As a pioneer in the field of coil winding technology, Schaeffler ELMOTEC STATOMAT is a leading manufacturer of special machines and precision tools for the production of stators. With more than 70 years of experience and an extensive machine and equipment portfolio, the company offers customers innovative and customized manufacturing solutions. Together with a strong partner network, they work daily on the manufacturing solutions for the electric motors of tomorrow.
Easy Engineering: What are the main areas of activity of the company?
Schaeffler ELMOTEC STATOMAT: Our winding equipment is used for stator production in a variety of industries. From vacuum cleaners and pumps to conveyor belts and industrial robots – it is impossible to imagine modern applications without electric motors. Electrified powertrains have also recently become an interesting area of application for our innovative winding technologies. The challenges involved in manufacturing electric motors are just as diverse as the final applications. At Schaeffler ELMOTEC STATOMAT, we have therefore developed a wide range of solutions for the different needs of the individual business areas. Whether the focus is on best efficiency, maximum flexibility, or high output volume, we have a suitable solution for every application.
E.E: What’s the news about new products?
Schaeffler ELMOTEC STATOMAT: Together with our customers and a strong partner network we work on continuous improvements of our winding technology. One example is linear winding technology to produce concentrated windings or single tooth windings. With six parallel spindles and a speed of 1000 turns per minute, cycle times of 25 seconds can be achieved with maximum winding precision. Subsequent pressing of the winding allows the filling factor and therefore efficiency to be significantly increased. Integrated into a fully automated production line, an efficient production of hybrid modules can be realized.
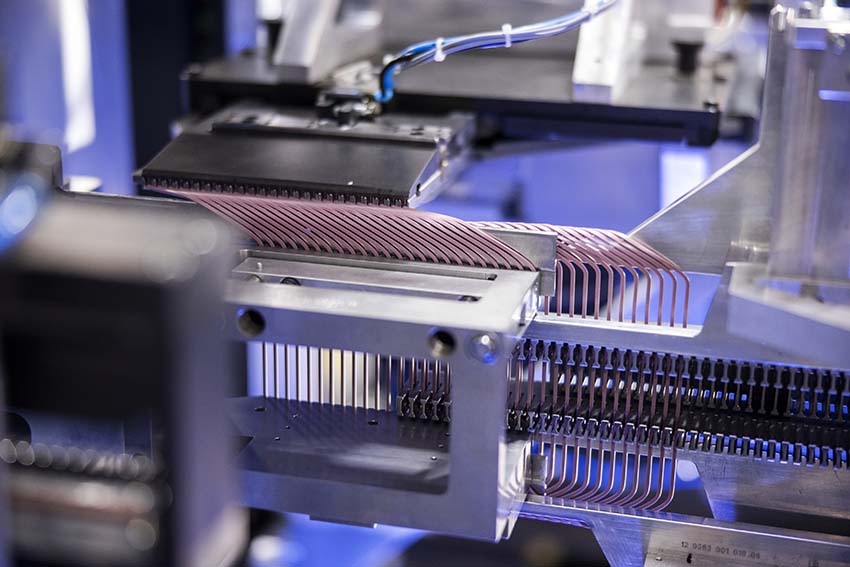
Another innovative example from the field of electromobility is the so-called flat wire wave winding (continuous hairpin). Here, a rectangular wire is continuously wound around a sword to produce a continuous winding mat. This manufacturing process combines the advantages of classic round wire winding technology with the advantageous electrical properties of rectangular wires. Flat wire wave winding allows compact windings to be produced and the required welding points to be reduced to a minimum. The resulting high-power density coupled with high winding quality is ideal for the challenges of e-mobility applications. The first customers for this technology are an American start-up in the field of premium electric vehicles, as well as a manufacturer of electric air cabs.
E.E: What are the ranges of products?
Schaeffler ELMOTEC STATOMAT: The extensive machine portfolio of Schaeffler ELMOTEC STATOMAT covers the core processes for the production of stators. These include the insertion of the slot insulation, the winding and insertion of coils, the forming of the winding, and the subsequent lacing of the final winding heads. Depending on individual customer requirements, we offer single machines, semi-automatic production cells up to fully automatic production lines (turnkey solutions). In our turnkey solutions, we also integrate machines from our partners, such as laser welding of the lead wires, and take over the complete project management. This ranges from design for engineering, design of the winding solutions, assembly of the individual machines and commissioning of the final line in the customer’s plant. With a comprehensive after-sales service offering, Schaeffler ELMOTEC STATOMAT thus accompanies its customers throughout the entire equipment life cycle.
E.E: At what stage is the market where you are currently active?
Schaeffler ELMOTEC STATOMAT: We are currently witnessing high dynamics in our main markets, the traditional customers from the manufacturing industry and the automotive customers. Due to increased raw material costs and energy prices, as well as stricter legal regulations, the demand for energy-efficient and compact electric motors is rising. The increasing shortage of skilled workers further increases the need for automated manufacturing solutions. Although electric motors have been around for over 100 years, we are currently experiencing an exciting phase with many new motor concepts and applications. Electric motors are driving the world. Therefore, we anticipate continuous growth in our core markets.
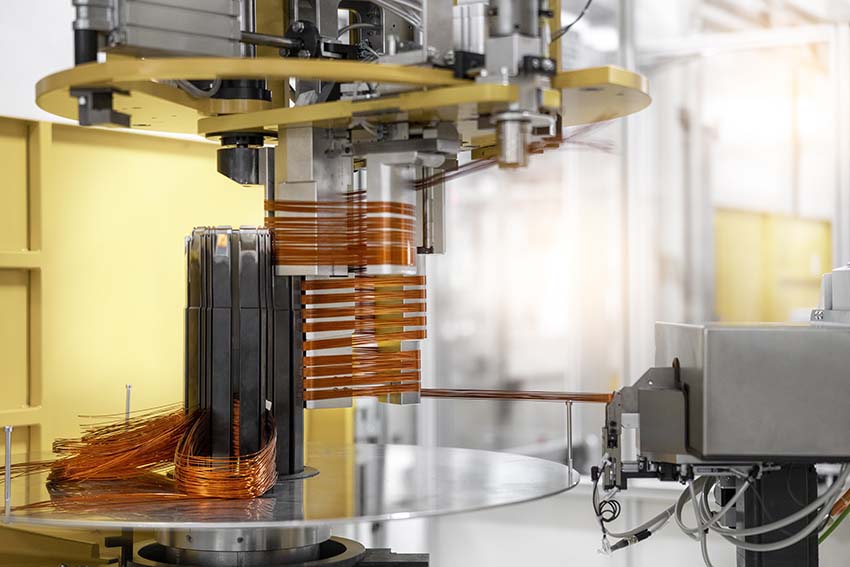
E.E: What can you tell us about market trends?
Schaeffler ELMOTEC STATOMAT: Our customers in industrial production, for example in the field of gear motors, are faced with the challenge of manufacturing increasingly efficient motors. These motors should be even more compact and resource friendly. However, end customers do not want to compromise on quality and price. Schaeffler ELMOTEC STATOMAT offers a twist-free winding method that can wind and insert up to 40 parallel wires. This allows our customers to achieve significantly higher copper fill factors and thus increased motor efficiency. The industry’s requirements are also characterized by increasing automation and maximum flexibility, down to batch size one. This poses a challenge for machine builders like Schaeffler ELMOTEC STATOMAT to develop clever automation solutions and setup concepts. We are currently working with our partners on precisely these solutions.
Specifically in the field of electromobility, we are currently witnessing a multitude of new trends and applications. With our process innovations, we at Schaeffler ELMOTEC STATOMAT actively drive innovation in this area. Together with our customer, we have achieved a high-speed concept through the flat wire wave winding technology (continuous hairpin), setting a new benchmark in power density. The high power density results in minimal space requirements for the drive unit. This not only enables a high electric range but also opens up entirely new design concepts for interior space utilization. The flat wire wave winding also offers the significant advantage that, compared to the conventional hairpin technology, the number of welding points can be reduced to a minimum. This drastically reduces the motor’s probability of failure. With maximum power density and high reliability, this technology is particularly exciting for aviation applications such as air caps. Using multiple winding mats in one stator package, enables a redundancy that is significantly enhancing safety. Furthermore, we see a growing demand for electric motors that do not require magnets in the rotor. In these motors, the magnetic field is generated by a rotor wound with copper coils. Specifically for this application, we are currently developing a modular winding concept that allows for a high variety of rotor options and at the same time a high production volume.
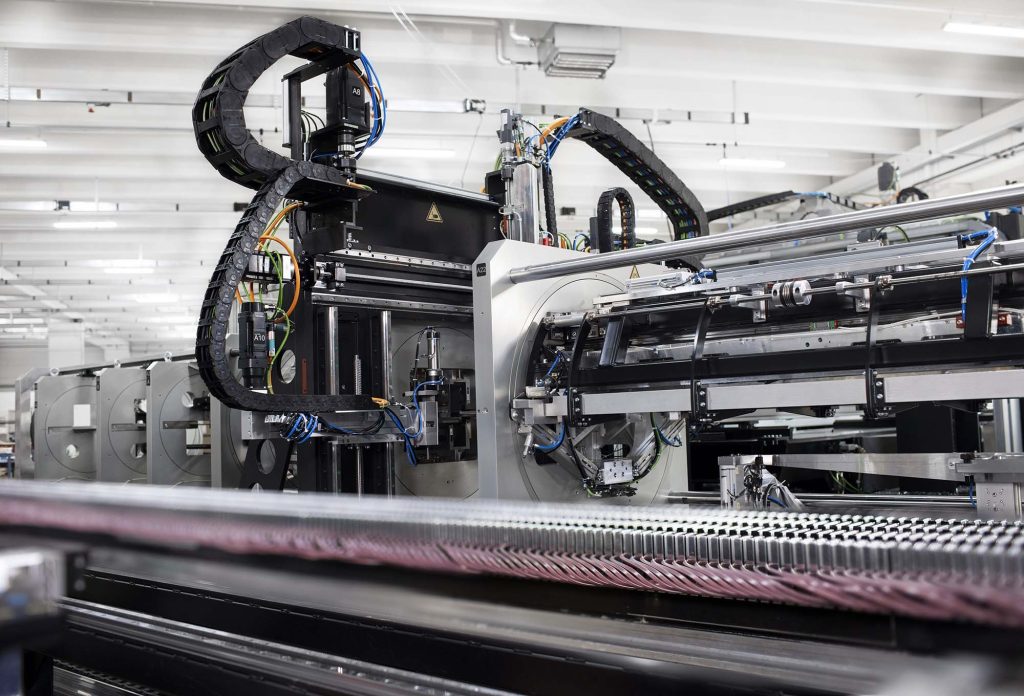
E.E: What are the most innovative products marketed?
Schaeffler ELMOTEC STATOMAT: As mentioned above, our most innovative products include the flat wire wave winding (continuous hairpin), which is also nominated for this year’s “Best of Industry Award,” the linear winding technology for hybrid modules, and the twist-free winding. Schaeffler ELMOTEC STATOMAT’s winding technology has proven itself in serial production for over 70 years. This profound experience in the field of winding technology, coupled with smart automation solutions, makes us a strong industrialization partner!
E.E: What estimations do you have for 2023?
Schaeffler ELMOTEC STATOMAT: After overcoming the COVID pandemic and with significantly more relaxed supply chains, we can feel that our customers are increasingly investing in the future. More than ever, innovation and reliability play a crucial role in this regard. With our precise and flexible winding technologies, as well as a strong partner network for complete automation of the manufacturing process, we look optimistically towards the future and are ready to tackle new challenges together with our customers.