Performance, quality, innovative engineering, reliability, expert people, this is what makes the Italian manufacturing the leading global providers of rotary foundation equipment and service in the construction industry. World-renowned for its technological advances, SIP&T is the best solution to reduce costs and keep your project on schedule.
When drillers need to ramp up their capability on deep foundation job, they turn to SIP&T expertise because it makes the difference. Based in the South of Italy, the company has become a leader in drilling tools by working closely with customers. SIP&T knows that contractors are always in a hurry that’s why it offers high performing tools with exact specifications in fast delivery time.
With SIP&T tools the performances are beyond expectations, construction companies can meet large and deep piles efficiently and safely. This type of custom approach has been SIP&T’s stock in trade for decades.
Beginning as a small machine shop and developing technical skills to realize tools that are custom designed, the company was built on one-on-one customer service and precision manufacturing.
Today more than 100 skilled personnel are dedicated to deliver a customer service that make SIP&T a go-to company for kelly bars, casings, all types of rotary tools, CFA augers, Soil Displacement Tools, Tremie Pipes, Stop-End Elements, as well as a host of services that include Kelly/drilling tool rebuilds and a massive stock of spares.
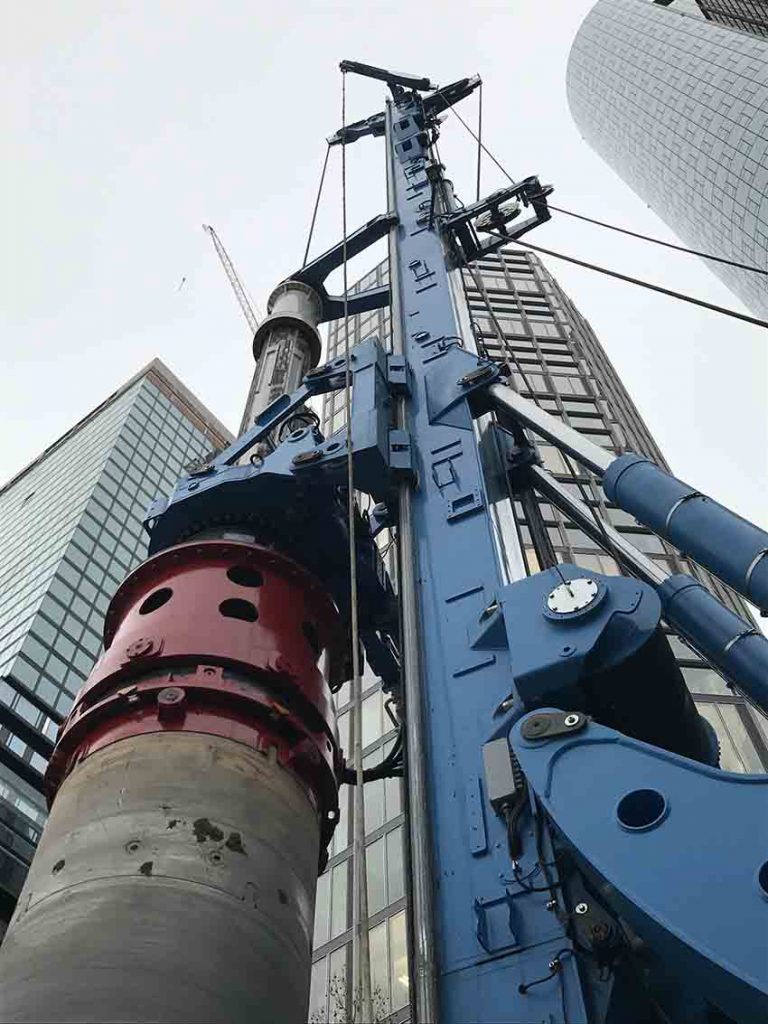
Looking to the future
Thanks to remarkable investments in research and technology and a constant upgrading of the production facilities, the company has extended its potential by becoming a landmark, all the production line is specifically designed and customized to match any drilling rotary torque.
Nowadays SIP&T is framing a new facility close to the existing warehouse that will help the production to reduce the delivery time considerably. The new spaces will also improve
the employee’s quality of work and life and will foster the development of the open innovation model. This is another evidence of the progress and continue growth of the company. In addition, in recent years, SIP&T has taken another step forward – a defining moment in its growth – several original equipment manufacturer (OEM) agreements have been signed with some of the biggest players in the field. A strategic milestone that enabled the company to grow fast offering a complete range of high-quality products and service to all drilling industry operators.
Must have
There are many recent innovations that underline the understanding at the core of SIP&T’s success. However, the design of the automatic casing drive adaptor (AUTO CDA) and special progressive rock auger (PRA-S line) spotlight the SIP&T’s unique capabilities. The company’s core business is, without any doubt, Kelly bar production. Understanding customer requests, analyzing reports from the different construction sites where SIP&T Kelly bars are used, studying their performance in geologically challenging soil strata and checking their output, the company decided to enrich and develop the know-how by introducing the Finite Element Method (FEM) for each Kelly bar. Designing Kelly bars is essentially a repetitive process: a concept is developed, feasibility analysis is started, drawings are produced, prototypes are built and tested, the results are evaluated and the process repeats until the right version is consolidated. FEM analysis is fundamental in facing and solving the challenges that come up during the various product development stages. SIP&T has gained enormous benefits from implementing this analysis into its production process; in detail, the variety of materials used to build Kelly bars has been increased, optimized weight, thickness and shape, reduced testing time and consequentially the time-to-market.
However, the greatest advantage is in the Kelly bar production stage, during whom SIP&T team noted a considerable reduction in the weight of the applied materials and its waste, reduced production times and, at the same time, increased production capacity and energy efficiency. From a commercial point of view, the company has recorded a remarkable increase in demand and price-quality ratio by differentiating the product.
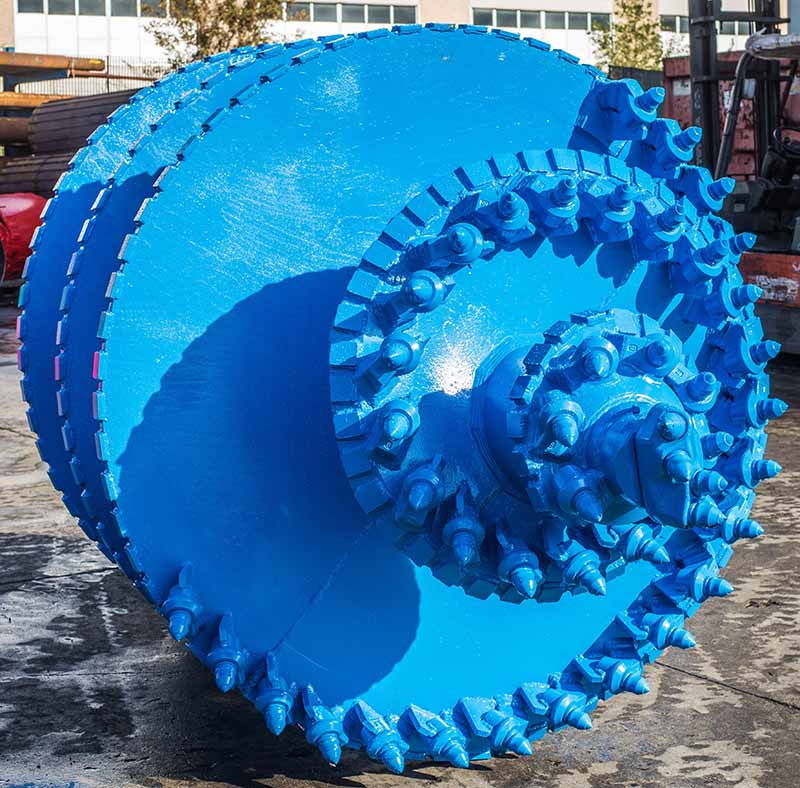
The outstanding feedback from construction sites have confirmed improvements in Kelly bar behaviour and have, therefore, strengthened customer loyalty. The number and types of Kelly bars on the market have been increased, almost completely eliminating the cost and number of Kelly bar returns due to breakage or design flaws. All these above issues allow to fast (two-three weeks) supply the final user with the finished equipment, built in accordance with the drill torque and the project features of the pile to drill.
To date, SIP&T designs and produces the right Kelly bar compatible with the related rotary head for all major drill brands and models.
The torque range to keep in mind is vast and goes from a minimum of 40 kNm to a maximum of 480 kNm; the maximum reachable depth is up to 100 m. All Kelly bars can optionally be supplied with a sound damping system. It consists in sound absorbing pads which are glued into the recesses between the drive keys and the outer surface of the kelly outer section. The pads are protected against mechanical damage by metal sheeting. The system mainly reduces disturbing high frequency sound emissions that are generated primarily by jerky kelly movements and amplified by the hollow Kelly sections. The sound damping system can also be fitted to existing kelly bars retrospectively.
The AUTO CDA has been designed and built internally and entirely by the company, it is applied to the casing that SIP&T itself manufactures and is compatible with all the casings produced by other companies. It is an automatic casing connector system that can be used with any type of piling rig and its maximum advantage is the ability to increase both safety and productivity in foundation works, eliminating both the related dangers and the huge amount of time necessary for the jointing of the casing pipes that until now was often performed manually.
The casings are made of high quality steel and are proposed for the construction of foundation works in soils that require the covering of the hole, intended to be drilled, which otherwise could collapse. The Auto CDA performs by a mechanical locking/ unlocking system of the two male/ female joints generally positioned at the extreme of two casing pipes, which must be coupled or used, as said earlier, on any model of drilling machine, also of large torque. The system is directly controllable from the rig cabin and all the manual operations carried out so far by the site personnel can become a distant memory, with undisputed advantages both for the safety and for the casing arrangements and the piling rig itself.
The PRA-S Line has been designed to handle the most difficult drilling conditions, this auger is the evolution result of years of drilling experience; it has been studied to work in very hard rock strata having a Compressive Strength more than 100 MPa.
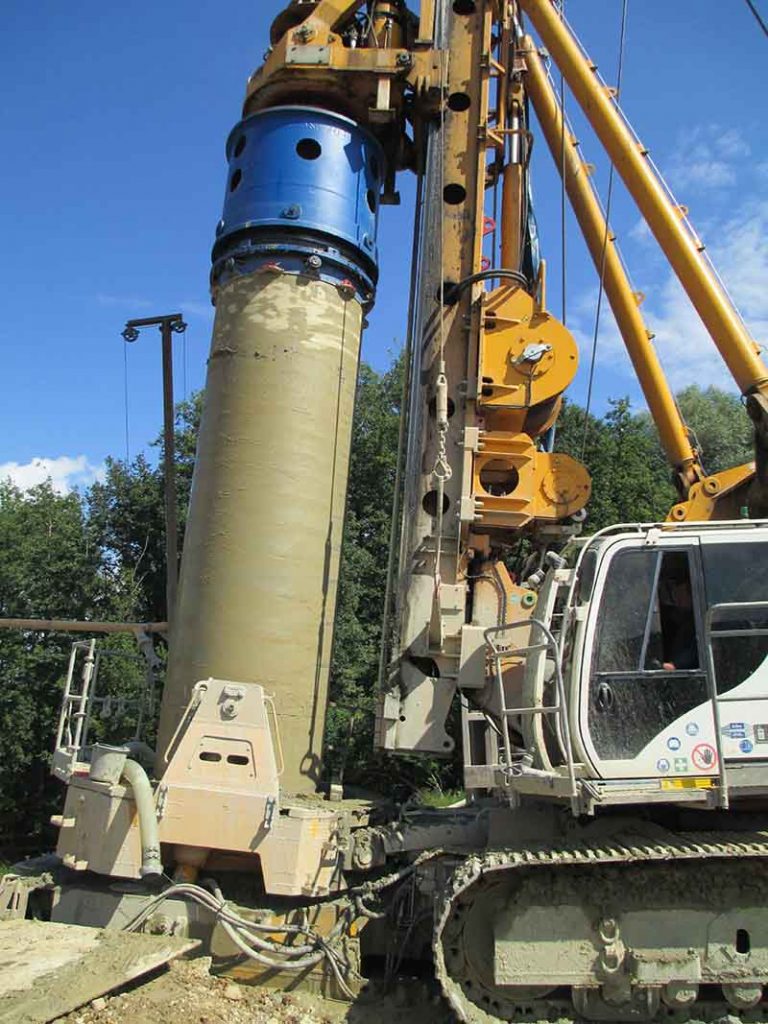
The geometry of the chisels arrangement is optimized for reaching excellent cutting performance, the flights pitch has been specifically designed to get better output characteristics for the high torque drilling rigs in order to improve material handling. Auger main features are:
– High and fast drilling capacity – optimized cutting geometry yields fast drilling rates, due to its flight, which increases in diameter progressively, and its special chisels and holders, this auger displays excellent ripping characteristics.
– Low and easy maintenance – replaceable strips having HB 600 are highly wear resistant while the special setting angle allows the Betek (we use only that!) round shank chisels to sharpen themselves as they turn.
High operational reliability – quality and design that come with 25 years of experience in the design and production of rotary drilling tools.
In conclusion, rock drilling for piling applications using conventional drill tools is usually limited to rock strengths of 100MPa compressive strength (UCS) or less.
The PRA-S Line presents an alternative hard rock drilling method which is suitable to penetrate rock when conventional drill tools become either ineffective or reach refusal. Over the last year, many piling contractors are excavating linear meters of extremely high strength rock in excess of 200MPa compressive strength (UCS) using innovatively designed and built PRA-S Line. This special auger is achieving up to ten times faster production rates than conventional drilling tools and up to four times faster production rates than air roller core barrels in similar rock formations and are therefore attractive options for hard rock drilling requirements for bored piles.
SIP&T s.p.a.
Via Giovanni Agnelli n.6, Zona PIP, 84981 Baronissi (SA) – Italy
Tel: +39 089.9566338
info@sipdrill.it