Located in Cavaillon, in the south of France, Sterne, member of the Exsto Group, is specialized in design, development and manufacturing of tailormade solutions made from high performance elastomers. Innovation is part of Sterne’s DNA. Silicone is a material full of surprises, that has yet not given all its secrets. This high tech, truly eco-friendly material can be used to make an infinite number of different things! Silicone is a permanent source of innovation. But at Sterne, innovation is not just a product matter. Innovation has always been present in the organization starting with the Quality Management System, that centralizes the processes and the administration.
Easy Engineering: How important is innovation and R&D for actual and future products?
STERNE: We innovate to develop high performance silicone technical solutions. We innovate to prepare tomorrow’s challenges. We innovate for a more responsible future. Innovation at Sterne is a will and a reality. Aiming for a better world is what gives a meaning to our work.
E.E: What are the needs of the users on the markets that you are active?
STERNE: The users’ needs are always more and more demanding. The race for performance and better-quality products is a daily challenge. The global warming issue is also changing the needs to which silicone brings answers. Products made out of high-quality silicone are more durable, thus help reduce rubbish; today the end users are more concerned about the impact on environment at each stage of the life of a product, beginning with their manufacturing. We, at Sterne, are convinced that silicone has a role to play regarding the global warming issue and a more responsible future.
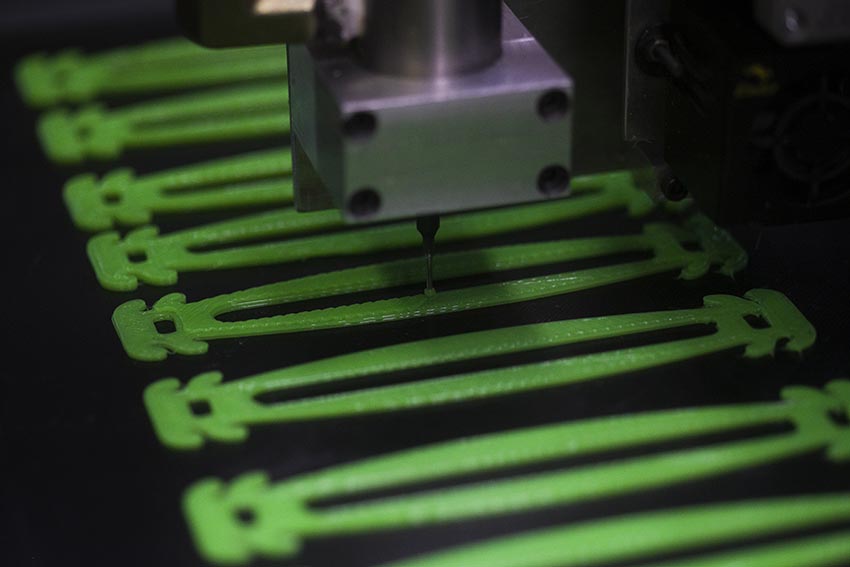
E.E: What products/solutions does your company bring that are the most innovative?
STERNE: Our concerns for a better and more responsible future have led us to develop new transformation processes.
We are able to transform UV-cured silicones. This high potential process has a lot of advantages. It requires less energy than standard transformation process. Indeed, the reticulation happens at a temperature lower than 70°C, and the process itself takes less time. We have made the choice to devote an entire environment to this process. We are able to manufacture products through this process using all our know-how (extrusion, molding, making and 3D printing). In order to answer all the needs, we have developed a panel of specific materials. UV-cured silicones offer high performance properties for high-demanding applications. It is also possible to mold over thermosensitive materials such as plastics or electronic components, which open the scope of possibilities.
Another major innovation we have set up are our 3D silicone printing technologies. Ideal for prototyping and reducing development costs and securing investment as the design loop stages are done upstream, before launching the making of a machined mold. 3D printing is also suitable for unique design need or small series. For instance, to replace a broken piece or produce a tailormade component in small quantities, for which the making of a machined mold would not be cost-effective.
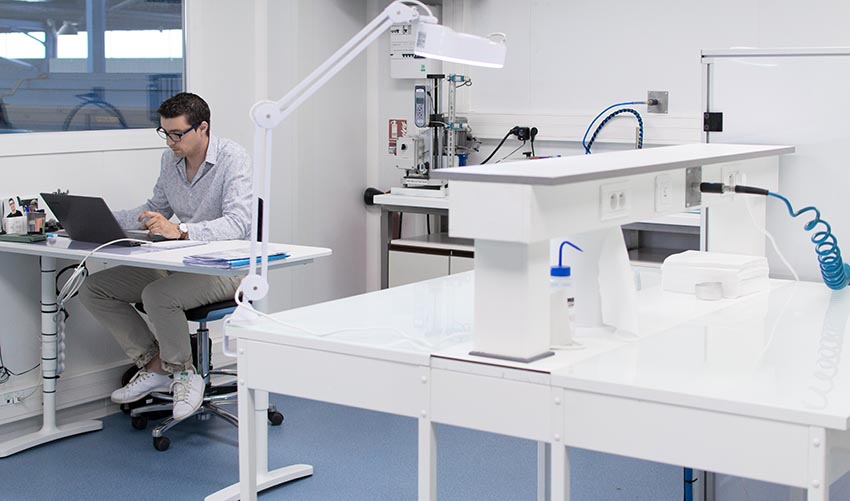
E.E: What are the challenges that users encounter in their line of work?
STERNE: Whatever the area, the challenges are changing at a fast pace. For instance, health research is constantly evolving. The new discoveries in health issues bring up new needs, changes in the legal requirements, thus there is a constant need to adapt, ameliorate existing products or develop new ones … The medical industry has no place for error. Perfection is the only option. In the industry area, performance challenges are also demanding for our customers: safety, traceability, faster production… Users need products they can trust. They rely on our silicone expertise.
E.E: How does innovation help them in these situations?
STERNE: As we develop tailormade solutions, innovation is very important for our customers. It is what makes their project is possible. It is what makes their product is trustable. It is what helps them being more performant, reduce their costs, save energy…
E.E: How is digitalization changing your field of activity?
STERNE: Digitalization is giving us an opportunity to be more performant by bringing a real-time monitoring of the production process, a smoother organization process, more fluid communication between the services, a better traceability of the steps. It helps us being more reactive, minimize the chances of errors, reduce our environmental impact.
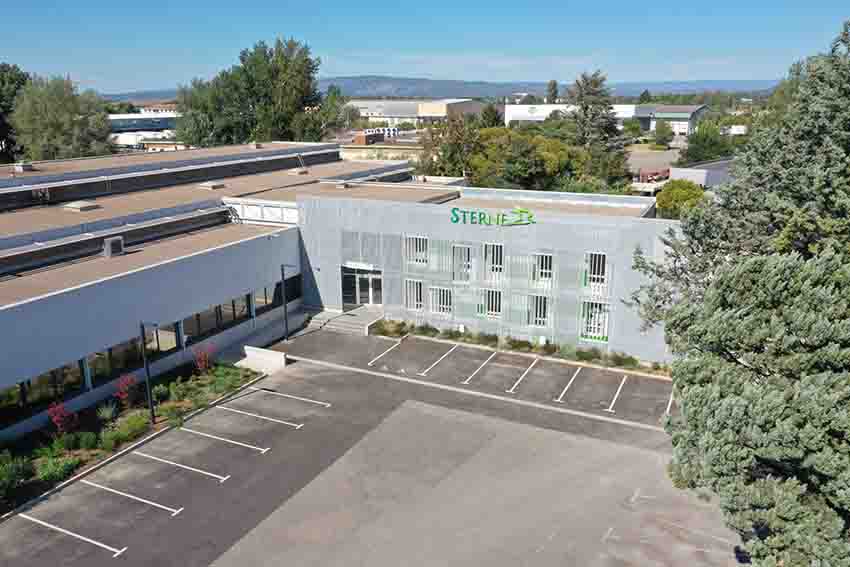
E.E: What tasks/processes can users do easier and more efficient with your products/solutions because of innovation?
STERNE: The choice of the material (silicone) is made because it answers an issue. Every product that we manufacture is an innovation and a part of the global answer to the need of the customer, and of course, contributes to efficiency.
E.E: Tell us some tips & tricks about prevention / maintenance for your products/solutions?
STERNE: We bring our expertise in the silicone matter and manufacturing processes. We are intermediaries. Prevention / maintenance is assured by our customers.
Sterne SAS,
CAVAILLON, France
Mail: contact@sterne-elastomere.com
Phone: +33 (0)432 501 697