STADLER designs and builds turnkey plants for the waste recycling market. The company delivers a complete package – starting with the planning and creation of the flow diagram, through project planning to complete assembly and commissioning. STADLER develops plants for the processing of waste such as MSW, lightweight packaging, plastic bottles, paper and cardboard, commercial waste, mixed construction materials and bulky waste, and the recovery of the recyclable materials they contain.
In addition to its activities as a supplier of complete plants, STADLER also develops and produces a large part of the conveyor technology used, steel structures, walkways, electrical installation and specific sorting machines such as screening drums, ballistic separators and label removers.
Easy Engineering: What was the research behind the products/solutions design?
STADLER: The central point of research and development is the goal of building recycling plants that convince with high sorting quality and at the same time are characterised by high availability through maximum uptime. This can only be achieved if both the complete plant layout and each individual unit meet the requirements.
For this reason, research and development always consist of the complete plant layouts and the improvement of individual machines. This is particularly important in waste recycling, where the enormous variability of the waste to be processed is a big issue. Each plant and each unit must be able to cope with a wide range of possible input materials and still deliver high efficiency and robustness.

E.E: Which are the key aspects of the process of product/solution development?
STADLER: Feedback from practical experience is particularly important in order to assess the performance of the machines and plants with real waste. Over the years, STADLER has built a large number of plants of various sizes for processing a wide range of waste types, acquiring a wealth of experience in waste recycling.
E.E: How quickly do you adapt your products/solutions to different requirements?
STADLER: With our practical experience, we are constantly developing our machines and plant layouts further. A new plant always incorporates the experience gained from projects already implemented and the customer’s experience as a plant operator.
As a result, our standard units are gradually adapted and further developed through a combination of many years of experience and current market requirements.
In the same way, the flow diagrams and layouts of the complete plants are adapted to the constant changes in waste management in various countries and regions.
Within the design and development department, we also employ our own team, who works specifically on optimising the material flows in the plants and can therefore deliver their findings quickly.
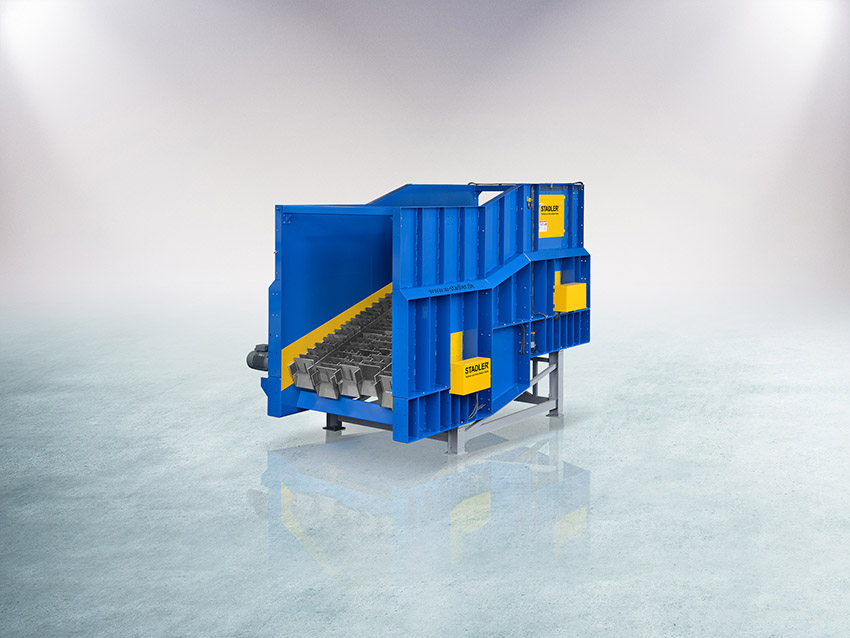
E.E: What are the most common requirements from clients?
STADLER: Regardless of the size of the plants and the waste to be processed, maximum sorting quality with the greatest possible plant availability is always required. This requires good planning of the arrangement of the sorting units to ensure the right recyclables are sorted at the right place. This is combined with the simplest possible plant cleaning and maintenance in order to keep costs and downtime as low as possible.
E.E: How do your products/solutions solve problems that your clients may have?
STADLER: In the construction of our machines, we pay special attention to robustness. A standardised modular system for the individual units helps us to meet the requirements of the customer and the waste to be processed as precisely as possible without losing the advantages of fast and cost-effective production. Each of our options and variants of the individual units has been tested through use in previous projects. For example, depending on the waste to be processed, we offer different ballistic separators that are optimally matched to their application by their design, or the customer can choose between different belt qualities.
Depending on the requirements for the sorting result and the infeed material, each plant is optimally assembled with regard to the arrangement of the units.
E.E: Tell us about products/solutions innovation.
STADLER: The waste recycling industry is driven by a multitude of changes. On the one hand, there is a large number of different markets with a wide variety of requirements and raw material availability. On the other hand, legal requirements for recycling play a major role. For example, in future, this will drive a significant increase in the importance of the recycling of construction waste in Europe. In addition, the composition of the various waste streams is subject to constant change. New packaging materials are constantly presenting the industry with new challenges.
STADLER is continuously working on new ways to meet these requirements, from the individual machine to the entire recycling plant; from small adjustments to the machines or processes to the implementation of new technologies to handle new waste streams or sort new, challenging material compositions.

E.E: What are the trends in product/solution design in your area of activity?
STADLER: At the complete plant level, the trend is towards larger and more flexible plants. In order to maintain an overview here, effective and continuous monitoring of the material flows and sorting results by means of sensors is indispensable.
Sensor-based monitoring of the machine data of the individual units is useful for maintenance and for assessing the system’s overall function.
In any case, storing the data in a database and displaying it intelligently is an important step for the future. On the one hand, it helps us to further improve our plants, and on the other hand, it gives the plant operator a full overview of the processes in his plant and their condition at all times.
Furthermore, increasingly automated sorting processes are being used, some with robot support. The plant concepts also contain increasingly advanced process steps to create new products from the recycled materials, such as the production of new bottles from recycled PET.
E.E: What are your estimations for the rest of the year?
STADLER: We are seeing a growing recycling industry worldwide. This is the only way to reduce environmental pollution and recover important raw materials. STADLER is doing its part with modern and efficient facilities. Despite the Covi-19 pandemic, we are working at full capacity. The development of new markets such as electronic scrap and construction waste recycling will further expand our know-how and help us to continue to improve our plants and products in the future.