Fresh concrete is often praised for its robust nature but harbors a hidden vulnerability at its core, especially when it’s paired with steel rebars. Since this new concrete possesses a high pH level due to the presence of calcium hydroxide, a protective film is formed between them. However, this protective shield doesn’t hold out for long.
Eventually, carbonation occurs over the concrete layer, and the film dissolves. With the shield compromised, the stage is set for corrosion. This electrochemical phenomenon causes the noble steel to expand up to six times its original size. This expansion exerts immense tensile stress on the surrounding concrete, pushing it beyond its limits. The result is nothing but cracking, spalling, and a visible manifestation of the internal struggle.
One of the most effective lines of defense against corrosion is protective coating. Let’s explore the most common option, fusion-bonded epoxy, in detail.
What is Fusion-Bonded Epoxy?
Back in the 1960s, highway bridge decks were observed to degrade rapidly due to corrosion. Then, in the 1970s, Fusion-bonded epoxy was developed as a solution to protect the steel bars inside these massive concrete structures.
FBE involves an electrostatic method to adhere the epoxy to the steel rebars. First, the rebars are heated to 180 to 250°C and then sprayed with epoxy powder. Once the powder touches the hot bar, it melts, gels down, and eventually cures onto the rebar, resulting in a highly effective protective coating. Since thermosetting is an irreversible process, it helps against the attack of chloride ions on the surface of the rebar and the gradual occurrence of corrosion.
Generally, FBE serves as a physical and electrochemical barrier that keeps the steel safe from oxygen, moisture, and chloride ions. Since the epoxy has high electrical resistance, it cuts off the flow of electrons that can start the process of corrosion. It works as a circuit breaker and even reduces cathodic sites where oxygen needs to be reduced to encourage corrosion.
Looking at fusion-bonded epoxy steel rebars, chloride ions must penetrate the concrete and epoxy. If the epoxy used is of high quality, the ions can take a significant time to travel to the bars, enough to delay the onset of corrosion. The research conducted by the Concrete Reinforcing Steel Institute demonstrates that utilizing fusion-bonded epoxy-coated reinforcement bars remain a financially efficient solution, even when extending the structure’s lifespan by just 1 to 2 years.
What Field Studies Show
Even though FBE has many advantages, it remains a controversial fix. Many research studies show that FBE is a durable solution. For instance, a 35-year field study showed that the epoxy-coated bars remained in excellent condition without any major corrosion.
However, the controversies remain. One of the primary reasons is the field study of the marine bridge substructures in the Florida Keys around the 1980s. After less than a decade of construction, the concrete structures started to spall and crack due to corrosion.
Another example consists of three marine structures in Virginia that were seven years and eight years old at the time of investigation. When specimens of each rebar were observed, it showed signs of debonding, which could occur depending on the moisture conditions, the temperature of the concrete, and the initial coating defects of the epoxy.
Several other field cases from New York and Pennsylvania bridges showed weakened adherence in a span of 6 to 10 years.
Surprisingly, most of the cracks and defects weren’t due to the passing of time but were actually associated with careless transportation, handling, and installation of the product. The demand for better adhesion resulting in a more durable coating can be met with significant improvement to the heating and adhering process.
How to Improve FBE Longevity?
As mentioned earlier, the FBE process can be improved by curating the right conditions before the adhering process and using the right amount of heat.
In general, constructing with epoxy-coated rebars can be more effective with proper handling inspection and fulfilling the requirements. Once the requirements are made known and thoroughly checked, the process can take place seamlessly.
The epoxy that sticks to the rebars should have the following few qualities for an increase in longevity:
- Effective cohesion to the surface
- Chemical and mechanical resistance capable of enduring all temperatures throughout changing seasons.
- Strong mechanical impact strength
- Resistant to aggressive chemicals
Common Challenges And How To Get Past Them?
The following are some common issues while using FBE Coating:
Curing Conditions
Coating defects may result from temperature and timing variations. For optimal coating performance, monitoring and regulating the curing process parameters is essential.
ThermESC International has developed the Fusion® series of induction heating technology. This advanced technology utilizes precision induction heating, material handling, and process controls that ensure optimal curing conditions are maintained therefore optimal FBE durability is achieved.

Achieving The Desired Coating Thickness
The powder particle size and pipeline architecture can have an impact on the coating thickness, depending on the method used for coating application. Overcoming this difficulty can be aided by operator training and proper equipment configuration.
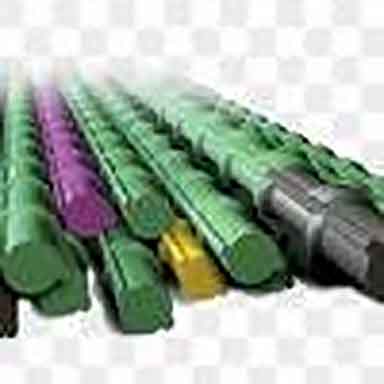
Ensuring Adequate Surface Preparation
The effectiveness of the coating may be jeopardized by contaminants on the surface of the rebar and interfere with the coating’s adhesion. To meet this difficulty, a thorough cleaning and appropriate procedure selection for surface preparation are necessary. For rebar coating shot blast machines work well. Companies like, Blastec® – The Industry Leader in Shot Blasting Machines, are producing advanced surface preparation solutions for Epoxy Coated rebar manufacturing.
Maintenance And Longevity
Here are some FBE coating maintenance tips:
- It is imperative to adhere to appropriate maintenance procedures following the application of FBE coating to guarantee durability.
- Regular inspections are necessary to find any damage or flaws in the coating. If there are any flaws, you should fix them right away to stop corrosion.
Using the Right Equipment in the manufacturing and handling of FBE coated rebar:
To keep the Fusion Bonded Epoxy coating undamaged, you must adhere to recommended handling and transit procedures. This includes keeping the coating safe during storage and transit, avoiding sharp objects, and utilizing the proper lifting and rigging equipment.
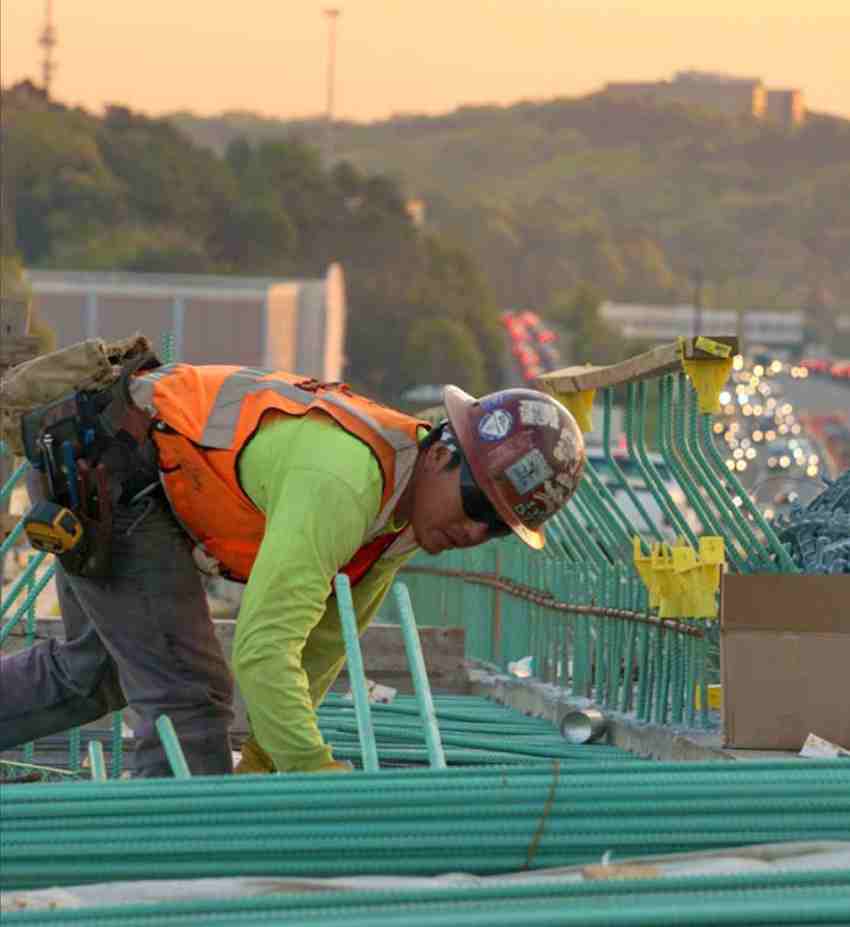
Conclusion
Fusion-bonded epoxy is the most economical solution to protect the steel bars from corrosion when used inside concrete. Following Concrete Reinforcing Steel Institute’s process and handling guidelines combined with utilizing the advanced technologies available for precise cleaning, Blastec® – The Industry Leader in Shot Blasting Machines, and heating, ThermESC, of the rebar prior to applying the epoxy will substantially improve the adhesion lifetime of epoxy used in FBE. This is essential in reducing maintenance costs and cutting down on maintenance and repairs on the structures in which it is used. Advances in the manufacturing and handling of FBE rebar has made FBE the most used defense against rebar corrosion. To uplevel your rebar coating line’s production performance, quality, and effectiveness give ThermESC a call today.
For more information or to get a quote, give us a call at 970-483-5232 or visit our website and check out the fusion series.