conventional optimizers, for example, work with a manually created geometry that is modified by parameters. ELISE can insert completely new parameters or generate completely different geometries.
ELISE offers very sophisticated functions for reconstructing geometries after a topology optimization, which make it possible to smooth the “humpy” geometries that often occur during topology optimizations. In this way, solid models are created from the optimized geometry, which in turn can be further processed in the CAD system. If desired, special functions ensure that, for example, inner edges become round and outer edges become angular, as is often desired in the technical field.
At the end of the workflow ELISE shows the found shape and – depending on the output component – the results of the simulation with deformations and colored areas. The exciting thing about the component system is that it is independent of the geometry. So, for example, instead of the steering knuckle, you can enter the geometry of a wishbone, adjust the forces accordingly, and run through the same optimization routine. This flexibility is reflected in the concept of technical DNA – the basic system remains the same, the environmental parameters change. In many cases, 70 to 80 percent of the DNA – which represents engineering knowledge – can be reused, even when it comes to completely different components.
ELISE offers components that meet specific requirements for certain manufacturing technologies, such as support structures and a build plate for 3D printing. The company is working with a number of partners to develop additional components, including Materialise with its eStage software for generating support structures for 3D printing, and Hexagon/MSC with Emendate for generative design. Other partners include Fraunhofer IAPT with LBM Cost for 3D printing cost calculation and iPoint with Umberto for calculating the CO2 footprint of the design.
What are the most important fields of application?
Moritz Maier: ELISE offers mature Design for Additive Manufacturing (DfAM) capabilities with support structure generation, optimization of build-direction, warping analysis, slicing, etc. In addition, we enable the integration of third party software for industry-grade support structure generation and process simulation.
Our exploration and optimization capabilities can be used for Design of Experiments (DoE), sensitivity analyses, meta models and optimization tasks. ELISE can handle continuous (NLP), discrete/integer (IP) and mixed integer (MINLP) problems within single- and multi-objective optimization. ELISE is suitable for problems with up to thousands of variables and hundreds of objectives.
Where does ELISE come from? What is your history?
Moritz Maier: On August 1, 2018 we found ELISE GmbH and from now on develop our Generative Engineering Software, which is the logical consequence of what we have learned in more than 10 years of bionic research and engineering services.
As a technology transfer spin-off of the Alfred Wegener Institute (Bremerhaven, Germany), we continue to investigate the shells of marine plankton organisms in the Department of Bionic Lightweight Structures at the Institute for marine Resources in order to develop more effective constructions.

In 2017, our working method was published as VDI guideline 6224 part 3. It specifies the procedure for product development and optimization of lightweight structures based on natural model organisms within the framework of a defined product development process in lightweight structural construction. With our €3 million funding in 2019 we mark one of the largest seed rounds for deep-tech start-ups in Germany. The financial investors UVC Partners, Cherry Ventures, Venture Stars and BMWi Ventures support us in the further development of our Generative Engineering platform.
The first open Generative Engineering platform got launched in September 2020.
Do you have cooperation with other companies?
Moritz Maier: ELISE partners help customers of all sizes and in all industries take advantage of Generative Engineering to accelerate their product development. At ELISE, we rely on our ecosystem of partners to make our solutions even more relevant and accessible to companies like yours. Here are just a few reasons why you should consider working with an ELISE partner.
ELISE partners play a critical role by building, extending, adapting and enriching our Generative Engineering platform to deliver innovative and customized solutions that meet customers’ demanding requirements. Among our partners, you find Fraunhofer IAPT, EDAG Group or RLE International. Our partners must adhere to stringent requirements in all areas of their business operations, solutions and services. This gives you the assurance that you are working with a partner recognized by ELISE.
We encourage our partners to focus on the things that matter most to our clients, such as customer satisfaction and quality. This creates a culture that focuses strongly on building customer relationships, not just closing deals.