Plasmo is an innovative, globally operating technology company which is specialized for quality assurance systems for thermal joining processes (automated production processes).
Plasmo’s focus is on quality assurance solutions that enable customers to implement a secure, efficient and cost-optimized production. The expertise ranges from monitoring of welding processes, as well as the control of weld seams, geometric shapes and surfaces up to tailored solutions in the field of machine vision and analysis software. A wide range of services with comprehensive engineering rounds off the portfolio – worldwide. The expert team assists its customers from the moment the control task is defined until implementation of the control system.
Plasmo’s diode and camera-based systems are combinable to achieve the most efficient and cost-opimized result in your production. One of these combination possibilities – processobserver with plasmoeye – with deep learning for the welding of battery cells incl. integration in the reworking concept is ready to be implemented by e.g. battery manufacturers. Our solutions are successfully in use not only in the field of e-mobility in battery production, but in additive production – both for monitoring powder bed fusion and for direct energy deposition processes. Plasmo’s customers are automotive suppliers, steel manufacturer, aviation and shipping industry, machine engineering and lots more.
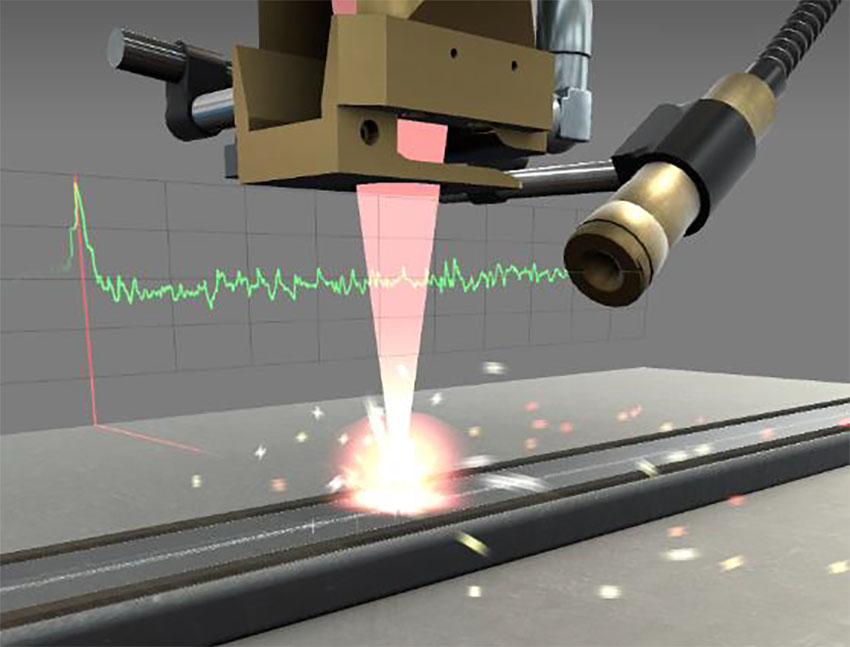
What’s new?
The processobserver series has proven itself over years in large production environments and is used extremely successfully in the automotive sector and other areas where fast, safety-critical applications are part of everybody´s daily business.
The new processobserver generation is now on the market. It provides the following benefits:
Compact Design – with diodebased sensors, the process light is measured by a photodiode. The new sensor is not only convincing due to its compact design, but is also able to measure optical radiation in various wavelength ranges with high resolution and low noise.
High Inspection Speed – with the specially developed amplifier electronics and a measuring frequency of up to 250,000 samples per second, monitoring high speed applications such as battery welding in the electromobility sector is no longer a problem. The welding of extremely short seams with high cycle times and the highest quality requirements is monitored.
Flexible Optical Integration – there are several ways in which the optical radiation can be guided from the process to the sensor: With “off-axis” integration, the process is observed from a lateral perspective. On-axis”, the process is observed directly via the beam path of the laser, or the sensor is integrated directly into the processing laser. Different integration methods can be combined easily to provide a maximum of process data and control.
Scalability – multiple sensors can be integrated via Ethernet into a sensor network, making the system very scalable. Sampling rate, sensitivity and a number of other parameters can also be adapted to the respective application.
The plasmoeye is a very flexible, camera-based system, which can be used to observe and document (without system intervention) and/or monitor and control (interactively).
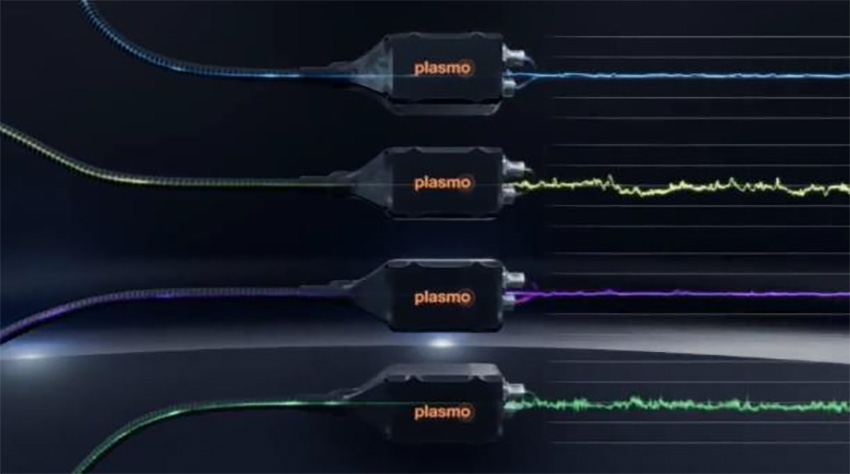
Typically, this application is used to monitor welding and additive manufacturing processes, but it can also be used in any other application where a video or photo of a workpiece or geometrically detectable variables are interesting. The plasmoeye helps to understand what happened and how future defects can be avoided (root cause analysis), so that downtimes are avoided or shortened.
The camera based plasmo profileobserver is primarily used for the detection, measurement and documentation of geometric/surface defects, e.g. a weld seam, solder seam and other geometric profiles. Another field of application is gap measurement/zero gap.
It´s important that the smallest pores are quickly detected, evaluated and visualized. This ensures that only components that meet the company’s quality specifications are transported to the subsequent production areas. The quality inspection is carried out continuously, contact-free and non-destructively. Thanks to the large data memory and plasmo dashboards, reports, statistics and trend analyses can reviewed individually. Irregularities of
The profileobserver is suitable for a variety of applications and offers a constant detection of smallest defects at high process speed due to its in-line triangulation measuring method. Due to the high resolution, large inspection fields can be inspected with a remarkable processing speed of up to 30kHz. In the field of gap measurement/seam finding, the profileobserver enables the detection of the technical zero gap.
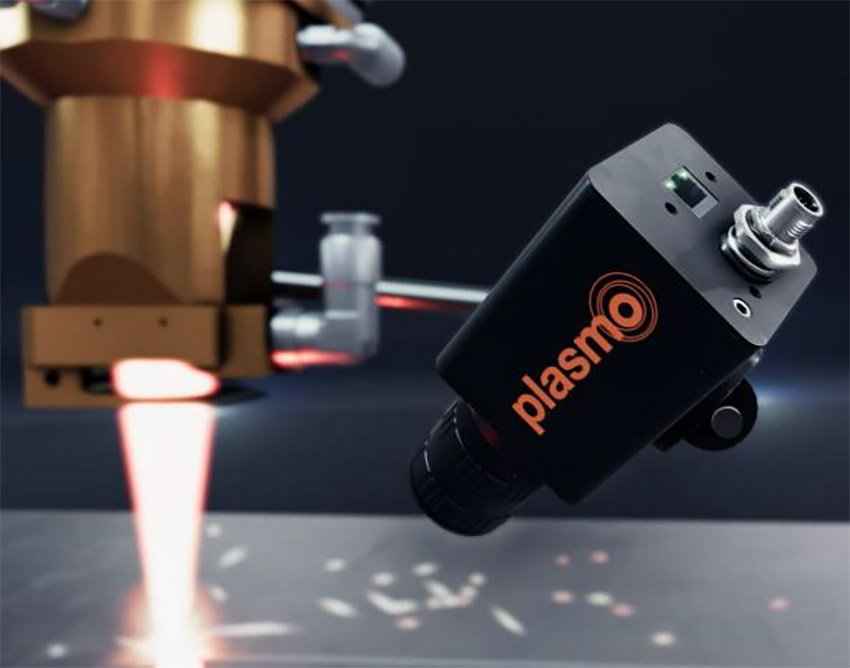
As a combination, the system can be used simultaneously for seam detection (pre process/”joint”) as well as for seam surface inspection or surface analysis (post process/”bead”) – and all this with one and the same hardware! The seam tracking is detected during the first pass (pre-process), and the surface analysis is carried out on the return path.
The focus of plasmo and its products is primarily on the production market. This market has been developing steadily for years. However, the branches within the market that are relevant for plasmo are at different stages. Either quality monitoring systems are already used in large quantities in an automated manner or the monitoring is still carried out completely manually. In the branches with high acceptance, the customers are aware of the technological as well as commercial advantages. On the one hand, production lines are highly automated and produce quantities in the range of several 100,000 – 1 million components per year. On the other hand, defects must be detected that cannot be detected with manual controls. Manual inspection is therefore often not economically reasonable or technologically possible. If the components are also safety-relevant, the manufacturers have to prove for several years that the products were completely free of defects on delivery. All relevant component and process information is also stored by the monitoring systems and transferred fully automatically to designated servers for long-term data storage. Success in these industries often is based on the fact that the development of monitoring systems in these sectors was very closely linked to the development of the process technologies used.
New trends within the production market, on the other hand, are appearing above all in industries that have previously used very few automated monitoring systems. These trends are triggered by the new and further development of monitoring systems. The systems are becoming increasingly simple to install and operate, making their use in conventional and more price-sensitive production more and more interesting from an economic perspective. Technological developments make it possible to monitor processes that were previously considered unmonitorable. Weldings with welding times in the range of a few milliseconds can thus be monitored without any problems. Even high-speed joining processes with process speeds of 1m/s and higher no longer present any challenges. These different industries offer an enormous development potential within the market and completely new areas of application for automated monitoring systems.

The innovations within the market with its branches are naturally based on the further development of the individual systems and the associated new areas of application. An increasingly important factor, however, is the interaction and networking of the systems with each other. The goal of future-oriented production is to detect errors before they happen. To achieve this, it is no longer sufficient to quickly detect the error during the individual process step. Because then the error has already happened. Instead, plant-specific parameters and information should be transferred to the system for evaluation before the actual production process. Such parameters could be, for example, axis positions, position information of the components to be joined, feedback signals from clamping devices and protective gas supply systems. Any information and values that are available in digital form can be transferred to the process monitoring system before the process starts. If all boundary conditions are within the defined standard, the process is started. A pioneer in this field is the new generation of plasmo evaluation software V6 of the processobserver. This software is able to record, analyze and evaluate freely definable, additional data.
These data now provide the basic framework for the next step, the Machine Learning. The systems now try to predict independently on the basis of the collected data what will happen and how this can be optimized or, in the case of an error, prevented prematurely. These systems are currently under development and represent the next step in the field of monitoring systems.
Additional to this, our concept for AM-DED, which has been praised by the community and the market, taking into account user maturity levels, faster time to market and safe investments – all absolute trend topics!
With over 850 plasmo systems in operation worldwide, the growing list of clients includes top international companies established in different industries. Various automobile manufacturers as well as companies in the steel or other industries trust in quality assurance solutions of plasmo. Thanks to this customer base and consistent further development, plasmo will be able to supply the new branches with its new applications just as successfully as before.