Stevia Automation was founded in 2010 in Poland, with the purpose to improve the intralogistics processes and make the logistic operations easier for clients.
Their passion is helping to create and transform the vision and idea of their client into a working system. The company focuses on delivering control systems for intralogistics and automotive sectors. So far, they have successfully completed many worldwide projects.
Stevia Automation’s product – the control system – is created by them from the first concept of the client’s system, through designing, installation and programming to the commissioning. The company also offers technical support after installation. They have gained a lot of experience working at the client’s warehouses and production halls and they are able to provide precise advice when it comes to designing new ideas of the projects.
The company has been providing their services for the leaders of the industry.
Easy Engineering: What are the main areas of activity of the company?
We usually take part in the projects as a subcontractor for control systems. Our company is providing comprehensive control systems for whole installations or single machines from various industry sectors. With skillful staff and many years of experience, we offer complete services. Our scope includes electrical designing, procurement, control cabinets prefabrication with electrical installation on-site, as well as PLC, SCADA and robots programming and commissioning. We are also providing technical consulting services, and technical support for every installed system.
E.E: What’s the news about new products?
For us and our customers, a very useful part of every new project is virtual commissioning, which contributes towards the common success. It allows for viewing and testing the concept of the project before the real-life commissioning phase. It also enables our engineers to improve the created software, which makes their job more efficient. Engineers create the virtual model of the exactly the same system as planned for real-life implementation, so that the mechanical construction as well as its software can be tested.
“The most important feature of virtual commissioning for me is being able to prepare new employees for the work on-site.” – says Igor Pułanecki, our Technical Director – ”It helps a lot with training young engineers, as they can make sure that the program works correctly, and be less stressed before the real-life commissioning. It is beneficial for our clients, too, as they know beforehand that they will be getting the final product well done.”
For the clients, it is a good opportunity to see the test version of the project and its impact on the company’s processes, it also helps the client to point out any elements that need modifications. Using virtual commissioning, we can select the version of the project that fits our customers’ needs the most and make sure that the project is 100% technically correct.
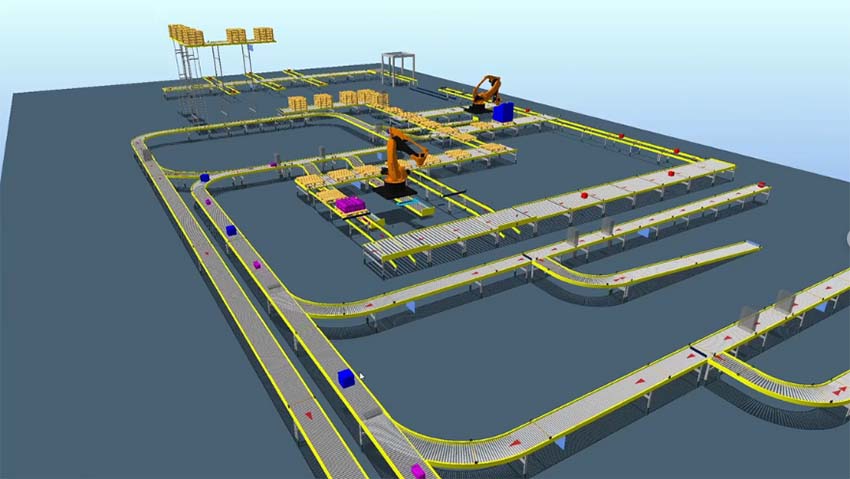
E.E: What are the ranges of products?
We specialize particularly in control systems for intralogistics, the automotive industry, and machines. We mostly concentrate our activities around PLC, SCADA and robots programming; however, our scope includes also preparing EPLAN design of the project, procurement, control cabinets prefabrication connected with electrical installation on site. Additionally, we provide technical and functional consulting when it comes to creating a concept version of the system.
We provide the commissioning of the system’s hardware and software at our client’s location. After that process, we provide assistance in production ramp-up, as well as technical support for the entire system. As we are gaining more and more experience through the years, we look forward to more projects to be completed around the world for any business, thinking about its system automation.
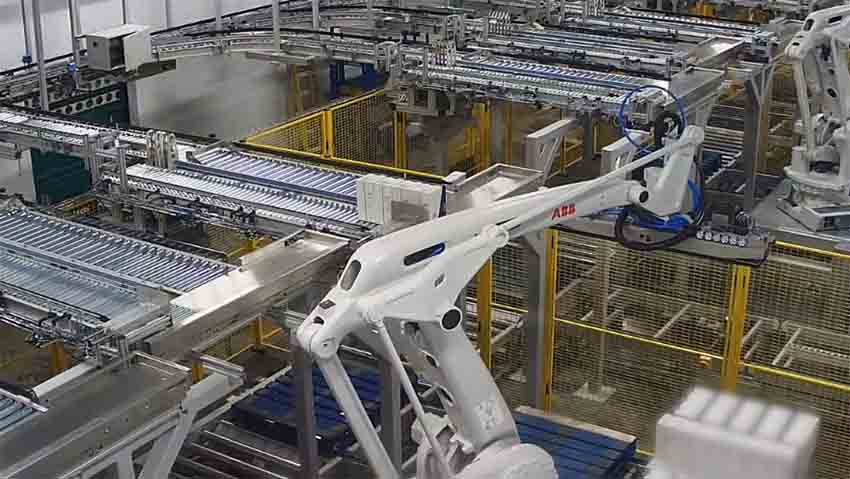
E.E: At what stage is the market where you are currently active?
The branch of intralogistics is still growing, despite the COVID pandemic and unstable political situation in the world. The pandemic caused human behavior change and high e-commerce growth.
The role of human operators in the production and warehouse processes has decreased, which is quite useful in case of such disruption like for example global pandemic or a shortage of workers in the market. “We notice that small companies are starting from single installation elements, like automated sorters or robotic cells.” – states Paweł Wróbel, Managing Director – ”Then, constantly developing, the companies are adding more and more system features. In the next couple of years, the demand for automated warehouse systems will increase in many more countries in the world. There will be more compact, but scalable systems, in order to speed up the process of implementation.”
E.E: What can you tell us about market trends?
The feature that will gain popularity in the next few years is Automation as a Service, which helps smaller companies to implement the automation. The strategy of Automation as a Service works on the principle of outsourcing of automation systems and engineers. That decreases the general cost of investment for the company. It is a big advantage also for companies that are hesitating on the decision to implement an automated system.
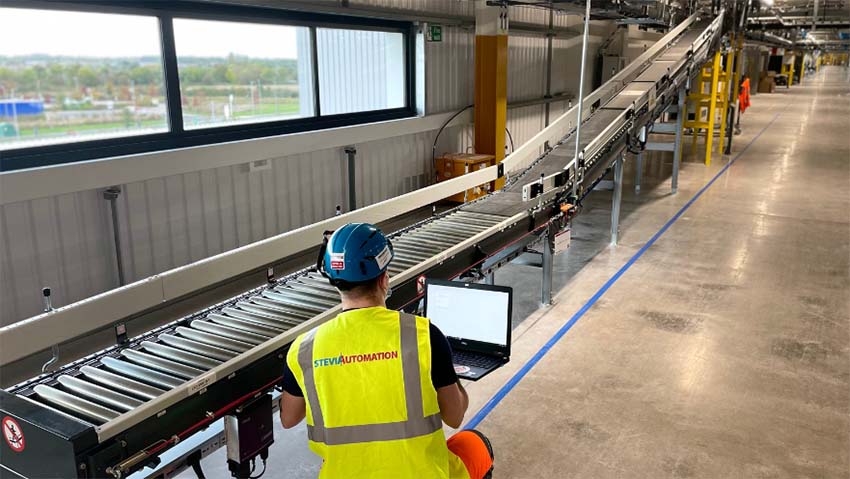
“Currently, in the intralogistics sector, the automation and robotic systems are mainly used in the large companies, having a good position on the market and being recognizable to the world. “ – says Paweł Wróbel, Managing Director – “Over the next 5-10 years, it is going to change, as a lot of smaller companies are showing their interest in automated intralogistics systems.”
To sum up, automated systems will develop and gain popularity also among the smaller companies, as the priority is now to increase the speed and accuracy of fulfillment and to speed up the delivery time of goods.
E.E: What are the most innovative products marketed?
In our opinion, the most innovative products that are marketed in our industry are modern production ecosystems that should integrate the systems at every level. It leads to the state, where all the automation elements, production and business systems are unified. Going further, warehouse, transport and distribution are coming together into one system, so that you can see the transparent view of all processes throughout the entire company, including logistics.
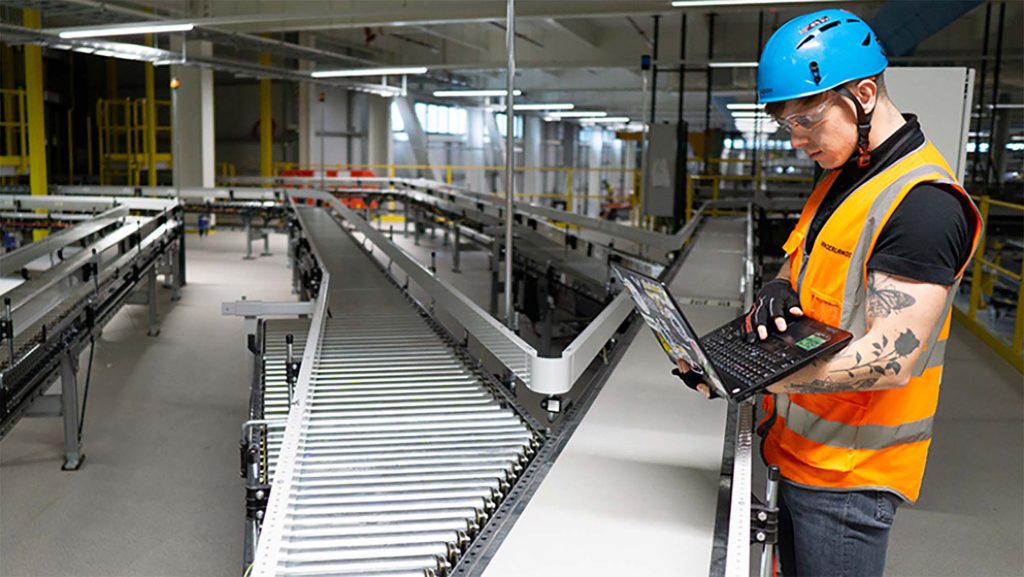
The key point here is to develop communication interfaces and integration tools between all these systems. The mentioned integration is needed if we want to have a transparent view on our company and distribution system. We need to develop fast and standardized communication interfaces between each of them that guarantees high throughput of information.
E.E: What estimations do you have for the rest of 2023?
As there is not much time left in 2023, we would like to continue our existing projects through the end of this year. It is so far a good year for us, full of development opportunities and many exciting projects. We always pay attention to maintain in touch with our clients, to hear their needs, and we keep creating good relationships with our potential clients. We hope to develop even more in 2024 and we already have some interesting plans and projects going on next year.