Rimatem® is a German market-leading system provider in the field of modular masonry construction with orders national and international. The company developed out of a construction company and prefabrication plant for concrete walls and ceilings with the idea of also prefabricating walls of all kinds of masonry blocks in the factory. Thus, Rimatem® started with the development and selling of the semi-automatic machine HA for the production of masonry walls in the factory, which was continuously optimised and further developed up to the most flexible machine type HA4. There is also an ongoing production at their own site, so that there is a direct link to practice and processes as well as components are constantly being further improved through feedback from workers.
With the fully automatic machine VA, a machine type with highly automated technology and a daily output up to 1500 m² exist, too. The robot automatic machine RA as a modular, scalable solution is the latest development which extends the performance spectrum.
According to the individual requirements walls up to 12 m long and 4 m high made of aerated concrete, lightweight concrete, concrete blocks but also bricks as well as sand-lime bricks can be automatically mortared or glued in wall thicknesses from 10 to 50 cm on the different machine types. Rimatem®’s customers include not only construction companies but also predominantly stone manufacturers all over the world.
However, the main areas of activity of Rimatem® do not only offer wall and efficient transport systems. Their offer also includes a wide range of services around the production of modular walls:
From consulting, projection of the production facilities to training of the employees after commissioning of the machine – Rimatem® considers the total process.
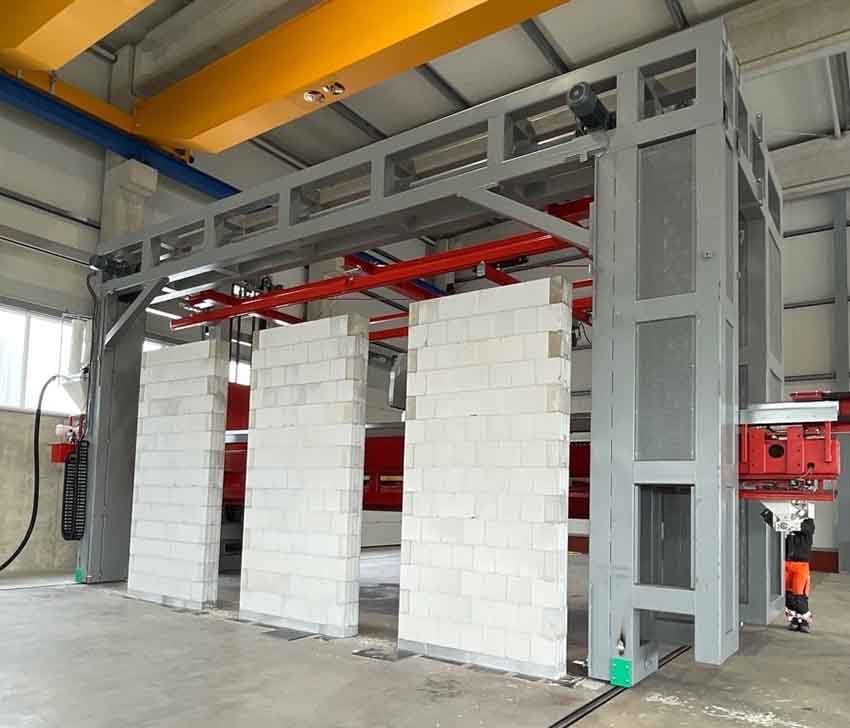
Interview with Nina Häußler, Project Engineer at Rimatem.
Easy Engineering: At what stage is the market where you are currently active?
Nina Häußler: Rising construction costs, increased quality and environmental requirements as well as a shortage of housing and skilled workers are worldwide challenges that the construction industry has to deal with. Unattractive jobs, outdated construction methods and a strong need to catch up in digitalisation characterise the construction industry in a cross-sector comparison. Furthermore, in addition to the lack of workers who are willing to perform such physically demanding work, the type of construction will also be influenced in the future by increasingly cramped conditions on construction sites as well as prevailing price and deadline pressure. For these reasons, factory-based prefabrication of walls made of all kinds of masonry blocks is becoming more and more important. This was also confirmed by the great interest in the Rimatem®-system at Bauma 2022 in Munich.
The current situation in the construction industry is thus also a chance to rethink the current way construction is done and drive innovations.
E.E: What can you tell us about market trends?
N.H: Promoting digitalisation in project handling, integrating BIM-based planning and moving processes from the construction site to the factory are topics that Rimatem® drives forward every day.
According to Rimatem®, working independently of the weather due to consistent climate conditions in the production hall every year, the (protected) storage of the produced masonry in dry conditions and production checks before delivery in particular are potentials that make prefabricated construction more efficient, faster and more precise compared to conventional construction.
Especially nowadays, when sustainability is becoming more important than the years before, the reduction of dirt and noise on construction sites, as well as the elimination of return transports of surplus material leads also to positive (climate-friendly) effects when building with modular walls.
A strong demand from existing as well as new customers is the integration of further production steps, such as electrical installation, window installation or plastering of the raw construction wall, in the factory.
We are already taking these (possible) processes of the future into account when sketch up individual plants for costumers in early phases. Initial practical tests have led to positive results – both in the factory and on the construction site, which is why the trend is clearly moving step by step towards optimized modular masonry walls.
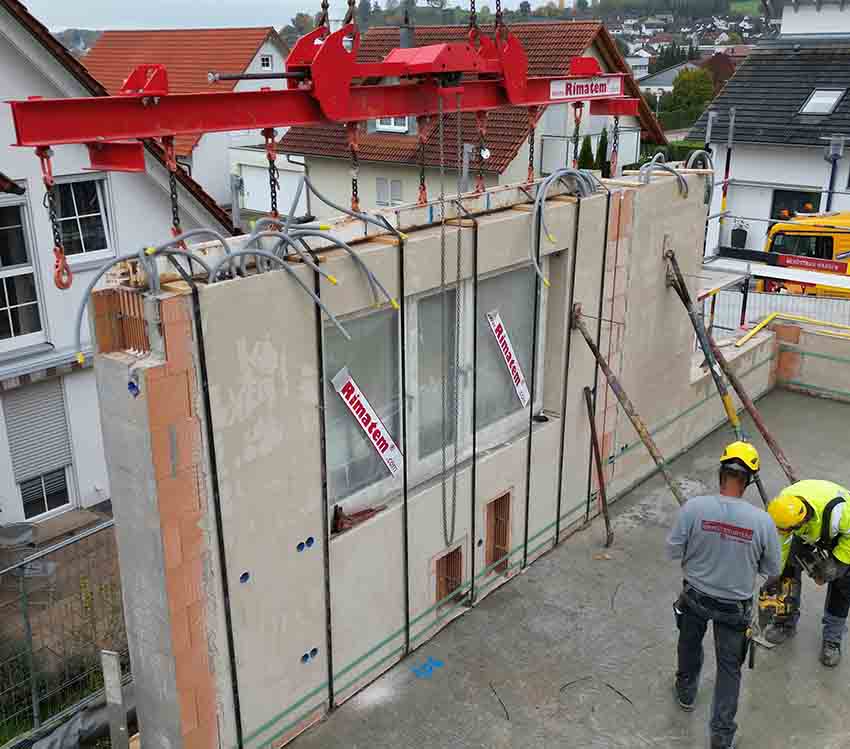
E.E: What estimations do you have for 2023?
N.H: The current construction economic activity is forcing the industry to long-term investments in new, innovative systems. The topic of prefabrication is also increasingly coming to the fore on a political and legal level. We therefore expect continued high demand for our machines as well as services related to modular masonry.
At the same time, we will further develop and optimise our existing systems and digital processes.
“The purest form of madness is to leave everything as it is and still hope that something will change!” [Albert Einstein, German physicist]