A crane at rest is a costly crane. A crane that is not moving as fast as it safely can, for as long as it safely can, is costly too: it’s not making as much return on the capital used to build it as it could. Port operators know that anything that keeps cranes moving contributes to the throughput of their terminals and hence their profitability. Anything that slows or stops cranes moving does the opposite: throughput falls while capital equipment lies idle, depreciating as operators watch.
The challenge for port operators is two- fold. The first is that the nature of their business is to move large masses quickly in a challenging operating environment. The second is that some of the equipment used in such environments has intrinsic features that make it vulnerable to the effects of rough handling. The combination of these challenges can lead to unscheduled stoppages for repairs, as well as requiring the implementation of scheduled maintenance programs. And that’s costly.
For example, a modern crane mounts its lifting mechanism on a trolley that runs on rails fixed to a gantry mounted up to 60m above ground level. The gantry has a hinged boom that can be swung up, out of the way, when ships are docking and undocking. When the boom is level, it can extend more than 60m beyond its hinge point to reach containers stacked on the far side of the biggest ships. The crane’s operator sits in a cabin that is mounted to the trolley.
THE ISSUE WITH SHOCK
To allow for the boom to move up and down, a discontinuity in the structure and rail system exists. The intrinsic issue with this set-up is that the crane trolley must traverse a discontinuity in the rail at the hinge, where two so-called ‘short rails’ meet, moving at speed while carrying loads of 30 tons or more. The resultant shock, as the trolley crosses the gap, can cause accelerations of up to three times the force of Gravity. This turns the 30-tonne static load of the container into an impulse of considerably higher loads, which must be absorbed by the short rails used on either side of the boom hinge. And if the short rails are not aligned with each other horizontally, the trolley’s transition from one to the other will create large lateral forces as well.
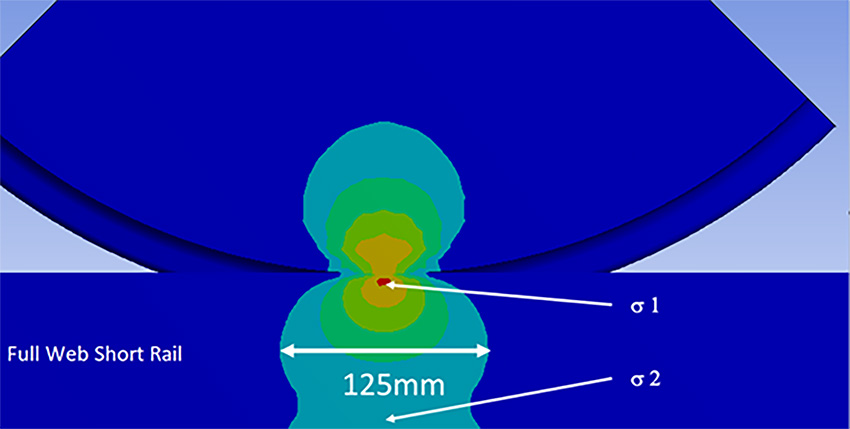
These vertical and horizontal forces can chip the short rail or cause it to deform temporarily. If a lot of material is lost or the deformation is permanent, then the next time a trolley crosses the hinge joint it will experience even greater forces, leading to more chipping and deformation in a feedback loop that can end in rail failure. The regular shocks created by the trolley crossing the gap at the hinge joint and the subsequent vibrations can affect the rail welds, crane structure and any embedded electronics on both the crane and the trolley. The same shocks and vibrations also cause rail clips and hold-down bolts to loosen over time. This creates a health and safety issue if such fixings fall off the gantry the next time the boom is lifted.
The short rails bear the direct impact of the trolley’s passing, but that impulse is then dissipated in the rest of the crane’s structure as small elastic deformations, as well as vibration and noise. Each of these has its own effects, on everything from the tightness of bolts and the position of sensors to the operating lifetime of any electronic equipment mounted in the operator’s cabin.
Such regular shocks also have a profound effect on operators, who may be expected to move up to 30 containers per hour during shifts of up to 12 hours. Each time the trolley crosses the discontinuity in the trolley rails at the gantry’s hinge joint, they are subject to shock, vibration, and noise. This can cause operators to suffer health issues such as back pain. The cumulative effect of these repetitive shocks may also undermine operators’ confidence in their safety and hence break their concentration. This can reduce their performance, especially on long shifts, as they slow the movement of the crane to reduce the number and magnitude of the shocks. And as we said at the start, slow cranes are costly.
RESPONDING TO THE PROBLEM
The obvious response to this issue is to mount short rails, made of high-grade steel, on a damping material, so that the impulse created by the trolley passing over the hinge can be absorbed and dissipated.
Unfortunately, such solution which is recommended on the rest of the track doesn’t resist to the severe mechanical constraints created by the rail discontinuity at hinge. The material just will not stay in place under the rail when subject to repetitive shock.

Our response, formulated by the Gantrex R&D team, has been to develop a patented technique in which we constrain a shock-absorbing elastomeric material within a U-shaped channel along the length of the short rail. This stops the material migrating under load and so retains its integrity over its designed operating lifetime of two million container moves. The Gantrex HingeGuardTM short rails have already been installed on several cranes around the world with more cranes pending installation in 2022/2023.
To ensure the robustness of the product we have invested in an extensive design effort, including multiple prototypes cyclic testing under severe loading conditions, and many FEA simulations. We have also completed vibration analysis on site, which has showed that when compared to a standard short rail, the Gantrex HingeGuardTM short rail reduces the impulse caused by a trolley crossing a hinge gap by 80%, and reduces the subsequent vibration by 30%. You can see why it works in the figures below.
The Gantrex HingeGuardTM short rail is one of a set of components that make up the overall impulse and vibration reduction system. Others include clamps that exert a powerful vertical force clamping the base block to the structure, shear blocks that stop the rail moving longitudinally, and clips that can be adjusted in situ to keep short rails in alignment with each other across the hinge gap. This reduces the likelihood of large lateral forces being exerted on the rail.
The technology may be impressive, but what value does it offer terminal operators? Reaching for the back of a virtual envelope, if we say that it costs $100 to move a container, a good crane operator moves 30 containers an hour, and assuming cranes run at 70% utilization over 24 hours, then a crane can earn, or give up, $50,000 of revenue per day. Currently, a crane may need one or two short-rail replacements during the approximate ten-year lifetime of the long rails that forms the rest of the trolley track on the gantry. If each replacement takes five days, then the cost of short-rail wear is $250,000 to $500,000 per long-rail lifetime. Across a terminal with 20 cranes, that’s between $500,000 and $1m per year in lost revenue.

If the extended lifetime of the Gantrex HingeGuardTM short rails enables operators to replace them at the same service intervals as the long rails, all that revenue can be recouped. The reduction in shock, vibration and noise should also improve operators’ health and safety, giving them the confidence to sustain their throughput and hence the terminal’s profitability. In the end, it all goes back to efficient capital utilization and the fact that a crane at rest is a costly crane.
ABOUT THE AUTHOR
Dr Nicolas Dinter, Group Innovation Manager, Gantrex, is an experienced R&D professional and start-up facilitator. He began his career studying material properties, and later launched an incubator for mobility businesses. He was the driving force behind the Gantrex HingeGuard™ short rail development and testing. Nicolas has an engineering degree, a PhD and an MBA.
ABOUT THE ORGANISATION
Gantrex is the global market leader in the production, distribution, installation and maintenance of high- quality crane rail solutions. Gantrex’ products are used in many different applications and end-markets including ports, shipyards, steel mills, aluminium smelters, railway depots and heavy industries. Gantrex is an international company with sales and service centers in 20 countries on 5 continents.